一种耐用型超疏水复合材料涂层及其制备方法与流程



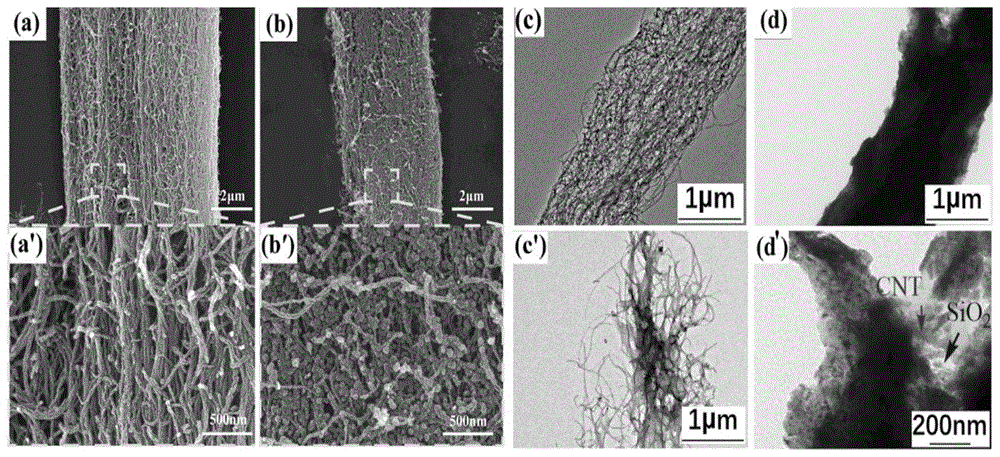
本发明涉及一种耐用型超疏水复合材料涂层及其制备方法,具体涉及一种具有优异抗冲击、耐摩擦及自修复功能的微/纳米结构表面的超疏水复合材料涂层及其制备方法。
背景技术:
具有超疏水性能的材料在自清洁、防冰、防雾、防腐、油水分离等不同领域中具有非常广阔的应用前景。研究表明,通过设计复杂的微米/纳米多级结构,通过引入低表面能物质可实现材料表面超疏水性能。目前,疏水无机纳米粒子(sio2、zno、tio2、cnt、al2o3、石墨烯等)常用于构建微米/纳米多级表面结构来实现材料的疏水性,但是无机纳米颗粒间由于弱的范德华力相互作用,使得超疏水涂层表面表现出脆弱的机械性能和耐受性,严重影响材料的超疏水性,极大限制了超疏水材料在实际生活中的应用。因此,制备具有良好机械性能和稳定耐用的超疏水涂层材料是一项具有挑战性的任务。
综上述分析,针对目前发展超疏水涂层材料存在的问题及其发展趋势,提高涂层组分之间的作用及赋予涂层自修复功能对于构建具有稳定结构的耐用型环保超疏水材料及拓展其应用具有积极意义。
技术实现要素:
本发明针对现有无机粒子间及粒子/粘结剂界面作用弱等导致超疏水涂层耐用性差问题,通过将一种具有强相互粒子作用的结构稳定的由多级纳米粒子组合杂化而成的微米级粒子与环氧体系胶粘剂结合,制备一种具有微/纳米级表面结构的复合材料超疏水涂层。本发明公开的超疏水涂层具有操作简便、耐用和疏水性好的特点,且所制备的涂层具有优异的力学性能和耐磨性。尤其是,本发明疏水纳米sio2粒子存储在acntb的孔隙中,当涂层结构被破坏时,通过热解方式分解胶粘剂,形成的气体产物的可促使sio2迁移至涂层表面,与裸露的cnt构建新的纳米结构表面,可恢复涂层的超疏水性能。
为了达到上述目的,本发明采用的技术方案是:
一种耐用型超疏水复合材料涂层,其制备方法包括以下步骤,将acntb-sio2-偶联剂悬浮液涂覆在acntb-sio2-偶联剂、环氧树脂、二缩水甘油醚封端的聚二甲基硅氧烷、端氨基超支化聚硅氧烷混合物的凝胶体表面,然后固化,得到耐用型超疏水复合材料涂层;或者将acntb-sio2-偶联剂悬浮液涂覆在环氧树脂、端氨基超支化聚硅氧烷混合物的凝胶体表面,然后固化,得到耐用型超疏水复合材料涂层;或者将acntb-sio2-偶联剂悬浮液涂覆在环氧树脂、二缩水甘油醚封端的聚二甲基硅氧烷、端氨基超支化聚硅氧烷混合物的凝胶体表面,然后固化,得到耐用型超疏水复合材料涂层;或者将acntb-sio2-偶联剂悬浮液涂覆在acntb-sio2-偶联剂、环氧树脂、端氨基超支化聚硅氧烷混合物的凝胶体表面,然后固化,得到耐用型超疏水复合材料涂层。
本发明中,将多壁碳取向碳纳米管束、碱、溶剂、正硅酸四乙酯混合反应后,加入硅烷偶联剂,继续反应,得到acntb-sio2-偶联剂。
进一步的,多壁碳取向碳纳米管束、正硅酸四乙酯、硅烷偶联剂、碱、溶剂的重量比为(1~2)∶(9~14)∶(2~5)∶(9~12)∶(100~200);其中,多壁碳取向碳纳米管束(acntb)的束直径为10~25μm,长为30~100μm,具有丰富的孔隙结构,所有cnt沿一定方向取向且cnt间具有明显的物理缠结;硅烷偶联剂为γ-甲基丙烯酰氧基丙基三甲氧基硅烷、六甲基硅氮烷、十二烷基三甲氧基硅烷、乙烯基三甲氧基硅烷、苯基三甲氧基硅烷或者十六烷基三甲氧基硅烷;碱为氨水或三乙醇胺;溶剂为水、乙醇、乙酸乙酯或其混合物。acntb-sio2-偶联剂的制备方法为,室温下将acntb粒子加入碱的溶剂中,搅拌后,加入teos和溶剂的混合溶液,30~60℃反应18-36h后,加入硅烷偶联剂,继续搅拌6h后结束反应,自然冷却至室温,得到的悬浮液用乙醇洗涤2~5次,离心三次,然后在60℃的真空烘箱中干燥12h后得到黑色的微米级acntb-偶联剂改性sio2纳米杂化粒子(acntb-sio2-偶联剂),其中,sio2组装在acntb中孔隙结构中及cnt表面。
本发明中,混合物中,acntb-sio2-偶联剂、环氧树脂、二缩水甘油醚封端的聚二甲基硅氧烷、端氨基超支化聚硅氧烷的重量份分别为0-1份、70-100份、0-70份、30-60份,其中acntb-sio2-偶联剂的用量可以为0,也可以不为0;二缩水甘油醚封端的聚二甲基硅氧烷的用量可以为0,也可以不为0;悬浮液中,acntb-sio2-偶联剂的重量份为4.0-20份。本发明中,acntb-sio2-偶联剂总量为4.0-20份,包括可能添加在凝胶体体系中的acntb-sio2-偶联剂和悬浮液中acntb-sio2-偶联剂用量。
本发明中,环氧树脂为双酚a环氧树脂、双酚f型环氧树脂、双酚s型环氧树脂、氢化双酚a型环氧树脂、酚醛环氧树脂、多官能基缩水甘油醚树脂、缩水甘油酯型环氧树脂、卤素环氧树脂中的一种或者几种;二缩水甘油醚封端的聚二甲基硅氧烷(dgetpdms)为无色透明液体,粘度(25℃)为50-10000mpa.s,比重(25℃)为1.05-1.10。
本发明中,固化工艺为(50~70℃)/1h+(80~150℃)/1-2h。
本发明公开了上述耐用型超疏水复合材料涂层在制备耐磨疏水涂层中的应用;所述耐磨疏水涂层具有多级微/纳米结构表面。
本发明耐用型超疏水复合材料涂层的制备方法为:在30~150℃将环氧树脂、acntb-sio2-偶联剂(0-1份)、dgetpdms(0-70份)、hbpsi混合均匀,维持10-20min后,得到树脂胶粘剂预聚体平铺凝胶,待预聚体达到凝胶状态时,再将含acntb-sio2-偶联剂的甲苯悬浮液滴涂在凝胶体表面,待溶剂挥发之后,经(50~70℃)/1h+(80~150℃)/1-2h固化处理得到具有微/纳米结构表面的耐用型超疏水环氧/acntb-sio2-偶联剂复合材料涂层;acntb-sio2-偶联剂∶甲苯的重量比为1∶(25~50)。
上述技术方案中,acntb-sio2-偶联剂粒子具有稳定的结构,sio2纳米粒子组装在微米级acntb粒子孔隙中可以有效传递acntb中cnt承受的载荷,并限制cnt相对滑移,反之,由于sio2纳米粒子组装在acntb中的孔隙结构中,sio2纳米粒子被cnt固定住。微米级acntb-sio2-偶联剂粒子中cnt与sio2粒子限制与被限制作用关系使得cnt与sio2之间作用增强,从而使得微米级acntb-sio2-偶联剂粒子具有稳定的结构。
上述技术方案中,端氨基超支化聚硅氧烷hbpsi的胺值为0.5~0.65mol/100g,比如0.59mol/100g;hbpsi的合成工艺可以为:在60℃下,将3-氨基丙基三乙氧基硅烷(kh550)、去离子水和无水乙醇混合,氮气保护下搅拌4h,将反应体系冷却至室温后得到透明的液体,使用真空减压装置将反应体系减压,获得hbpsi,其胺值0.59mol/100g,其中kh550、去离子水、无水乙醇的质量比为22:100:16。
本发明制备的超疏水涂层的具有多级微/纳米结构表面,超疏水涂层的表面的水接触角(ca)可到达155-168°,滚动角小于5°。尤其是,超疏水涂层具有优异的抗摩擦性能及力学性能,涂层经100g负载作用下的800目砂纸磨损近300次循环后(一次循环摩擦行程10cm)及经1188kpa的水压冲击120s仍然可保持超疏水性能。由于acntb-sio2-偶联剂粒子的存在,损坏的涂层经加热处理可使得树脂部分分解,且纳米sio2在热及分解产物气流作用下易迁移至涂层表面,其与cnt可构建新的纳米结构表面,可恢复涂层的超疏水性能。
取向碳纳米管束(acntb)是由许多cnt沿一定方向排列通过范德华力作用且碳管之间具有一定的物理缠结结合而成的聚集体(束径一般为微米级),由于单根碳管比较长,物理缠结碳纳米管不易解离,但是acntb具有丰富的孔隙结构,这使得acntb结构不稳定,在外力作用下,acntb中的cnt易发生滑移,cnt间作用较差,不能有效承载。本发明室温下将acntb粒子加入碱的溶剂中,搅拌后加入teos和溶剂的混合溶液,反应后加入硅烷偶联剂,继续搅拌后结束反应,自然冷却至室温,得到的悬浮液经乙醇洗涤、离心、干燥,得到黑色的微米级acntb-偶联剂改性sio2纳米杂化粒子(acntb-sio2-偶联剂),其中,sio2组装在acntb中孔隙结构中及cnt表面,可加强cnt间的作用,有效传递cnt管间作用力,增加acntb结构稳定性,sio2作为一种疏水粒子,其易通过四甲基硅烷(teos)水解并改性获得,acntb的丰富的孔隙结构为储备超疏水sio2粒子准备了充分的条件,sio2粒子储存在acntb孔隙中不但能提高acntb中cnt间的作用,增强acntb结构稳定性,还有助于维持或改善acntb的超疏水性。
由于上述技术方案运用,本发明与现有技术相比具有下列优点:
本发明制备的超疏水涂层具有突出的抗冲击性能,适应绝大多数基体材料,涂层制备工艺简单,由于所制备的sio2@acntb粒子具有明显的结构稳定性,粒子之间具有强的相互作用。因此形成的复合材料涂层具有突出的耐用超疏水性能稳定性。此外,损坏的涂层经高温处理可使得树脂部分分解,使sio2在热及分解产物气流作用下易迁移至涂层表面,与裸露的纳米粒子一起构建新型的纳米结构表面,可恢复涂层的超疏水性能。
附图说明
图1为实施例1中acntb及acntb-sio2-kh570的扫描电镜(sem)及透射电镜(tem)照片,其中,(a,a',c)未超声处理acntb,(c')超声5min处理的acntb,(b,b',d,d')超声5min处理后的acntb-sio2-kh570;
图2为实施例1中acntb及acntb-sio2-kh570的孔径分布及粒子表面积(由比表面与孔隙度分析仪得到);
图3为涂层的水接触角ca、滚动角sa、水滴在涂层表面的数码照片及涂层的sem照片,acntb-sio2-kh570(a,b,g,j),acntb(c,d,h,k),sio2-kh570(e,f,i,l);
图4为acntb-sio2-kh570和acntb压片后的acntb-sio2-kh570(a),acntb(b)涂层水滴在涂层表面的数码照片及涂层的sem照片;
图5为实施例1制备的超疏水e-51/acntb-sio2-kh570复合材料涂层,实施例1-1的e-51涂层及对比例1-2中涂层的水接触角ca及滚动角sa(a)、涂层实施例1-1(b),实施例1(c)及实施例1-2(d)中涂层的sem照片;
图6为实施例1制备的超疏水e-51/acntb-sio2-kh570复合材料涂层经不同水流冲击120s后复合材料涂层的ca与sa(a),水压1329kpa冲击后涂层表面sem图(b);
图7为实施例1制备的超疏水e-51/acntb-sio2-kh570复合材料涂层经砂粒(250g,平均粒径为251μm)不同冲击能量后复合涂层ca与sa(a),经过单颗沙粒冲击能量1.04×10-7j/grain的冲击后的涂层表面sem照片(b);
图8为实施例1制备的超疏水e-51/acntb-sio2-kh570复合材料涂层在100g载荷下800目砂纸打磨后ca和sa(a)及涂层摩擦循环2(b),60(c),260(d)和300(e)摩擦后的sem照片;
图9为实施例1制备的超疏水e-51/acntb-sio2-kh570复合材料涂层损伤且胶带剥离后及在300℃马弗炉中放置9h后的涂层的水接触角照片及sem照片,其中a、b、d对应损伤剥离后加热后涂层;c对应损伤剥离后未加热涂层;
图10为实施例2及对比例2中涂层的sem照片。
具体实施方式
本发明涉及的原料都是常规市售产品,涉及的具体操作方法以及测试方法,除特殊说明外,都是常规条件;下面结合附图和实施例,对本发明技术方案作进一步的描述。
实施例以及对比例中,多壁碳取向碳纳米管束(acntb)的束直径为10~25μm,长为30~100μm。
合成例
在60℃下,将3-氨基丙基三乙氧基硅烷(kh550)、去离子水和无水乙醇混合,氮气保护下搅拌4h,然后将反应体系冷却至室温后得到透明的液体,使用真空减压装置将反应体系减压除去溶剂,获得hbpsi,其胺值0.59mol/100g,其中kh550、去离子水、无水乙醇的重量比为22:100:16。
实施例1
搅拌条件下,将1.0g的acntb颗粒加入9.1g氨水和110g乙醇的混合溶液中,搅拌10min后,滴加入9.35g的teos和40g乙醇的混合溶液,60℃水浴加热,常规搅拌18h后加入2.5g的kh570,继续搅拌6h后,反应结束,自然冷却至室温,得到的悬浮液用乙醇洗涤离心三次,收集acntb-sio2-kh570颗粒,然后在60℃的真空烘箱中干燥12h后得到黑色acntb-sio2-kh570颗粒。
图1是本发明实施例1中acntb、acntb-sio2-kh570扫描电镜(sem)和透射电镜(tem)照片。从图1a,1a’和1c中可以看出,acntb中cnt具有一定的取向排列,cnt之间有明显的缠结,此外,acntb具有丰富的孔隙结构,但从图1c’中可以看出,经过超声处理后acntb的结构完整性明显破坏,cnt间易解离;从图1b,1b’,1d和1d’可以看出在经过超声处理的acntb-sio2-kh570中,碳管表面不仅吸附有纳米sio2颗粒,在碳管与碳管间隙间还镶嵌着纳米sio2,acntb-sio2-kh570的整体结构完整。可见由纳米sio2和acntb杂化构建的acntb-sio2-kh570粒子结构体系结构稳定,在外力作用下不易破环。图2是实施例1中acntb及acntb-sio2-kh570的孔径分布及粒子表面积,从图2中可以看出,由于acntb孔隙中组装了sio2,acntb-sio2-kh570的孔隙明显减少,孔隙变小,但是acntb-sio2-kh570的比表面积大于acntb,这说明acntb-sio2-kh570粒子与涂层的其它组分作用面积增加,有利于提高它们之间的作用力。
为了评估acntb-sio2-kh570粒子的超疏水性,将acntb-sio2-kh570粒子与甲苯按照质量比为1:9的比例配置成acntb-sio2-kh570溶液,将溶液滴涂至载玻片表面,使载玻片表面形成一层致密的acntb-sio2-kh570粒子层,在60℃的烘箱中将溶剂挥发干后继续处理1h,得到acntb-sio2-kh570涂层,采用同样的方法将acntb及sio2-kh570粒子滴涂至载玻片表面得到acntb和sio2-kh570涂层作为对比样品。图3是acntb-sio2-kh570、acntb及sio2-kh570涂层的水接触角(ca)、滚动角(sa)、数码照片及涂层的sem照片acntb涂层的ca和sa值分别为155.7±2.5°和2.5±0.5°。sio2-kh570涂层的ca和sa值分别为152.7±3°和4±0.5°。acntb-sio2-kh570涂层的ca和sa值分别为166.3±1°和1.8±0.5°。显然,acntb-sio2-kh570涂层具有比acntb和sio2-kh570涂层更高的ca和更低的sa值,表明acntb-sio2-kh570涂层具有很好的超疏水性能。对于超疏水表面,液滴与固体之间的气穴可形成稳定的液-气-固界面,具有复杂多级结构的固体表面可以增加表面上的气体分数并提供更稳定的气穴,赋予材料更好的疏水性。acntb-sio2-kh570的sem照片(图1)表明,acntb-sio2-kh570粒子是由acntb和sio2-kh570粒子构成,其具有复杂多级纳米结构的表面,因此可以具有优异的超疏水性。其中,搅拌条件下,向9.1g氨水和110g乙醇的混合溶液中滴加入9.35g的teos和40g乙醇的混合溶液,60℃水浴加热,常规搅拌18h后加入2.5g的kh570,继续搅拌6h后,反应结束,自然冷却至室温,得到的悬浮液用乙醇洗涤离心三次,收集颗粒,然后在60℃的真空烘箱中干燥12h后可得到纳米sio2-kh570颗粒。
图4是acntb-sio2-kh570和acntb涂层经压机常规压缩后得到的acntb-sio2-kh570和acntb片状材料的ca、水滴在涂层表面数码照片及压后sem照片。水在acntb-sio2-kh570和acntb片状材料的ca分别为147.4±2.5°和71.7±2.5°。显然,经压制的acntb-sio2-kh570片状材料仍然具有疏水性。从sem图(图4a)可以看出,压缩得到的acntb-sio2-kh570片状仍然留有很多孔隙结构;而压缩后的acntb间cnt间的孔隙明显减少。由于acntb-sio2-kh570中cnt间sio2颗粒的存在可以维持cnt间的间距,限制cnt的位移,因此可相对较好的维持了原有的结构,这说明acntb-sio2-kh570涂层结构稳定性好。
在30℃,将2g环氧树脂(e-51)、0.02gacntb-sio2-kh570、0.6gdgetpdms(无色透明液体,粘度(25℃)为5000mpa.s,比重(25℃)为1.08)、0.88ghbpsi混合均匀,维持10min后,得到树脂胶粘剂预聚体,随后将胶粘剂预聚体均匀刮涂覆在铝板基底表面(胶粘剂预聚体层厚度为70μm),15min后预聚体达到凝胶状态时,再将含acntb-sio2-kh570的甲苯悬浮液(acntb-sio2-kh570、甲苯分别为0.086g、4.3g)滴涂在树脂预聚体表面,放置30分钟后,经60℃/1h+100℃/1h固化处理得到具有微/纳米结构表面的耐用型超疏水e-51/acntb-sio2-kh570复合材料涂层,为耐用型超疏水复合材料涂层,涂层厚度为100μm。
以下对比例1-1、对比例1-2、对比例1-3为了与实施例对比,体现本发明预料不到的技术效果。
对比例1-1
在30℃,将2g环氧树脂(e-51)、0.6gdgetpdms(无色透明液体,粘度(25℃)为5000mpa.s,比重(25℃)为1.08)、0.88ghbpsi混合均匀,维持10min后,得到树脂胶粘剂预聚体,随后将胶粘剂预聚体均匀刮涂覆在铝板基底表面,待预聚体达到凝胶状态时,经60℃/1h+100℃/1h固化处理得到e-51涂层,涂层厚度为100μm。
对比例1-2
在30℃,将2g环氧树脂(e-51)、0.02gacntb-sio2-kh570、0.6gdgetpdms(无色透明液体,粘度(25℃)为5000mpa.s,比重(25℃)为1.08)、0.88ghbpsi混合均匀,维持10min后,得到树脂胶粘剂预聚体,与acntb-sio2-kh570甲苯悬浮液(acntb-sio2-kh570:甲苯=0.086g:4.3g)共混后,然后刮涂在基材表面,待预聚体达到凝胶状态时,经60℃/1h+100℃/1h固化处理得到e-51/acntb-sio2-kh570-blend涂层,涂层厚度为100μm。
图5为水滴在实施例1制备的超疏水e-51/acntb-sio2-kh570复合材料涂层、对比例1-1的e-51涂层及对比例1-2的e-51/acntb-sio2-kh570-blend涂层上的水接触角ca和滚动角sa值、涂层表面的sem照片。实施例1中涂层的ca和sa分别为:159°和2.5°。可以看出,与对比例1-1及对比例1-2涂层比,实施例1中的e-51/acntb-sio2-kh570复合材料涂层具有优异的超疏水性。从图5c的sem照片可以看出,e-51/acntb-sio2-kh570复合材料涂层具有微米突起,且涂层表面可以明显观察到纳米cnt和sio2粒子的存在,e-51/acntb-sio2-kh570复合材料涂层这种微/纳米结构的表面有利于会吸附大量的空气分子,减少水滴与涂层表面的接触,使涂层表现出优异的超疏水性;而对比例1-1及对比例1-2涂层具有低的ca及高的sa值。
图6是不同水流冲击(120s)后实施例1制备的超疏水e-51/acntb-sio2-kh570复合材料涂层的ca与sa及水压1329kpa冲击后涂层表面sem图。从图6a可以发现,虽然经过不同水压冲击后,ep/acntb-sio2-kh570涂层ca略有减小,sa值逐渐增加,但经过1188kpa的水压冲刷120s后ep/acntb-sio2-kh570涂层ca值为151.4±1.5°,sa值保持在7.1±1.5°。涂层在经过1329kpa的水压冲击后,ca降至147.7±1.5°,sa从2.5±0.5°增加到14.3±3°,此时,涂层的超疏水性才可能消失,但是仍具有高的疏水性。从图6b可以看出,在经过1329kpa的压力冲击后,涂层表面可清晰观察到裸露的cnt,大量裸露的粒子可有效保障涂层的疏水性。
图7是实施例1制备的超疏水e-51/acntb-sio2-kh570复合材料涂层经砂粒(平均粒径为251μm)不同冲击能量后复合涂层ca与sa和经过1.04×10-7j/grain的能量冲击后的涂层表面sem照片。随着石英砂冲击能量增加,冲击后的复合材料涂层的ca和sa值分别缓慢降低和增加。当冲击能量为1.04×10-7j/grain时,涂层ca为151.3±1.6°,sa为11.5±1.9°,表明涂层对砂粒冲击也表现出良好的抗冲击性能。在经历1.04×10-7j/grain的沙粒冲击后,复合材料涂层的损伤区域仍能保持较好的粗糙表面结构,且表面可以观察到突起的纳米粒子,这对超疏水性能的维持起到了积极作用。当冲击能量到达1.3×10-7j/grain时,涂层的ca和sa分别为125.7±2°和45.2±2.9°,失去超疏水性能。
水流冲击实验(图6)和落砂试验(图7)表明实施例1中的复合材料涂层具有优异的耐冲击性能,且具有优异的强度和韧性,粒子之间具有强的相互作用可能有效抵抗外力,对涂层使用寿命的延长起到了积极作用。
图8为实施例1制备的超疏水e-51/acntb-sio2-kh570复合材料涂层在100g载荷下800目砂纸打磨后ca和sa的变化及涂层表面的sem照片。从图中可以看出,当涂层经历2次摩擦循环时,涂层的ca增加,sa略降低;从图8b可以可看出,涂层表面有明显突出的cnt,这种表面结构可以使涂层表面吸附的空气分子增加,减少水滴与涂层表面的接触。尤其是,当摩擦循环达到260次时,涂层的ca和sa保持150°以上和10°以下,这说明涂层仍然具有超疏水性,此时涂层表面仍然具有丰富的纳米粒子。本发明e-51/acntb-sio2-kh570复合材料涂层可经受住近300次砂纸打磨循环(涂层在砂纸表面摩擦行程近30m),说明涂层具有优异的耐磨性,主要原因在于涂层具有优异的力学性能,且与胶粘剂层作用力大,使得涂层能有效抵抗外力磨损。
本实施例1中制备的超疏水e-51/acntb-sio2-kh570复合材料涂层与现有文献报道的超疏水涂层相比,具有如下优势:(1)不含氟,涂层绿色环保;(3)超疏水涂层兼具有高耐冲击性能和摩擦性能,目前文献报道的涂层中,未见水冲击压达到1188kpa,砂粒冲击能达到1.04×10-7j/grain时仍保持超疏水性的涂层,且在具有高冲击性能下,同时报道砂纸打磨循环近300次后仍具有超疏水性能的涂层的文献也未见。
实施例1制备的超疏水e-51/acntb-sio2-kh570复合材料涂层在100g载荷下800目砂纸打磨300次后用3m胶带剥离(去除表面颗粒浮层),得到损伤涂层;然后在300℃马弗炉中放置9h,测试加热前后涂层表面的水接触角照片及sem照片,见图9。e-51/acntb-sio2-kh570复合材料涂层损伤且胶带剥离后失去疏水性,在300°c加热9h后涂层的ca从123°变为160.4±2.5°,sa则小于1°。从sem照片可以看出,受损涂层在300°c加热后,涂层表面聚集有纳米粒子,这种结构有利于涂层超疏水性能的恢复。
对比例1-3
在30℃,将2g环氧树脂(e-51)、0.02gacntb-sio2-kh570、0.6gdgetpdms(无色透明液体,粘度(25℃)为5000mpa.s,比重(25℃)为1.08)、0.88g3-氨基丙基三乙氧基硅烷(kh550)混合均匀,维持10min后,得到树脂胶粘剂预聚体,随后将胶粘剂预聚体均匀刮涂覆在铝板基底表面,15min后预聚体达到凝胶状态时,再将含acntb-sio2-kh570的甲苯悬浮液(acntb-sio2-kh570、甲苯分别为0.086g、4.3g)滴涂在树脂预聚体表面,放置30分钟后,经60℃/1h+100℃/1h固化处理得到具有微/纳米结构表面的e-51/kh550/acntb-sio2-kh570复合材料涂层,在经水压1188kpa/120s、砂粒冲击能量1.04×10-7j/grain及50次砂纸摩擦循环后均不具有超疏水性(ca<130°,sa>15°)。
对比例1-4
在30℃,将2g环氧树脂(e-51)、0.02gacntb-sio2-kh570、0.6gdgetpdms(无色透明液体,粘度(25℃)为5000mpa.s,比重(25℃)为1.08)、0.88ghbpsi混合均匀,维持10min后,得到树脂胶粘剂预聚体,随后将胶粘剂预聚体均匀刮涂覆在铝板基底表面(胶粘剂预聚体层厚度为70μm),15min后预聚体达到凝胶状态时经60℃/1h+100℃/1h固化处理,再滴涂含acntb-sio2-kh570的甲苯悬浮液(acntb-sio2-kh570、甲苯分别为0.086g、4.3g),放置30分钟后,经60℃/1h+100℃/1h固化处理得到涂层,经过1次砂纸摩擦后不具备疏水性(ca<120°,sa>35°)。
综上述分析,利用具有稳定结构的多级纳米粒子杂化形成的超疏水acntb-sio2-kh570粒子制备的超疏水环氧复合材料涂层具有优异的耐用性。
实施例2
搅拌条件下,将1.0g的acntb颗粒加入9.1g氨水和110g乙醇的混合溶液中,搅拌10min后,滴加入9.35g的teos和40g乙醇的混合溶液,60℃水浴加热,匀速搅拌18h后加入2.5g的kh570,继续搅拌6h后,反应结束,自然冷却至室温,得到的悬浮液用乙醇洗涤离心三次,收集acntb-sio2-kh570颗粒,然后在60℃的真空烘箱中干燥12h后得到黑色acntb-sio2-kh570颗粒。
在30℃,将2g环氧树脂(e-51)、0.02gacntb-sio2-kh570、0.6gdgetpdms(无色透明液体,粘度(25℃)为5000mpa.s,比重(25℃)为1.08)、0.88ghbpsi混合均匀,维持10min后,得到树脂胶粘剂预聚体,随后将胶粘剂预聚体均匀刮涂覆在铝板基底表面(胶粘剂预聚体涂层厚度为70μm),15min后预聚体达到凝胶状态时,再将含acntb-sio2-kh570-甲苯悬浮液(acntb-sio2-kh570:甲苯=0.114g:5.7g)滴涂在树脂预聚体表面,放置30分钟后,经60℃/1h+100℃/1h固化处理得到具有微/纳米结构表面的耐用型超疏水e-51/acntb-sio2-kh570复合材料涂层,涂层厚度为100μm。
对比例2-1
在30℃,将2g环氧树脂(e-51)、0.02gacntb-sio2-kh570、0.6gdgetpdms(无色透明液体,粘度(25℃)为5000mpa.s,比重(25℃)为1.08)、0.88ghbpsi混合均匀,维持10min后,得到树脂胶粘剂预聚体,与acntb-sio2-kh570悬浮液(acntb-sio2-kh570:溶剂=0.4g:18g)共混后,然后刮涂在基材表面,经60℃/1h+100℃/1h固化处理得到e-51/acntb-sio2-kh570-blend涂层,涂层厚度为100μm。
图10是实施例2及对比例2-1中涂层的sem照片,表1是实施例2及对比例2-1中涂层的性能数据;测试方法同实施例1。从图10及表1中可以看出,本发明采用少量的acntb-sio2-kh570粒子可使涂层获得超疏水性,涂层表面具有微/纳米结构表面。而采用共混技术需要加入大量的acntb-sio2-kh570粒子才能使涂层获得较高的ca,但是sa却明显大于10°,涂层不具备超疏水性。由表1可知,实施例2中的涂层在经水压1188kpa、砂粒冲击能量1.04×10-7j/grain及250次砂纸摩擦循环后均具有超疏水性,涂层破坏后可在300°c加热9h恢复超疏水性能。
对比例2-2
搅拌条件下,向9.1g氨水和110g乙醇的混合溶液中滴加入9.35g的teos和40g乙醇的混合溶液,60℃水浴加热,匀速搅拌18h后加入2.5g的kh570,继续搅拌6h后,反应结束,自然冷却至室温,得到的悬浮液用乙醇洗涤离心三次,收集颗粒,然后在60℃的真空烘箱中干燥12h后得到sio2-kh570颗粒。
在30℃,将2g环氧树脂(e-51)、0.02gsio2-kh570、0.6gdgetpdms(无色透明液体,粘度(25℃)为5000mpa.s,比重(25℃)为1.08)、0.88ghbpsi混合均匀,维持10min后,得到树脂胶粘剂预聚体,随后将胶粘剂预聚体均匀刮涂覆在铝板基底表面(胶粘剂预聚体层厚度为70μm),15min后预聚体达到凝胶状态时,再将含sio2-kh570-甲苯悬浮液(sio2-kh570:甲苯=0.114g:5.7g)滴涂在树脂预聚体表面,放置30分钟后,经60℃/1h+100℃/1h固化处理得到e-51/sio2-kh570复合材料涂层(涂层厚度为100μm),在经水压1188kpa/120s、砂粒冲击能量1.04×10-7j/grain及80次砂纸摩擦循环后均不具有超疏水性(ca<130°,sa>15°)。
对比例2-3
搅拌条件下,60℃下,向10g的acntb颗粒和100g乙醇的混合溶液中滴加入0.2g的kh570,继续搅拌6h后,反应结束,自然冷却至室温,得到的悬浮液用乙醇洗涤离心三次,收集颗粒,然后在60℃的真空烘箱中干燥12h后得到acntb-kh570颗粒。
在30℃,将2g环氧树脂(e-51)、0.02gacntb-kh570、0.6gdgetpdms(无色透明液体,粘度(25℃)为5000mpa.s,比重(25℃)为1.08)、0.88ghbpsi混合均匀,维持10min后,得到树脂胶粘剂预聚体,随后将胶粘剂预聚体均匀刮涂覆在铝板基底表面(胶粘剂预聚体层厚度为70μm),15min后预聚体达到凝胶状态时,再将含acntb-kh570-甲苯悬浮液(acntb-kh570:甲苯=0.114g:5.7g)滴涂在树脂预聚体表面,放置30分钟后,经60℃/1h+100℃/1h固化处理得到e-51/acntb-kh570复合材料涂层(涂层厚度为100μm),在经水压1188kpa/120s、砂粒冲击能量1.04×10-7j/grain及30次砂纸摩擦循环后均不具有超疏水性(ca<110°,sa>35°)。
综上述分析,利用具有稳定结构的多级纳米粒子杂化形成的超疏水acntb-sio2-kh570粒子制备的超疏水环氧复合材料涂层具有优异的耐用性。
实施例3
搅拌条件下,将2.0g的acntb颗粒加入12g氨水和150g乙醇的混合溶液中,搅拌10min后,逐滴加入14g的teos和50g乙醇的混合溶液,60℃水浴加热,常规搅拌36h后加入5g的乙烯基三乙氧基硅烷(vtes),继续搅拌6h后,反应结束,自然冷却至室温,得到的悬浮液用乙醇洗涤离心三次,收集acntb-sio2-vtes颗粒,然后在60℃的真空烘箱中干燥12h后得到黑色acntb-sio2-vtes颗粒。
在80℃,将2g环氧树脂(e-44)、0.6ghbpsi混合均匀,维持20min后,得到树脂胶粘剂预聚体,随后将胶粘剂预聚体均匀刮涂覆在铝板基底表面(胶粘剂预聚体层厚度为70μm),待预聚体达到凝胶状态时,再将含预先准备好的acntb-sio2-vtes-甲苯悬浮液(acntb-sio2-vtes:甲苯=0.08g:2g)逐渐滴涂在树脂预聚体表面,待溶剂挥发之后,经50℃/1h+80℃/2h固化处理得到具有微/纳米结构表面的耐用型超疏水e-44/acntb-sio2-vtes复合材料涂层,涂层厚度为100μm。
对比例3-1
在80℃,将2g环氧树脂(e-44)、0.6ghbpsi混合均匀,维持20min后,得到树脂胶粘剂预聚体,与acntb-sio2-vtes悬浮液(acntb-sio2-vtes:溶剂=0.08g:2g)共混后,然后刮涂在基材表面,经50℃/1h+80℃/2h固化处理得到e-44/acntb-sio2-vtes-blend涂层,涂层厚度为100μm。
表2是实施例3及对比例3中涂层的性能数据。从表2中可以看出,当采用相同少量的acntb-sio2-vtes粒子时,利用本发明技术制备的复合材料涂层可获得优异的超疏水性,而采用共混技术获得的涂层的ca低于150°,sa明显大于10°,涂层不具备超疏水性。由表2可知,实施例3中的涂层在经水压1188kpa/120s、砂粒冲击能量1.04×10-7j/grain及300次砂纸摩擦循环后均具有超疏水性,涂层破坏后可在300°c加热9h恢复超疏水性能。
对比例3-2
搅拌条件下,向12g氨水和150g乙醇的混合溶液中逐滴加入14g的teos和50g乙醇的混合溶液,60℃水浴加热,常规搅拌36h后加入5g的乙烯基三乙氧基硅烷(vtes),继续搅拌6h后,反应结束,自然冷却至室温,得到的悬浮液用乙醇洗涤离心三次,收集sio2-vtes颗粒,然后在60℃的真空烘箱中干燥12h后得到sio2-vtes颗粒。
在80℃,将2g环氧树脂(e-44)、0.6ghbpsi混合均匀,维持20min后,得到树脂胶粘剂预聚体,随后将胶粘剂预聚体均匀刮涂覆在铝板基底表面(胶粘剂预聚体层厚度为70μm),待预聚体达到凝胶状态时,再将含预先准备好的sio2-vtes-甲苯悬浮液(sio2-vtes:甲苯=0.08g:2g)逐渐滴涂在树脂预聚体表面,待溶剂挥发之后,经50℃/1h+80℃/2h固化处理得到e-44/sio2-vtes复合材料涂层(涂层厚度为100μm),在经水压1188kpa/120s、砂粒冲击能量1.04×10-7j/grain及70次砂纸摩擦循环后均不具有超疏水性(ca<140°,sa>10°)。
综上述分析,利用具有稳定结构的多级纳米粒子杂化形成的超疏水acntb-sio2-vtes粒子制备的超疏水环氧复合材料涂层具有优异的耐用性。
实施例4
搅拌条件下,将1.2g的acntb颗粒加入9g氨水和90g乙醇的混合溶液中,搅拌10min后,逐滴加入9.0g的teos和10g乙醇的混合溶液,60℃水浴加热,匀速搅拌18h后加入2g的十二烷基三甲氧基硅烷(dtms),继续搅拌6h后,反应结束,自然冷却至室温,得到的悬浮液用乙醇洗涤离心三次,收集acntb-sio2-dtms颗粒,然后在60℃的真空烘箱中干燥12h后得到黑色acntb-sio2-dtms颗粒。
在50℃,将1.4g酚醛环氧树脂(f51)、1.4gdgetpdms和1.2ghbpsi混合均匀,20min后得到树脂胶粘剂体系,随后将胶粘剂体系均匀刮涂覆在铝板基底表面(胶粘剂预聚体层厚度为70μm),体系达到凝胶状态时,再将含预先准备好的acntb-sio2-dtms-甲苯悬浮液(acntb-sio2-dtms:甲苯=0.4g:20g)逐渐滴涂在树脂预聚体表面,待溶剂挥发之后,经70℃/1h+150℃/1h固化处理得到f51/acntb-sio2-dtms复合材料涂层,涂层厚度为100μm。
对比例4-1
在50℃,将2g环氧树脂(f51)、1.4gdgetpdms、1.2ghbpsi混合均匀,20min后得到树脂胶粘剂预聚体,与acntb-sio2-dtms悬浮液(acntb-sio2-dtms:溶剂=0.4g:20g)共混后,然后刮涂在基材表面,经70℃/1h+150℃/1h固化处理得到f51/acntb-sio2-dtms涂层,涂层厚度为100μm。
表3是实施例4及对比例4-1中涂层性能数据。从表3中可以看出,采用相同含量的acntb-sio2-dtms粒子,利用本发明技术可使涂层获得优异的超疏水性;而采用共混技术的涂层获得ca低于150°,sa明显大于10°,涂层不具备超疏水性。由表3可知,实施例4中的涂层在经水压1188kpa/120s、砂粒冲击能量1.04×10-7j/grain及250次砂纸摩擦循环后均具有超疏水性,涂层破坏后可在320°c加热5h恢复超疏水性能。
对比例4-2
搅拌条件下,向9g氨水和90g乙醇的混合溶液中逐滴加入9.0g的teos和10g乙醇的混合溶液,60℃水浴加热,匀速搅拌18h后加入2g的十二烷基三甲氧基硅烷(dtms),继续搅拌6h后,反应结束,自然冷却至室温,得到的悬浮液用乙醇洗涤离心三次,收集颗粒,然后在60℃的真空烘箱中干燥12h后得到sio2-dtms颗粒。
搅拌条件下,将10g的acntb颗粒加入90g乙醇的中,搅拌10min后,60℃水浴加热下加入0.5g的十二烷基三甲氧基硅烷(dtms),继续搅拌6h后,反应结束,自然冷却至室温,得到的悬浮液用乙醇洗涤离心三次,收集颗粒,然后在60℃的真空烘箱中干燥12h后得到acntb-dtms颗粒。
在50℃,将1.4g酚醛环氧树脂(f51)、1.4gdgetpdms和1.2ghbpsi混合均匀,20min后得到树脂胶粘剂体系,随后将胶粘剂体系均匀刮涂覆在铝板基底表面(胶粘剂预聚体层厚度为70μm),体系达到凝胶状态时,再将含预先准备好的acntb-dtms/sio2-dtms/甲苯悬浮液(acntb-dtms、sio2-dtms、甲苯的重量分别为0.2g、0.2g、20g)逐渐滴涂在树脂预聚体表面,待溶剂挥发之后,经70℃/1h+150℃/1h固化处理得到复合材料涂层,涂层厚度为100μm,在经水压1188kpa/120s、砂粒冲击能量1.04×10-7j/grain及20次砂纸摩擦循环后均不具有超疏水性(ca<130°,sa>20°)。
综上述分析,利用多级纳米粒子杂化形成的acntb-sio2-dtms粒子制备的超疏水环氧复合材料涂层具有优异的耐用性。
为了确保sio2可有效传递载荷,sio2必须有效嵌入acntb的孔隙中。本发明中,cnt与sio2之间有强的相互作用,这样sio2能有效传递载荷,从而有效增强acntb结构稳定性,确保后续合成的涂层具有稳定的力学性能与超疏水性能稳定性。进一步的,acntb中的孔隙可作为微反应容器或模腔,有利于teos渗入并原位水解产生纳米sio2嵌入孔隙中,此时,sio2粒子被限制在孔隙结构中,当acntb受力时,sio2可在cnt间传递载荷,提acntb粒子的承载作用力。acntb-sio2体系中纳米粒子之间具有强的相互作用,即具有稳定结构的acntb-sio2体系粒子可以提高涂层的微观稳定性加强。更有趣的是,acntb-sio2体系基本保留了原有的acntb的高的长束径比,其在重力场和流体动力的驱动下,易沿流体方向取向,构建有特殊表面结构涂层。由于sio2镶嵌在acntb孔隙中,使得单位体积acntb-sio2粒子的比表面积也远大于acntb粒子的比表面积,因此,acntb-sio2粒子与胶粘剂作用会增强,有利于超疏水涂层稳定性的提高。
起点商标作为专业知识产权交易平台,可以帮助大家解决很多问题,如果大家想要了解更多知产交易信息请点击 【在线咨询】或添加微信 【19522093243】与客服一对一沟通,为大家解决相关问题。
此文章来源于网络,如有侵权,请联系删除


