一种具有微纳层级结构的超疏水涂料及其制备方法与流程



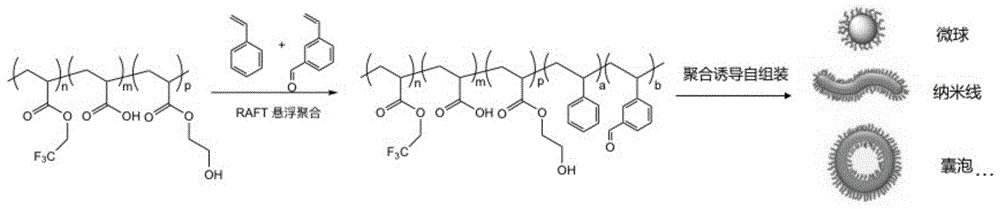
本发明涉及涂料和超疏水材料
技术领域:
,特别是指一种具有微纳层级结构的超疏水涂料及其制备方法。
背景技术:
:自上世纪70年代荷叶的超疏水自清洁效应被发现以来,仿生超疏水和超疏油便迅速成为一个具有巨大实际应用潜力的研究领域。也作为一个仿生学的生动例子在自然和技术之间搭起了一道桥梁。尤其在新材料研发方面,超疏水表面因其优秀的疏水性能和广泛的应用前景,成为国内外研究的热点之一。固体表面的浸润性由其化学结构和表面微观结构共同决定。接触角和滚动角是评价固体表面润湿性的重要参数,超疏水性表面一般是指与水的接触角大于150°,同时滚动角小于10°的一种界面性能。从固体表面化学组成角度出发,固体表面自由能越大,就越容易被液体所润湿,因此,超疏水表面的制备通常需在表面覆盖氟碳链或有机硅烷链来降低表面能,但是在光滑表面上采用化学方法来调节表面自由能,通常仅能有限的使接触角增加到120°而不能更高。要达到更高的接触角,就必须设计材料表面的微观结构,具有微米-纳米的双微观复合结构能有效提高疏(亲)水表面的疏(亲)水性能。近年来,随着表面层级结构概念的提出和印证,利用低表面能的化合物构造具有微观层级结构的表面可进一步增大涂层的疏水角度,从而达到超疏水甚至超疏油的性能。目前,多种技术(如静电纺丝、离子刻蚀、光刻、溶胶-凝胶法、相分离和化学气相沉积法)被用于制备仿生超疏水表面。采用这些技术制备的表面具有精确的微纳结构,但这些技术多数存在工艺繁琐、条件苛刻、成本高和选材范围窄等问题,很难应用于实际的生产生活中。cn111500144a公开了一种纳米sio2接枝丙烯酸树脂的超疏水涂层,制备方法是:(1)向反应瓶中加入二氯甲烷溶剂和纳米sio2,超声分散均匀后加入三硫代碳酸酯、4-二甲氨基吡啶和1-乙基-(3-二甲基氨基丙基)碳酰二亚胺盐酸盐,置于恒温水浴锅中在30-40℃恒温下反应24-36h,将溶液减压蒸馏,使用甲醇洗涤固体产物并干燥,制备得到三硫代碳酸酯化纳米sio2。(2)向反应瓶中加入1,4-二氧六环溶剂、乳化剂op-10和十二烷基苯磺酸钠,以及甲基丙烯酸甲酯、丙烯酸丁酯和甲基丙烯酸,进行高速乳化过程,形成聚合单体乳液。(3)在氮气氛围中,向反应瓶中加入1/3体积的聚合单体乳液,加热至65-75℃,缓慢滴加引发剂偶氮二异丁腈的1,4-二氧六环溶液,匀速搅拌反应30-60min,再加入剩余2/3体积的聚合单体乳液、甲基丙烯酰氧基丙基三甲氧基硅烷和甲基丙烯酸十二氟庚酯,匀速搅拌反应20-30h,将溶液倒入成膜模具中,自然流延并干燥成膜,制备得到纳米sio2接枝丙烯酸树脂的超疏水防腐涂层。cn111534190a公开了一种双响应自修复超疏水涂层材料,包括:(a)至少一种为负载疏水性物质的聚多巴胺复合微球,(b)至少一种涂膜接触角大于90度的基体树脂,(c)非必须溶剂,(d)非必须粉体,(e)非必须助剂;各组分重量百分比为:负载疏水性物质的聚多巴胺复合微球1-50%,基体树脂10-80%,溶剂0-80%,粉体0-50%,助剂0-20%,其总重量满足100%;将载疏水性物质的聚多巴胺复合微球、基体树脂、溶剂0-80%和助剂0-20%共混来制备涂料,成膜后涂层的接触角大于150°、滚动角小于10°;当涂层受到环境破坏而失去超疏水性时,通过外界刺激,可使聚多巴胺复合微球中包覆的疏水性物质释放,实现超疏水涂层材料的自修复。但是上述专利的方法工艺复杂,成本高昂,而且在制备超疏水涂层时不能稳定地制备得到。因此,寻找一种简单易行且可实现大面积制备超疏水表面的方法是目前工业化实际应用亟须解决的重要问题。技术实现要素:为了克服现有技术中制备超疏水涂层工艺繁复,重复性不好的缺点,本发明利用聚合诱导自组装通过构筑层级结构制备超疏水纳米涂料。首先将低表面能的含氟单体通过raft聚合,得到大分子链转移剂,再与苯乙烯单体共聚,通过聚合诱导自组装方法原位生成具有不同纳米结构的聚合物的分散液。此悬浮聚合方法可通过控制单体比例、反应时间等因素一步法制得不同纳米尺度及形貌的聚合物微结构,如纳米微球、纳米线、囊泡以及更为复杂的微纳米结构。将不同尺寸及形貌的纳米颗粒按照一定配比混合,与水性固化交联剂、增强剂等助剂混合均匀后即可涂敷于待处理基材表面,形成稳定的具有层级结构的高强度聚合物超疏水薄膜。该方法操作简单,施工工艺灵活,可选择喷涂、辊涂、刷涂等多种涂敷方式。另外,该涂层可在金属、木材、混凝土、玻璃等多种基材表面实现超疏水性能。为实现上述目的,本发明采用如下技术方案:本发明还提供了一种具有微纳层级结构的超疏水涂料,包括如下原料:两种以上的不同形貌的聚合物的分散液,水性交联剂,溶剂;所述聚合物为核-壳结构,核为含有芳环的聚合物链段,壳为具有低表面能的聚合物链段。进一步地,所述超疏水涂料,包括如下重量份原料:总计30-50份的两种以上的不同形貌的聚合物的分散液,3-8份水性交联剂,40-60份溶剂。所述不同形貌的聚合物为核-壳结构,核为聚苯乙烯链段,壳为含氟的大分子链转移剂,聚合物形貌包括微球、纳米线、囊泡,多层复杂结构。所述聚合物微球的平均粒径为30-100nm,优选为40-60nm;所述聚合物纳米线的直径为30-100nm,优选为40-60nm,聚合物纳米线长度为2-50μm,优选为2-10μm;所述聚合物囊泡的直径200-500nm,优选为300-400nm;所述多层复杂结构的粒径为1-5μm。所述两种以上的不同形貌的聚合物的分散液中,任一一种形貌的聚合物和其他形貌的聚合物质量比值不超过3倍,优选不超过2倍。举例而言,若分散液中含有两种形貌的聚合物,所述两种不同形貌的聚合物的质量比为1:3-1:3,优选为1-2:1-2;若分散液中含有三种形貌的聚合物,所述三种不同形貌的聚合物的质量比为1:3-1:3:1-3,优选为1-2:1-2:1-2。优选地,所述超疏水涂料还加入1-3份附着力增强剂,所述附着力增强剂选自带有氨基的硅烷偶联剂,比如3-氨基丙基三甲氧基硅烷、氨丙基甲基二乙氧基硅烷、γ-二乙烯三胺丙基甲基二甲氧基硅烷、n-(β-氨乙基)-γ-氨丙基三甲氧基硅烷、3-氨基丙基三乙氧基硅烷、苯氨基甲基三甲氧基硅烷中的至少一种。本发明提供的超疏水涂料是通过构建不同微观层级结构,将不同纳米尺寸的聚合物,即聚合物纳米微球,聚合物纳米线,聚合物囊泡,聚合物多层复杂结构的分散液按照一定比例两两或多种混合实现,比如将形貌为纳米微球的聚合物分散液与形貌为纳米线的聚合物分散液混合,纳米线聚合物分散液与囊泡形分散液混合,纳米球的聚合物分散液和囊泡形分散液混合,纳米球的聚合物分散液和多层复杂结构的聚合物分散液,以及聚合物微球,聚合物纳米线,聚合物囊泡,聚合物多层复杂结构中任意三种以上的混合。只要能保证混合液中纳米聚合物形貌多样化、粒径分布覆盖纳米至微米尺度即可形成超疏水涂层。所述水性交联剂选自水性氨基树脂,优选为醚化氨基树脂,比如甲醚醚化氨基树脂(maprenalmf920、maprenalmf915、maprenalmf904、maprenalvmf3950、resimeneaq7550、resimene717、resimene730、resimene735、resimene745)、混醚化氨基树脂(maprenalmf927、maprenalmf905,resimene751、resimene757、resimenece7511),异丁醚化氨基树脂(maprenalmf580、maprenalmf590、maprenalmf650、maprenalmf800),正丁醚化氨基树脂(maprenalvmf3611、maprenalmf625、resimene750、resimene891、resimene7215)。所述溶剂为水或者醇类溶剂,或者醇水混合溶剂。所述醇类溶剂选自甲醇,乙醇,异丙醇。若为醇水混合溶剂,醇和水的质量比为1-2:1-2。所述不同形貌的聚合物的分散液,是通过可逆加成-断裂链转移自由基聚合反应制得,包括以下步骤:(1)制备含氟大分子链转移剂:含氟单体,丙烯酸及其衍生物在引发剂1,链转移剂存在下进行raft聚合得到含氟大分子链转移剂;(2)将步骤(1)所得含氟大分子链转移剂,苯乙烯,引发剂2继续进行raft聚合反应,反应结束后搅拌,通过聚合物的自组装得到聚合物分散液;通过调节苯乙烯的用量和/或调控反应时间分别得到不同形貌的核-壳结构聚合物的分散液。进一步地,在步骤(1)中所述含氟单体选自丙烯酸氟代烷基酯,氟代烷基聚醚丙烯酸酯,氟代烷基是碳原子数为1-6的部分氟代或者全氟代的烷基酯,丙烯酸氟代烷基酯包括丙烯酸三氟乙酯,丙烯酸四氟丙酯,丙烯酸五氟丙酯,丙烯酸六氟丁酯,丙烯酸六氟异丙酯,丙烯酸七氟丁酯,丙烯酸八氟戊酯,丙烯酸九氟己酯;所述氟代烷基聚醚丙烯酸酯包括其中n为1-10的整数。丙烯酸氟代烷基酯中的氟代烷基的碳链不易过长,否则会影响含氟大分子链转移剂可以和苯乙烯单体在醇溶剂中混溶,这是后面raft悬浮聚合的前提条件。所述丙烯酸衍生物选自(甲基)丙烯酸酯,比如(甲基)丙烯酸甲酯,(甲基)丙烯酸乙酯,(甲基)丙烯酸丙酯,(甲基)丙烯酸羟乙酯,(甲基)丙烯酸羟丙酯。步骤(1)中,溶剂为水和氧杂环烷烃按照质量比6-8:2-4的复配。所述氧杂环烷烃选自四氢呋喃,氧杂环丁烷,1,3-二氧戊环,1,4-二氧六环。步骤(1)的反应条件是在惰性气氛下,60-80℃反应2-3h。所述引发剂1和引发剂2没有特别的限定,常规能用于raft反应的自由基引发剂即可,比如偶氮二异丁腈,4,4’-偶氮二(4-氰基戊酸),2,2'-氮杂双(2-咪唑啉)二盐酸盐,2,2'-偶氮二异丁基脒二盐酸盐,2,2'-偶氮二(2-甲基丙腈),1,1’-偶氮腈基环己烷,过硫酸钾。所述链转移剂为双硫酯化合物或三硫酯化合物,比如2-氰基-2-丙基苯并二硫,2-(苯基硫代甲酰硫基)丙酸,(2-乙氧基二硫代酸酯基)醋酸乙烯酯,4-氰基-4-[[(十二烷硫基)硫酮甲基]硫基]戊酸,α-二硫代萘甲酸异丁腈酯,4-氰基-4-乙基三硫代戊酸,s,s'-双(2-甲基-2-丙酸基)三硫代碳酸酯,2-(乙基三硫代碳酸酯基)-2-甲基丙酸。优选为带有氰基,三硫酯基,羧基的链转移剂,比如4-氰基-4-乙基三硫代戊酸,4-氰基-4-[[(十二烷硫基)硫酮甲基]硫基]戊酸。优选地,引发剂的用量为单体总摩尔量的0.5-1‰;所述链转移剂的用量为单体总摩尔量的2-6%。所述单体总摩尔量是含氟单体和丙烯酸衍生物物质的量的总和。更为优选地,所述引发剂1为4,4’-偶氮二(4-氰基戊酸),用量为单体总摩尔量的0.75-0.9‰;所述链转移剂为4-氰基-4-[[(十二烷硫基)硫酮甲基]硫基]戊酸,用量为单体总摩尔量的3-5%。发明人发现,以4,4’-偶氮二(4-氰基戊酸)作为引发剂,以4-氰基-4-[[(十二烷硫基)硫酮甲基]硫基]戊酸作为链转移剂,配合适当的用量,用于raft聚合,能够得到分子量可控的大分子链转移剂,分子量分布极窄,pdi(mw/mn)为1.05-1.3。更有利于得到规格,形貌,分子量及其分布非常接近的大分子链转移剂,进而在步骤(2)的苯乙烯非均相的raft反应的成核过程中,聚苯乙烯的链段可以同步地稳定成核,所得到的核-壳结构的聚合物分子量,尺寸以及形貌同步稳定增长,最终通过控制反应时间能够得到不同形貌的聚合物的分散液,分散液中的聚合物形貌,尺寸基本一致。可以方便地通过后续的不同形貌聚合物分散液在水性交联剂的作用下制备得到超疏水涂料。进一步地,在步骤(2)中,含氟大分子链转移剂的用量为苯乙烯单体摩尔量的0.1-0.3‰,引发剂2的用量为苯乙烯单体摩尔量的0.01-0.05‰,苯乙烯单体在溶剂中的浓度控制在6-10m,优选为7-8m。步骤(2)的搅拌速度和搅拌时间没有特别的限定,只要能够充分让分散液中的聚合物自组装为一定形貌和尺寸即可。在本发明的一个具体实施方式中,搅拌速度为300-500r/min,搅拌时间为12-24h。步骤(2)的raft聚合反应,溶剂没有特别的限定,只要是大分子链转移剂和苯乙烯单体的良溶剂,并且是聚苯乙烯的不良溶剂即可,在本发明的一个实施方式中,溶剂选自异丙醇,乙酸乙酯,正丁醇,四氢呋喃,乙醚,异丙醚,三氯甲烷,二氯甲烷中的至少一种。步骤(2)的raft聚合反应,是在惰性气氛,搅拌条件下,加热体系至80-110℃进行反应。更进一步地,在步骤(2)中,还加入带有醛基的单体,和胺类物质。所述带有醛基的单体为3-乙烯基苯甲醛;所述胺类物质选自多元烷基胺,优选为乙二胺,丙二胺,丙三胺,丁二胺中的至少一种。进一步优选地,所述带有醛基的单体的用量为苯乙烯单体摩尔量的3-10%,所述胺类物质的用量为苯乙烯单体的1-5‰。加入醛基的单体,和胺类物质的目的是醛基和胺基会发生缩合反应,加强含氟单体的聚合物和苯乙烯聚合物之间的交联程度,以使得形成的不同形貌的含氟复合物形状锚定下来,所得分散液稳定,可以长时间保持稳定的形貌。利用raft可以方便地制备得到不同形貌的聚合物分散液,在本发明的一个优选试试方式中,步骤(2)中,加入苯乙烯,引发剂2后,通过调控聚合反应时间的长短,即可获得不同形貌的聚合物分散液。由于raft是一个稳定,可控的,分子量增加基本呈线性增长的可控活性聚合,利用raft的特点,聚苯乙烯高分子链段的增长是随着反应时间线性增加的,因此,在不同时间内即可得到不同形貌,不同粒径尺寸的聚合物分散液。调控聚合反应时间是使raft聚合反应结束,中止聚合反应的方式是本领域所熟知的,比如降温(自然冷却或者冰水浴冷却),加入阻聚剂等方式。本发明通过控制聚合反应时间的不同,就可以得到不同形貌的聚合物分散液。举例而言,在步骤(2)中,在苯乙烯浓度为7-8m,引发剂2的用量为苯乙烯单体摩尔量的0.01-0.05‰的条件下,进行含氟大分子链转移剂和苯乙烯的raft反应,反应1.5-3小时得到聚合物微球;反应4-6小时得到聚合物纳米线;反应7-8小时得到聚合物囊泡;反应9小时以上得到聚合物多层复杂结构。这里的反应时间实在一定的聚合条件下得到的,在不同单体浓度,引发剂用量,反应温度等条件下影响下,得到不同形貌聚合物分散液所需要的反应时间是不同的,因此本领域技术人员应当理解,上述不停反应时间得到不同形貌的聚合物分散液,是在特定条件下优选得到的一种可以获得稳定,形貌单一,聚合物分子量分布窄的聚合物分散液;但上述反应时间的限定,不应理解是对本发明的一种限制,只是一种具体情况下的举例,本领域技术人员在本发明思路指导下,是容易根据在不同的反应条件下,比如调控不同的反应时间,以得到不同的形貌的聚合物分散液。本发明利用聚合诱导自组装技术,制备具有高浓度的不同纳米结构的自组装聚合物,固含质量分数可高达30%以上,优选实施例可以达到接近50%。方法工艺简单,操作方便,可实现一步法制备不同尺寸及形貌的纳米自组装体结构,其聚合物形貌通常包括微球、纳米线、囊泡等,为实现层级结构的构建提供了新的方法和思路。本发明还提供了所述超疏水涂料的制备方法,包括以下步骤:将两种以上的不同形貌的聚合物的分散液按照一定质量比混合均匀,加入水性交联剂和溶剂,可选地,还可以加入附着力增强剂,搅拌混合均匀即得超疏水涂料。本发明还提供了所述超疏水涂料的用途,是将超疏水涂料涂覆在需要进行处理的基材表面,干燥后加热固化,即在基材的表面形成超疏水涂层;优选地,需要进行处理的基材表面在涂覆超疏水涂料之前,先经过表面活性剂或清洗剂清洗。所述需要进行处理的基材包括但不限于织物,玻璃,电缆,混凝土,木板,纸板,水泥,金属,陶瓷;所述涂覆的手段包括但不限于喷涂,刷涂,辊涂,浸涂。进一步地,所述干燥是在室温下干燥4-10h,带基材表面基本无溶剂为止;所述加热固化是在90-150℃下固化2-10min。经过本发明超疏水涂料涂覆的基材表面,通过涂覆、干燥、固化的简单步骤即可达到超疏水效果,其与水的接触角大于150°,滚动角小于10°,具有有益的超疏水性能。本发明是利用具有一定微观形貌的聚合物分散液,通过可逆加成-断裂链转移自由基聚合(raft)中的非均相悬浮聚合将低表面能的含氟丙烯酸酯单体、醇溶性丙烯酸酯单体与苯乙烯通过化学键合形成的有机聚合物纳米结构,形貌包括纳米微球、纳米线、囊泡,多层复合结构等。将不同尺寸和形貌的有机聚合物纳米分散液按照一定比例混合后,与水性交联剂、助剂等配制得到的涂料涂敷于基材表面,可在其表面形成一层致密的聚合物薄膜,该薄膜具有微纳米层级结构,具有超疏水、耐磨擦、耐酸碱,附着力高的优越性能,克服了传统无机纳米材料超疏水涂层易脱落,机械性能差,成本高等缺陷。另一方面,以醇和水混合物为溶剂更加节能环保,易于施工,适合商业化推广。有益效果本发明具有微纳米层级结构的超疏水涂层生产制备工艺简单,反应条件温和,可适用于多种不同的基底和规模化生产,热稳定性和化学稳定性好。采用含氟聚合物纳米粒子代替氟化硅氧烷纳米材料,大大降低超疏水涂料的成本。另外,以醇和水混合物为溶剂更加节能环保,易于施工,适合商业化推广,在超疏水领域具有重要的潜在应用价值。附图说明图1是本发明实施例的raft聚合反应形成核-壳结构聚合物自组装为不同形貌的聚合物分散液的示意图。图2是实施例1制备得到的不同形貌聚合物分散液的电镜照片。图3是不同形貌的聚合物分散液和交联剂等涂覆在基材表面形成超疏水涂层的示意图。图4是实施例1所得超疏水涂层扫描电镜照片。图5是实施例1玻璃表面制备层级结构聚合物超疏水涂层与水的接触角。图6是实施例1制备得到超疏水涂料在各种基材形成超疏水涂层后的疏水效果。图7是实施例5中聚合物纳米分散液的电镜照片。图8是实施例6中聚合物纳米分散液的电镜照片。图9是实施例8中聚合物纳米分散液的电镜照片。具体实施方式以下以具体实施例对本发明的超疏水涂料做进一步的解释和说明,本发明实施例中所用物质若未有特殊说明,均为商购的试剂。实施例1(1)制备含氟大分子链转移剂含氟大分子链转移剂是通过可逆加成-断裂链转移自由基聚合实现,具体操作如下:将含氟单体丙烯酸三氟乙酯(1.2g,7.8mmol),丙稀酸羟乙酯(1.7g,15mmol),丙稀酸(1.1g,15mmol),引发剂4,4’-偶氮二(4-氰基戊酸)(9mg,0.032mmol),链转移剂4-氰基-4-[[(十二烷硫基)硫酮甲基]硫基]戊酸(0.65g,1.6mmol),混合溶剂水/1,4-二氧六环(80:20/m:m,40g)加入100ml圆底烧瓶中,通氮气20分钟后,密封置于60℃磁力搅拌器中搅拌2小时,反应结束后,得到的混合溶液冷却后将多余溶剂蒸馏去除,最终得到的含氟大分子链转移剂用于制备多形貌聚合物纳米分散液,通过gpc测试含氟大分子链转移剂的重均分子量mw为10800g/mol,pdi(mw/mn)为1.07。(2)多形貌聚合物纳米分散液制备多形貌聚合物分散液是采用raft可控自由基聚合方法中的非均相悬浮聚合反应,通过聚合诱导自组装原理实现。具体操作如下:将上述含氟大分子链转移剂(0.54g,0.05mmol),苯乙烯单体(25g,0.24mol),3-乙烯基苯甲醛(1.67g,12.6mmol),引发剂1,1’-偶氮腈基环己烷(1.23mg,0.005mmol)溶解于异丙醇,使苯乙烯浓度为7.5m,通氮气10分钟后,放置于90℃磁力搅拌器中搅拌反应2小时,用冰水浴冷却降温使聚合反应中止,反应结束后,减压将未参加反应的单体抽出,加入1,3-丙二胺(37mg,0.5mmol)室温搅拌24小时,即得到形貌为球形的聚合物纳米分散液,聚合物微球的粒径为40-50nm。相同方法反应5小时,则得到形貌为线形的聚合物纳米分散液,聚合物纳米线的直径50-60nm,长度可达微米级;如若反应7小时,则得到形貌为囊泡形的聚合物纳米分散液,聚合物囊泡的直径为220-260nm;如若反应9小时以上,则得到形貌更为复杂的不规则囊泡分散液,粒径可达数微米。所得聚合物分散液的固含量可以达到40%以上。3)制备含有多形貌聚合物微粒的超疏水涂料将上述制备的球形聚合物纳米分散液与形貌为线形的聚合物纳米分散液按照质量比1:1混合并室温搅拌30分钟。将50份配制好的聚合物分散液混合液,5份水性交联剂maprenalmf920和44份醇水混合溶剂(乙醇:水=1:1,v/v),搅拌情况下,缓慢滴加1份附着力增强剂kh-550并持续搅拌30分钟,即可得到聚合物超疏水涂料。4)织物纤维表面制备层级结构聚合物超疏水涂层织物纤维表面制备具有层级结构的聚合物超疏水涂层是通过喷涂工艺实现的。具体操作如下:纯棉织物纤维首先用十二烷基硫酸钠溶液(1wt%)浸泡清洗1小时,70℃真空干燥箱中干燥12小时。室温下将该溶液用高容积低压喷枪均匀喷涂于上述处理好的织物表面,室温干燥6小时后,120℃固化5分钟,即可达到超疏水涂层,其厚度约20μm,其接触角159°,滚动角3°。图1是本发明实施例的raft聚合反应形成核-壳结构聚合物自组装为不同形貌的聚合物分散液的示意图。式中高分子n:5-20,m:10-50,p:10-50,a:100-1000,b:0-10。具体是含氟单体和丙烯酸衍生物在引发剂和链转移剂作用下发生raft聚合合成含氟大分子链转移剂,该大分子链转移剂仍还有三硫酯基团,可以再后续的和苯乙烯聚合成核的反应中继续作为raft试剂,最后聚合得到聚苯乙烯为核,大分子含氟链转移剂为壳的核-壳结构化合物。通过调控反应时间,因成核的聚苯乙烯分子量不同,链的长短不同进而形成不同形貌的聚合物分散液。图2是实施例1制备得到的不同形貌聚合物分散液的电镜照片。从左到右分别是聚合物纳米微球,纳米线、囊泡、聚合物多层复杂结构。图4是实施例1所得超疏水涂层扫描电镜照片,可以看出是纳米线和球的微纳米层级复合结构。实施例2(1)制备含氟大分子链转移剂同实施例1步骤(1)(2)多形貌聚合物纳米分散液制备多形貌聚合物分散液是采用可控自由基聚合方法中的非均相悬浮聚合反应,通过聚合诱导自组装原理实现。具体操作如下:将上述含氟大分子链转移剂(0.54g,0.05mmol),苯乙烯单体(25g,0.24mol),3-乙烯基苯甲醛(1.67g,12.6mmol),引发剂1,1’-偶氮腈基环己烷(1.23mg,0.005mmol)溶解于异丙醇,使苯乙烯浓度为7m,通氮气10分钟后,放置于90℃磁力搅拌器中搅拌5小时,用冰水浴冷却降温使聚合反应中止,反应结束后,减压将未参加反应的单体抽出,加入1,3-丙二胺(37mg,0.5mmol)室温搅拌16小时,即得到形貌为线形的聚合物纳米分散液,聚合物纳米线的直径45-65nm,长度可达微米级;相同方法将反应时间延长至8小时,则得到形貌为囊泡形的聚合物纳米分散液,聚合物囊泡的直径240-320nm。3)制备含有多形貌聚合物微粒的超疏水涂料将上述制备的线形聚合物纳米分散液与形貌为囊泡的聚合物纳米分散液按照质量比2:1混合并室温搅拌30分钟。将40份配制好的聚合物分散液混合液,4份水性交联剂maprenalmf920和55份醇水混合溶剂(乙醇:水=1:1,v/v)混合均匀,搅拌情况下,缓慢滴加1份附着力增强剂并持续搅拌30分钟,即可得到聚合物超疏水涂料。4)玻璃表面制备层级结构聚合物超疏水涂层玻璃表面制备具有层级结构的聚合物超疏水涂层是通过喷涂工艺实现的。具体操作如下:玻璃板基材首先在室温下10%的techogentt105清洗剂中超声清洗1小时,随后用去离子水清洗并氮气干燥。室温下将步骤(3)得到的超疏水涂料用高容积低压喷枪均匀喷涂于上述处理好的织物表面,室温干燥6小时后,120℃固化5分钟,即可达到超疏水效果,其接触角154°,滚动角为5°。实施例3其他步骤和条件和实施例1相同,区别在于步骤(2)中制备核-壳结构聚合物时,反应3小时,得到形貌为球形的聚合物纳米分散液,聚合物微球的粒径为50-60nm;反应6小时,得到形貌为线形的聚合物纳米分散液,聚合物纳米线的直径55-65nm,长度为微米级。最终得到在玻璃表面的超疏水涂层其接触角156°,滚动角为3°。实施例4其他步骤和条件和实施例1相同,区别在于步骤(2)中制备核-壳结构聚合物时,反应1.5小时,得到形貌为球形的聚合物纳米分散液,聚合物微球的粒径为35-43nm;反应4小时,得到形貌为线形的聚合物纳米分散液,聚合物纳米线的直径45-55nm,长度为微米级。最终得到在玻璃表面的超疏水涂层其接触角153°,滚动角为5°。实施例5其他步骤和条件和实施例1相同,区别在于步骤(2)中制备核-壳结构聚合物时,反应2小时得到形貌为球形的聚合物纳米分散液,替换为反应3.5小时得到聚合物纳米分散液,其电镜照片见图7,同时含有球形聚合物和线形聚合物,所述球形聚合物粒径为45-65nm,所述线形聚合物的直径为30-40nm,长度约500-800nm。最终得到在玻璃表面的超疏水涂层其接触角147°,滚动角为7°。实施例6其他步骤和条件和实施例1相同,区别在于步骤(2)中制备核-壳结构聚合物时,反应5小时,得到形貌为线形的聚合物纳米分散液,替换为反应6.5小时,得到的聚合物纳米分散液,其主要自组装的形貌为纳米线,纳米线的直径50-70nm,长度为微米级,还含有部分粒径位130-170nm左右的囊泡形态的聚合物,其电镜照片见图8。最终得到在玻璃表面的超疏水涂层其接触角145°,滚动角为8°。实施例7其他步骤和条件和实施例1相同,区别在于步骤(1)中,引发剂替换为等摩尔量的2,2'-氮杂双(2-咪唑啉)二盐酸盐va-044。最终所得含氟的大分子链转移剂重均分子量mw为12600g/mol,pdi=1.26。步骤(2)中以相同的反应时间制备得到球形和线形的聚合物纳米分散液,即反应2小时得到聚合物微球,其粒径为40-60nm;反应5小时,得到形貌为线形的聚合物纳米分散液,聚合物纳米线的直径220-310nm,长度为微米级。所得涂料最终得到在玻璃表面的超疏水涂层其接触角151°,滚动角为8°。实施例8其他步骤和条件和实施例1相同,区别在于步骤(2)中不加入3-乙烯基苯甲醛。实施例8没有加入3-乙烯基苯甲醛,raft反应结束后,也由于缺少了醛基和胺基反应形成的交联作用,得到的不同形貌的嵌段聚合物会溶于涂料配制过程中的四氢呋喃、甲苯、丙酮等溶剂或者助剂,会破环聚合物自组装的形貌,得到的只是微球,不能得到纳米线和囊泡等形貌。实施例8所得聚合物分散液的电镜照片如图9所示。实施例9其他步骤和条件和实施例1相同,区别在于步骤(3)中,不加入附着力增强剂kh-550。所得涂料最终得到在玻璃表面的超疏水涂层其接触角156°,滚动角为4°。应用例1对本发明实施例最终所得涂层进行疏水、硬度和附着力的测试,结果如下表1所示:1.硬度测试是采用铅笔硬度测试,测试方法参照gb6739—86。2.附着力是参照iso4624-2004进行,使用划格测试器,将试样涂于样板上,干燥16小时后,用划格器平行拉动3-4cm,切刀间隙2mm,应切穿漆膜至底材;然后用同样的方法与前者垂直,形成许多小方格。使用目视或者放大镜对照标准进行对比定级。其分级的标准描述为:0-切割边缘完全平滑,无一格脱落1-交叉处有少许涂层脱落,受影响面积不能明显大于5%2-在切口交叉处或沿切口边缘有涂层脱落,影响面积为5%-15%3-涂层沿切割边缘部分或全部以大面积脱落受影响的交叉切割面积在15%-35%5-沿边缘整条脱落,有些格子部分或全部脱落,受影响面积35%-65%表1应用例2为了测试所得超疏水涂层的的耐磨性,耐候性,进行以下试验,将试验后的超疏水涂层重新进行接触角和滚动角的测试,结果如下表2所示。1.耐磨试验:在500g砝码压力下,以砂纸边缘为界,在320目砂纸上反复摩擦200次,测试摩擦后的接触角。2.刮伤试验:用尖锐小刀,在涂层表面来回刮1000次,测试接触角。3.耐酸试验:用5wt%hcl浸泡30min后,测试接触角。4.耐碱试验:用5wt%naoh浸泡30min后,测试接触角。表2耐磨试验刮伤试验耐酸试验耐碱试验实施例1156°157°159°159°实施例2151°152°153°153°实施例3152°154°154°155°实施例4149°150°152°151°实施例5139°144°143°144°实施例6132°143°140°143°实施例7135°147°148°148°实施例8142°139°125°129°实施例9139°115°142°145°以上详细描述了本发明的优选实施方式,但是,本发明并不限于此。在本发明的技术构思范围内,可以对本发明的技术方案进行多种简单变型,包括各个技术特征以任何其它的合适方式进行组合,这些简单变型和组合同样应当视为本发明所公开的内容,均属于本发明的保护范围。当前第1页1 2 3 
起点商标作为专业知识产权交易平台,可以帮助大家解决很多问题,如果大家想要了解更多知产交易信息请点击 【在线咨询】或添加微信 【19522093243】与客服一对一沟通,为大家解决相关问题。
此文章来源于网络,如有侵权,请联系删除



tips