改性纳米氧化石墨烯作为低渗油藏提高采收率化学剂的应用的制作方法



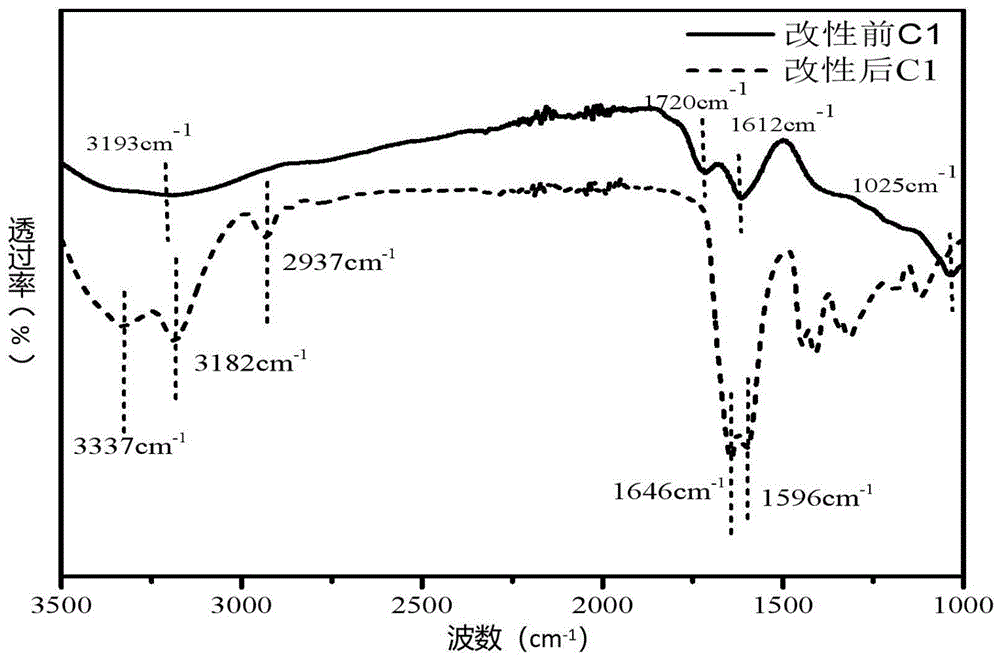
本申请涉及改性纳米氧化石墨烯作为低渗油藏提高采收率化学剂应用,属于化学材料领域。
背景技术:
:石油在国民经济中有着不可替代的作用,随着我国国民经济的迅速增长,对石油的需求也在不断地快速提高。根据《中国油气产业发展分析与展望报告蓝皮书(2018—2019)》中的数据,2018年我国原油产量1.89亿吨,原油进口量4.62亿吨,对外依存度攀升至近70%。而经过一次采油、二次采油之后,地下依然有丰富的石油存量,但开采难度逐渐增大,特别是渗透率低于50md的低渗油藏,巨大的石油储量难以动用。因此针对低渗油藏开发高效的提高采收率技术是实现国家能源安全迫切的战略需求。低渗油藏广泛分布于全国20多个油区,自上个世纪90年代以来在大庆、吉林、辽河、胜利、长庆等主要油田陆续发现了许多低渗油藏。据统计,新探明的石油地质储量中,低渗油藏储量所占的比例高达60%~70%,低渗油藏是我国今后相当长一段时间内增产增储的主要基础。目前用于低渗油藏的提高采收率技术包括水驱、表面活性剂驱、聚合物驱、微生物驱和复合驱等技术体系。现有技术在低渗油藏的应用都存在着各式各样的问题。低渗油藏水驱的波及面积小,易水窜水淹,驱油效率低,水驱采收率仅20%左右,大部分原油滞留在油藏中无法采出。表面活性剂驱技术在现场应用时存在地层吸附损耗高、不耐二价盐、产出液油水乳化难处理等问题。而由于低渗油藏的喉道细小、孔隙结构复杂,聚合物驱在低渗油藏应用时存在地层堵塞、不耐高温高盐的问题,导致其不能有效提高采收率。而微生物驱油技术存在见效时间短、激活剂窜流、驱油效率不理想等问题。二元、三元复合驱技术不仅存在上述问题,而且由于大量化学品注入地层后,不易生物降解,会造成地下水资源污染和油藏生态环境的破坏。目前,将纳米材料驱油技术应用于低渗油藏的研究报道较少,主要为改性的纳米二氧化硅材料。专利申请号cn201810838339.7公布了一种包含鼠李糖脂表面活性剂、纳米二氧化硅的纳米颗粒悬浮液及其在低渗透油藏提高采收率中的应用。但是纳米二氧化硅材料应用于低渗油藏时,依然会存在地层吸附大、不耐高温高盐等局限性。技术实现要素:根据本申请的第一方面,提供了改性纳米氧化石墨烯作为低渗油藏提高采收率化学剂应用,由于改性的纳米氧化石墨烯材料尺寸小于300nm,而且是柔性片层结构,可以通过形变适应低渗油藏的孔喉大小,地层吸附损耗小,能够耐受高温高盐条件,将有助于克服目前低渗油藏开发过程中面临的问题。所述改性纳米氧化石墨烯作为油藏提高采收率化学剂应用,所述改性纳米氧化石墨烯由微晶氧化石墨烯经改性剂改性而成,所述改性纳米氧化石墨烯的粒径≤300nm,将所述改性纳米氧化石墨烯与矿化水混合形成流体注入油藏地层。可选地,将所述改性纳米氧化石墨烯与矿化水混合形成质量浓度为0.05~0.2%流体注入油藏地层。可选地,所述油藏是指渗透率低于50md的低渗透油藏。可选地,所述微晶氧化石墨烯为粒径≤200nm的微晶氧化石墨烯,可选地,所述微晶氧化石墨烯的粒径上限可选自150nm、100nm,优选所述微晶氧化石墨烯的粒径为50~100nm。可选地,所述微晶氧化石墨烯的制备方法包括:对微晶石墨粉进行氧化,得到微晶氧化石墨,其中,微晶石墨粉碳含量可选75~100wt%;对所述微晶氧化石墨进行剥离、除杂得到粒径≤200nm的微晶氧化石墨烯。通过采用微晶石墨粉作为原料,一方面原料来源广,可有效降低改性纳米石墨烯的生产成本,便于提高采收率化学剂推广应用;另一方面,微晶石墨中石墨的粒径远远小于鳞片石墨中石墨的粒径,以微晶石墨为原料可以获得尺寸更小的改性纳米氧化石墨烯材料。可选地,所述微晶石墨粉的粒径为≤5μm。可选地,所述微晶石墨粉的粒径为100nm~5μm;所述微晶石墨粉的粒径上限可选自5μm、1.6μm、1.3μm、1μm、900nm、800nm、700nm、600nm、500nm、400nm、300nm或200nm,下限可选自1.6μm、1.3μm、1μm、900nm、800nm、700nm、600nm、500nm、400nm、300nm、200nm或100nm。优选地,所述微晶石墨粉的粒径为≤1.6μm。微晶石墨粉的粒径≤1.6μm时,可以提高采收率,从而具有优异的驱油性能,并且岩心的吸附较低,损耗较少。采用该粒径范围的微晶石墨粉经过氧化、剥离、除杂后可以得到粒径≤200nm的微晶氧化石墨烯。可选地,所述对微晶石墨粉进行氧化的条件包括:采用化学氧化法,以浓硫酸、高锰酸钾、双氧水作为氧化剂;每克微晶石墨粉对应的浓硫酸用量为20~100克;每克微晶石墨粉对应的高锰酸钾用量为1~5克;所述双氧水浓度为25~40%,每克微晶石墨粉对应双氧水的用量为0.1~1.2克。其他反应条件如搅拌条件、反应温度、反应时间、分离条件、洗涤条件等均与传统hummers化学氧化法相同。可选地,所述对所述微晶氧化石墨进行剥离的条件包括:通过超声剥离;超声功率为700~750w;优选720w;超声频率为10~30hz;优选20hz;超声时间为0.5~2h。通过在该条件下进行超声剥离,极大地缩短了小粒径微晶氧化石墨烯的制备时间,提高了生产效率。进一步地,所述对微晶石墨粉进行氧化、剥离之后,还包括:通过离心方式除杂;离心转速为100~1000rpm;离心时间为5~20min。可选地,离心转速上限可选自1000rpm、800rpm、700rpm、600rpm、500rpm、400rpm、300rpm或200rpm,下限可选自800rpm、700rpm、600rpm、500rpm、400rpm、300rpm、200rpm或100rpm。离心时间上限可选自20min、15min或10min,下限可选自15min、10min或5min。该方法制备过程属于常温常压,操作安全简单,制备的纳米级改性氧化石墨烯提高采收率化学剂在水中具有良好的分散性可选地,所述改性剂包括脂肪醇聚氧乙烯醚、月桂酸二乙醇酰胺、n-乙烯基吡咯烷酮、聚乙烯亚胺、聚乙二醇、油酸、α-烯烃磺酸钠、丙烯酸、丙烯酰胺中的至少一种,所述改性纳米氧化石墨烯的制备方法为:将含有微晶氧化石墨烯分散液、改性剂的混合物,在催化剂作用下反应,得到改性纳米氧化石墨烯。通过使用催化剂使改性剂和位于微晶氧化石墨烯上的羧基、羟基、环氧基发生反应,将改性基团接枝到微晶氧化石墨烯上,从而使微晶氧化石墨烯由亲水转变成既亲水又亲油。当该材料作为应用于石油开采时,可以有效地降低油水之间的界面张力,从而提高石油采收率,经过改性后也提高材料的耐温耐盐性,降低了材料在地层环境的吸附性。可选地,所述微晶氧化石墨烯分散液中,微晶氧化石墨烯的浓度为0.01~30mg/ml。可选地,所述微晶氧化石墨烯和所述改性剂的质量之比为1:1~1:100。可选的,所述催化剂为二环己基碳二亚胺、n,n-二异丙基碳二亚胺、1-乙基-(3-二甲氨基丙基)碳二亚胺盐酸盐、n-羟基琥珀酰亚胺、偶氮二异丁腈、过硫酸钾、过硫酸铵、过氧化氢、4-二甲氨基吡啶、氢氧化钠、盐酸中的至少一种。可选的,所述催化剂的用量和所述改性剂的质量之比为1:1~1:100。可选地,所述反应的条件包括:在搅拌条件下反应;搅拌速率为100~800rpm;搅拌时间为1小时~8小时;可选地,所述改性纳米氧化石墨烯在所述流体中的质量浓度为0.001~0.02%。所述改性纳米氧化石墨烯在所述流体中的质量浓度上限可选自0.02%、0.015%、0.01%或0.005%,下限可选自0.015%、0.01%、0.005%、0.001%。可选地,所述水的矿化度为2000~50000mg/l。所述水的矿化度上限可选自50000mg/l、45000mg/l、40000mg/l、35000mg/l30000mg/l、25000mg/l、20000mg/l、15000mg/l、10000mg/l、5000mg/l、4000mg/l或3000mg/l,下限可选自45000mg/l、40000mg/l、35000mg/l30000mg/l、25000mg/l、20000mg/l、15000mg/l、10000mg/l、5000mg/l、4000mg/l、3000mg/l或2000mg/l。在一可选具体实施例中,所述改性纳米氧化石墨烯的制备方法包括:步骤(1)购买符合粒径要求的微晶石墨粉,使用化学氧化法将其氧化,得到微晶氧化石墨;步骤(2)将步骤(1)中微晶氧化石墨,通过低转速离心、静置过滤等方式去除底层大颗粒杂质,并通过去离子水洗涤,获得较纯的微晶氧化石墨凝胶;步骤(3)将步骤(2)中获得的微晶氧化石墨进行超声剥离,并将超声剥离后的微晶氧化石墨烯凝胶进行除杂,获得平均粒径为100-200nm的微晶氧化石墨烯分散液;步骤(4)将步骤(3)中微晶氧化石墨烯分散液进行改性,获得适用于低渗油藏的改性纳米氧化石墨烯提高采收率化学剂。可选地,步骤(1)中筛选出粒径在为≤1.3μm的微晶石墨样品;可选地,步骤(1)使用的氧化剂为浓硫酸、高锰酸钾、双氧水,浓硫酸使用量为石墨的20~100倍,高锰酸钾使用量为石墨的1~5倍,双氧水使用量为石墨的0.1~1.0倍;可选地,步骤(2)离心转速为100-1000rpm,离心时间5-20min;可选地,步骤(3)超声时间为0.5-2h,超声功率720w,频率20hz。本申请能产生的有益效果包括:(1)改性纳米氧化石墨烯材料是柔性片层结构,且尺寸小于300nm,适应低渗油藏的孔喉大小;(2)改性纳米氧化石墨烯材料可以耐受80℃~120℃的高温,可以耐受50000~200000ppm高矿化度盐水,能够适应更苛刻的油藏条件;(3)相较于油田常用的聚丙烯酰胺、表面活性剂等材料,改性纳米氧化石墨烯材料在地层吸附损耗很少;(4)本申请提供的改性纳米氧化石墨烯制备过程属于常温常压,操作安全简单,制备的纳米级改性氧化石墨烯提高采收率化学剂在水中和各种油性溶剂中具有良好的分散性;(5)选择微晶石墨作为原料,相较于选择相同目数的鳞片石墨原料,可以制备出尺寸更小的改性纳米氧化石墨烯材料。附图说明图1是实施例1中的改性之前的微晶氧化石墨烯、改性后的改性纳米氧化石墨烯的红外谱图;图2是实施例1中由微晶石墨出发,氧化剥离、接枝改性后的改性纳米氧化石墨烯的粒径分布图;图3是对比例1中由鳞片石墨出发,氧化剥离、接枝改性后的改性纳米氧化石墨烯的粒径分布图;图4是实施例1中由微晶石墨出发,氧化剥离、接枝改性后的改性纳米氧化石墨烯的扫描电镜照片。具体实施方式下面结合实施例详述本申请,但本申请并不局限于这些实施例。如无特别说明,本申请的实施例中的原料均通过商业途径购买。其中,微晶石墨粉购自南方石墨有限公司,型号分别为3000目(初始粒径5μm),8000目(初始粒径1.6μm),15000目(初始粒径1μm);鳞片石墨粉购自青岛伟杰石墨有限公司,型号为15000目(初始粒径1μm);浓硫酸、高锰酸钾、双氧水、聚乙烯亚胺、月桂醇聚氧乙烯醚、聚乙二醇、n-乙烯基吡咯烷酮、二氯甲烷、偶氮二异丁腈、n,n-二异丙基碳二亚胺、1-乙基-(3-二甲氨基丙基)碳二亚胺盐酸盐、n-羟基琥珀酰亚胺、4-二甲氨基吡啶、纳米二氧化硅、鼠李糖脂等试剂购自上海阿拉丁生化科技股份有限公司。如无特别说明,实施例中反应均为室温下进行。本申请的实施例中分析方法如下:利用马尔文激光粒度仪(购自上海思百吉仪器系统有限公司)进行粒径测试;利用carlzeissevo18型扫描电子显微镜(:购自德国卡尔蔡司公司)进行扫描电镜sem测试;利用nicoletis50傅立叶变换红外光谱仪(购自赛默飞世尔科技股份有限公司)进行红外测试;采用dnqp型室内石油驱替设备(购自南通华兴石油仪器有限公司)进行室内石油驱替实验;室内石油驱替实验使用的岩心选用美国贝雷砂岩天然岩心,购自北京东方智盛石油科技有限公司,渗透率为20~50md;利用1260型高效液相色谱仪(购自美国agilent公司)进行驱出液中样品浓度的测试。本申请实施例中提高采收率计算方法为:实施例11、量取250ml质量分数为98%的浓硫酸,倒入放有搅拌子的500ml玻璃烧杯中搅拌,将称取的5.00g15000目的微晶石墨粉缓慢加入烧杯中,在冰水浴中进行磁力搅拌30min后,边搅拌边缓慢加入研磨好的高锰酸钾粉末25g,继续在冰水浴中保持搅拌120min,撤去冰水浴,将温度升至37℃,继续保持搅拌120min,缓慢加入去离子水,控制温度低于60℃,加水直至反应体系温度不再上升,滴加5ml30%浓度的h2o2;2、将溶液放置于离心机,设置转速800转,时间5分钟,静置后过滤除去大颗粒杂质,转入1000ml烧杯中,加去离子水洗至ph≥6,获得微晶氧化石墨凝胶;3、将微晶氧化石墨凝胶放入超声波分散机中以720w功率、20hz频率超声分散60min进行剥离,之后,转移至离心机以3000rpm转速离心5min,去除杂质,获得微晶氧化石墨烯分散液,使用马尔文激光粒度仪测试平均粒径;4、向上述微晶氧化石墨烯分散液中依次加入50克聚乙烯亚胺、10克1-乙基-(3-二甲氨基丙基)碳二亚胺盐酸盐、6克n-羟基琥珀酰亚胺,调节混合物ph至6~7,保持搅拌反应24小时后过滤离心,在去离子水中再分散得到聚乙烯亚胺改性纳米氧化石墨烯作为提高采收率化学剂,记为c1;5、使用马尔文激光粒度仪测试平均粒径见图2,使用sem观察纳米材料形貌见图4,使用红外光谱仪检测改性剂接枝程度见图1,使用矿化水将改性纳米氧化石墨烯分散液稀释到指定浓度,放入设定温度的烘箱进行耐温耐盐稳定性考察。6、使用矿化水将改性纳米氧化石墨烯分散液稀释到指定浓度,进行室内石油驱替实验,评价提高采收率性能,检测驱出液中改性纳米氧化石墨烯的浓度,评价吸附损耗程度。实施例2本实施例采用8000目的微晶石墨替代实施例1中15000目微晶石墨粉,采用跟实施例1相同的方法和步骤,得到聚乙烯亚胺修饰的改性纳米氧化石墨烯提高采收率化学剂,记为c2。实施例3本实施例制备方法与实施例1基本相同,不同之处在于步骤1中使用3000目的微晶石墨粉,最终所得产品记为c3。实施例4本实施例制备方法与实施例1基本相同,不同之处在于,步骤1中浓硫酸用量为100ml,高锰酸钾用量为5克,最终得到聚乙烯亚胺修饰的改性纳米氧化石墨烯提高采收率化学剂,记为c4。实施例5步骤1-3与实施例1相同;4、向上述微晶氧化石墨烯分散液中依次加入50克n-乙烯基吡咯烷酮、5克偶氮二异丁腈,通入氮气排除氧气,升温至70℃,保持500转每分搅拌,反应5小时后得到聚乙烯吡咯烷酮改性纳米氧化石墨烯作为提高采收率化学剂,记为c5;步骤5、6与实施例1相同。实施例6步骤1-3与实施例1相同;4、将上述微晶氧化石墨烯水分散液烘干后,使用二氯甲烷溶解,加入50克月桂醇聚氧乙烯醚,1克1-(3-二甲氨基丙基)-3-乙基碳二亚胺盐酸盐、1克4-二甲氨基吡啶,室温搅拌反应24小时后稀盐酸洗、水洗、过滤得到月桂醇聚氧乙烯醚改性纳米氧化石墨烯水分散液作为提高采收率化学剂,记为c6;步骤5、6与实施例1相同。实施例7本实施例制备方法与实施例6基本相同,不同之处在于步骤4中使用聚乙二醇替代月桂醇聚氧乙烯醚,最终得到聚乙二醇修饰的改性纳米氧化石墨烯提高采收率化学剂,记为c7。实施例8本实施例制备方法与实施例6基本相同,不同之处在于,采用油酸替代月桂醇聚氧乙烯醚,得到油酸修饰的改性纳米氧化石墨烯提高采收率化学剂,记为c8。对比例1本对比例采用15000目的鳞片石墨替代实施例1中的微晶石墨,采用跟实施例1相同的制备方法和步骤,得到聚乙烯亚胺修饰的改性纳米氧化石墨烯提高采收率化学剂,记为d1。对比例2将平均粒径为15nm的纳米二氧化硅颗粒与鼠李糖脂按质量比25:1的比例混合,得到提高采收率化学剂,记为d2.产物分析对实施例1中的改性之前的微晶氧化石墨烯、聚乙烯亚胺改性后的改性纳米氧化石墨烯进行红外谱图测定,结果如图1所示。从图1中可以看出,改性前微晶氧化石墨烯,在1720cm-1和1612cm-1处的特征吸收峰分别归因于氧化石墨烯上羧酸基团的碳氧双键和氧化石墨烯上的碳碳双键。而改性纳米氧化石墨烯的红外谱图上有强烈的酰胺键(3337cm-1、3182cm-1、1646cm-1,1596cm-1)的红外特征吸收峰,证明聚乙烯亚胺在微晶氧化石墨烯上接枝成功。实施例2、3、4也表现出与实施例1相同或相似特征,证明聚乙烯亚胺改性接枝成功。实施例5、6、7、8中改性前、后氧化石墨烯的红外谱图对比显示酯键出现,证明改性剂接枝成功。产品粒径如表1所示:表1产品粒径表上述的c1、d1粒径测试结果显示相较于鳞片石墨,选用微晶石墨可以有效降低产品的尺寸,而且c1~c8的结果显示优选的氧化剂用量、改性剂种类、催化剂用量能够使得改性后纳米氧化石墨烯提高采收率化学剂的尺寸更小。基于纳米二氧化硅的对比产品d2显示了最小的粒径尺寸,但后续的耐温耐盐性能、吸附性能测试将显示其缺陷。以c1为典型代表,图2为改性纳米氧化石墨烯的粒径分布图,由图2可以看出,改性纳米氧化石墨烯c1的平均粒径为143.2nm。以c1为典型代表,图4为改性氧化石墨烯的扫描电镜照片,由扫描电镜照片可以看出,改性纳米氧化石墨烯为一种多褶皱的柔性片层纳米材料。实施例9将实施例1~8及对比例1~2提供的产品进行耐温耐盐性能测试:配置测试样品:将产品c1、c2、c3、c4、c5、c6、c7、c8、d1及d2分别与矿化度为50000ppm的水混合得到产品质量分数为0.1%的分散液样品,分别记为h1、h2、h3、h4、h5、h6、h7、h8、h9、h10;将产品c1、c2、c3、c4、c5、c6、c7、c8、d1及d2分别与矿化度为100000ppm的水混合得到产品质量分数为0.1%的分散液样品,分别记为g1、g2、g3、g4、g5、g6、g7、g8、g9、g10;将产品c1、c2、c3、c4、c5、c6、c7、c8、d1及d2分别与矿化度为200000ppm的水混合得到产品质量分数为0.1%的分散液样品,分别记为l1、l2、l3、l4、l5、l6、l7、l8、l9、l10;耐温耐盐性能测试方法:将上述分散液样品放置于精密恒温箱中,设定温度为80℃、100℃、120℃。观察恒温放置7天后的稀释液外观,在光线充足的环境下观察是否有沉淀、悬浮颗粒。产品耐温耐盐性能测试结果如表2所示:表2产品耐温耐盐稳定性测试结果表2的耐温耐盐性能测试结果说明,实施例1~8中的改性氧化石墨烯提高采收率化学剂,相较于对比例1~2中的化学剂产品,能够耐受更高的温度和矿化度。产品c1~c8能够同时耐受120℃的高温和20万矿化度盐水保持稳定分散,不会出现沉淀,而对比产品d1只能耐受到80℃的温度,对比产品d2只能耐受到5万矿化度盐水。表中,“√”表示未出现沉淀、悬浮颗粒,“×”表示出现沉淀、悬浮颗粒实施例10对分散液样品h1、h2、h3、h4、h5、h6、h7、h8、h9、h10进行驱油性能和吸附性能测试:驱油性能测试方法:首先岩心110℃下干燥12小时,抽真空下注入矿化水进行水饱和,通过称重法得到孔体积pv,然后注入原油进行油饱和,记录饱和油量v1,70℃老化48小时,注入矿化水进行水驱至没有油驱出(注入体积2pv),接着依次进行提高采收率化学剂驱(注入2pv体积的提高采收率化学剂)、后续水驱(注入体积2pv)。注入速率维持在0.2ml/min,记录水驱阶段出油体积v2、提高采收率化学剂驱阶段出油体积v3、后续水驱阶段出油体积v4。计算(v3+v4)/v1×100%即为提高采收率值。样品驱油性能测试结果如表3所示:表3产品驱油性能测试结果样品h1h2h3h4h5h6h7h8h9h10提高采收率%24.122.321.520.421.320.920.220.810.39.8结果分析:从表3中可以看出,h1~h8的提高采收率结果均超过20%,可见其能够进入岩心内部,将第一次水驱后的剩余油驱替出来,从而实现采收率的提升;而h9、h10的提高采收率结果均小于11%,可见其驱油性能明显低于本申请实施例提供的产品;尤其是实施例1中的产品c1,在质量分数为0.1%的浓度(分散液中矿化度为5万ppm)下,提高采收率高达22.1%,显示其优异的驱油性能;而对比例2中的产品d2,在质量分数为0.1%的浓度(分散液中矿化度为5万ppm)下,提高采收率仅为9.8%,驱油效果不佳。吸附性能测试:通过高效液相色谱仪检测驱油性能实验中驱出液中样品h1、h2、h3、h4、h5、h6、h7、h8、h9、h10的浓度,评价吸附损耗程度。驱出液中样品浓度为c驱,驱出液体积为v驱,注入样品浓度为0.1%,注入体积为2pv,吸附率计算方法:表4产品吸附性能测试结果样品h1h2h3h4h5h6h7h8h9h10吸附率%8.29.49.710.211.610.811.111.730.259.4结果分析:从表4中可以看出,h1~h8的吸附率结果均低于12%,可见其在岩心的吸附较低,损耗较少;而h9、h10的吸附率结果均大于30%,可见其在岩心中吸附损失很大。以上所述,仅是本申请的几个实施例,并非对本申请做任何形式的限制,虽然本申请以较佳实施例揭示如上,然而并非用以限制本申请,任何熟悉本专业的技术人员,在不脱离本申请技术方案的范围内,利用上述揭示的技术内容做出些许的变动或修饰均等同于等效实施案例,均属于技术方案范围内。当前第1页1 2 3 
起点商标作为专业知识产权交易平台,可以帮助大家解决很多问题,如果大家想要了解更多知产交易信息请点击 【在线咨询】或添加微信 【19522093243】与客服一对一沟通,为大家解决相关问题。
此文章来源于网络,如有侵权,请联系删除



tips