压井用三元复合暂堵剂及其压井暂堵施工方法与流程



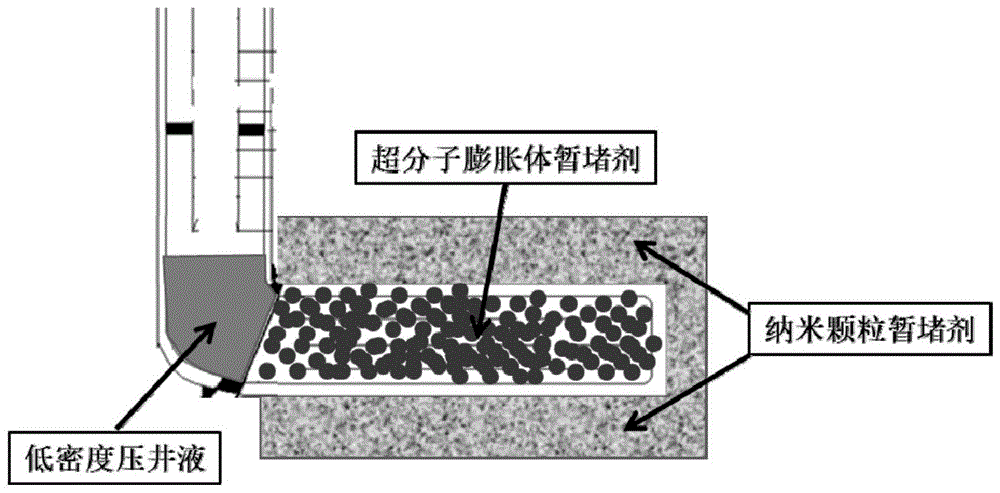
本发明涉及油田化学
技术领域:
,特别涉及一种压井用三元复合暂堵剂及其压井暂堵施工方法。
背景技术:
:上世纪80年代我国的暂堵技术才发展起来,在许多方面是对传统的堵水技术的借鉴。随着堵水技术的发展,对暂堵剂的开发和应用日趋成熟,出现了不同类型凝胶型暂堵技术。屏蔽暂堵技术的使用较为广泛。上世纪90年代,屏蔽暂堵技术在我国得到了迅猛发展和广泛应用。屏蔽暂堵技术主要是根据孔喉大小、裂缝宽窄和分布有目的地在某些液相体系中加入多级配的架桥粒子,在压差作用下,瞬间在井壁边缘形成一层低渗透率的屏蔽环,有效起到阻止某些液相体系中的固体颗粒和滤液侵入储层造成各种伤害。油井完成后可通过射孔、反排及酸或油溶的方式解堵,恢复储层的原始状态。利用类似的原理将凝胶型暂堵剂屏蔽压井液体系进入地层,来实现修井完井的作业目的。但是针对特定地质条件下,如地层漏失严重、气窜快、井况复杂、地层温度高、井口压力高,常规暂堵压井往往出现压井就漏,漏完就喷,无法进行后续施工作业。这种情况下,只能采用复合暂堵压井技术。目前在复合暂堵剂方面的研究有:水化膨胀复合暂堵材料:目前最常用的暂堵方法是桥接暂堵,技术关键在于暂堵剂中颗粒尺寸的分布是否和漏失通道直径相匹配。由于漏失地层的裂缝宽度和孔隙尺寸不能准确掌握,暂堵剂配方无法优选和确定,施工的不确定性增大,暂堵成功率降低。为此,左凤江等研制了水化膨胀复合暂堵材料。该堵剂克服了桥接暂堵时架桥骨架在正、负压差作用下容易破坏的缺陷,引入了具有遇水延时膨胀特性的材料。随着与钻井液接触时间的延长,该材料会吸水膨胀至原体积的5~18倍,使“封堵墙”更加致密紧凑,与裂缝间的摩擦阻力进一步加强,“封堵墙”在正、负压差作用下的抗破坏能力增强。该材料中还添加了长纤维材料,弥补了棉纤维和木质纤维强度低的缺陷,增强了暂堵材料在长裂缝中的缠绕封堵强度。通过各种材料的合理级配,可充分发挥各物质的合力作用,具有较好的弹性和挂阻特征,进入裂缝后能产生较高的桥塞强度,达到快速、安全、有效暂堵的目的。该暂堵剂在长庆油田白马北区水源3井(bmbs3)应用,一次暂堵成功。复合暂堵材料blcm:复合暂堵材料blcm(blendoflost-circulationmaterials)主要是由粒径2~120mm的特殊纤维颗粒组成,添加了适当尺寸的植物纤维及聚合物颗粒。其中的木质纤维类物质在水或水基钻井液的浸泡下膨胀,可增加对垫层的封堵能力。特立尼达岛(trinidad)东海岸某井(井深1400m)使用直径245mm钻头钻进时发生失返性漏失,导致泵压不稳定,无法正常钻进,用常规方法暂堵效果不好,改用blcm材料成功处理了井漏。blcm材料吸水膨胀,形成了具有一定的强度和黏弹性的网状结构,在压差作用下被挤入漏失层,并根据漏失层的形状自动填充,从而解决了漏失问题。交联聚合物暂堵材料:davidson等人介绍了一种用于处理严重漏失的交联聚合物体系,此体系由适当尺寸的特殊纤维和水溶性交联聚合物组成。纤维材料吸水膨胀后悬浮在暂堵浆中,在形成的堵塞中纵横交错、相互拉扯,起强有力的“拉筋”作用,加强了楔塞的机械强度。吸水膨胀的凝胶及含“拉筋”材料的滤饼共同在漏失通道中形成塞状的封堵垫层,该垫层在漏层中不易移动,因而可达到暂堵目的。另外,此暂堵材料对地层无伤害,受地层温度影响可在两星期内降解,期间有足够的时间来钻进和完井。将此凝胶用于giove-2井,成功地治理了失返性漏失并恢复了循环钻进。微粒复合凝胶暂堵剂:lecolier等研究制备了纳米复合有机/无机凝胶暂堵剂。聚合物暂堵剂交联后形成的凝胶能有效封堵裂缝的条件是裂缝壁面的剪切应力不大于凝胶的静切力。但许多交联聚合物的交联反应在地面进行,在钻穿漏失层前可能过早形成凝胶体。1990年法国石油研究院的zaitoun等人报道用不加交联剂的可胶凝聚合物(主要是各种类型的聚丙烯酰胺)暂堵,主要利用聚合物在地层孔喉中的桥接吸附来选择性地降低水相渗透率而较小降低气相渗透率,以达到堵水不堵气的目的。由于聚合物吸附层的就地舒展性,既能提高传统暂堵方法的效果,又不至于因交联作用而降低气井的产能,并根据地层的不同条件,选用不同类型的聚合物,研究了相适应的不同处理方法。法国石油研究院于2005年提出一种新方法,使用含有膨胀聚合物颗粒和凝胶颗粒的暂堵剂,并把这种材料命名为微复合有机/无机胶。此材料含有有机复合凝胶材料,活性有机增韧剂和活性无机膨胀增强剂,通过有机结构剂和膨胀增强剂的特殊成网机制,在漏层近井壁带快速吸水膨胀并吸附搭桥交联,形成三维网架结构,固相颗粒在网架结构上聚凝沉积成富集体,大大提高了暂堵效率,有效抑制暂堵浆向漏层深部漏失。这种暂堵剂在漏层驻留性强,封堵层短时间内承压能力高,流动性好,初凝时间易调整。增加活性有机增韧剂的含量可以增强微复合胶的强度,压力对微复合凝胶体的形成过程有一定影响,但水的矿化度及温度对其稳定性影响不大。经岩心实验表明,此复合胶具有良好的密封性,且对环境无不良影响,其组成分可以干混,便于储存和运输。该胶在160℃下热滚16h不会发生降解。综上所述,现有的压井暂堵技术在特定地质条件下,如地层漏失严重、气窜快、井况复杂、地层温度高、井口压力高,常规暂堵压井技术往往出现压井就漏,漏完就喷,无法进行后续施工作业。技术实现要素:本发明的目的是提供一种在压井施工过程中能够实现对井下的水、气进行有效暂堵的压井用三元复合暂堵剂。本发明的另一目的是提供一种采用上述压井用三元复合暂堵剂实施的压井暂堵施工方法,以解决现有常规压井暂堵技术无法解决在地层漏失严重、气窜快、井况复杂、地层温度高、井口压力高等特定地质条件下实现有效暂堵,进而导致无法进行后续施工作业等问题。为此,本发明技术方案如下:一种压井用三元复合暂堵剂,包括可溶性纳米级微粒暂堵剂、超分子膨胀体和低密度压井液;其中,可溶性纳米级微粒暂堵剂由15~25kg分散剂、2500~4000kg氯化钠、60~90kg黄原胶、6000~7500kg二水氯化钙、1~3kg亚硫酸钠和80~180kg钼酸钠溶解在15~19.5m3的地层水中混合配制而成;超分子膨胀体暂堵剂为丙烯酸和丙烯酰胺共聚交联所得凝胶体;低密度压井液为1wt.‰的聚丙烯酰胺水溶液,聚丙烯酰胺的分子量1000万~1500万。优选,在15.0~19.5m3的地层水中加入15~25kg分散剂,搅拌20~40min后,继续加入2500~4000kg氯化钠和60~90kg黄原胶,继续搅拌10~30min,慢速加入6000~7500kg二水氯化钙、1~3kg亚硫酸钠和80~180kg钼酸钠,室温下搅拌10~50min,即得到可溶性纳米级微粒暂堵剂;其中,分散剂为十二烷基硫酸钠、木质素磺酸钠或十二烷基苯磺酸钠。优选,超分子膨胀体暂堵剂的制备方法为:将质量比为3:7丙烯酸和丙烯酰胺溶解在水中,加入占单体总重量的1.0wt.%的过硫酸铵为引发剂和0.03wt.%的clb型交联剂,在60℃下反应5h;将所得产物经烘干、粉碎后,即得到超分子膨胀体暂堵剂。一种采用上述压井用三元复合暂堵剂实现的压井暂堵施工方法,其步骤为:根据地质条件和完井情况依次向地层正注微粒暂堵剂、隔离液、超分子暂堵剂、低密度压井液和常规压井液以完成暂堵施工。而待修井或其他作业完成后,通过连续油管注入破胶液即可对超分子暂堵剂进行破胶,即可实现解堵。如图1所示,该压井暂堵施工方法通过将水溶性纳米暂堵剂主要是通过筛管进入近井地层对储层和大的裂缝进行滤饼封堵,注入超分子膨胀体暂堵剂对筛管进行充填式封堵,注入低密度压井液进一步使超分子膨胀体暂堵剂在高压下封填紧密,进而实现对作业井进行有效的封堵。优选,上述压井暂堵施工方法的具体施工步骤如下:s1、正注高强度微粒暂堵剂,使其填充在钻孔与筛管之间的环空空间前端;其中,可溶性纳米级微粒暂堵剂用量根据公式:q=πr12h计算得到,q为需注入的液量,r1为需注入地层的半径,φ为地层孔隙度,h为注入地层长度,其取值略大于筛管长度;s2、正注隔离液;s3、正注1wt.%的超分子暂堵剂配液,使其以爬坡压力>7mpa的压力条件注入至在筛管内;注入完成后停泵1h,充分膨胀以填充满筛管;其中,超分子膨胀体暂堵剂的用量根据筛管的体积和超分子膨胀体暂堵剂在水中膨胀倍数计算得到;s4、正注低密度压井液,将其作为顶替液进行顶替施工,其用量使低密度压井液进一步填充于筛管缝隙内并在筛管与上部管柱连接处形成一段液封;s5、正注清水作为常规压井液,封堵作业完成;在上述步骤s1~s5中,各工作液的注入排量均为300~350l/min。优选,在修井作业结束后,通过连续油管以300~350l/min的排量相正注破胶液,并于关井24h后返排,完成解堵;其中,破胶液为0.2~2wt.%的过硫酸铵和1.5~0.1wt.%的高锰酸钾的混合溶液。与现有技术相比,该压井用三元复合暂堵剂由可溶性纳米级微粒暂堵剂、超分子膨胀体暂堵剂和低密度压井液构成;其在暂堵施工过程中,该压井用三元复合暂堵剂中的可溶性纳米级微粒暂堵剂主要是通过筛管进入近井地层对储层和大的裂缝进行滤饼封堵,继而注入超分子膨胀体暂堵剂对筛管进行充填式封堵,最后注入低密度压井液进一步使超分子膨胀体暂堵剂在高压下封填得更紧密,从而达到三元协同作用,对作业井进行有效的封堵。附图说明图1为本发明的压井用三元复合暂堵剂作用于压井暂堵的原理示意图;图2(a)为本发明实施例1中对可溶性纳米级微粒暂堵剂进行水驱的流量压差变化测试的结果示意图;图2(b)为本发明实施例1中对可溶性纳米级微粒暂堵剂进行顶替液驱的流量压差变化测试的结果示意图;图2(c)为本发明实施例1中对可溶性纳米级微粒暂堵剂进行转向剂驱的流量压差变化测试的结果示意图;图2(d)为本发明实施例1中对可溶性纳米级微粒暂堵剂进行盐水解堵的流量压差变化测试的结果示意图;图3为本发明实施例1中不同浓度的超分子膨胀体暂堵剂在0.5%kcl溶液中膨胀倍数的曲线示意图;图4为本发明实施例1中不同浓度的老化超分子膨胀体暂堵剂在0.5%kcl溶液中膨胀倍数的曲线示意图;图5为本发明的实施例1中针对超分子膨胀体暂堵剂的突破压力评价的测试装置的结构示意图。具体实施方式下面结合附图及具体实施例对本发明做进一步的说明,但下述实施例绝非对本发明有任何限制。实施例1一种压井用三元复合暂堵剂,包括可溶性纳米级微粒暂堵剂、超分子膨胀体暂堵剂和低密度压井液。其中,可溶性纳米级微粒暂堵剂由20kg十二烷基硫酸钠、3500kg工业级氯化钠、80kg黄原胶、7000kg二水氯化钙、2kg除氧剂和2kg缓蚀剂,溶解在15m3的地层水中混合配制而成。该可溶性纳米级微粒暂堵剂具体制备方法如下:在15m3的地层水中加入20kg十二烷基硫酸钠,搅拌20~40min后,继续加入再将80kg黄原胶和7000kg工业级氯化钠,继续搅拌10~30min,慢速加入178kg二水氯化钙,同时加入2kg除氧剂亚硫酸钠和150kg缓蚀剂钼酸钠,室温下搅拌30min,即得到20m3可溶性纳米级微粒暂堵剂。超分子膨胀体暂堵剂为丙烯酸和丙烯酰胺的共聚物胶联所得;其具体制备方法如下:将质量比为3:7丙烯酸和丙烯酰胺溶解在水中,再加入占单体总重量的1.0wt.%的过硫酸铵为引发剂和0.03wt.%的clb型交联剂,搅拌混合均匀,并于60℃下反应5h;将所得果冻状凝胶体经烘干、粉碎后,即得到超分子膨胀体暂堵剂。性能测试:首先,对可溶性纳米级微粒暂堵剂的封堵性能和解堵性能进行评价。具体通过压裂转向剂岩心驱替过程分别测试出盐水驱的流量压差变化、顶替液驱的流量压差变化、转向剂驱的流量压差变化和盐水解堵的流量压差变化。具体测试方法如下:(一)填制填砂管并装配填砂管封堵实验装置:该实验使用的填砂管的内径为3.96cm,内长为8.36cm,用100-200目的石英砂填制,填砂使用液压机压力为6mpa,在填砂管内部出口端放置一张300目的钢丝筛网防止石英砂流走,填制过程中多次敲击填砂管的外壁可使内部砂子和各部分压力较为均匀,当液压机压力下降需要再次压制6mpa,直到再次敲击填砂管外壁时压力不下降。装配填砂管封堵实验装置:将平流泵、中间容器、填砂管和末端接收器。实验在常温条件下进行。(二)使用液体的配置及参数:盐水为1%的nacl溶液,密度为1.15g/cm3,黏度为1.01mpa.s;顶替液为1‰的聚丙烯酰胺溶液,其用于驱走盐水防止后注入的转向剂中颗粒溶解;压裂转向剂的黏度为32.5mpa·s;酸化转向剂的黏度为72.5mpa·s。(三)填砂管渗透的测定:(1)游标卡尺测定填砂管的内径和内长(精确度为0.01cm),称量填砂管干重为m1;(2)连接装置:500ml的zr-3型活塞容器为中间容器,中间容器下端口与平流泵连接,上端口与填砂管的进口端连接,填砂管的出口端放置一个10ml量程量筒;(3)测孔隙度:在中间容器内注入500ml的盐水,各连接口旋紧后,打开中间容器的下端口阀门,打开平流泵设置参数,保护压强ph设为40mpa,视实际情况设置流速f,并开始注入盐水,注入过程中主要观察是否有漏水现象;(4)测量岩心堵前渗透率:当填砂管末端有液体流出时,每隔30s记录一次平流泵上压力读数(由于填砂管的一端与大气相通,另一端与平流泵相通,所以平流泵上压力的示数就是填砂管两端的压差),并用量筒测量实际流量,当压力和流量都趋于平稳说明填砂管已注满水,此时测量填砂管湿重m2,计算其孔隙体积和堵前岩心渗透率;其中,孔隙体积计算公式如下:pv=(m2-m1)/ρ,式中,m1为填砂管干(g);m2为填砂管湿重(g);ρ为流体密度(g/cm3)。堵前岩心渗透率计算公式如下:k=(q×μ×l)/(a×δp)×10-1,式中,δp为岩心两端的压差(mpa);μ为流体的黏度(mpa·s);q一定压差下流体流过岩心的流量(ml/s);l为岩心长(cm);a为岩心截面积(cm2);k为岩心的渗透率(μm2);其中,堵前岩心渗透率记为k1。(5)顶替盐水:暂停平流泵后,将中间容器内的盐水换成顶替液,连接好容器后将流量参数稍调大,开启平流泵,当压力稍有上升,且压力和流量稳定后说明填砂管中的水相已经完全被顶替液驱替。(6)测量封堵率:暂停平流泵后,将中间容器内的顶替液换成转向剂,连接好容器后将平流泵的流量稍调小;开启平流泵,每隔30s记录压力和流量,注入一定pv量后,暂停平流泵,计算堵后岩心渗透率,计算公式同上,记为k2。封堵率计算公式如下:η=(kw-k’w)/(kw)×100%,式中,η为封堵率;k1为堵前岩心渗透率(μm2);k2为堵后岩心渗透率(μm2)。(7)测量解堵率:暂停平流泵后,将中间容器内的转向剂换成水驱液,连接好容器后开启平流泵。每隔30s记录压力和流量,当压力和流量都趋于平稳,暂停平流泵,计算解堵后的岩心渗透率,计算公式同式(4-2)记为k3。解堵率计算公式如下:g=(k3-k’2)/(k1-k’2)×100%,式中,g为解堵率;k1为封堵前岩心渗透率(μm2);k2为封堵后岩心渗透率(μm2);k3为解堵后岩心渗透率(μm2);由于本实验在填制填砂管的过程中已经在填砂管出口端加入了钢丝网,且本型号的填砂管两段的封堵头长度不同,能够承受的压力也不同,因此解堵的时候选择正驱解堵;(8)关掉平流泵,卸下中间容器和填砂管,将其冲洗干净放置在烘箱中烘干待下次使用。如图2(a)所示为对可溶性纳米级微粒暂堵剂进行水驱的流量压差变化测试的结果示意图。由图2(a)的测试结果可以看出,用盐水驱替4min后压差和流量都稳定,说明此时填砂管中已注满盐水,压差为0.2mpa,流量为0.03ml/s,可以计算出堵前岩心渗透率k1=1.132μm2;此时填砂管的湿重m2=4527.74g。如图2(b)所示为对可溶性纳米级微粒暂堵剂进行顶替液驱的流量压差变化测试的结果示意图。由图2(b)的测试结果可以看出,用顶替液驱替时,在4.5min后压差和流量都稳定,压差为0.3mpa比盐水驱替时稍高,是因为顶替液为聚丙烯酰胺溶液黏度和密度都稍高于盐水,因此稳定后会导致两段压差稍高,说明此时填砂管内的盐水已经完全被顶替液驱替。如图2(c)所示为对可溶性纳米级微粒暂堵剂进行转向剂驱的流量压差变化测试的结果示意图。图2(c)为向填砂管中注入压裂转向剂,此时平流泵的流量为0.03ml/s,可以看到随着注入时间的增加,压差一直在增加,流量则一直降低,而流量的降低出现多个平台区,这是因为在转向剂中的固体颗粒被注入到填砂管中时不会均匀的堵塞整个填砂管,某些区域被封堵以后,转向剂就向其他区域注入,注入到一定量时这些区域也被封堵,随着注入时间和量的增加,填砂管被均匀的封堵,使流量不断降低;此时压差为21.6mpa,流量为0.00833ml/s,计算出堵后岩心渗透率k2=0.085μm2,由k1、k2计算出压裂转向剂的封堵率为92.49%。如图2(d)所示为对可溶性纳米级微粒暂堵剂进行盐水解堵的流量压差变化测试的结果示意图。由图2(d)的测试结果可以看出,封堵后用盐水解堵,此时平流泵的流量为0.03ml/s,可以看出由于填砂管中的孔隙被转向剂中的颗粒封堵,开始注入盐水时,压差随着注入时间和量的增加而增加,而一直没有流体从填砂管中通过,说明封堵效果较好。当压差达到21.9mpa时,压差陡降为0.2mpa,与此同时填砂管出口端流出第一滴液体,说明此时填砂管内部突破,突破压力为21.9mpa。流量和压差均稳定时说明已经解堵完成,此时压差为0.2mpa,流量为0.0267ml/s,计算出解堵后的岩心渗透率k3=0.9145μm2,由k1、k2、k3计算出解堵率为77.03%。继而,在一定压力下向填砂管注入盐水,测定水流过填砂管时两端的压力,当流量稳定在2.7ml/min时,δp为0.3mpa,得填砂管水测渗透率k为0.231d。然后以一定压力向填砂管注入暂堵剂,挤注1.2倍孔隙体积后,填砂管两端的压差为1.8mpa;注完1.2pv暂堵剂之后,将填砂管掉头用盐水驱替,第一滴暂堵剂流出时驱替压力4.4mpa,计算得出突破压力为14.67mpa/m;而暂堵剂突破后压力稳定在6.4mpa,流速为0.0365ml/s,算得堵后渗透率k'w为0.0034d,封堵率η为98.5%。接着,用模拟现场回注水进行解堵实验,注入不同量的现场回注水解堵后,测定填砂管的渗透率。测试结果如下表1所示。表1:注入量/pv流速q/ml/min端压差δp/mpa解堵率/%12.350.550.3522.550.3580.2532.60.396.15从表1的测试结果可以看出,当用2pv的回注水解堵后,解堵率达80.25%,而用3pv的回注水解堵后,解堵率可达96.15%。该暂堵剂不用加入其他的破胶剂即可达到很好的解堵效果,主要是因为暂堵颗粒是可溶于水的氯化钠,故此暂堵剂有很好的解堵性能。(二)对超分子膨胀体暂堵剂的膨胀性能性能、抗温性能和突破压力性能依次进行评价。(1)超分子膨胀体暂堵剂在盐水中的膨胀性能评价:在常温下将超分子膨胀体暂堵剂剪成长度为3~5mm小块,置于不同体积的0.5wt.%kcl溶液中,分别配制得到2.0wt.‰、3.0wt.‰、4.0wt.‰和5.0wt.‰的超分子膨胀体暂堵剂溶液;将配制好的超分子膨胀体暂堵剂溶液在常温下静置24h,取出,用滤纸吸干水份,称量,根据公式计算其膨胀倍数,以考察聚合物的抗盐性,同时观察不同溶液浓度下3~5mm超分子膨胀体暂堵剂的吸水的性能。如图3所示为不同浓度的超分子膨胀体暂堵剂在0.5wt.%kcl溶液中膨胀倍数的曲线示意图。从图3的测试结果可以看出,超分子膨胀体暂堵剂膨胀倍数随着时间的增加而增大,在18h之前膨胀很快,但是在18h后膨胀速率减小,其原因是随着水分的减少,溶液中kcl的浓度增大;而当盐水浓度比较低时,高分子中的亲水基团吸水能力较强,随着kcl溶液浓度的提高,水溶液中含有的盐使溶液的渗透压降低,向高分子内部渗透的水分子减少,吸水速度下降;钾离子的存在,使得高分子的电离能力减弱,离子间的静电斥力减弱,交联形成的网状结构不稳定,最终导致吸水能力下降。综上所述,该超分子膨胀体暂堵剂能够在0.5%wt.kcl溶液中表现出较好的膨胀性能,抗盐性能好。(2)超分子膨胀体暂堵剂的抗温性能评价:在常温下将超分子膨胀体暂堵剂剪成长度为3~5mm小块在156℃高温高压反应釜中进行封闭老化24h,将老化后产品置于不同体积的0.5wt.%kcl溶液中,以分别配制得到2.0wt.‰、3.0wt.‰、4.0wt.‰和5.0wt.‰的超分子膨胀体暂堵剂溶液;将配制好的超分子膨胀体暂堵剂溶液在常温下静置24h,取出,用滤纸吸干水份,称量,根据公式计算其膨胀倍数,以考察其抗温性。如图4所示为不同浓度的老化超分子膨胀体暂堵剂在0.5wt.%kcl溶液中膨胀倍数的曲线示意图。从图4的测试结果可以看出,老化后的超分子膨胀体暂堵剂的膨胀倍数和未老化的膨胀倍数几乎接近,说明该超分子膨胀体暂堵剂具有较好的耐温性能。(3)超分子膨胀体暂堵剂的突破压力性能评价:突破压力是衡量微观流向改变剂强度的一个指标,在实验室采用单岩心来进行评价。如图5所示为实验装置,其中,氮气瓶1分别通过管路同时向第一中间容器2和第二中间容器3泵送氮气,使第一中间容器2和第二中间容器3通过连通管路同时向与之连接的填砂管4泵送氮气,且连通管路上设有压力表。在该性能测试中,超分子膨胀体暂堵剂采用不同矿化度的水配制为溶液,并分别用渗透率为4000~4500×10-3μm2的填砂管进行评价,填砂管的长度为10cm、直径为1cm,超分子膨胀体暂堵剂的配液浓度为0.2wt.%,微观流向改变剂注入量为1pv。测试结果如下表2所示。从表2的测试结果可以看出,该超分子膨胀体暂堵剂对地层进行封堵的突破压力是很高的,尤其是在高矿化度的水中使用的突破压力更高,其原因是颗粒在高矿化度的水中的膨胀度小,使膨胀体的强度远远大于在低矿化度水中的强度。实施例2华北油田储气库某井存在地层漏失严重,常规堵漏压井,达不到暂堵取管柱作业工况要求;气窜快,压力上窜小于2小时;井况复杂,施工难度大,井深大于4000米;地层温度高达156℃、井口压力高达30mpa;作业周期长,4天以上。利用常规堵漏压井技术,注入550方堵漏压井液,4次堵漏,耗时2个月时间,也未能堵住。基于此,继而采用实施例1的压井用三元复合暂堵剂实现的压井暂堵施工方法,具体施工步骤如下:s1、暂堵施工设计:s101、准备两个带搅拌器的15m3配液罐,相应地,与配液罐配合使用的柱塞泵的排量为12~20m3/h;s102、根据公式:q=πr12φh,计算得到可溶性纳米级微粒暂堵剂用量:其中,q为需注入的液量,r1为需注入地层的半径,φ为地层孔隙度,h为注入地层长度,其取值较筛管略长;在本实施例中,r1=0.3m,一类储层厚度29.4m,其孔隙度25.6%,二类储层厚度30.2m,其孔隙度9.6%,暂堵剂固含量为6.0%,进而可计算得到可溶性纳米级微粒暂堵剂用量为48m3;s103、采用1wt.‰的分子量1000万~1500万的聚丙烯酰胺(hpam)溶液为隔离液,其水解度为30%,该隔离液在120℃温度以上的环境中可实现24h自动降解;在本实施例中,隔离液的用量为10m3;s104、根据公式:q=πr22l对超分子膨胀体暂堵剂的用量进行计算,其中,q为需注入的液量,r2为筛管半径,l为筛管长度;在本实施例中,筛管体积为8.3m3,超分子膨胀体暂堵剂常温下溶于水的膨胀倍数为10,因此暂堵剂的加量至少为0.83m3,基于预设配制1wt.%的超分子暂堵剂配液,故计算得超分子暂堵剂配液的施工用液量为83m3;s105、配制10m3的低密度压井液;该低密度压井液为1wt.‰的分子量1000万~1500万的聚丙烯酰胺(hpam)溶液,其水解度30%;该隔离液在120℃温度以上的环境中可实现24h自动降解;s106、采用清水作为常规压井液,其用量为30m3;s107、采用0.2~2wt.%的过硫酸铵(aps)和1.5~0.1wt.%的高锰酸钾的混合物作为破胶液,其用量为8.3m3;s2、如下表3所示为本次施工的各组分用量及泵注程序:表3:如上表3所示,现场具体施工流程为:(1)配制高强度微粒暂堵剂和超分子膨胀体暂堵剂配液;(2)连接管线,在25mpa的压力下试压,保证其不刺不漏;(3)正注高强度微粒暂堵剂,使其填充在钻孔与筛管之间的环空空间前端;(4)正注隔离液;(5)正注超分子膨胀体暂堵剂,使其以爬坡压力>7mpa的压力条件注入至在筛管内;注入完成后停泵1h,充分膨胀以填充满筛管;(6)正注低密度压井液,将其作为顶替液进行顶替施工,使低密度压井液进一步填充于筛管缝隙内并在筛管与上部管柱连接处形成一段液封;(7)注入压井液;(8)修井作业;(9)待修井结束后,注入破胶液解堵,关井24h,返排,正常生产。经过本次施工,施工前油套压均为27mpa,施工后油压变为0mpa,套压为0mpa;关井观察,24h后油压仍然为0mpa,10小时后套压略升至0.5mpa,24h后升至4mpa,注入清水30m3,油套压变为0mpa。修井一周后,注入破胶液,10h开始返排,返排液粘度为7mpa.s。综上所述,本申请对地层漏失严重、地层温度高达156℃的井能够得到有效封堵,且解堵快。当前第1页1 2 3 
起点商标作为专业知识产权交易平台,可以帮助大家解决很多问题,如果大家想要了解更多知产交易信息请点击 【在线咨询】或添加微信 【19522093243】与客服一对一沟通,为大家解决相关问题。
此文章来源于网络,如有侵权,请联系删除



tips