一种车载显示屏的双面胶膜以及制备方法与流程



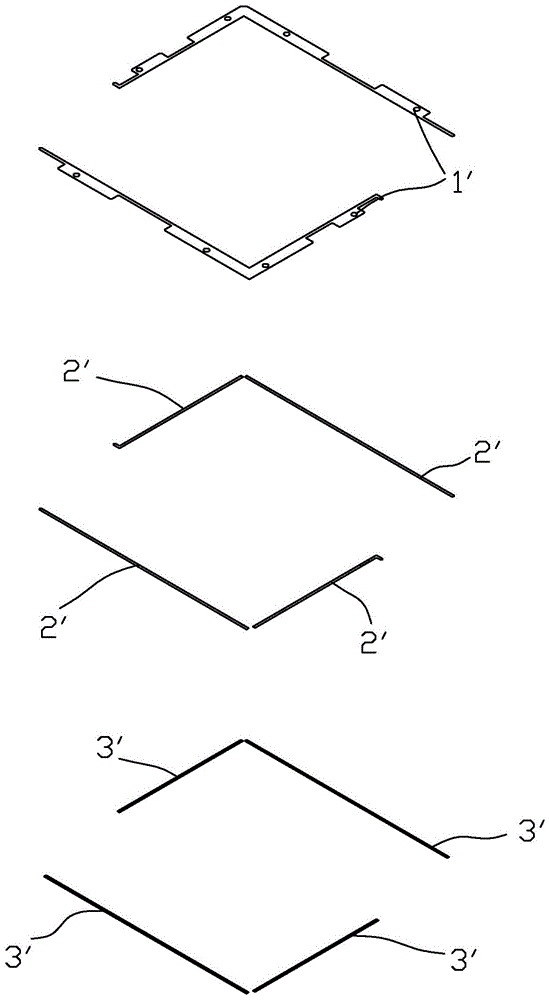
本发明涉及车载显示屏领域,具体涉及一种车载显示屏的双面胶膜以及制备方法。
背景技术:
现有的用于车载显示屏的双面胶结构如图1所示,产品由四条胶条3’、四条小承载膜2’以及二个l型的大承载膜1’组成,一个l型的大承载膜1’的两条边各粘合一条小承载膜2’,每个小承载膜2’粘合一条胶条3’,小胶条3’分别用治具套孔组装形成一个回字型。该结构的缺点在于:产品生产过程中需要生产两次l型结构,生产机台调试耗时,手工剪条耗时,客户端组装需要分两次套孔定位,然后需要分四次撕掉小承载膜,效率低成本高。需要进一步的改进。
技术实现要素:
为此,本发明提供的一种车载显示屏的双面胶膜以及制备方法,能够有效解决上述问题。
为实现上述目的,本发明提供的技术方案如下:
一种车载显示屏的双面胶膜,包括:
大承载膜,所述大承载膜具有一粘性表面;
反贴膜,所述反贴膜为无粘性膜,并贴合于大承载膜的粘性表面;
小承载膜,所述小承载膜为无粘性的离型膜,所述小承载膜为呈方框型结构的一体膜,所述小承载膜设置于反贴膜的外围并贴合于大承载膜的粘性表面;
双面胶条,双面胶条设有四条,并分别粘于小承载膜的四条边框上;
托底离型膜,所述托底离型膜覆盖所述双面胶条、小承载膜以及反贴膜的表面。
进一步的,所述大承载膜上还开设有避让口,所述避让口由反贴膜所覆盖。
进一步的,所述大承载膜还向外延伸形成有手撕耳部,所述手撕耳部的粘性表面贴设有无粘性的无粘膜片。
进一步的,所述小承载膜也向外延伸形成有手撕耳部。
进一步的,所述小承载膜的手撕耳部的形成位置与大承载膜的手撕耳部的形成位置相重合。
一种车载显示屏的双面胶膜的制备方法,包括如下步骤:
a1,提供一第一流水线和托底膜,该托底膜作为传送载带贯通整个第一流水线;
a2,将大承载膜原膜贴于第一托底膜上,并撕去大承载膜原膜自带的保护膜层,留下具有一粘性表面的大承载膜层;
a3,将无粘性的反贴膜原膜贴合于大承载膜层的粘性表面,切出所需要的反贴膜的结构,并排除多余的废料;
a4,在步骤a3所得到的中间产品的表面贴小承载膜原膜;
a5,在小承载膜原膜的表面贴第一双面胶原膜,撕去第一双面胶原膜自带的保护膜层,形成第一双面胶层;
a6,在裸露的第一双面胶层的表面贴一层无粘性的第一面纸层;将第一双面胶层切出横向分布的二条双面胶条,并排除多余的废料;
a7,提供第二流水线,第二流水线上制备纵向的双面胶条,并通过异步拼接的方式将纵向的双面胶条拼接至第一流水线上小承载膜原膜的表面,横向分布的二条双面胶条和纵向分布的二条双面胶条拼接形成一方框形结构;
a8,在第一流水线上排除由第二流水线拼接至小承载膜原膜的废料;
a9,在步骤a8所得到的产品表面贴一层无粘性的第二面纸层;
a10,将托底膜之上的所有膜层一次冲切成型,并排除废料;
a11,在步骤a10形成的产品表面贴一离型膜层,并通过冲切形成单个的双面胶膜成品。
进一步的,步骤a3中,还包括在大承载膜上切出避让口,所述避让口由反贴膜所覆盖。
进一步的,所述步骤a10中,排除废料的具体步骤还包括:
a10-1,上拉排除方框型结构的小承载膜外围的外框废料;
a10-2,表面贴合排废胶带,通过提取刀提取位于方框型结构的小承载膜中间的废料;
a10-3,贴合第三面纸层,排除剩余废料;
a10-4,贴合马拉胶带,排除剩余废料。
进一步的,所述大承载膜还向外延伸形成有手撕耳部,所述手撕耳部的粘性表面贴设有无粘性的无粘膜片。
进一步的,所述小承载膜也向外延伸形成有手撕耳部;所述小承载膜的手撕耳部的形成位置与大承载膜的手撕耳部的形成位置相重合。
通过本发明提供的技术方案,具有如下有益效果:
四条双面胶条直接贴合于一体连接且呈方框型结构的小承载膜上,小承载膜再贴合于一张大的大承载膜上;使用时,将托底离型膜撕去,此时四条双面胶条在大承载膜和一体连接的小承载膜的支撑下能够很好的保持定位,并能够轻易的粘贴装配,后续再依次撕去大承载膜和小承载膜,操作简便(分别撕一次即可),可有效提高效率。
小承载膜的中间设有反贴膜,以阻隔大承载膜的粘性,撕除更快捷、方便,小承载膜直接是一整张撕开,精准组装,提高效率和降低人工组装成本。
双面胶膜的制备中,采用主流水线(即第一流水线)和第二流水线的异步拼接一次制备成型,直接用边定位,无需重复;减少机台调试次数,也无需人工剪条,效率高。
对于同行业竞争,成本和技术上有绝对的市场优势。
附图说明
图1所示为背景技术中双面胶膜的结构分解示意图;
图2所示为实施例中双面胶膜的结构分解示意图;
图3所示为实施例中双面胶膜的制备工艺示意图。
具体实施方式
为进一步说明各实施例,本发明提供有附图。这些附图为本发明揭露内容的一部分,其主要用以说明实施例,并可配合说明书的相关描述来解释实施例的运作原理。配合参考这些内容,本领域普通技术人员应能理解其他可能的实施方式以及本发明的优点。图中的组件并未按比例绘制,而类似的组件符号通常用来表示类似的组件。
现结合附图和具体实施方式对本发明进一步说明。
参照图2所示,本实施例提供一种车载显示屏的双面胶膜,包括:大承载膜10、反贴膜20、小承载膜30、双面胶条40以及托底离型膜50,所述大承载膜10具有一粘性表面(在图2中粘性表面为下表面);所述反贴膜20为无粘性膜,并贴合于大承载膜10的粘性表面;所述小承载膜30为无粘性的离型膜,所述小承载膜30为呈方框型结构的一体膜,即由同一张膜模切而成的。所述小承载膜30设置于反贴膜20的外围并贴合于大承载膜10的粘性表面;所述双面胶条40为泡棉双面胶,设有四条,并分别粘于小承载膜30的四条边框上;所述托底离型膜50覆盖所述双面胶条40、小承载膜30以及反贴膜20的表面(图2中为下表面)。所述托底离型膜50和大承载膜10共同将反贴膜20、小承载膜30和双面胶条40包覆住。
四条双面胶条40直接贴合于一体连接且呈方框型结构的小承载膜30上,小承载膜30再贴合于一张大的大承载膜10上;使用时,将托底离型膜50撕去,此时四条双面胶条40在大承载膜10和一体连接的小承载膜30的支撑下能够很好的保持定位,并能够轻易的粘贴装配,后续再依次撕去大承载膜10和小承载膜30,操作简便(分别撕一次即可),可有效提高效率。
同时,小承载膜30的中间设有反贴膜20,以阻隔大承载膜10的粘性,撕除更快捷、方便,小承载膜30直接是一整张撕开,精准组装,提高效率和降低人工组装成本。
本实施例还提供一种上述图2所示的车载显示屏的双面胶膜的制备方法,结合图3所示,包括如下步骤(下述以单个产品的描述为例):
a1,提供一第一流水线和托底膜100(本实施例中定义为第一托底膜100),该第一流水线上设置有1-16的16个工位,该托底膜100作为传送载带贯通整个第一流水线,即贯通16个工位。
a2,将大承载膜原膜101贴于第一托底膜100上,并撕去大承载膜原膜101自带的保护膜层,留下具有一粘性表面的大承载膜层;
该步骤由第1工位完成,即大承载膜原膜101和托底膜100均设置于第1工位的前方,通过第1工位的辊轮压紧贴合,第1工位输出后撕去大承载膜原膜101自带的保护膜层,大承载膜层即作为图2中大承载膜10的原料,并继续往下传送。
a3,将无粘性的反贴膜原膜102贴合于大承载膜层的粘性表面,切出所需要的反贴膜20的结构,并排除多余的废料;
该步骤由第2工位完成,无粘性的反贴膜原膜102设置于第2工位的前方并贴合于大承载膜层的粘性表面,第2工位上设置有a刀,通过该a刀模切出图2中反贴膜20的结构,即上述位于小承载膜30中间的反贴膜20部分;完成模切后排除多余的废料;产品继续往下传送。
a4,在步骤a3所得到的中间产品的表面贴小承载膜原膜103;
该步骤由第3工位完成,小承载膜原膜103设置于第3工位的前方,与第2工位输出的产品贴合后通过第3工位的辊轮压紧,使其贴合于大承载膜层的粘性表面,此时,小承载膜原膜103是一整张膜,其中间区域是覆盖在反贴膜20上,外围是粘合于大承载膜层的粘性表面。
a5,在小承载膜原膜103的表面贴第一双面胶原膜104,撕去第一双面胶原膜104自带的保护膜层,形成第一双面胶层;
该步骤由第4工位完成,第一双面胶原膜104设置于第4工位的前方,与第3工位输出的产品贴合后通过第4工位的辊轮压紧,使其贴合于小承载膜原膜103上;随后撕去第一双面胶原膜104自带的保护膜层,裸露出整面的胶层,形成第一双面胶层。
a6,在裸露的第一双面胶层的表面贴一层无粘性的第一面纸层105;将第一双面胶层切出横向分布的二条双面胶条,并排除多余的废料;
该步骤由第5工位完成,第一面纸层105设置于第5工位的前方,与第4工位输出的产品贴合(即贴于裸露的第一双面胶层的表面)后,一起输入至第5工位,第5工位设置有b刀,该b刀只切出横向(即沿传送方向)的二条双面胶条,模切完成后排除废料,该废料包括多余的双面胶以及第5工位前贴的第一面纸层105。完成后继续向后传送。第6工位只是传送工位,之后传送至第7工位。
a7,提供第二流水线,第二流水线上制备纵向的双面胶条,并通过异步拼接的方式将纵向的双面胶条拼接至第一流水线上小承载膜原膜103的表面,横向分布的二条双面胶条和纵向分布的二条双面胶条拼接形成一方框形结构。
该第8工位和第9工位同时也作为第二流水线,即第8工位和第9工位均包含上层机构和下层机构,上层机构作为第二流水线,下层机构作为第一流水线的一部分。第二流水线中,其传送方向与第一流水线相反,是由第9工位传送至第8工位,再由第8工位传送至第7工位。
将托底膜200(本实施例中定义为第二托底膜200)和复合好的双面胶(本实施例中定义为第二双面胶原膜201)经第9工位的后方(前后方向以第一流水线的传送方向为基准)输入,经第9工位的辊轮压紧后输出至第8工位,由第9工位的上层机构输出的产品与离型膜202经第8工位的后方输入,同时,在进入第8工位前,先剥离第二托底膜200,使第二双面胶原膜201直接与离型膜202贴合。
第8工位具有c刀,该c刀为纵向切断刀,用于切出纵向分布的双面胶条,由第8工位输出后通过排废胶带203进行排废。之后再传送至第7工位。
在第7工位上,具有第一流水线输入的产品以及第二流水线输入的纵向分布的双面胶条;通过异步拼接的方式将纵向分布的双面胶条粘于第一流水线的小承载膜原膜103上,此时,横向分布的二条双面胶条和纵向分布的二条双面胶条拼接形成一方框形结构。
具体的,异步拼接为现有拼接工艺,在此不再详述。
再具体的,第8工位和第9工位的下层机构只起到传送的作用。
a8,在第一流水线上排除由第二流水线拼接至小承载膜原膜103的废料;
经第9工位传送至第10工位,再经第10工位输出后进行该步骤的排除废料,该废料如由第二流水线的离型膜202等。
a9,在步骤a8所得到的产品表面贴一层无粘性的第二面纸层106;
该步骤由进入第11工位前完成,将第二面纸层106覆盖住整个表面,以起到隔绝双面胶条的胶层。
a10,将托底膜100之上的所有膜层一次模切成型,并排除废料;
该步骤由第11工位完成,第11工位具有d刀,通过d刀的模切将托底膜100之上的大承载膜层、小承载膜原膜103以及其上的双面胶条的形状一次模切成型,形成如图2中大承载膜10、小承载膜30以及双面胶条40的结构,即形成方框型结构的小承载膜30以及贴于小承载膜30表面的双面胶条40;所述小承载膜30位于反贴膜20的外围。
具体的,因前方工位(即步骤a6和a7)在设置双面胶条时可能存在对位偏差等因素,因此,在前方工位设置的双面胶条的尺寸较大,再通过该第11工位的d刀一次模切成型,能够保证双面胶条40与小承载膜30的对位。
再具体的,本步骤中,排除废料的具体步骤还包括:
a10-1,上拉排除方框型结构的小承载膜30外围的外框废料;
该步骤由第11工位输出后直接拉取大承载膜层的废料即可。
a10-2,表面贴合排废胶带107,通过提取刀提取位于方框型结构的小承载膜30中间的废料;
该步骤由第12工位完成,在输入第12工位之前先在产品表面贴合排废胶带107,用于粘贴在反贴膜20上层的小承载膜废料,第12工位设有e刀(即提取刀),将排废胶带107和小承载膜废料提出,实现位于中间的小承载膜废料的排废。
a10-3,贴合第三面纸层108,排除废料;
该步骤直接在第12工位和第13工位之间完成,用于将双面胶条等有粘性的剩余废料排除。
具体的,第13工位只作为传送工位。
a10-4,贴合马拉胶带109,排除废料。
该步骤由第14工位完成,在第14工位之前贴合马拉胶带109,经第14工位的辊轮压紧后直接拉取进行收废,用于将无粘性的一些膜层废料的排除。
通过上述排废的步骤,能够很好的将废料排除,保证产品的洁净度,以供后续继续作业。当然的,在其它实施例中,排废的操作不局限于此。
a11,在步骤a10形成的产品表面贴一离型膜层1001,并通过模切形成单个的双面胶膜成品。模切后的离型膜层即为托底离型膜50。
该步骤由第15工位和第16工位完成,在第15工位贴上离型膜层1001,并通过第15工位的辊轮压紧,之后输出至第16工位,第16工位上设置有f刀,通过f刀将托底离型膜50模切成型。
完成上述步骤后,即形成上述所述的车载显示屏的双面胶膜。在第16工位的后端设置有接片槽300,作为承载的托底膜100实现收卷,而成品则落在接片槽300内实现收集。
双面胶膜的制备中,采用主流水线(即第一流水线)和第二流水线的异步拼接一次制备成型,直接用边定位,无需重复;减少机台调试次数,也无需人工剪条,效率高。
具体的,上述公开了a刀、b刀、c刀、d刀、e刀和f刀的功能,其上述各种刀具的结构和形状,是本领域的技术人员通过上述的功能描述能够自行的实现的,在此就不再一一详述。
进一步的,本实施例中,所述大承载膜10上还开设有避让口11,所述避让口11由反贴膜20所覆盖。该避让口11的设置用于避让线路板上的ic(integratedcircuit)器件等。具体的,在实际制备时,在第2工位的a刀进行切割成型。当然的,在其它实施例中,也可以无需设置该避让口11。
进一步的,本实施例中,所述大承载膜10还向外延伸形成有手撕耳部12(定义为第一手撕耳部12),所述手撕耳部12(即第一手撕耳部12)的粘性表面贴设有无粘性的无粘膜片60。设置该第一手撕耳部12,能够快速的将大承载膜10撕去,手撕操作简单。该第一手撕耳部12由第11工位一次冲切时成型。
再具体的,无粘膜片60与反贴膜20属于同一种膜,均是由被模切的反贴膜原膜102形成的。即在第2工位上,a刀同时切出了反贴膜20和该无粘膜片60,将无粘膜片60留在对应的位置,该位置即为后续切出第一手撕耳部12的位置。
再进一步的,本实施例中,所述小承载膜30也向外延伸形成有手撕耳部31(定义为第二手撕耳部31)。设置该第二手撕耳部31,能够快速的将小承载膜30撕去,手撕操作简单。
再具体的,所述小承载膜30的手撕耳部31的形成位置与大承载膜10的手撕耳部12的形成位置相重合。二个手撕耳部(第一手撕耳部12和第二手撕耳部31)可在第11工位一次冲切时成型,节省工艺步骤。当然的,在其它实施例中不局限于此。
尽管结合优选实施方案具体展示和介绍了本发明,但所属领域的技术人员应该明白,在不脱离所附权利要求书所限定的本发明的精神和范围内,在形式上和细节上可以对本发明做出各种变化,均为本发明的保护范围。
起点商标作为专业知识产权交易平台,可以帮助大家解决很多问题,如果大家想要了解更多知产交易信息请点击 【在线咨询】或添加微信 【19522093243】与客服一对一沟通,为大家解决相关问题。
此文章来源于网络,如有侵权,请联系删除


