一种涂料及其制备方法、一种原油输送管道防结蜡的方法与流程



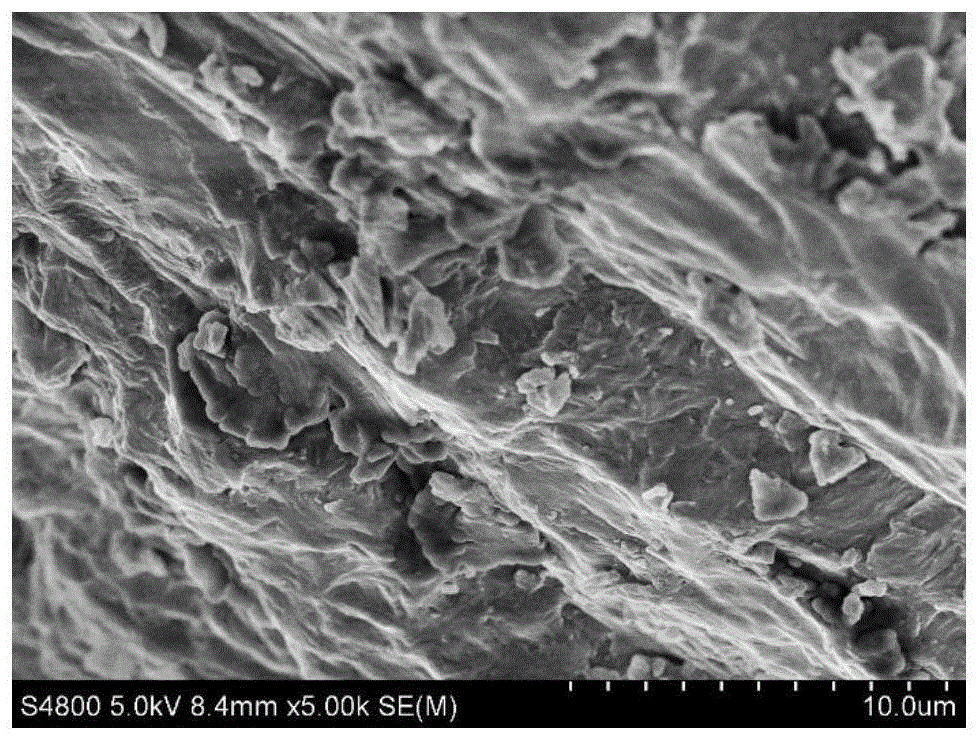
本发明属于石油与天然气工程-油气储运工程
技术领域:
,尤其涉及一种涂料及其制备方法、一种原油输送管道防结蜡的方法。
背景技术:
:我国原油大多数为“三高”原油,即含蜡高、凝点高和粘度大。原油输送管道在运行一段时间后,在管道内壁会沉积一定厚度的结蜡层。管道内壁结蜡后管内径变小,摩阻增加,输送能力下降,大大降低原油输送效率,需要定期清除结蜡层,造成大量的能源浪费。目前,现有技术中缓解原油管道内壁结蜡的主要手段是在原油管道内壁涂覆超疏油材料,使亲油性的蜡不容易沉积。但是,这样的内涂层并没有改变原油输送的热力环境,不能抑制蜡析出,在某些涂层有缺陷的地方,结蜡现象甚至更加严重。技术实现要素:鉴于此,本发明的目的在于提供一种涂料及其制备方法、一种原油输送管道防结蜡的方法,将本发明提供的涂料涂覆在原油输送管道的内壁表面能够控制管壁附近油温在原油的析蜡温度以上,可有效抑制蜡析出,解决蜡沉积问题。为了实现上述发明目的,本发明提供了以下技术方案:本发明提供了一种涂料,包括以下质量份数的组分:聚合物树脂80~100份、有机溶剂10~20份、固化剂20~30份、有机硅树脂微球1~10份和碳材料5~10份;所述碳材料包括石墨烯、氧化石墨烯、胺化石墨烯、导电碳粉和碳纳米管中的一种或多种;所述碳材料的平均粒径为30~500nm。优选地,所述有机硅树脂微球包括聚甲基硅倍半氧烷微球、聚二甲基硅倍半氧烷微球、聚苯基硅倍半氧烷微球和聚二苯基倍半氧烷微球中的一种或多种。优选地,所述有机硅树脂微球的平均粒径为50nm~1μm。优选地,所述固化剂包括二乙烯基三胺、氨乙基哌嗪、间苯二胺、二氨基二苯基甲烷、酰胺基胺和尿素中的一种或多种。优选地,所述聚合物树脂包括聚乙烯、聚苯乙烯、聚丙烯、聚氯乙烯、聚乙酸乙烯、聚丙烯腈、乙酸乙烯-氯乙烯共聚物、氯乙烯-偏氯乙烯共聚物和苯乙烯-丙烯腈共聚物中的一种或多种。本发明还提供了上述技术方案所述涂料的制备方法,包括以下步骤:将聚合物树脂、有机溶剂、固化剂、有机硅树脂微球和碳材料混合,得到所述涂料。本发明还提供了一种原油输送管道防结蜡的方法,包括以下步骤:将上述技术方案所述涂料或由上述技术方案所述制备方法制得的涂料涂覆在原油输送管道的内壁表面,经固化在所述内壁表面形成涂层后,在所述原油输送管道的两端施加电压;所述电压为6~60v。本发明提供的涂料,包括以下质量份数的组分:聚合物树脂80~100份、有机溶剂10~20份、固化剂20~30份、有机硅树脂微球1~10份和碳材料5~10份;所述碳材料包括石墨烯、氧化石墨烯、胺化石墨烯、导电碳粉和碳纳米管中的一种或多种;所述碳材料的平均粒径为30~500nm。在本发明中,添加的碳材料具有焦耳热效应,将碳材料作为原料之一,涂覆于原油输送管道的内壁表面形成的涂层具有良好的导电性与导热性,通过在原油输送管道的两端施加较小的电压,即可产生大量的热量,能够控制管壁及附近油温在原油的析蜡温度以上,可有效抑制蜡析出,缓解蜡沉积问题。且本发明提供的涂料成本低。本发明提供的原油输送管道防结蜡的方法,能耗低,在管道两道施加较小电压即可,施工环境安全。附图说明图1为实施例1得到的涂层的sem图;图2为实施例1~4得到的涂层随施加电压的时间的温度变化图;图3为实施例5得到的涂层随施加电压的时间的温度变化图;图4为不同涂料得到涂层的tafel极化曲线图;图5为实施例7~10得到涂层的tafel极化曲线图。具体实施方式本发明提供了一种涂料,包括以下质量份数的组分:聚合物树脂80~100份、有机溶剂10~20份、固化剂20~30份、有机硅树脂微球1~10份和碳材料5~10份。在本发明中,若无特殊说明,所采用的原料均为本领域常规市售产品。本发明提供的涂料包括质量份数为80~100份的聚合物树脂,优选为85~95份,更优选为90份。在本发明中,所述聚合物树脂优选包括聚乙烯、聚苯乙烯、聚丙烯、聚氯乙烯、聚乙酸乙烯、聚丙烯腈、乙酸乙烯-氯乙烯共聚物、氯乙烯-偏氯乙烯共聚物和苯乙烯-丙烯腈共聚物中的一种或多种。在本发明中,所述聚合物树脂作为涂料的基材。本发明提供的涂料包括质量份数为10~20份的有机溶剂,优选为12~18份,更优选为15份。在本发明中,所述有机溶剂优选包括丙烯酸乙酯、醋酸丁酯、环己酮、乙二醇丁醚和乙酸丁酯纤维素中的一种或多种。本发明提供的涂料包括质量份数为20~30份的固化剂,优选为22~28份,更优选为25份。在本发明中,所述固化剂优选包括二乙烯基三胺、氨乙基哌嗪、间苯二胺、二氨基二苯基甲烷、酰胺基胺和尿素中的一种或多种。本发明提供的涂料包括质量份数为1~10份的有机硅树脂微球,优选为2~8份,更优选为5份。在本发明中,所述有机硅树脂微球优选包括聚甲基硅倍半氧烷微球、聚二甲基硅倍半氧烷微球、聚苯基硅倍半氧烷微球和聚二苯基倍半氧烷微球中的一种或多种。在本发明中,所述有机硅树脂微球的平均粒径优选为50nm~1μm。在本发明中,有机硅树脂微球能够提高涂层的韧性,防止涂层因原油的输送磨蚀而迅速失效,且有机硅树脂微球能够在涂层内形成“硅网络结构”,降低涂层的孔隙率,进而降低水分子在涂层中的渗透率,从而提高涂层的防腐性能。本发明提供的涂料包括质量份数为5~10份的碳材料,优选为7~9份,更优选为8份。在本发明中,所述碳材料包括石墨烯、氧化石墨烯、胺化石墨烯、导电碳粉和碳纳米管中的一种或多种,优选为胺化石墨烯。在本发明中,当所述碳材料优选为胺化石墨烯时,所述胺化石墨烯的胺化程度优选为70~100%;当所述碳材料优选为氧化石墨烯时,所述氧化石墨烯的氧化程度优选为25~50%;当所述碳材料优选为石墨烯时,所述石墨烯的纯度优选>99%。在本发明中,所述碳材料的平均粒径为30~500nm,优选为100~400nm,更优选为200~300nm。本发明添加的碳材料具有焦耳热效应,将碳材料作为原料,涂覆于原油输送管道的内壁表面形成的涂层具有良好的导电性与导热性,且本发明通过调节碳材料与其他组分之间的比例,有效的提高了碳材料在涂料中的分散性,进一步提高涂层的导电性与导热性,从而实现在较低电压下,产生大量热量的目的。在本发明中,若碳材料的质量份数过少,则碳材料在涂料中的分散性较差,涂层的导电性能较差;若碳材料的质量份数过多,则成本较高。在本发明具体实施例中,所述碳材料和有机硅树脂微球的质量比优选为1:1~1.5,在上述范围内,本发明得到的涂层具有优异的防腐性能。本发明提供的涂料优选由上述技术方案所述聚合物树脂、有机溶剂、固化剂、有机硅树脂微球和碳材料组成。本发明还提供了上述技术方案所述涂料的制备方法,包括以下步骤:将聚合物树脂、有机溶剂、固化剂、有机硅树脂微球和碳材料混合,得到所述涂料。本发明对所述聚合物树脂、有机溶剂、固化剂、有机硅树脂微球和碳材料混合的顺序没有特殊的限定,采用任意混合的顺序均可。在本发明中,所述混合的方式优选为超声分散,所述超声分散的功率优选为600~1800w;所述超声分散的频率优选为20~120khz;所述超声分散的时间优选为120min。本发明还提供了一种原油输送管道防结蜡的方法,包括以下步骤:将上述技术方案所述涂料或由上述技术方案所述制备方法制得的涂料涂覆在原油输送管道的内壁表面,经固化,在所述内壁表面形成涂层后,在所述原油输送管道的两端施加电压。在本发明中,所述涂覆的方式优选为刷涂或喷涂;当所述涂覆的方式优选为刷涂时,所述刷涂的刷涂量优选为50~800g/cm2,更优选为200~500g/cm2;当所述涂覆的方式优选为喷涂时,所述喷涂的压力优选为0.5mpa;所述喷涂的流量优选为0.5~2ml/cm2;所述喷涂的距离优选为20~60cm。在本发明中,所述固化的温度优选为110~140℃;所述固化的时间优选为5~15min。在本发明中,所述电压为6~60v,优选为25~40v。本发明在原油输送过程中,优选持续施加压力。本发明优选在所述原油输送管道的首末端分别接经变压的火线和零线来对所述原油输送管道施加压力。下面结合实施例对本发明提供的涂料及其制备方法、原油输送管道防结蜡的方法进行详细的说明,但是不能把它们理解为对本发明保护范围的限定。实施例1将聚乙烯80份、丙烯酸乙酯10份、二乙烯基三胺20份、聚甲基硅倍半氧烷微球1份(平均粒径为110nm)和胺化石墨烯5份(平均粒径为349.56nm)混合,得到涂料。将得到的涂料刷涂于原油输送管道内表面,刷涂量为800g/cm2,在120℃固化5min形成涂层,在20.1℃的条件下,在原油输送管道,两端分别施加6v、12v、18v、24v、30v和60v电压,施加600s后撤去施加的电压,对涂层表面温度进行测量,测量结果参见表1和图2,得到的涂层的sem图参见图1。实施例2本实施例与实施例1的区别仅在于,碳材料为导电碳粉,平均粒径为296.14nm。对涂层表面温度进行测量,测量结果参见表1和图2。实施例3本实施例与实施例1的区别仅在于,碳材料为碳纳米管,平均粒径为297.24nm。对涂层表面温度进行测量,测量结果参见表1和图2。实施例4本实施例与实施例1的区别仅在于,胺化石墨烯的平均粒径为177.48nm。对涂层表面温度进行测量,测量结果参见图2。表1实施例1~3得到的涂层施加不同电压后产生的温度结果图2为实施例1~4得到的涂层随施加电压的时间的温度变化图,其中,a为实施例1得到的涂层,b为实施例2得到的涂层,c为实施例4得到的涂层,d为实施例3得到的涂层,图2的测试条件为在20.1℃的条件下,在原油输送管道两端施加18v电压,施加600s后撤去施加的电压。结合图2和表1分析可知,不同碳材料具有的焦耳热效应不同,其中,胺化石墨烯的焦耳热效应最佳;对同一碳材料来说,随着管道两端施加电压的增大,涂层产生的热量增多;且同一碳材料的粒径对于焦耳热效应的影响较大,随着碳材料粒径增大,涂层产生的热量呈现先增多后减少的趋势。实施例5本实施例与实施例1的区别仅在于胺化石墨烯的平均粒径分别为30.13nm、85.58nm、177.48nm、349.56nm和499.78nm。对制得的涂层的防蜡率进行测试,测试结果参见表2。对涂层表面温度进行测量,测量结果参见图3。实施例6本实施例与实施例2的区别仅在于导电碳粉的平均粒径分别为115.38nm、235.19nm、296.14nm、375.55nm和488.78nm。对制得的涂层的防蜡率进行测试,测试结果参见表2。实施例7本实施例与实施例3的区别仅在于碳纳米管的平均粒径分别为158.21nm、221.58nm、297.24nm、366.13nm和453.97nm。对制得的涂层的防蜡率进行测试,测试结果参见表2。表2不同碳材料的不同粒径对涂层防蜡效果的影响结果注:表2中的防蜡率是与无涂层的原油输送管道表面对比数据,防蜡率的计算公式参见式1。图3为实施例5得到的涂层随施加电压的时间的温度变化图,其中,a的粒径为30.13nm,b的粒径为85.58nm,c的粒径为177.48nm,d的粒径为349.56nm,e的粒径为499.78nm。图3的测试条件为在20.1℃的条件下,在原油输送管道两端施加18v电压,施加600s后撤去施加的电压。实施例6和7得到的涂层随施加电压的时间的温度变化图与实施例5相近,以实施例5为例说明,结合图3和表2分析可知,碳材料的粒径对于涂层产生的热量以及防蜡率有重要影响。对比例1本对比例与实施例1的区别仅在于:胺化石墨烯1份(平均粒径为349.56nm)。将实施例1及对比例1得到的涂料刷涂于原油输送管道内表面,刷涂量为800g/cm2,在120℃固化5min形成涂层,在20.1℃的条件下,在原油输送管道两端分别施加60v电压,在600s内测量涂层表面温度,对涂层表面温度进行测量,测量结果参见表3。表3实施例1和对比例1得到涂层施加电压后产生的温度结果由上述实验数据分析可知,当胺化石墨烯添加量为1份时,得到的涂层基本不体现出发热性能,说明碳材料的用量对于涂层的发热效果有重要的影响。实施例8本实施例与实施例1的区别仅在于:胺化石墨烯6份(平均粒径为349.56nm)。实施例9本实施例与实施例1的区别仅在于:胺化石墨烯8份(平均粒径为349.56nm)。实施例10本实施例与实施例1的区别仅在于:胺化石墨烯10份(平均粒径为349.56nm)。将实施例1、实施例8~10得到的涂料刷涂于原油输送管道内表面,刷涂量为800g/cm2,在120℃固化5min形成涂层,在20.1℃的条件下,在原油输送管道两端分别施加60v电压,在600s内测量涂层表面温度,对涂层表面温度进行测量,测量结果参见表4。表4实施例1、实施例8~10得到涂层施加电压后产生的温度结果60v电压下的施加时间实施例1实施例8实施例9实施例1030s27.8℃29.9℃32.4℃34.6℃150s39.8℃42.5℃46.8℃49.5℃450s66.7℃68.2℃70.5℃74.3℃600s80.5℃82.1℃85.6℃88.5℃由上述实验数据分析可知,随着胺化石墨烯添加量的升高,涂层发热性能逐渐变好。防腐性能测试将常规市售的聚丙烯腈与乙酸乙烯-氯乙烯共聚物涂料(以下称纯树脂涂料)、胺化石墨烯涂料和实施例1制得的涂料分别涂刷于316不锈钢电极表面,刷涂量均为800g/cm2;其中胺化石墨烯涂料由10份丙烯酸乙酯、25份二乙烯基三胺和10份胺化石墨烯混合制备得到。将316不锈钢裸钢和刷涂不同涂料后的316不锈钢电极分别浸润在质量百分含量为3.0%的nacl溶液中,0.5~1h后,测试上述样品的涂层的tafel极化曲线,具体结果参见表5和图4。表5不同涂料得到涂层的腐蚀电位和腐蚀电流图4为不同涂料得到涂层的tafel极化曲线图,其中,a为裸钢、b为纯树脂涂料得到的涂层、c为胺化石墨烯涂料得到的涂层、d为实施例1涂料得到的涂层,结合图4和表5分析可知,在不锈钢表面刷涂涂料后,腐蚀电位较裸钢均有明显提高,且其中实施例1涂料得到涂层的腐蚀电位最高,自腐蚀电流明显减小,说明本发明提供的涂料得到的涂层的防腐性能最好。分析原因可知,聚甲基硅倍半氧烷微球的加入提高了聚合物树脂的阳极保护能力,且聚甲基硅倍半氧烷微球能够在涂层内形成“硅网络结构”,使得涂层孔隙率降低,因而水分子在其中的渗透率大幅降低,从而提升了聚合物涂层的防腐性能。实施例11本实施例与实施例1的区别仅在于,称取聚乙烯80份、丙烯酸乙酯10份、二乙烯基三胺20份、聚甲基硅倍半氧烷微球3份(平均粒径为50nm)和胺化石墨烯5份(平均粒径为30.13nm)。实施例12本实施例与实施例1的区别仅在于,称取聚乙烯80份、丙烯酸乙酯10份、二乙烯基三胺20份、聚甲基硅倍半氧烷微球5份(平均粒径为50nm)和胺化石墨烯5份(平均粒径为30.13nm)。实施例13本实施例与实施例1的区别仅在于,称取聚乙烯80份、丙烯酸乙酯10份、二乙烯基三胺20份、聚甲基硅倍半氧烷微球7.5份(平均粒径为50nm)和胺化石墨烯5份(平均粒径为30.13nm)。实施例14本实施例与实施例1的区别仅在于,称取聚乙烯80份、丙烯酸乙酯10份、二乙烯基三胺20份、聚甲基硅倍半氧烷微球10份(平均粒径为50nm)和胺化石墨烯5份(平均粒径为30.13nm)。防腐性能测试将实施例11~14制得的涂料制得的涂料分别刷涂于316不锈钢电极表面;将刷涂后的316不锈钢电极分别浸润在质量百分含量为3.0%的nacl溶液中,0.5h后,测试上述样品的涂层的tafel极化曲线,具体结果参见表6和图5,不同涂料的刷涂量均为800g/cm2。表6实施例11~14得到的涂层的腐蚀电位和腐蚀电流图5为实施例11~14得到涂层的tafel极化曲线图,其中,a为实施例11、b为实施例14、c为实施例12、d为实施例13,结合图5和表6分析可知,随着涂层中的聚甲基硅倍半氧烷微球质量的增加,自腐蚀电流呈现出先减小后增大的趋势,自腐蚀电压呈现出先增大后减小的趋势。说明随着聚甲基硅倍半氧烷微球加入量的提高,可以增强胺化石墨烯涂层的防腐性能,但是聚甲基硅倍半氧烷微球加入量超过一定范围后,涂层的防腐性能开始下降,分析原因可知大量聚甲基硅倍半氧烷微球产生聚集,降低涂层的致密性,导致腐蚀介质容易进入金属基体表面发生腐蚀反应。力学性能测试表7不同涂料得到的涂层的力学性能测试结果纯树脂涂料胺化石墨烯涂料实施例1涂料冲击强度×10-1/j·m-118.731.568.4测试方法gbt1843-2008gbt1843-2008gbt1843-2008拉伸模量×10-4/kpa315458765测试方法gbt2282002gbt2282002gbt2282002由上述实验结果可知,聚甲基硅倍半氧烷微球的加入,能够明显地提高涂层的韧性。实施例15本实施例与实施例1的区别仅在于,本实施例中碳材料为胺化石墨烯(平均粒径为85.58nm)和石墨烯(平均粒径为23.77nm)的混合物,胺化石墨烯和石墨烯的质量比为1:1,其中胺化石墨烯为2.5份。对制得的涂层的防蜡率进行测试,测试结果参见表8。实施例16本实施例与实施例1的区别仅在于,本实施例中碳材料为胺化石墨烯(平均粒径为85.58nm)和导电碳粉(平均粒径为488.78nm)的混合物,胺化石墨烯和导电碳粉的质量比为1:1,其中胺化石墨烯为2.5份。对制得的涂层的防蜡率进行测试,测试结果参见表8。对实施例15~16制得的涂层的温度进行测试,测试条件为在原油输送管道两端施加18v电压,施加600s后撤去施加的电压,具体结果参见表8。表8实施例15~16制得的涂层的防蜡效果的影响结果以及涂层表面温度测试结果实施例15实施例16防蜡率/wt%85.1545.77涂层表面温度(℃)71.265.3由上述实验结果分析可知,当多种碳材料混合时具有良好防蜡效果。以上所述仅是本发明的优选实施方式,应当指出,对于本
技术领域:
的普通技术人员来说,在不脱离本发明原理的前提下,还可以做出若干改进和润饰,这些改进和润饰也应视为本发明的保护范围。当前第1页1 2 3 
起点商标作为专业知识产权交易平台,可以帮助大家解决很多问题,如果大家想要了解更多知产交易信息请点击 【在线咨询】或添加微信 【19522093243】与客服一对一沟通,为大家解决相关问题。
此文章来源于网络,如有侵权,请联系删除
相关标签: 原油



tips