合成ε-己内酯的方法与流程



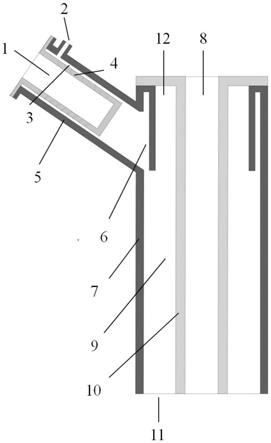
合成
ε-己内酯的方法
技术领域
[0001]
本发明属于有机合成工艺技术领域,具体涉及一种以环己酮和双氧水为原料,在微反应装置中合成ε-己内酯的连续工艺。
背景技术:
[0002]
ε-己内酯是一种环境友好型聚酯单体,主要用于具有独特生物相容性、生物降解性与良好渗透性的高分子材料聚己内酯的合成,也可作为改性材料与其他高分子单体共聚或高分子材料共混提高其光泽度、透明度、生物降解性与防黏性等,是近年来一种具有十分广阔市场应用前景的精细化学品。
[0003]
目前国际上ε-己内酯生产方法主要是过氧酸氧化法,即用过氧酸作氧化剂氧化环己酮合成ε-己内酯,这种方法研究相对比较成熟,但该方法合成前期的过氧酸浓缩过程和后续产生的高浓度易爆环己酮过氧化物的纯化过程均存在较高的危险性,因此产能受到一定的限制。目前采用的过氧酸主要有过氧甲酸、过氧乙酸、过氧丙酸、三氟过氧乙酸、过氧苯甲酸、间氯过氧苯甲酸。ε-己内酯在国外主要由德国巴斯夫、瑞典帕斯托和日本大赛璐三家生产,其生产技术均采用过氧酸氧化法且都严格保密。ε-己内酯在国内仅有中国石化巴陵石化公司正常生产,其使用了过氧化氢共沸脱水氧化丙酸制备过氧丙酸,再氧化环己酮制备ε-己内酯,据报道其装置生产规模为200吨/年,产品纯度大于99.9%。巴陵石化ε-己内酯生产技术研究始于2006年,2007年小试研究合成出合格的ε-己内酯产品,2011年底中试装置通过中国石化集团公司鉴定,目前已经完成了10000吨/年的工艺包编制,但是出于安全角度考虑一直没有具体实施项目扩建。为了提高过程的安全可控性最近也有人提出利用微通道反应技术理念进行己内酯的连续化合成工艺研究。微通道技术通过常规反应器所不具备的一系列特性(通道尺寸微型化、较大的换热比表面积、优良的传质传热特性、连续反应、可跳过经逐级放大试验直接放大、生产灵活且安全性能高)可以实现对常规间歇釜式氧化反应工艺的突破。
[0004]
中国专利cn 103539770 a公开了一种基于过氧乙酸氧化环己酮制备ε-己内酯的微通道反应技术,中国专利cn 106279093 a公开了一种基于间氯过氧苯甲酸氧化环己酮制备ε-己内酯的微通道反应技术,上述两种工艺均需要先制备过氧酸再利用过氧酸对环己酮进行氧化,工艺流程较长,同时要对反应后的有机酸进行分离回收用于过氧酸的再次制备,分离成本较大,在规模化生产中具有一定难度。
技术实现要素:
[0005]
本发明要解决的技术问题之一是提供一种利用微通道反应器合成ε-己内酯的微通道方法。
[0006]
一种合成ε-己内酯的方法,包括使含有钨酸钠的均相催化剂和氧化剂的水相原料与含有环己酮和带水剂的油相原料,在微混合器中混合,所得的液相原料和气相原料在微反应器中进行反应分离耦合,获得ε-己内酯的步骤,所述微混合器和微反应器组成微通道
装置。所述合成ε-己内酯的方法中,反应分离耦合过程中气相原料和液相原料的体积比为(1~30):1,微反应器反应温度为50~150℃,压力为-0.1~0.1mpa,在微反应器中的停留时间为0.5~30min。以质量百分比计,所述水相原料中氧化剂的含量为10%~70%,优选为20%~50%,所述均相催化剂选自钨酸盐与草酸的配位化合物;以质量百分比计,均相催化剂在水相原料中的含量为0.1~5.0%,草酸与钨酸钠的摩尔比为1.0~2.0。所述合成ε-己内酯的方法,以质量百分比计,所述的油相原料中带水剂的含量为20~80%,所述氧化剂选自双氧水、叔丁基过氧化氢、过氧乙酸、过氧丙酸;优选为双氧水、过氧丙酸;更优选为双氧水;所述带水剂选自苯、甲苯、丙酸乙酯、乙酸乙酯、四氯化碳或二氯乙烷;优选为甲苯、丙酸乙酯。气相原料选自空气、氮气、氦气、氩气;优选为氮气、氦气。水相原料和油相原料经预热器预热后进入微混合器,预热温度为40~60℃。在微混合器中的混合过程,包括:将均相催化剂和氧化剂经过水相原料入口进入混合器喷嘴,经微筛斜孔分散后和由油相原料入口进入的环己酮和带水剂在混合通道中接触;微混合器出口得到的液相原料包含环己酮、氧化剂、均相催化剂与带水剂。在微反应器中的反应分离耦合过程,包括:所述液相原料经过连接管路由液相原料入口进入微反应器,通过加热管壁中的加热介质提供反应所需热量;微反应器的液相产物由液相产物出口处排出,所述液相产物包含ε-己内酯、环己酮、均相催化剂和带水剂,气相产物携带带水剂和水份由气相产物出口处排出,经冷却后通过油水分离进行带水剂的回收并循环使用。该液相原料与气相原料在反应通道中为逆流接触,所述微混合器的个数大于等于2,优选为偶数个,微混合器位于微反应器两侧的对称位置,微混合器中轴线与微反应器的中轴线夹角为30-150
°
,优选为60-120
°
。所述微筛斜孔分布于微混合器喷嘴柱状体的侧面,水力学直径为5~500微米,优选20~200微米,开孔率为1~70%,优选为10~20%,斜孔倾角为20~160
°
,优选为60~120
°
。
[0007]
本发明提供的合成ε-己内酯方法的有益效果为:
[0008]
本发明提供的一种合成ε-己内酯的微通道方法实现了ε-己内酯的连续化生产,通过微尺度效应强化非均相液液体系的高效混合实现了较高的环己酮转化率,能够达到85%以上,也通过微尺度结构的限域效应实现了装置内反应流体以平推流模式流动,从而能够精确地控制反应停留时间,实现了较高的ε-己内酯选择性;同时也基于微通道技术构建了反应脱水耦合过程,通过有效地在线分离手段降低ε-己内酯合成体系中的水含量,避免因ε-己内酯水解而导致的产品收率下降,属于一种低碳环保、节能减排的工艺路线。
附图说明
[0009]
图1为本发明提供的带微尺度多孔喷嘴混合器和微尺度同轴环管降膜反应器的结构示意图。
[0010]
图中:水相原料入口(1);油相原料入口(2);混合通道(3);微筛斜孔(4);混合器套管(5);液相原料入口(6):反应器外壁(7);导热油入口(8);反应通道(9);加热管壁(10);液相产物出口(11);气相产物出口(12);
具体实施方式
[0011]
下面通过实施例对本发明作进一步说明,但并不因此而限制本发明的内容。
[0012]
下列实施例系根据本发明方法的要求在微反应器中进行。
[0013]
【实施例1】
[0014]
使用计量泵输送含氧化剂和催化剂的水相原料,其中双氧水质量分数为40%,催化剂质量分数为1.5%,催化剂中草酸与钨酸钠的用量摩尔比为1.0;使用计量泵输送含有带水剂的油相原料,其中带水剂甲苯质量分数为50%。水相原料中氧化剂与油相原料中环己酮摩尔比为3.5,两股物料分别通过预热器预热在微混合器中50℃下充分进行混合过程。微混合器出口液体经过连接管路后进入微反应器作为液相原料,通过液相原料入口进入微反应器中在与由下部气相入口进入的空气逆流接触并进行环己酮氧化反应,通过加热管壁中的加热介质提供反应所需热量。反应通道内部通过加热管壁中的导热油控制其温度在90℃,反应压力为常压,通过调节计量泵的流量及反应通道的长度来控制反应物料的停留时间为10min,通过调节气体质量流量计控制反应通道中的气液比为10:1。微反应器的液相产物作为目标产品粗品ε-己内酯由液相产物出口处排出,气相产物携带带水剂和水份由气相产物出口处排出,经冷却后通过油水分离进行回收循环使用。所使用的微通道装置主体均采用不锈钢316l加工而成,微混合器的个数为2个,微混合器位于微反应器两侧的对称位置,微混合器中轴线与微反应器的中轴线夹角为60
°
,微筛斜孔分布于微混合器喷嘴柱状体的侧面,水力学直径为100微米,开孔率为15%,微筛斜孔为60
°
。粗品ε-己内酯分析结果表明此过程中环己酮的转化率为87.1%,ε-己内酯选择性为94.8%。
[0015]
【实施例2】
[0016]
使用计量泵输送含氧化剂和催化剂的水相原料,其中双氧水质量分数为30%,催化剂质量分数为1.5%,催化剂中草酸与钨酸钠的用量摩尔比为1.0;使用计量泵输送含有带水剂的油相原料,其中带水剂甲苯质量分数为50%。水相原料中氧化剂与油相原料中环己酮摩尔比为3.5,两股物料分别通过预热器预热在微混合器中50℃下充分进行混合过程。微混合器出口液体经过连接管路后进入微反应器作为液相原料,通过液相原料入口进入微反应器中在与由下部气相入口进入的空气逆流接触并进行环己酮氧化反应,通过加热管壁中的加热介质提供反应所需热量。反应通道内部通过加热管壁中的导热油控制其温度在90℃,反应压力为常压,通过调节计量泵的流量及反应通道的长度来控制反应物料的停留时间为10min,通过调节气体质量流量计控制反应通道中的气液比为10:1。微反应器的液相产物作为目标产品粗品ε-己内酯由液相产物出口处排出,气相产物携带带水剂和水份由气相产物出口处排出,经冷却后通过油水分离进行回收循环使用。所使用的微通道装置主体均采用不锈钢316l加工而成,微混合器的个数为2个,微混合器位于微反应器两侧的对称位置,微混合器中轴线与微反应器的中轴线夹角为60
°
,微筛斜孔分布于微混合器喷嘴柱状体的侧面,水力学直径为100微米,开孔率为15%,斜孔倾角为60
°
。粗品ε-己内酯分析结果表明此过程中环己酮的转化率为84.2%,ε-己内酯选择性为95.1%。
[0017]
【实施例3】
[0018]
使用计量泵输送含氧化剂和催化剂的水相原料,其中过氧乙酸质量分数为15%,催化剂质量分数为1.5%,催化剂中草酸与钨酸钠的用量摩尔比为1.0;使用计量泵输送含有带水剂的油相原料,其中带水剂甲苯质量分数为50%。水相原料中氧化剂与油相原料中环己酮摩尔比为3.5,两股物料分别通过预热器预热在微混合器中50℃下充分进行混合过程。微混合器出口液体经过连接管路后进入微反应器作为液相原料,通过液相原料入口进入微反应器中在与由下部气相入口进入的空气逆流接触并进行环己酮氧化反应,通过加热
管壁中的加热介质提供反应所需热量。反应通道内部通过加热管壁中的导热油控制其温度在90℃,反应压力为常压,通过调节计量泵的流量及反应通道的长度来控制反应物料的停留时间为10min,通过调节气体质量流量计控制反应通道中的气液比为10:1。微反应器的液相产物作为目标产品粗品ε-己内酯由液相产物出口处排出,气相产物携带带水剂和水份由气相产物出口处排出,经冷却后通过油水分离进行回收循环使用。所使用的微通道装置主体均采用不锈钢316l加工而成,微混合器的个数为2个,微混合器位于微反应器两侧的对称位置,微混合器中轴线与微反应器的中轴线夹角为60
°
,微筛斜孔分布于微混合器喷嘴柱状体的侧面,水力学直径为100微米,开孔率为15%,斜孔倾角为60
°
。粗品ε-己内酯分析结果表明此过程中环己酮的转化率为86.6%,ε-己内酯选择性为94.2%。
[0019]
【实施例4】
[0020]
使用计量泵输送含氧化剂和催化剂的水相原料,其中过氧丙酸质量分数为15%,催化剂质量分数为1.5%,催化剂中草酸与钨酸钠的用量摩尔比为1.0;使用计量泵输送含有带水剂的油相原料,其中带水剂甲苯质量分数为50%。水相原料中氧化剂与油相原料中环己酮摩尔比为3.5,两股物料分别通过预热器预热在微混合器中50℃下充分进行混合过程。微混合器出口液体经过连接管路后进入微反应器作为液相原料,通过液相原料入口进入微反应器中在与由下部气相入口进入的空气逆流接触并进行环己酮氧化反应,通过加热管壁中的加热介质提供反应所需热量。反应通道内部通过加热管壁中的导热油控制其温度在90℃,反应压力为常压,通过调节计量泵的流量及反应通道的长度来控制反应物料的停留时间为10min,通过调节气体质量流量计控制反应通道中的气液比为10:1。微反应器的液相产物作为目标产品粗品ε-己内酯由液相产物出口处排出,气相产物携带带水剂和水份由气相产物出口处排出,经冷却后通过油水分离进行回收循环使用。所使用的微通道装置主体均采用不锈钢316l加工而成,微混合器的个数为2个,微混合器位于微反应器两侧的对称位置,微混合器中轴线与微反应器的中轴线夹角为60
°
,微筛斜孔分布于微混合器喷嘴柱状体的侧面,水力学直径为100微米,开孔率为15%,斜孔倾角为60
°
。粗品ε-己内酯分析结果表明此过程中环己酮的转化率为86.0%,ε-己内酯选择性为95.1%。
[0021]
【实施例5】
[0022]
使用计量泵输送含氧化剂和催化剂的水相原料,其中双氧水质量分数为40%,催化剂质量分数为2.0%,催化剂中草酸与钨酸钠的用量摩尔比为1.0;使用计量泵输送含有带水剂的油相原料,其中带水剂甲苯质量分数为50%。水相原料中氧化剂与油相原料中环己酮摩尔比为3.5,两股物料分别通过预热器预热在微混合器中50℃下充分进行混合过程。微混合器出口液体经过连接管路后进入微反应器作为液相原料,通过液相原料入口进入微反应器中在与由下部气相入口进入的空气逆流接触并进行环己酮氧化反应,通过加热管壁中的加热介质提供反应所需热量。反应通道内部通过加热管壁中的导热油控制其温度在90℃,反应压力为常压,通过调节计量泵的流量及反应通道的长度来控制反应物料的停留时间为10min,通过调节气体质量流量计控制反应通道中的气液比为10:1。微反应器的液相产物作为目标产品粗品ε-己内酯由液相产物出口处排出,气相产物携带带水剂和水份由气相产物出口处排出,经冷却后通过油水分离进行回收循环使用。所使用的微通道装置主体均采用不锈钢316l加工而成,微混合器的个数为2个,微混合器位于微反应器两侧的对称位置,微混合器中轴线与微反应器的中轴线夹角为60
°
,微筛斜孔分布于微混合器喷嘴柱状体
的侧面,水力学直径为100微米,开孔率为15%,斜孔倾角为60
°
。粗品ε-己内酯分析结果表明此过程中环己酮的转化率为88.8%,ε-己内酯选择性为94.1%。
[0023]
【实施例6】
[0024]
使用计量泵输送含氧化剂和催化剂的水相原料,其中双氧水质量分数为40%,催化剂质量分数为1.5%,催化剂中草酸与钨酸钠的用量摩尔比为1.0;使用计量泵输送含有带水剂的油相原料,其中带水剂丙酸乙酯质量分数为50%。水相原料中氧化剂与油相原料中环己酮摩尔比为3.5,两股物料分别通过预热器预热在微混合器中50℃下充分进行混合过程。微混合器出口液体经过连接管路后进入微反应器作为液相原料,通过液相原料入口进入微反应器中在与由下部气相入口进入的空气逆流接触并进行环己酮氧化反应,通过加热管壁中的加热介质提供反应所需热量。反应通道内部通过加热管壁中的导热油控制其温度在90℃,反应压力为常压,通过调节计量泵的流量及反应通道的长度来控制反应物料的停留时间为10min,通过调节气体质量流量计控制反应通道中的气液比为10:1。微反应器的液相产物作为目标产品粗品ε-己内酯由液相产物出口处排出,气相产物携带带水剂和水份由气相产物出口处排出,经冷却后通过油水分离进行回收循环使用。所使用的微通道装置主体均采用不锈钢316l加工而成,微混合器的个数为2个,微混合器位于微反应器两侧的对称位置,微混合器中轴线与微反应器的中轴线夹角为60
°
,微筛斜孔分布于微混合器喷嘴柱状体的侧面,水力学直径为100微米,开孔率为15%,斜孔倾角为60
°
。粗品ε-己内酯分析结果表明此过程中环己酮的转化率为87.0%,ε-己内酯选择性为95.5%。
[0025]
【实施例7】
[0026]
使用计量泵输送含氧化剂和催化剂的水相原料,其中双氧水质量分数为40%,催化剂质量分数为1.5%,催化剂中草酸与钨酸钠的用量摩尔比为1.0;使用计量泵输送含有带水剂的油相原料,其中带水剂甲苯质量分数为30%。水相原料中氧化剂与油相原料中环己酮摩尔比为3.5,两股物料分别通过预热器预热在微混合器中50℃下充分进行混合过程。微混合器出口液体经过连接管路后进入微反应器作为液相原料,通过液相原料入口进入微反应器中在与由下部气相入口进入的空气逆流接触并进行环己酮氧化反应,通过加热管壁中的加热介质提供反应所需热量。反应通道内部通过加热管壁中的导热油控制其温度在90℃,反应压力为常压,通过调节计量泵的流量及反应通道的长度来控制反应物料的停留时间为10min,通过调节气体质量流量计控制反应通道中的气液比为10:1。微反应器的液相产物作为目标产品粗品ε-己内酯由液相产物出口处排出,气相产物携带带水剂和水份由气相产物出口处排出,经冷却后通过油水分离进行回收循环使用。所使用的微通道装置主体均采用不锈钢316l加工而成,微混合器的个数为2个,微混合器位于微反应器两侧的对称位置,微混合器中轴线与微反应器的中轴线夹角为60
°
,微筛斜孔分布于微混合器喷嘴柱状体的侧面,水力学直径为100微米,开孔率为15%,斜孔倾角为60
°
。粗品ε-己内酯分析结果表明此过程中环己酮的转化率为84.2%,ε-己内酯选择性为91.6%。
[0027]
表1
[0028][0029][0030]
【实施例8】
[0031]
使用计量泵输送含氧化剂和催化剂的水相原料,其中双氧水质量分数为40%,催化剂质量分数为1.5%,催化剂中草酸与钨酸钠的用量摩尔比为1.0;使用计量泵输送含有带水剂的油相原料,其中带水剂甲苯质量分数为50%。水相原料中氧化剂与油相原料中环己酮摩尔比为4.0,两股物料分别通过预热器预热在微混合器中50℃下充分进行混合过程。微混合器出口液体经过连接管路后进入微反应器作为液相原料,通过液相原料入口进入微反应器中在与由下部气相入口进入的空气逆流接触并进行环己酮氧化反应,通过加热管壁中的加热介质提供反应所需热量。反应通道内部通过加热管壁中的导热油控制其温度在90℃,反应压力为常压,通过调节计量泵的流量及反应通道的长度来控制反应物料的停留时间为10min,通过调节气体质量流量计控制反应通道中的气液比为10:1。微反应器的液相产物作为目标产品粗品ε-己内酯由液相产物出口处排出,气相产物携带带水剂和水份由气相
产物出口处排出,经冷却后通过油水分离进行回收循环使用。所使用的微通道装置主体均采用不锈钢316l加工而成,微混合器的个数为2个,微混合器位于微反应器两侧的对称位置,微混合器中轴线与微反应器的中轴线夹角为60
°
,微筛斜孔分布于微混合器喷嘴柱状体的侧面,水力学直径为100微米,开孔率为15%,斜孔倾角为60
°
。粗品ε-己内酯分析结果表明此过程中环己酮的转化率为87.8%,ε-己内酯选择性为93.8%。
[0032]
【实施例9】
[0033]
使用计量泵输送含氧化剂和催化剂的水相原料,其中双氧水质量分数为40%,催化剂质量分数为1.5%,催化剂中草酸与钨酸钠的用量摩尔比为1.0;使用计量泵输送含有带水剂的油相原料,其中带水剂甲苯质量分数为60%。水相原料中氧化剂与油相原料中环己酮摩尔比为3.5,两股物料分别通过预热器预热在微混合器中50℃下充分进行混合过程。微混合器出口液体经过连接管路后进入微反应器作为液相原料,通过液相原料入口进入微反应器中在与由下部气相入口进入的空气逆流接触并进行环己酮氧化反应,通过加热管壁中的加热介质提供反应所需热量。反应通道内部通过加热管壁中的导热油控制其温度在90℃,反应压力为常压,通过调节计量泵的流量及反应通道的长度来控制反应物料的停留时间为10min,通过调节气体质量流量计控制反应通道中的气液比为10:1。微反应器的液相产物作为目标产品粗品ε-己内酯由液相产物出口处排出,气相产物携带带水剂和水份由气相产物出口处排出,经冷却后通过油水分离进行回收循环使用。所使用的微通道装置主体均采用不锈钢316l加工而成,微混合器的个数为2个,微混合器位于微反应器两侧的对称位置,微混合器中轴线与微反应器的中轴线夹角为60
°
,微筛斜孔分布于微混合器喷嘴柱状体的侧面,水力学直径为100微米,开孔率为15%,斜孔倾角为60
°
。粗品ε-己内酯分析结果表明此过程中环己酮的转化率为85.1%,ε-己内酯选择性为95.4%。
[0034]
【实施例10】
[0035]
使用计量泵输送含氧化剂和催化剂的水相原料,其中双氧水质量分数为40%,催化剂质量分数为1.5%,催化剂中草酸与钨酸钠的用量摩尔比为1.0;使用计量泵输送含有带水剂的油相原料,其中带水剂甲苯质量分数为50%。水相原料中氧化剂与油相原料中环己酮摩尔比为3.5,两股物料分别通过预热器预热在微混合器中50℃下充分进行混合过程。微混合器出口液体经过连接管路后进入微反应器作为液相原料,通过液相原料入口进入微反应器中在与由下部气相入口进入的空气逆流接触并进行环己酮氧化反应,通过加热管壁中的加热介质提供反应所需热量。反应通道内部通过加热管壁中的导热油控制其温度在60℃,反应压力为常压,通过调节计量泵的流量及反应通道的长度来控制反应物料的停留时间为10min,通过调节气体质量流量计控制反应通道中的气液比为10:1。微反应器的液相产物作为目标产品粗品ε-己内酯由液相产物出口处排出,气相产物携带带水剂和水份由气相产物出口处排出,经冷却后通过油水分离进行回收循环使用。所使用的微通道装置主体均采用不锈钢316l加工而成,微混合器的个数为2个,微混合器位于微反应器两侧的对称位置,微混合器中轴线与微反应器的中轴线夹角为60
°
,微筛斜孔分布于微混合器喷嘴柱状体的侧面,水力学直径为100微米,开孔率为15%,斜孔倾角为60
°
。粗品ε-己内酯分析结果表明此过程中环己酮的转化率为76.0%,ε-己内酯选择性为98.1%。
[0036]
【实施例11】
[0037]
使用计量泵输送含氧化剂和催化剂的水相原料,其中双氧水质量分数为40%,催
化剂质量分数为1.5%,催化剂中草酸与钨酸钠的用量摩尔比为1.0;使用计量泵输送含有带水剂的油相原料,其中带水剂甲苯质量分数为50%。水相原料中氧化剂与油相原料中环己酮摩尔比为3.5,两股物料分别通过预热器预热在微混合器中50℃下充分进行混合过程。微混合器出口液体经过连接管路后进入微反应器作为液相原料,通过液相原料入口进入微反应器中在与由下部气相入口进入的空气逆流接触并进行环己酮氧化反应,通过加热管壁中的加热介质提供反应所需热量。反应通道内部通过加热管壁中的导热油控制其温度在120℃,反应压力为常压,通过调节计量泵的流量及反应通道的长度来控制反应物料的停留时间为10min,通过调节气体质量流量计控制反应通道中的气液比为10:1。微反应器的液相产物作为目标产品粗品ε-己内酯由液相产物出口处排出,气相产物携带带水剂和水份由气相产物出口处排出,经冷却后通过油水分离进行回收循环使用。所使用的微通道装置主体均采用不锈钢316l加工而成,微混合器的个数为2个,微混合器位于微反应器两侧的对称位置,微混合器中轴线与微反应器的中轴线夹角为60
°
,微筛斜孔分布于微混合器喷嘴柱状体的侧面,水力学直径为100微米,开孔率为15%,斜孔倾角为60
°
。粗品ε-己内酯分析结果表明此过程中环己酮的转化率为91.8%,ε-己内酯选择性为90.7%。
[0038]
【实施例12】
[0039]
使用计量泵输送含氧化剂和催化剂的水相原料,其中双氧水质量分数为40%,催化剂质量分数为1.5%,催化剂中草酸与钨酸钠的用量摩尔比为1.0;使用计量泵输送含有带水剂的油相原料,其中带水剂甲苯质量分数为50%。水相原料中氧化剂与油相原料中环己酮摩尔比为3.5,两股物料分别通过预热器预热在微混合器中50℃下充分进行混合过程。微混合器出口液体经过连接管路后进入微反应器作为液相原料,通过液相原料入口进入微反应器中在与由下部气相入口进入的空气逆流接触并进行环己酮氧化反应,通过加热管壁中的加热介质提供反应所需热量。反应通道内部通过加热管壁中的导热油控制其温度在90℃,反应压力为常压,通过调节计量泵的流量及反应通道的长度来控制反应物料的停留时间为20min,通过调节气体质量流量计控制反应通道中的气液比为10:1。微反应器的液相产物作为目标产品粗品ε-己内酯由液相产物出口处排出,气相产物携带带水剂和水份由气相产物出口处排出,经冷却后通过油水分离进行回收循环使用。所使用的微通道装置主体均采用不锈钢316l加工而成,微混合器的个数为2个,微混合器位于微反应器两侧的对称位置,微混合器中轴线与微反应器的中轴线夹角为60
°
,微筛斜孔分布于微混合器喷嘴柱状体的侧面,水力学直径为100微米,开孔率为15%,斜孔倾角为60
°
。粗品ε-己内酯分析结果表明此过程中环己酮的转化率为89.0%,ε-己内酯选择性为94.5%。
[0040]
【实施例13】
[0041]
使用计量泵输送含氧化剂和催化剂的水相原料,其中双氧水质量分数为40%,催化剂质量分数为1.5%,催化剂中草酸与钨酸钠的用量摩尔比为1.0;使用计量泵输送含有带水剂的油相原料,其中带水剂甲苯质量分数为50%。水相原料中氧化剂与油相原料中环己酮摩尔比为3.5,两股物料分别通过预热器预热在微混合器中50℃下充分进行混合过程。微混合器出口液体经过连接管路后进入微反应器作为液相原料,通过液相原料入口进入微反应器中在与由下部气相入口进入的空气逆流接触并进行环己酮氧化反应,通过加热管壁中的加热介质提供反应所需热量。反应通道内部通过加热管壁中的导热油控制其温度在90℃,反应压力为常压,通过调节计量泵的流量及反应通道的长度来控制反应物料的停留时
间为30min,通过调节气体质量流量计控制反应通道中的气液比为10:1。微反应器的液相产物作为目标产品粗品ε-己内酯由液相产物出口处排出,气相产物携带带水剂和水份由气相产物出口处排出,经冷却后通过油水分离进行回收循环使用。所使用的微通道装置主体均采用不锈钢316l加工而成,微混合器的个数为2个,微混合器位于微反应器两侧的对称位置,微混合器中轴线与微反应器的中轴线夹角为60
°
,微筛斜孔分布于微混合器喷嘴柱状体的侧面,水力学直径为100微米,开孔率为15%,斜孔倾角为60
°
。粗品ε-己内酯分析结果表明此过程中环己酮的转化率为89.8%,ε-己内酯选择性为93.6%。
[0042]
【实施例14】
[0043]
使用计量泵输送含氧化剂和催化剂的水相原料,其中双氧水质量分数为40%,催化剂质量分数为1.5%,催化剂中草酸与钨酸钠的用量摩尔比为1.0;使用计量泵输送含有带水剂的油相原料,其中带水剂甲苯质量分数为50%。水相原料中氧化剂与油相原料中环己酮摩尔比为3.5,两股物料分别通过预热器预热在微混合器中50℃下充分进行混合过程。微混合器出口液体经过连接管路后进入微反应器作为液相原料,通过液相原料入口进入微反应器中在与由下部气相入口进入的空气逆流接触并进行环己酮氧化反应,通过加热管壁中的加热介质提供反应所需热量。反应通道内部通过加热管壁中的导热油控制其温度在90℃,反应压力为常压,通过调节计量泵的流量及反应通道的长度来控制反应物料的停留时间为10min,通过调节气体质量流量计控制反应通道中的气液比为30:1。微反应器的液相产物作为目标产品粗品ε-己内酯由液相产物出口处排出,气相产物携带带水剂和水份由气相产物出口处排出,经冷却后通过油水分离进行回收循环使用。所使用的微通道装置主体均采用不锈钢316l加工而成,微混合器的个数为2个,微混合器位于微反应器两侧的对称位置,微混合器中轴线与微反应器的中轴线夹角为60
°
,微筛斜孔分布于微混合器喷嘴柱状体的侧面,水力学直径为100微米,开孔率为15%,斜孔倾角为60
°
。粗品ε-己内酯分析结果表明此过程中环己酮的转化率为88.3%,ε-己内酯选择性为94.8%。
[0044]
表2
[0045]
实施例891011121314氧化剂双氧水双氧水双氧水双氧水双氧水双氧水双氧水水相原料氧化剂质量分数/%40404040404040水相原料催化剂质量分数/%1.51.51.51.51.51.51.5带水剂甲苯甲苯甲苯甲苯甲苯甲苯甲苯油相原料带水剂质量分数/%50505050505050氧化剂与环己酮摩尔比4.03.53.53.53.53.53.5混合过程温度/℃50405050505050反应过程温度/℃909060120909090反应停留时间/min10101010203010反应体系气液比(体积比)10101010101030微混合器个数2222222微混合器与微反应器夹角/
°
60606060606060微筛孔直径/μm100100100100100100100开孔率/%15151515151515斜孔倾角/
°
60606060606060环己酮转化率/%87.885.176.091.889.089.888.3ε-己内酯选择性/%93.895.498.190.794.593.694.8
[0046]
【实施例15】
[0047]
使用计量泵输送含氧化剂和催化剂的水相原料,其中双氧水质量分数为40%,催化剂质量分数为1.5%,催化剂中草酸与钨酸钠的用量摩尔比为1.0;使用计量泵输送含有带水剂的油相原料,其中带水剂甲苯质量分数为50%。水相原料中氧化剂与油相原料中环己酮摩尔比为3.5,两股物料分别通过预热器预热在微混合器中50℃下充分进行混合过程。微混合器出口液体经过连接管路后进入微反应器作为液相原料,通过液相原料入口进入微反应器中在与由下部气相入口进入的空气逆流接触并进行环己酮氧化反应,通过加热管壁中的加热介质提供反应所需热量。反应通道内部通过加热管壁中的导热油控制其温度在90℃,反应压力为常压,通过调节计量泵的流量及反应通道的长度来控制反应物料的停留时间为10min,通过调节气体质量流量计控制反应通道中的气液比为10:1。微反应器的液相产物作为目标产品粗品ε-己内酯由液相产物出口处排出,气相产物携带带水剂和水份由气相产物出口处排出,经冷却后通过油水分离进行回收循环使用。所使用的微通道装置主体均采用不锈钢316l加工而成,微混合器的个数为4个,微混合器位于微反应器四周的对称位置,微混合器中轴线与微反应器的中轴线夹角为60
°
,微筛斜孔分布于微混合器喷嘴柱状体的侧面,水力学直径为100微米,开孔率为15%,斜孔倾角为60
°
。粗品ε-己内酯分析结果表明此过程中环己酮的转化率为85.2%,ε-己内酯选择性为96.2%。
[0048]
【实施例16】
[0049]
使用计量泵输送含氧化剂和催化剂的水相原料,其中双氧水质量分数为40%,催化剂质量分数为1.5%,催化剂中草酸与钨酸钠的用量摩尔比为1.0;使用计量泵输送含有带水剂的油相原料,其中带水剂甲苯质量分数为50%。水相原料中氧化剂与油相原料中环己酮摩尔比为3.5,两股物料分别通过预热器预热在微混合器中50℃下充分进行混合过程。微混合器出口液体经过连接管路后进入微反应器作为液相原料,通过液相原料入口进入微反应器中在与由下部气相入口进入的空气逆流接触并进行环己酮氧化反应,通过加热管壁中的加热介质提供反应所需热量。反应通道内部通过加热管壁中的导热油控制其温度在90℃,反应压力为常压,通过调节计量泵的流量及反应通道的长度来控制反应物料的停留时间为10min,通过调节气体质量流量计控制反应通道中的气液比为10:1。微反应器的液相产物作为目标产品粗品ε-己内酯由液相产物出口处排出,气相产物携带带水剂和水份由气相产物出口处排出,经冷却后通过油水分离进行回收循环使用。所使用的微通道装置主体均采用不锈钢316l加工而成,微混合器的个数为8个,微混合器位于微反应器四周的对称位置,微混合器中轴线与微反应器的中轴线夹角为60
°
,微筛斜孔分布于微混合器喷嘴柱状体的侧面,水力学直径为100微米,开孔率为15%,斜孔倾角为60
°
。粗品ε-己内酯分析结果表明此过程中环己酮的转化率为84.5%,ε-己内酯选择性为97.1%。
[0050]
【实施例17】
[0051]
使用计量泵输送含氧化剂和催化剂的水相原料,其中双氧水质量分数为40%,催化剂质量分数为1.5%,催化剂中草酸与钨酸钠的用量摩尔比为1.0;使用计量泵输送含有带水剂的油相原料,其中带水剂甲苯质量分数为50%。水相原料中氧化剂与油相原料中环己酮摩尔比为3.5,两股物料分别通过预热器预热在微混合器中50℃下充分进行混合过程。微混合器出口液体经过连接管路后进入微反应器作为液相原料,通过液相原料入口进入微反应器中在与由下部气相入口进入的空气逆流接触并进行环己酮氧化反应,通过加热管壁中的加热介质提供反应所需热量。反应通道内部通过加热管壁中的导热油控制其温度在90
℃,反应压力为常压,通过调节计量泵的流量及反应通道的长度来控制反应物料的停留时间为10min,通过调节气体质量流量计控制反应通道中的气液比为10:1。微反应器的液相产物作为目标产品粗品ε-己内酯由液相产物出口处排出,气相产物携带带水剂和水份由气相产物出口处排出,经冷却后通过油水分离进行回收循环使用。所使用的微通道装置主体均采用不锈钢316l加工而成,微混合器的个数为2个,微混合器位于微反应器两侧的对称位置,微混合器中轴线与微反应器的中轴线夹角为60
°
,微筛斜孔分布于微混合器喷嘴柱状体的侧面,水力学直径为100微米,开孔率为15%,斜孔倾角为60
°
。粗品ε-己内酯分析结果表明此过程中环己酮的转化率为80.7%,ε-己内酯选择性为93.1%。
[0052]
【实施例18】
[0053]
使用计量泵输送含氧化剂和催化剂的水相原料,其中双氧水质量分数为40%,催化剂质量分数为1.5%,催化剂中草酸与钨酸钠的用量摩尔比为1.0;使用计量泵输送含有带水剂的油相原料,其中带水剂甲苯质量分数为50%。水相原料中氧化剂与油相原料中环己酮摩尔比为3.5,两股物料分别通过预热器预热在微混合器中50℃下充分进行混合过程。微混合器出口液体经过连接管路后进入微反应器作为液相原料,通过液相原料入口进入微反应器中在与由下部气相入口进入的空气逆流接触并进行环己酮氧化反应,通过加热管壁中的加热介质提供反应所需热量。反应通道内部通过加热管壁中的导热油控制其温度在90℃,反应压力为常压,通过调节计量泵的流量及反应通道的长度来控制反应物料的停留时间为10min,通过调节气体质量流量计控制反应通道中的气液比为10:1。微反应器的液相产物作为目标产品粗品ε-己内酯由液相产物出口处排出,气相产物携带带水剂和水份由气相产物出口处排出,经冷却后通过油水分离进行回收循环使用。所使用的微通道装置主体均采用不锈钢316l加工而成,微混合器的个数为2个,微混合器位于微反应器两侧的对称位置,微混合器中轴线与微反应器的中轴线夹角为60
°
,微筛斜孔分布于微混合器喷嘴柱状体的侧面,水力学直径为200微米,开孔率为15%,斜孔倾角为60
°
。粗品ε-己内酯分析结果表明此过程中环己酮的转化率为85.3%,ε-己内酯选择性为95.6%。
[0054]
【实施例19】
[0055]
使用计量泵输送含氧化剂和催化剂的水相原料,其中双氧水质量分数为40%,催化剂质量分数为1.5%,催化剂中草酸与钨酸钠的用量摩尔比为1.0;使用计量泵输送含有带水剂的油相原料,其中带水剂甲苯质量分数为50%。水相原料中氧化剂与油相原料中环己酮摩尔比为3.5,两股物料分别通过预热器预热在微混合器中50℃下充分进行混合过程。微混合器出口液体经过连接管路后进入微反应器作为液相原料,通过液相原料入口进入微反应器中在与由下部气相入口进入的空气逆流接触并进行环己酮氧化反应,通过加热管壁中的加热介质提供反应所需热量。反应通道内部通过加热管壁中的导热油控制其温度在90℃,反应压力为常压,通过调节计量泵的流量及反应通道的长度来控制反应物料的停留时间为10min,通过调节气体质量流量计控制反应通道中的气液比为10:1。微反应器的液相产物作为目标产品粗品ε-己内酯由液相产物出口处排出,气相产物携带带水剂和水份由气相产物出口处排出,经冷却后通过油水分离进行回收循环使用。所使用的微通道装置主体均采用不锈钢316l加工而成,微混合器的个数为2个,微混合器位于微反应器两侧的对称位置,微混合器中轴线与微反应器的中轴线夹角为60
°
,微筛斜孔分布于微混合器喷嘴柱状体的侧面,水力学直径为500微米,开孔率为15%,斜孔倾角为60
°
。粗品ε-己内酯分析结果表
明此过程中环己酮的转化率为83.1%,ε-己内酯选择性为95.2%。
[0056]
【实施例20】
[0057]
使用计量泵输送含氧化剂和催化剂的水相原料,其中双氧水质量分数为40%,催化剂质量分数为1.5%,催化剂中草酸与钨酸钠的用量摩尔比为1.0;使用计量泵输送含有带水剂的油相原料,其中带水剂甲苯质量分数为50%。水相原料中氧化剂与油相原料中环己酮摩尔比为3.5,两股物料分别通过预热器预热在微混合器中50℃下充分进行混合过程。微混合器出口液体经过连接管路后进入微反应器作为液相原料,通过液相原料入口进入微反应器中在与由下部气相入口进入的空气逆流接触并进行环己酮氧化反应,通过加热管壁中的加热介质提供反应所需热量。反应通道内部通过加热管壁中的导热油控制其温度在90℃,反应压力为常压,通过调节计量泵的流量及反应通道的长度来控制反应物料的停留时间为10min,通过调节气体质量流量计控制反应通道中的气液比为10:1。微反应器的液相产物作为目标产品粗品ε-己内酯由液相产物出口处排出,气相产物携带带水剂和水份由气相产物出口处排出,经冷却后通过油水分离进行回收循环使用。所使用的微通道装置主体均采用不锈钢316l加工而成,微混合器的个数为2个,微混合器位于微反应器两侧的对称位置,微混合器中轴线与微反应器的中轴线夹角为60
°
,微筛斜孔分布于微混合器喷嘴柱状体的侧面,水力学直径为100微米,开孔率为30%,斜孔倾角为60
°
。粗品ε-己内酯分析结果表明此过程中环己酮的转化率为87.7%,ε-己内酯选择性为94.1%。
[0058]
【实施例21】
[0059]
使用计量泵输送含氧化剂和催化剂的水相原料,其中双氧水质量分数为40%,催化剂质量分数为1.5%,催化剂中草酸与钨酸钠的用量摩尔比为1.0;使用计量泵输送含有带水剂的油相原料,其中带水剂甲苯质量分数为50%。两股物料分别通过预热器预热在微混合器中50℃下充分进行混合过程。微混合器出口液体经过连接管路后进入微反应器作为液相原料,通过液相原料入口进入微反应器中在与由下部气相入口进入的空气逆流接触并进行环己酮氧化反应,通过加热管壁中的加热介质提供反应所需热量。反应通道内部通过加热管壁中的导热油控制其温度在90℃,反应压力为常压,通过调节计量泵的流量及反应通道的长度来控制反应物料的停留时间为10min,通过调节气体质量流量计控制反应通道中的气液比为10:1。微反应器的液相产物作为目标产品粗品ε-己内酯由液相产物出口处排出,气相产物携带带水剂和水份由气相产物出口处排出,经冷却后通过油水分离进行回收循环使用。所使用的微通道装置主体均采用不锈钢316l加工而成,微混合器的个数为2个,微混合器位于微反应器两侧的对称位置,微混合器中轴线与微反应器的中轴线夹角为60
°
,微筛斜孔分布于微混合器喷嘴柱状体的侧面,水力学直径为100微米,开孔率为15%,斜孔倾角为30
°
。粗品ε-己内酯分析结果表明此过程中环己酮的转化率为83.3%,ε-己内酯选择性为96.3%。
[0060]
表3
[0061]
实施例15161718192021微混合器个数4822222微混合器与微反应器夹角/
°
60609060606060微筛孔直径/μm100100100200500100100
开孔率/%15151515153015斜孔倾角/
°
60606060606030环己酮转化率/%85.284.580.785.383.187.783.3ε-己内酯选择性/%96.297.193.195.695.294.196.3
[0062]
【对比例1】在间歇反应器中进行ε-己内酯的合成
[0063]
(1)装置搭建:采用美国parr公司生产的parr 4566台式反应釜作为反应装置,主体均采用不锈钢316l加工而成,反应釜容积300毫升,内径2.5英寸,内深4.0英寸,上述装置采用电加热方式进行温度控制,内置搅拌桨用于反应物料的混合,反应器外接冷凝分馏装置用于将体系内水分脱除并将带水剂回流。
[0064]
(2)ε-己内酯合成:加入100毫升水相原料,选用双氧水作为氧化剂,其中双氧水质量分数为40%,催化剂质量分数为1.5%,催化剂中草酸与钨酸钠的用量摩尔比为1.0;加入60毫升含有带水剂的油相原料,选用甲苯作为带水剂,其中甲苯质量分数为50%。反应物料在反应釜内通过内置搅拌桨充分进行混合后,通过电加热将反应器温度控制在90℃,反应压力为常压,反应过程中生成的水分通过带水剂不断脱除,反应100min后停止加热并收集目标产物。粗品ε-己内酯分析结果表明此过程中环己酮的转化率为86.6%,ε-己内酯选择性为92.3%。
[0065]
由表1可知:实施例1的反应停留时间远小于对比例1,与对比例1相比,实施例1的反应时间的仅为其10%,说明采用本发明所述的方法可大幅提高装置产能。
起点商标作为专业知识产权交易平台,可以帮助大家解决很多问题,如果大家想要了解更多知产交易信息请点击 【在线咨询】或添加微信 【19522093243】与客服一对一沟通,为大家解决相关问题。
此文章来源于网络,如有侵权,请联系删除



tips