一种微孔陶瓷雾化芯及其制造的方法与流程



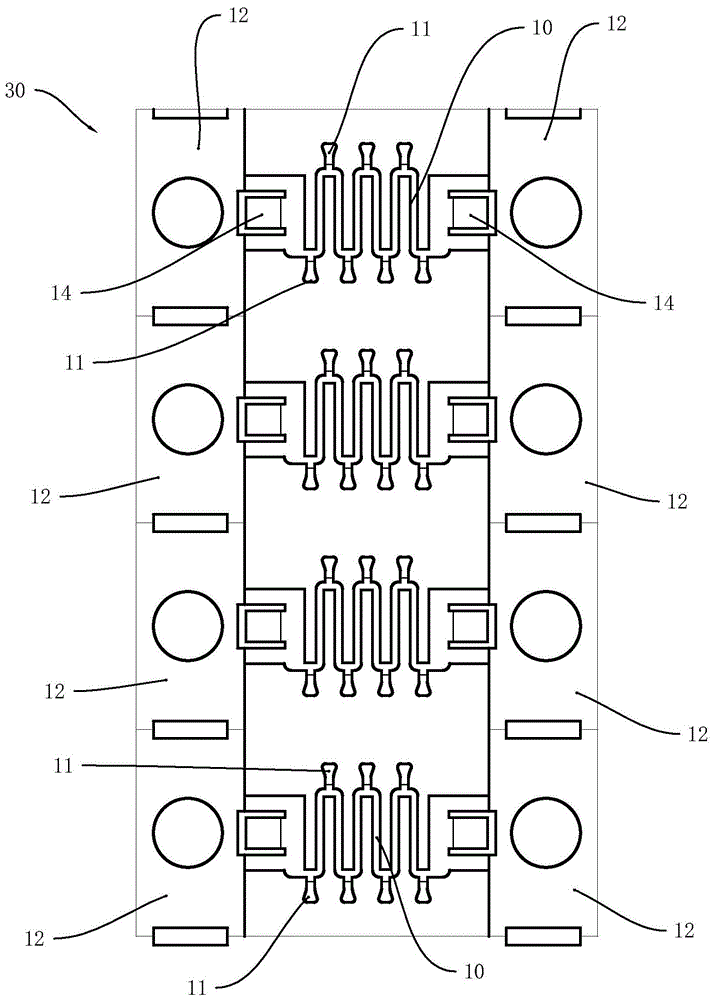
本发明涉及雾化芯技术领域,尤其是一种微孔陶瓷雾化芯及其制造的方法。
背景技术:
传统的电子烟雾化器用的微孔陶瓷雾化芯的发热片是烧结在微孔陶瓷体表面,烧结时,由于发热片埋入微孔陶瓷体的深浅程度不一致,因此,热胀冷缩后,发热片容易脱离微孔陶瓷体,影响产品的合格率;同时由于发热片埋入微孔陶瓷体的深浅程度不一致,在雾化加热过程中,加热雾化时形成干烧及温度不一致,影响口感。
技术实现要素:
本发明的目的是解决现有技术的不足,提供一种微孔陶瓷雾化芯及其制造的方法。
本发明的一种技术方案:
一种微孔陶瓷雾化芯,包括设有引线的发热线路以及微孔陶瓷基体,所述发热线路设有加强肋,所述发热线路镶嵌在微孔陶瓷基体表面,所述加强肋嵌入微孔陶瓷基体内。
本发明的另一种技术方案:
一种制造微孔陶瓷雾化芯的方法,包括:
s1,成型片状的电阻片,通过蚀刻或冲压将电阻片加工成至少一发热线路,其中发热线路的两端具有固定块、边缘具有加强肋;
s2,折弯发热线路的加强肋,使得加强肋与发热线路成一夹角;
s3,在发热线路的两电极上焊接引线;
s4,将发热线路装到成型模内,成型模将发热线路两端的固定块固定以防止发热线路翘曲,往成型模内注入陶瓷浆液,发热线路与陶瓷浆液成型成一体,此时,陶瓷浆液形成微孔陶瓷基体,发热线路的加强肋埋入微孔陶瓷基体内,发热线路一侧面嵌在微孔陶瓷基体内,另一侧面外露在微孔陶瓷基体表面;
s5,去除发热线路周边的固定块;
s6,排胶,将步骤s5得到的表面镶嵌有发热线路的微孔陶瓷基体埋入具有陶瓷粉的排胶炉内,通过排胶炉将微孔陶瓷基体内的成型剂排出;
s7,高温烧结,通过高温烧结炉将排胶后的微孔陶瓷基体进行高温烧结形成具有一定强度的微孔陶瓷体。
一种优选方案是还包括s8,去粉,通过震动碾磨机将微孔陶瓷体表面的烧结粉去除。
一种优选方案是还包括s9,通过超声波清洗微孔陶瓷雾化芯表面的粉尘。
一种优选方案是还包括烘干微孔陶瓷雾化芯。
一种优选方案是步骤s1中电阻片蚀刻或冲压形成引线焊接板,引线焊接板形成发热线路的电极;
在步骤s2中折弯发热线路的引线焊接板,使得引线焊接板与发热线路成一夹角;
在步骤s3中在发热线路的两引线焊接板处分别焊接引线。
综合上述技术方案,本发明的有益效果:发热线路设有加强肋,发热线路镶嵌在微孔陶瓷体基座表面,加强肋嵌入微孔陶瓷体基座内;发热线路不易脱离微孔陶瓷体基座,发热线路与微孔陶瓷体基座固定牢固;通过本发明的工艺将发热线路的结构进行改善,在增加了发热线路的两端蚀刻或冲压形成固定块,将发热线路装到成型模内时,成型模将发热线路两端的固定块固定以防止发热线路翘曲,在成型过程中发热线路不容易产生移位及变形,发热线路烧结在微孔陶瓷体基座表面平整,雾化效果的一致性大大提高。
上述说明仅是本发明技术方案的概述,为了能够更清楚了解本发明的技术手段,而可依照说明书的内容予以实施,并且为了让本发明的上述和其他目的、特征和优点能够更明显易懂,以下特举较佳实施例,并配合附图,详细说明如下。
附图说明
图1是本发明中电阻片蚀刻或冲压后形成的示意图一;
图2是本发明中电阻片蚀刻或冲压后形成的示意图二;
图3是本发明发热线路的加强肋折弯时的示意图;
图4是本发明中微孔陶瓷雾化芯的立体图一;
图5是本发明中微孔陶瓷雾化芯的立体图二;
图6是本发明中微孔陶瓷雾化芯的透视图。
具体实施方式
为阐述本发明的思想及目的,下面将结合附图和具体实施例对本发明作进一步的说明。
第一实施例,如图1至图6所示,一种微孔陶瓷雾化芯1,包括设有引线13的发热线路10,以及微孔陶瓷基体20,所述发热线路10设有加强肋11,所述发热线路10镶嵌在微孔陶瓷基体20表面,所述加强肋11嵌入微孔陶瓷基体20内。
如图1至图6所示,加强肋11嵌入微孔陶瓷基体20,增加了发热线路10与微孔陶瓷基体20之间的牢固性,防止发热线路10从微孔陶瓷基体20表面脱离,提高了稳定性。
如图1至图6所示,发热线路10为s形或者其它异形,加强肋11设置在发热线路10的边缘,发热线路10的两端还设有引线焊接板14,引线焊接板14与发热线路10的平面呈一夹角,该夹角可以是90度,引线13与引线焊接板14焊接,发热线路10通过引线焊接板14与引线13焊接,增加了与引线13的焊接面积,提高了引线13与发热线路10之间的牢固性,防止引线13脱离发热线路10。
第二实施例,如图1至图6所示,一种制造微孔陶瓷雾化芯1的方法,包括:
s1,成型片状的电阻片30,通过蚀刻或冲压将电阻片30加工成至少一发热线路10,其中发热线路10的两端具有固定块12、边缘具有加强肋11;发热线路10的数量可以根据电阻片30的大小来确定,电阻片30可以蚀刻或冲压形成若干平行的发热线路10,每一发热线路10的两端都具有固定块12、边缘都具有加强肋11。
s2,折弯发热线路10的加强肋11,使得加强肋11与发热线路10成一夹角;本实施例中,通过过自动机将加强肋11折成图3中所示的形状,即加强肋11与发热线路10之间的夹角为90度。在一些情况下,加强肋11与发热线路10之间的夹角可以根据需要设置。
s3,在发热线路的两电极上焊接引线13;本实施例中通过碰焊、激光焊等工艺将纯镍的引线13焊接到发热线路10的两电极上。
s4,将发热线路10装到成型模内,成型模将发热线路10两端的固定块12固定以防止发热线路10翘曲,往成型模内注入陶瓷浆液,发热线路10与陶瓷浆液成型成一体,此时,陶瓷浆液形成微孔陶瓷基体20,发热线路10的加强肋11埋入微孔陶瓷基体20内,发热线路10一侧面嵌在微孔陶瓷基体20内,另一侧面外露在微孔陶瓷基体20表面。
s5,去除发热线路周边的固定块;
s6,排胶,将步骤s5得到的表面嵌有发热线路10的微孔陶瓷基体20埋入具有陶瓷粉的排胶炉内,通过排胶炉将微孔陶瓷基体内的成型剂排出。
s7,高温烧结,在高温烧结炉将排胶后的微孔陶瓷基体20和发热线路10进行高温烧结形成具有一定强度的微孔陶瓷雾化芯1。
如图1至图6所示,增加了发热线路的两端蚀刻或冲压形成固定块和加强肋,将发热线路装到成型模内时,成型模将发热线路两端的固定块固定以防止发热线路翘曲,在成型过程中发热线路不容易产生移位及变形,发热线路烧结在微孔陶瓷体基座表面平整,雾化效果的一致性大大提高。同时在成型过程中,加强肋嵌入微孔陶瓷基体20内,增加了发热线路10与微孔陶瓷基体20之间的牢固性,防止发热线路10从微孔陶瓷基体20表面脱离,提高了稳定性。
如图1至图6所示,一些实施例中,当电阻片30蚀刻或冲压形成若干平行的发热线路10时,每一发热线路10的两端都具有固定块12、边缘都具有加强肋11。
如图1至图6所示,一些实施例中,
一些实施例中,还包括s8,去粉,通过震动碾磨机将微孔陶瓷体20表面的烧结粉去除。
一些实施例中,还包括s9,通过超声波清洗微孔陶瓷雾化芯1表面的粉尘。
优选的,还包括烘干微孔陶瓷雾化芯1。
如图1至图6所示,一些实施例中,步骤s1中电阻片30蚀刻或冲压形成引线焊接板14,引线焊接板14形成发热线路10的电极;
在步骤s2中折弯发热线路10的引线焊接板14,使得引线焊接板14与发热线路10成一夹角;引线焊接板14与发热线路10之间的夹角为90度。
在步骤s3中在发热线路10的两引线焊接板14处分别焊接引线13。引线13与引线焊接板14相互平行焊接,增加引线焊接板14与引线13的焊接点,提高了引线13的牢固性。
以上是本发明的具体实施方式,应当指出,对于本技术领域的普通技术人员来说,在不脱离本发明原理的前提下,还可以做出若干改进和润饰,这些改进和润饰也视为本发明的保护范围。
起点商标作为专业知识产权交易平台,可以帮助大家解决很多问题,如果大家想要了解更多知产交易信息请点击 【在线咨询】或添加微信 【19522093243】与客服一对一沟通,为大家解决相关问题。
此文章来源于网络,如有侵权,请联系删除


