一种抗海洋生物污损涂料及其制备方法与流程



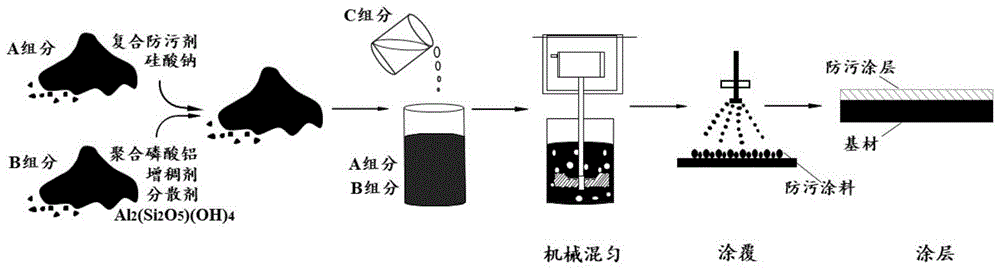
本发明属于涂料技术领域,具体涉及一种抗海洋生物污损涂料及其制备方法,可用于滨海电厂处于海水环境下的工程结构表面抗海洋生物污损防护。
背景技术:
海洋生物污损是指海洋环境中微生物、植物、动物在被海水浸没的设施表面不断粘附、生长、繁殖而形成的生物附着或生物腐蚀。海洋生物污损已成为人类开发、利用海洋资源所面临的全球性问题,其对港口和滨海电厂水下设施等造成了巨大的技术挑战和经济损失。据估计,每年因海洋生物污损所造成的经济成本高达65亿美元。海洋污损生物种类较多,归纳起来可分为三类:(1)微污损生物(细菌类、真菌类、硅藻微小海藻等);(2)软性污损生物(大型海藻等);(3)硬性污损生物(贝类、藤壶、苔藓虫类等)。相关资料显示,当材料浸入海水中,其表面会很快吸附一层由多聚糖、蛋白质、糖蛋白等组成的有机物膜;然后由单细胞微生物如细菌、硅藻和原生动物等相继在有机物膜上附着并分泌胞外代谢产物(eps)形成微生物膜;随后其它原核生物、真菌、藻类孢子以及大型污损生物幼虫在膜中发育生长;最后形成复杂的生物群落和大型污损生物层。
目前,针对于海水下静态设施的防污技术归纳起来可分为三种:(1)物理滤沥、清除法,(2)直接化学灭活法,(3)防污涂层涂覆。物理滤沥、清除法主要是通过机械设备来清除污损物,效率低且成本高昂;化学直接灭活法是直接向防护对象附近的海水中释放具有强氧化性和毒理性的化学试剂,除污损效果好,但易造成海水环境污染;防污涂层涂覆是研究最早,也是目前应用最广泛的抗海洋生物附着的方法。通常,防污涂料主要由高分子树脂、防污剂、溶剂等组成。但传统有机型防污涂料污染海水环境,分解产物易造成“微塑料”污染,且在流动海水冲蚀条件下防污寿命低。
技术实现要素:
本发明的目的在于提供一种抗海洋生物污损涂料,具有高效耐久抗海洋生物污损的特点,并且制备工艺简单、对环境友好,以解决现有技术存在的问题。
聚合磷酸铝具有很好的耐酸性,对大多数的酸均有耐腐蚀稳定性。聚合磷酸铝也具有良好的粘结能力,聚合磷酸铝优选三聚磷酸铝。
一种抗海洋生物污损涂料,主要包括以下重量百分比的组分:硅酸钠15~22%、复合防污剂15~25%、聚合磷酸铝10~14%、增稠剂1~2%、al2(si2o5)(oh)415~20%、分散剂1~3%、溶剂水余量。
抗海洋生物污损涂料在使用涂覆到基材表面前不把聚合磷酸铝和硅酸钠放在一起,要分开放置。
al2(si2o5)(oh)4作为无机填料加入配方中,能给涂层提供强度,提高涂层耐磨性能。在硅酸钠与聚合磷酸铝固化而成的膜层包裹下,协同形成具有一定溶蚀性的无机薄膜。
进一步的,所述硅酸钠、聚合磷酸铝、al2(si2o5)(oh)4的最佳比例为3:2:4。
进一步的,所述复合防污剂为cu2o、cuo、tio2、ag2o中的一种或一种以上的混合物。其中,cu2o和tio2可与吸附在其表面的h2o和o2形成活性很强的羟基自由基和活性氧,这种自由基具有很强的氧化和分解能力,能破坏有机物中c—c、c—h、c—o、o—h键,凝固微生物的蛋白质,对海洋生物细胞膜产生酶抑制作用,从而灭杀附着在其表面的海洋生物,其中对藤壶、贝类、苔藓虫等无脊椎动物特别有效。cu2o、cuo、ag2o的离子可与半胱氨酸的—sh基反应,导致藻类中以—sh基为活性点的酶失活,同时还能对藻类的细胞壁、细胞膜的结构造成不可逆损伤,有效防止藻类附着。
进一步的,所述复合防污剂中位粒径在80~150nm范围,粒径太大,比表面积就会过小,起不到吸附—sh、—cooh等基团的作用;粒径过小,价格高,不经济。复合防污剂中位粒径在80~150nm时具有极大的比表面积,且表面还原电势高,可以吸附细菌体内酶蛋白分子中的—sh、—cooh等基团,并与之反应,阻碍蛋白质的合成和能量来源,破坏了细菌的细胞膜,致使细菌死亡,从而有效防止海洋生物附着、生长。同时,在同样的含量系,纳米颗粒防污剂更有利于在海水条件下保持较高的有效离子浓度。
进一步的,所述增稠剂为海藻酸钠、羟乙基纤维素一种或两种混合,增稠剂的添加可使浆液粘稠度增加,便于涂刷粘结,且使涂层易于成膜;所述分散剂为木质素磺酸钙。
进一步的,所述复合防污剂包括最佳质量比为2:1:1:1的cu2o、cuo、tio2和ag2o。多种离子的协同作用可以有效地对多种海洋生物产生灭活作用。
进一步的,所述硅酸钠和复合防污剂的最佳比例为3:5。
一种抗海洋生物污损涂料的制备方法,包括以下工艺步骤:
(1)按比例称取硅酸钠和复合防污剂,混合搅拌均匀,得到a组分。
(2)按比例称取聚合磷酸铝、增稠剂、al2(si2o5)(oh)4、分散剂,混合搅拌均匀,得到b组分。
(3)将a组分和b组分分别包装,使用时再机械搅拌混匀,按比例加入c组分机械搅拌混匀,即可得到环保的新型抗海洋生物污损涂料;
(4)上述抗海洋生物污损涂料主要用于陶瓷基材、混凝土基材等表面。具体应用时,将抗海洋生物污损涂料均匀涂覆在基材表面,待其自然固化成型即可得到具有离子缓释效果的抗海洋生物污损涂层。
进一步的,步骤(4)所述涂覆方法为涂刷法或喷涂法。
与现有技术相比,本发明通过在工程基材表面涂覆高效持久的抗污损功能、耐腐蚀、对环境友好的抗污损涂料,达到预防基材浸蚀和防止海洋生物附着污损的目的。本发明以硅酸钠作为粘结材料,通过与聚合磷酸铝的反应,辅以无机填料al2(si2o5)(oh)4形成具有一定溶蚀性的无机薄膜,在海水冲蚀下,复合防污剂随着无机薄膜的可控溶蚀,不断释放出足够浓度的铜、银等离子,有效杀菌寿命长,对环境友好无害,多种防污剂混合添加,互相协同作用,有效防治多种海洋生物侵袭。本发明抗海洋生物污损涂料还可对混凝土微小裂缝进行有效修复,进而提高混凝土抗渗能力,具有很好的实用价值。
附图说明
图1是本发明的抗海洋生物污损涂料制备工艺流程图;
图2是本发明的抗海洋生物污损涂层结构示意图,其中1-防污涂层,2-基材。
具体实施方式
为使本发明的目的、技术方案和优点更加清楚,下面将结合附图对本发明作进一步地详细描述。
实施例1:
按比例称取硅酸钠15g和中位粒径80nm的复合防污剂25g混合搅拌均匀,复合防污剂包括cu2o10g、cuo5g、tio25g、ag2o5g,得到a组分;按比例称取聚合磷酸铝10g、增稠剂海藻酸钠1g、羟乙基纤维素1g,al2(si2o5)(oh)420g、分散剂木质素磺酸钙3g,混合搅拌均匀,得到b组分;将a组分和b组分机械搅拌混匀,按比例加入c组分水25g,机械搅拌混匀,得到抗海洋生物污损涂料。
将所得的抗海洋生物污损涂料均匀涂刷在陶瓷基材表面,待其自然固化成型后,在陶瓷基体表面形成均匀、致密的涂层,可有效抗海洋生物污损,保护海水浸没结构表面不受海洋生物侵袭。得到的抗海洋生物污损涂层在2年左右溶蚀掉。
实施例2:
按比例称取硅酸钠17g和中位粒径120nm的复合防污剂22g混合搅拌均匀,复合防污剂包括cu2o10g、tio26g、ag2o6g,得到a组分;按比例称取聚合磷酸铝11g、增稠剂海藻酸钠1g、羟乙基纤维素0.6g、al2(si2o5)(oh)418g、分散剂木质素磺酸钙2.4g,混合搅拌均匀,得到b组分;将a组分和b组分机械搅拌混匀,按比例加入c组分水28g,机械搅拌混匀,得到抗海洋生物污损涂料。
将所得的抗海洋生物污损涂料均匀涂刷在陶瓷基材表面,待其自然固化成型后,在陶瓷基体表面形成均匀、致密的涂层,可有效抗海洋生物污损,保护海水浸没结构表面不受海洋生物侵袭。得到的抗海洋生物污损涂层在2年左右溶蚀掉。
实施例3:
按比例称取硅酸钠20g和中位粒径120nm的复合防污剂18g混合搅拌均匀,复合防污剂包括cu2o9g、ag2o9g,得到a组分;按比例称取聚合磷酸铝13g、增稠剂海藻酸钠1.4g、al2(si2o5)(oh)416g、分散剂木质素磺酸钙1.6g,混合搅拌均匀,得到b组分;将a组分和b组分机械搅拌混匀,按比例加入c组分水30g,机械搅拌混匀;得到抗海洋生物污损涂料。
将所得的抗海洋生物污损涂料喷涂在混凝土基材表面,待其自然固化成型后,在混凝土基体表面形成均匀、致密的涂层,可有效抗海洋生物污损,保护海水浸没结构表面不受海洋生物侵袭。得到的抗海洋生物污损涂层在2年左右溶蚀掉。
实施例4:
按比例称取硅酸钠22g和中位粒径150nm的cu2o15g混合搅拌均匀,得到a组分;按比例称取聚合磷酸铝14g、增稠剂羟乙基纤维素1g、al2(si2o5)(oh)415g、分散剂木质素磺酸钙1g,混合搅拌均匀,得到b组分;将a组分和b组分机械搅拌混匀,按比例加入c组分水32g,机械搅拌混匀;得到抗海洋生物污损涂料。
将所得的抗海洋生物污损涂料喷涂在混凝土基材表面,待其自然固化成型后,在混凝土基体表面形成均匀、致密的涂层,可有效抗海洋生物污损,还能阻隔减缓海水对基体的腐蚀。得到的抗海洋生物污损涂层在2年左右溶蚀掉。
对比例1:
按比例称取硅酸钠15g和中位粒径80nm的复合防污剂25g混合搅拌均匀,复合防污剂包括cu2o10g、cuo5g、tio25g、ag2o5g,得到a组分;再按比例加入c组分水15g,机械搅拌混匀,得到抗海洋生物污损涂料。
对比例2:
按比例称取硅酸钠15g和中位粒径80nm的复合防污剂25g混合搅拌均匀,复合防污剂包括cu2o10g、cuo5g、tio25g、ag2o5g,得到a组分;按比例称取聚合磷酸铝10g、增稠剂海藻酸钠1g、羟乙基纤维素1g,分散剂木质素磺酸钙3g,混合搅拌均匀,得到b组分;将a组分和b组分机械搅拌混匀,按比例加入c组分水20g,机械搅拌混匀,得到抗海洋生物污损涂料。
对比例3:
称取中位粒径80nm的复合防污剂25g混合搅拌均匀,复合防污剂包括cu2o10g、cuo5g、tio25g、ag2o5g,得到a组分;按比例称取聚合磷酸铝25g、增稠剂海藻酸钠1g、羟乙基纤维素1g,al2(si2o5)(oh)420g、分散剂木质素磺酸钙3g,混合搅拌均匀,得到b组分;将a组分和b组分机械搅拌混匀,按比例加入c组分水25g,机械搅拌混匀,得到抗海洋生物污损涂料。
对比例4:
将市场购买的kp-1与中位粒径80nm的复合防污剂25g、增稠剂海藻酸钠1g、羟乙基纤维素1g、分散剂木质素磺酸钙3g,混合搅拌均匀,得到抗海洋生物污损涂料。其中复合防污剂包括cu2o10g、cuo5g、tio25g、ag2o5g。
将实施例1-4及对比例1-4的抗海洋生物污损涂料均匀的涂刷在陶瓷基材表面,涂层厚度为500μm,进行性能测试对比,如表1所示。其中,防污离子释放率、海洋生物附着面积、涂层失重量和抗污损性能测试方法为:将涂刷了抗海洋生物污损涂料的陶瓷基材浸于距海平面3米的海水中12个月后观察、测试。综合抗污损性能主要考虑:防污离子释放率、污损失重两个因素。
表1实施例1-4及对比例1-4的抗海洋生物污损涂料的性能对比
探索实验
1、复合防污剂的组分及比例探索
(1)将复合防污剂改为cu2o15g、tio25g、ag2o5g,其它的同实施例1。
(2)将复合防污剂改为cuo15g、tio25g、ag2o5g,其它的同实施例1。
(3)将复合防污剂改为cu2o10g、cuo5g、ag2o10g,其它的同实施例1。
(4)将复合防污剂改为cu2o10g、cuo5g、tio210g,其它的同实施例1。
(5)将复合防污剂改为cu2o6.25g、cuo6.25g、tio26.25g、ag2o6.25g,其它的同实施例1。
将涂刷了抗海洋生物污损涂料的陶瓷基材浸于距海平面3米的海水中12个月后观察、测试。(1)-(5)防污离子释放率(个/cm3)分别为:320、218、325、316、296。发现涂层形成的无机薄膜的抗污损性能均不及实施例1。
2、硅酸钠、聚合磷酸铝、al2(si2o5)(oh)4的最佳比例探索
硅酸钠、聚合磷酸铝、al2(si2o5)(oh)4的比例分别设为1:1:1、2:1:3、4:1:3,其它同实施例1。发现涂层形成的无机薄膜的的附着力、耐磨性能、溶蚀性等综合性能均不及实施例1。
3、所述硅酸钠和复合防污剂的最佳比例探索
将硅酸钠和复合防污剂的比例控制为1:1、2:1、1:2。其它同实施例1。发现溶蚀性、抗污性等综合性能均不及实施例1。
以上所述实施例仅表达了本发明的几种实施方式,其描述较为具体和详细,但并不能因此而理解为对发明专利范围的限制。应当指出的是,对于本领域的普通技术人员来说,在不脱离本发明构思的前提下,还可以做出若干变形和改进,这些都应落入本发明的保护范围。
起点商标作为专业知识产权交易平台,可以帮助大家解决很多问题,如果大家想要了解更多知产交易信息请点击 【在线咨询】或添加微信 【19522093243】与客服一对一沟通,为大家解决相关问题。
此文章来源于网络,如有侵权,请联系删除


