一种陶瓷用黑色色料、制备工艺及使用其的陶瓷砖的制作方法



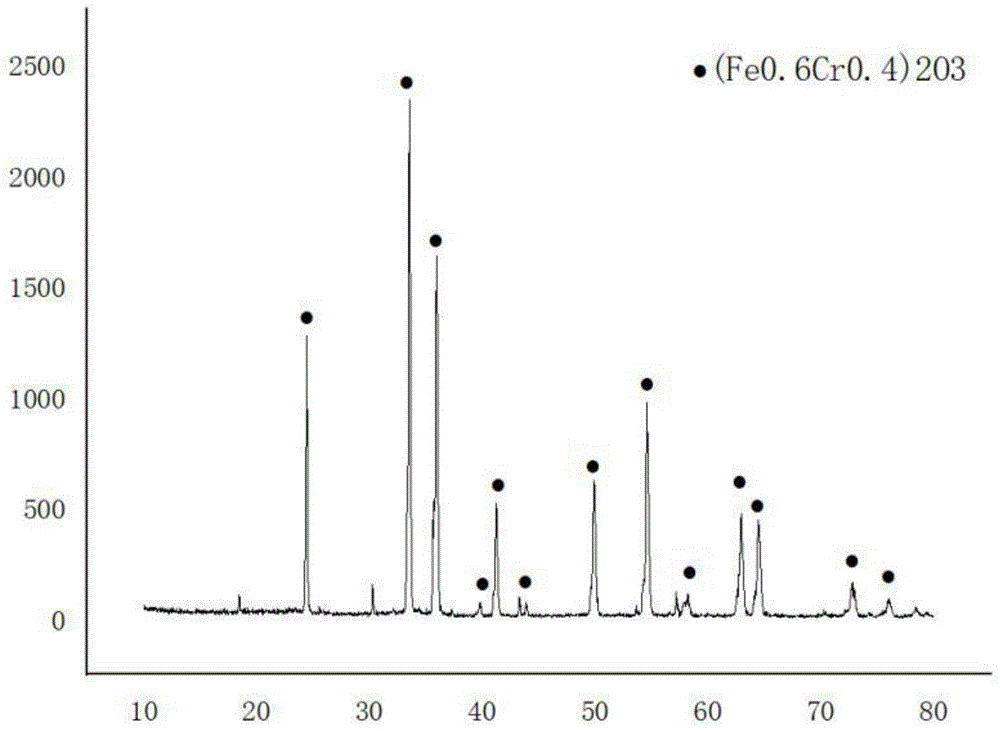
本发明涉及陶瓷色料
技术领域:
,尤其涉及一种陶瓷用黑色色料、制备工艺及使用其的陶瓷砖。
背景技术:
:陶瓷砖有较好的装饰效果,同时还具有易于清洁、使用寿命较长和生产成本低的优点,因此在家居建筑行业使用的非常广泛。传统的陶瓷用黑色色料主要以铁(fe)、铬(cr)、镍(ni)、锰(mn)、钴(co)等过渡金属氧化物作为原料,随着这些原料价格不断攀升,黑色色料因成本增加导致价位上涨,因此寻找价格低廉的原材料,研究开发价格低廉、发色效果好、发色稳定的黑色色料势在必行。在目前的炼钢工艺中带钢经过热轧工序后,在卷曲及冷却时带钢表面会生成氧化铁皮,为了使氧化铁皮不影响设备寿命及冷轧板表面质量和加工性能,会使用砂轮研磨、弯曲、喷丸、拉矫和酸洗等方法除去,保持带钢较好的性能,而去除的氧化铁皮通常直接作为废弃物处理,未能加以利用,造成了资源浪费的情况。技术实现要素:本发明的主要目的是提出一种陶瓷用黑色色料、制备工艺及使用其的陶瓷砖,旨在解决现有的黑色色料制作成本较高,未对废弃的氧化铁皮加以利用降低生产成本的技术问题。为实现上述目的,本发明提出一种陶瓷用黑色色料,所述陶瓷用黑色色料由包括如下组分的原料经焙烧制得:冷轧/热轧氧化铁皮65%-79%、cr2o320%-35%和三元复合矿化剂1%-2%。优选地,所述三元复合矿化剂包括na2co3、naf和sb2o3。优选地,所述na2co3、所述naf和所述sb2o3的质量比为(1.5-2.5):1:1。除此之外,本发明还提出一种如上述任一项所述的陶瓷用黑色色料的制备工艺,包括如下步骤:(1)按质量百分比,分别称取冷轧/热轧氧化铁皮、cr2o3、na2co3、naf和sb2o3;(2)将冷轧/热轧氧化铁皮、三聚磷酸钠加水后在球磨设备中混合球磨,之后再进行干燥。(3)将步骤(2)干燥后的冷轧/热轧氧化铁皮与cr2o3、na2co3、naf和sb2o3在搅拌设备中混合均匀,之后进行焙烧,再经过细磨后,即得到所述陶瓷用黑色色料。优选地,焙烧时,焙烧温度为1000℃-1030℃,焙烧时间为4-5h。优选地,干燥时,干燥温度为190℃-210℃,干燥时间为2-3h。优选地,干燥后所述冷轧/热轧氧化铁皮的细度为1.9-2.7μm。优选地,细磨后所述陶瓷用黑色色料的粒度为3-7μm。除此之外,本发明还提出一种使用上述任一项所述的陶瓷用黑色色料制得的陶瓷砖。本发明的黑色色料及使用其的陶瓷砖具有如下有益效果:利用了废弃的冷轧/热轧氧化铁皮,其富含feo、fe3o4和fe2o3,可以替代现有的氧化铁充当黑色色料的原料,并且冷轧/热轧氧化铁皮又不同于一般不锈钢钢渣,其组分中氧化硅、氧化铝、氧化镁、二氧化钛、氧化钙这些降低色料黑度的成分要少很多,且其还含有部分促进发色的组分,如fe3o4、mno、cr2o3和nio等,其中fe3o4和cr2o3为主要组成部分,再加上掺入的20-35%的cr2o3作为补充,在色料烧结时会形成黑色的fe2o3·cr2o3仿刚玉,此外冷轧/热轧氧化铁皮中的mno和nio可以与fe3o4和cr2o3形成尖晶石结构的固溶体,颜色互补,得到比较纯正黑色的色料。冷轧/热轧氧化铁皮的添加比例为65-79%,利用了废弃的氧化铁皮资源制作本方案中的陶瓷用黑色色料,更为环保节能,同时又节约了色料的生产成本。此外,本方案还添加有由na2co3、naf和sb2o3组成的三元复合矿化剂作为促进色料稳定发色的原料,降低色料的烧结温度,同时促使色料在瓷砖坯体中有更好的发色效果。附图说明为了更清楚地说明本发明实施例或现有技术中的技术方案,下面将对实施例或现有技术描述中所需要使用的附图作简单地介绍,显而易见地,下面描述中的附图仅仅是本发明的一些实施例,对于本领域普通技术人员来讲,在不付出创造性劳动的前提下,还可以根据这些附图示出的结构获得其他的附图。图1为本发明陶瓷用黑色色料实施例4的x-射线衍射图谱;图2为本发明陶瓷用黑色色料对比例3的x-射线衍射图谱。本发明目的的实现、功能特点及优点将结合实施例,参照附图做进一步说明。具体实施方式下面将结合本发明实施例中的附图,对本发明实施例中的技术方案进行清楚、完整地描述,显然,所描述的实施例仅仅是本发明的一部分实施例,而不是全部的实施例。基于本发明中的实施例,本领域普通技术人员在没有作出创造性劳动前提下所获得的所有其他实施例,都属于本发明保护的范围。另外,各个实施例之间的技术方案可以相互结合,但是必须是以本领域普通技术人员能够实现为基础,当技术方案的结合出现相互矛盾或无法实现时应当认为这种技术方案的结合不存在,也不在本发明要求的保护范围之内。本发明提出一种陶瓷用黑色色料。陶瓷用黑色色料主要添加至陶瓷砖坯中进行调色,其发色效果较稳定,制得的黑色瓷砖装饰效果较好,降低了色料的烧成温度,利用了废弃的冷轧/热轧氧化铁皮,节约了生产成本。在本发明一实施例中,一种陶瓷用黑色色料,按质量百分比,陶瓷用黑色色料由包括如下组分的原料经焙烧制得:冷轧/热轧氧化铁皮65%-79%、cr2o320%-35%和三元复合矿化剂1%-2%。具体的,本方案中的陶瓷用黑色色料由3种组分复配制得,其中氧化铬为该陶瓷用黑色色料主要成分之一,在色料中的添加比例为20-35%,使得色料的发色饱和度逐渐地增强,起到助色的作用;另一组份为冷轧/热轧氧化铁皮,其富含feo、fe3o4和fe2o3,可以替代现有的氧化铁充当黑色色料的原料,并且冷轧/热轧氧化铁皮又不同于一般不锈钢钢渣,其组分中氧化硅、氧化铝、氧化镁、二氧化钛、氧化钙这些降低色料黑度的成分要少很多,且其还含有部分促进发色的组分,如fe3o4、mno、cr2o3和nio等,其中fe3o4和cr2o3为主要组成部分,再加上掺入的20-35%的cr2o3作为补充,在色料烧结时会形成黑色的fe2o3·cr2o3仿刚玉,此外冷轧/热轧氧化铁皮中的mno和nio可以与fe3o4和cr2o3形成尖晶石结构的固溶体,颜色互补,得到比较纯正黑色的色料,冷轧/热轧氧化铁皮的添加比例为65-79%,利用了废弃的氧化铁皮资源制作本方案中的陶瓷用黑色色料,更为环保节能,同时也节约了生产成本。此外,本方案还添加有三元复合矿化剂作为促进色料稳定发色的原料,促进色料在瓷砖坯体中更好的发色效果。进一步地,三元复合矿化剂包括na2co3、naf和sb2o3。如此,该三元复合矿化剂由na2co3、naf和sb2o3三者复配形成,具有较低的共熔温度,可以在色料烧成过程中促进液相在较低温度下生成,从而降低色料的烧结温度,并能进一步促进陶瓷用黑色色料的发色效果,并且在冷轧/热轧氧化铁皮组分增加时,可以稳定色料的发色情况,保证黑色色料的纯度。进一步地,na2co3、naf和sb2o3的质量比为(1.5-2.5):1:1。具体的,在三元复合矿化剂中的na2co3比例最大,使矿化剂促进晶型生长的效果更好,na2co3、naf和sb2o3的质量比为(1.5-2.5):1:1时,其促进陶瓷黑色色料的发色效果最佳。除此之外,本发明还提出一种如上述任一项的陶瓷用黑色色料的制备工艺,包括如下步骤:(1)按质量百分比,分别称取冷轧/热轧氧化铁皮、cr2o3、na2co3、naf和sb2o3;(2)将冷轧/热轧氧化铁皮、三聚磷酸钠加水后在球磨设备中混合球磨,之后再进行干燥。(3)将步骤(2)干燥后的冷轧/热轧氧化铁皮与cr2o3、na2co3、naf和sb2o3在搅拌设备中混合均匀,之后进行焙烧,再经过细磨后,即得到陶瓷用黑色色料。具体地,按照质量比称取上述各个组分后,先对冷轧/热轧氧化铁皮进行处理,具体是将冷轧/热轧氧化铁皮与三聚磷酸钠加水后混合球磨,三聚磷酸钠的加入比例为冷轧/热轧氧化铁皮的0.3%左右,用于辅助球磨,具体球磨时间为8-10h,干燥之后得到细度较小的冷轧/热轧氧化铁皮,之后将冷轧/热轧氧化铁皮与cr2o3、na2co3、naf和sb2o3组分在搅拌设备中搅拌混合1-2h,混合均匀后进行焙烧,由于加入至瓷砖坯体中的色料粒度较小时,在瓷砖坯体中的发色效果更好,因此在焙烧之后还进行一步细磨工艺,细磨后即制得本方案的陶瓷用黑色色料。进一步地,焙烧时,焙烧温度为1000℃-1030℃,焙烧时间为4-5h。由于本方案中的陶瓷用黑色色料添加有上述组分,具有降低烧结温度的效果,因此本方案的焙烧温度为1000-1030℃,生产成本进一步降低,但需要保证4-5小时的焙烧时间,使得色料中的各个组分熔融完全,保证色料产品的最终效果。进一步地,干燥时,干燥温度为190℃-210℃,干燥时间为2-3h。可以理解,干燥过程使得球磨后的冷轧/热轧氧化铁皮含水量减少,便于后续的色料制备。进一步地,干燥后冷轧/热轧氧化铁皮的细度为1.9-2.7μm。如此,冷轧/热轧氧化铁皮的细度具体为1.9-2.7μm,需要保持在较小的粒度,以促进冷轧/热轧氧化铁皮中各个组分在焙烧过程中更好的发挥作用。进一步地,细磨后陶瓷用黑色色料的粒度为3-7μm。可以理解,陶瓷用黑色色料经筛网过筛,色料保持在该粒度之下,在保证陶瓷砖坯发色效果较好的同时,细磨成本可相对降低,有利于工业化生产。除此之外,本发明还提出一种使用上述任一项的陶瓷用黑色色料制得的陶瓷砖。本实施例所制得的陶瓷砖同样也具有较好的发色效果,在此不再一一赘述。以下结合具体实施例对本发明的技术方案作进一步详细说明,应当理解,以下实施例仅仅用以解释本发明,并不用于限定本发明。实施例1一种陶瓷用黑色色料的制备工艺,包括如下步骤:(1)分别称取79%的冷轧/热轧氧化铁皮、20%的cr2o3、1%的三元复合矿化剂(kcl、nacl和氟化钙的质量比为2.5:1:1);(2)将冷轧/热轧氧化铁皮、三聚磷酸钠加水后在球磨机中混合球磨,球磨9h,冷轧/热轧氧化铁皮的细度为2μm,之后进行干燥,干燥温度为190℃,干燥时间为3h;(3)将步骤(2)干燥后的冷轧/热轧氧化铁皮与cr2o3、kcl、nacl和氟化钙在搅拌机中混合均匀,之后进行焙烧,焙烧温度为1030℃,焙烧时间为4.5h,再经过细磨后,即得到所述陶瓷用黑色色料,所述陶瓷用黑色色料的细度为7μm。将上述制得的陶瓷用黑色色料以3%的量加入公知的陶瓷坯料中(坯料中发色金属离子的含量<0.5%),经球磨、干压后制成直径为55mm的圆饼型样品,再经过干燥,烧成后制得陶瓷砖样坯,其中烧成温度为1105℃。实施例2一种陶瓷用黑色色料的制备工艺,包括如下步骤:(1)分别称取73%的冷轧/热轧氧化铁皮、25.5%的cr2o3、1.5%的三元复合矿化剂(kcl、naf和kno3的质量比为1:1:1);(2)将冷轧/热轧氧化铁皮、三聚磷酸钠加水后在球磨机中混合球磨,球磨8.5h,冷轧/热轧氧化铁皮的细度为2.7μm,之后进行干燥,干燥温度为195℃,干燥时间为2.5h;(3)将步骤(2)干燥后的冷轧/热轧氧化铁皮与cr2o3、kcl、nacl和kno3在搅拌机中混合均匀,之后进行焙烧,焙烧温度为1020℃,焙烧时间为5h,再经过细磨后,即得到所述陶瓷用黑色色料,所述陶瓷用黑色色料的细度为4μm。将上述制得的陶瓷用黑色色料以3%的量加入公知的陶瓷坯料中(坯料中发色金属离子的含量<0.5%),经球磨、干压后制成直径为55mm的圆饼型样品,再经过干燥,烧成后制得陶瓷砖样坯,其中烧成温度为1105℃。实施例3一种陶瓷用黑色色料的制备工艺,包括如下步骤:(1)分别称取68%的冷轧/热轧氧化铁皮、30%的cr2o3、2%的三元复合矿化剂(kcl、nacl和kno3的质量比为1.5:1:1);(2)将冷轧/热轧氧化铁皮、三聚磷酸钠加水后在球磨机中混合球磨,球磨8h,冷轧/热轧氧化铁皮的细度为2.5μm,之后进行干燥,干燥温度为205℃,干燥时间为2.5h;(3)将步骤(2)干燥后的冷轧/热轧氧化铁皮与cr2o3、kcl、nacl和kno3在搅拌机中混合均匀,之后进行焙烧,焙烧温度为1005℃,焙烧时间为4h,再经过细磨后,即得到所述陶瓷用黑色色料,所述陶瓷用黑色色料的细度为3μm。将上述制得的陶瓷用黑色色料以3%的量加入公知的陶瓷坯料中(坯料中发色金属离子的含量<0.5%),经球磨、干压后制成直径为55mm的圆饼型样品,再经过干燥,烧成后制得陶瓷砖样坯,其中烧成温度为1105℃。实施例4一种陶瓷用黑色色料的制备工艺,包括如下步骤:(1)分别称取70%的冷轧/热轧氧化铁皮、28%的cr2o3、2%的三元复合矿化剂(na2co3、naf和sb2o3的质量比为2:1:1);(2)将冷轧/热轧氧化铁皮、三聚磷酸钠加水后在球磨机中混合球磨,球磨9h,冷轧/热轧氧化铁皮的细度为2.3μm,之后进行干燥,干燥温度为200℃,干燥时间为2h;(3)将步骤(2)干燥后的冷轧/热轧氧化铁皮与cr2o3、na2co3、naf和sb2o3在搅拌机中混合均匀,之后进行焙烧,焙烧温度为1025℃,焙烧时间为4.5h,再经过细磨后,即得到所述陶瓷用黑色色料,所述陶瓷用黑色色料的细度为5μm。将上述制得的陶瓷用黑色色料以3%的量加入公知的陶瓷坯料中(坯料中发色金属离子的含量<0.5%),经球磨、干压后制成直径为55mm的圆饼型样品,再经过干燥,烧成后制得陶瓷砖样坯,其中烧成温度为1105℃。将实施例1-4进行性能测试,具体的测试结果如下表1所示:表1其中,l为亮度值,a为红度值,b为黄度值,标准值为该公知的陶瓷坯料制得的陶瓷砖其黑色纯度最高时的lab值。评价项目:黑色纯度测试:采用广州市授科仪器科技有限公司生产的cm-2600-2500d分光测色计对陶瓷砖样坯进行检测。以上实施例表明,通过本方案的组分及配比制得的陶瓷用黑色色料,与标准黑色色料的lab值进行比较后可得出,实施例1-4的色彩偏离值△e均较小,△e均≦1.25,且最优实施例与标准黑色色料的色彩偏离值△e仅为0.48,陶瓷用黑色色料的纯度较高,在色料烧成温度较低的情况下制得的陶瓷砖均能保持较好的发色效果,进一步降低了陶瓷用黑色色料的生产成本。对比例1本对比例中各项条件与实施例4相同,不同之处在于:本对比例使用氧化铁来替换冷轧/热轧氧化铁皮。对比例2本对比例中各项条件与实施例4相同,不同之处在于:本对比例使用的矿化剂为nacl。对比例3本对比例中各项条件与实施例4相同,不同之处在于:本对比例使用的矿化剂为kcl。对比例4本对比例中各项条件与实施例4相同,不同之处在于:本对比例使用的矿化剂为kcl和nacl复合组成,kcl和nacl的质量比为2:1。对比例5本对比例中各项条件与对比例2相同,不同之处在于:焙烧温度为1150℃。对比例6本对比例中各项条件与对比例3相同,不同之处在于:焙烧温度为1150℃。对比例7本对比例中各项条件与对比例4相同,不同之处在于:焙烧温度为1150℃。将对比例1-7进行性能测试,具体的测试结果如下表2所示:表2根据以上对比例的测试结果可知,与标准黑色色料的lab值进行比较,对比例1与实施例4的色彩偏离值△e的差值均较小,利用废弃的冷轧/热轧氧化铁皮替换氧化铁这一组分后,制得的陶瓷用黑色色料仍具有较好的发色效果。根据对比例2-4可知,在使用单独组分的矿化剂或者两种组分复合组成矿化剂时,其制得的色料发色效果均一般,与标准黑色色料的lab值进行比较后△e>1.5,由对比例5-7的检测结果可知,只有在提高色料的焙烧温度时,色料的发色效果才有所提高,但提高焙烧温度后使用单独组分的矿化剂或两种组分复合的矿化剂的发色效果仍低于实施例4。此外,本方案还对实施例4和对比例3进行了x-射线衍射检测,利用x-射线衍射仪对实施例4与对比例3制得的色料进行xrd定性分析,测试结果如图1至图2所示,通过比较二者的衍射强度,在相同条件下,相较于使用常规矿化剂kcl,使用本方案中的三元复合矿化剂,色料的晶形发育更为完整,发色效果更好。实施例5本实施例中各项条件与实施例4相同,不同之处在于:本对比例使用的矿化剂为kcl、nacl和氟化钙复合形成。实施例6本实施例中各项条件与实施例4相同,不同之处在于:本对比例使用的矿化剂为kcl、naf和kno3复合形成。实施例7本实施例中各项条件与实施例4相同,不同之处在于:本对比例使用的矿化剂为kcl、nacl和kno3复合形成。将实施例5-7进行性能测试,具体的测试结果如下表3所示:表3矿化剂lab△e实施例4na2co3:naf:sb2o3=2:1:132.611.15-0.610.48实施例5kcl:nacl:氟化钙=2:1:131.811.43-0.30.95实施例6kcl:naf:kno3=2:1:131.911.23-0.240.83实施例7kcl:nacl:kno3=2:1:132.111.13-0.30.65标准/32.320.85-0.85/根据以上对比例的测试结果可知,与标准黑色色料的lab值进行比较,实施例4与实施例5-7的色彩偏离值△e的差值较大,在各组实施例中使用na2co3、naf和sb2o3复配时色料的发色效果最佳,而采用kcl+nacl+氟化钙、kcl+nacl+kno3以及kcl+naf+kno3复合时,烧成制得的陶瓷砖样坯色彩偏离值△e相对较大,发色效果较于na2co3、naf和sb2o3复配时要差。实施例8本对比例中各项条件与实施例4相同,不同之处在于:各组分的加入比例调整为73%的氧化铁、25%的氧化铬和2%的三元复合矿化剂。实施例9本实施例中各项条件与实施例8相同,不同之处在于:本对比例使用的矿化剂为kcl、nacl和氟化钙复合形成。实施例10本实施例中各项条件与实施例8相同,不同之处在于:本对比例使用的矿化剂为kcl、naf和kno3复合形成。实施例11本实施例中各项条件与实施例8相同,不同之处在于:本对比例使用的矿化剂为kcl、nacl和kno3复合形成。实施例12本对比例中各项条件与实施例4相同,不同之处在于:各组分的加入比例调整为75%的氧化铁、23%的氧化铬和2%的三元复合矿化剂。实施例13本实施例中各项条件与实施例12相同,不同之处在于:本对比例使用的矿化剂为kcl、nacl和氟化钙复合形成。实施例14本实施例中各项条件与实施例12相同,不同之处在于:本对比例使用的矿化剂为kcl、naf和kno3复合形成。实施例15本实施例中各项条件与实施例12相同,不同之处在于:本对比例使用的矿化剂为kcl、nacl和kno3复合形成。实施例16本对比例中各项条件与实施例4相同,不同之处在于:各组分的加入比例调整为78%的氧化铁、20%的氧化铬和2%的三元复合矿化剂。实施例17本实施例中各项条件与实施例12相同,不同之处在于:本对比例使用的矿化剂为kcl、nacl和氟化钙复合形成。实施例18本实施例中各项条件与实施例12相同,不同之处在于:本对比例使用的矿化剂为kcl、naf和kno3复合形成。实施例19本实施例中各项条件与实施例12相同,不同之处在于:本对比例使用的矿化剂为kcl、nacl和kno3复合形成。将实施例8-15进行性能测试,具体的测试结果如下表4所示:表4以上实施例表明,使用na2co3、naf和sb2o3复配成矿化剂时,增加冷轧/热轧氧化铁皮组分,色彩偏离值△e的差值≦0.04,制得的陶瓷砖黑色纯度相差较小,因此在提高冷轧/热轧氧化铁皮的添加比例时对陶瓷砖的发色效果影响较小,发色效果均较好,进一步减少了生产成本。而使用其他的矿化剂复配成三元矿化剂时,制得的陶瓷砖样坯发色效果不稳定,色彩偏离值△e的差值均≧0.1,制得的瓷砖产品相对来说将会存在较大色差。实施例20本实施例中各项条件与实施例4相同,不同之处在于:复合矿化剂中na2co3、naf和sb2o3的质量比为1.5:1:1。实施例21本实施例中各项条件与实施例4相同,不同之处在于:复合矿化剂中na2co3、naf和sb2o3的质量比为2.5:1:1。对比例9本对比例中各项条件与实施例4相同,不同之处在于:复合矿化剂中na2co3、naf和sb2o3的质量比为1:1:1。对比例9本对比例中各项条件与实施例4相同,不同之处在于:复合矿化剂中na2co3、naf和sb2o3的质量比为2:1:1。将实施例20-21和对比例8-9进行性能测试,具体测试结果如下表5所示:表5矿化剂lab△e实施例4na2co3:naf:sb2o3=2:1:132.611.15-0.610.48实施例20na2co3:naf:sb2o3=1.5:1:132.531.32-0.580.58实施例21na2co3:naf:sb2o3=2.5:1:132.581.35-0.550.64对比例8na2co3:naf:sb2o3=1:1:132.471.37-0.570.61对比例9na2co3:naf:sb2o3=3:1:132.591.42-0.540.70以上实施例和对比例表明,本方案使用的复合矿化剂中的na2co3、naf和sb2o3的质量比为在2:1:1时具有最佳的发色效果,复合矿化剂中的na2co3、naf和sb2o3在其他质量比时,其发色效果有所减弱,优选质量比为na2co3、naf和sb2o3=2:1:1。以上所述仅为本发明的优选实施例,并非因此限制本发明的专利范围,凡是在本发明的发明构思下,利用本发明说明书及附图内容所作的等效结构变换,或直接/间接运用在其他相关的
技术领域:
均包括在本发明的专利保护范围内。当前第1页1 2 3 
起点商标作为专业知识产权交易平台,可以帮助大家解决很多问题,如果大家想要了解更多知产交易信息请点击 【在线咨询】或添加微信 【19522093243】与客服一对一沟通,为大家解决相关问题。
此文章来源于网络,如有侵权,请联系删除



tips