一种整体编织型摩擦材料的制备方法与流程



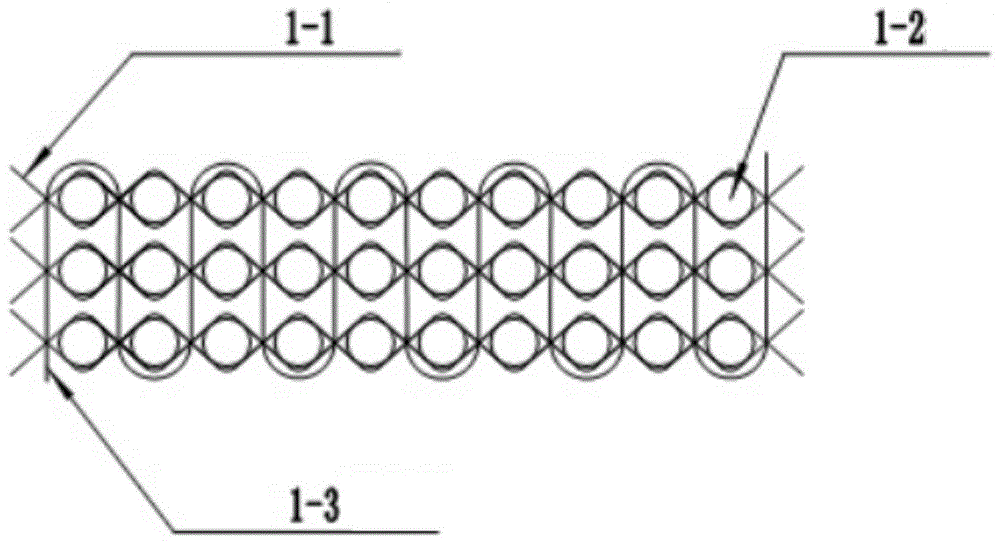
本发明涉及离合器用摩擦材料
技术领域:
,具体涉及一种整体编织型摩擦材料的制备方法。
背景技术:
:摩擦材料是各类机械制动和传动的关键零件,在汽车、摩托车、船舶、飞机、工程机械、运输机械、化工机械、矿山机械、石油机械、工程机械等各种机械中都不可缺少。摩擦材料在其应用领域属于关键的安全配件,虽然在主机中所占的成本比例很小,但其功能地位十分重要。摩擦材料质量的好坏,首当其冲地影响着机械的使用效果,好则意味成功、顺利,坏则导致失败、灾难。摩擦材料除了要求能达到制动或传动所需的力矩要求,还需要尽可能的保护对偶面,并且还要便于安装。尤其是需要在使用现场安装的摩擦片,该安装环境与在工厂安装时有很多安装辅助工具不同。在使用现场安装时,往往辅助工具匮乏,因此摩擦片的安装便易性对于用户来说极其重要。目前市场上的摩擦材料有编织型刹车带、挤出式刹车带、压制型摩擦片、层压式摩擦片、纸基摩擦片、粉末冶金摩擦片、碳碳复合材料、碳陶复合材料等类型。对于载荷大、压强大和使用较频繁的应用场合,一般选用压制型和层压式摩擦片;对于要求摩擦片强度较大的应用场合,一般采用纤维线或网格布浸胶后放在热压模具中热压成型。针对这种纤维线浸胶后热压成型的摩擦材料,为了改善摩擦性能,不得不添加一些较硬的材料组分,导致产品硬度过大,不易钻孔,在使用中容易划伤对偶面;而网格布浸胶热压成型的摩擦材料,厂家为了降低硬度,采用橡胶作为粘接剂,此种材料在使用中容易打滑,温度升高冒白烟,散发难闻的气味,并且层压材料有时会发生分层现象。现有技术cn103342985b公开了一种摩擦材料及其制备方法,其采用粘合剂、增强纤维和摩擦性能调节剂组成,该材料通过编织网格布,浸渍粘合剂、烘烤、叠好后加压硫化制备得到。其具有固化程度更高,摩擦系数更稳定的优点。然而,该摩擦材料仍具有产品硬度过大,不易钻孔的缺点。因此,针对现有的纤维线或网格布浸胶热压成型的摩擦材料,其具有硬度太大、不易钻孔、划伤对偶面、冒白烟、散发难闻气味和材料分层等问题,需要提供一种新的摩擦材料。鉴于此,特提出本发明。技术实现要素:本发明的目的在于提供一种整体编织型摩擦材料的制备方法。为实现上述目的,本发明的技术方案如下:本发明涉及一种整体编织型摩擦材料的制备方法,包括以下步骤:1)制备合股线:将金属纤维、无机纤维和/或有机纤维进行合股,制成合股线;优选地,所述金属纤维选自铜丝、锌丝、银丝中的至少一种;所述无机纤维为玻璃纤维和/或玄武岩纤维;所述有机纤维选自涤纶、腈纶、锦纶、丙纶、芳纶纤维、棉线中的至少一种。优选地,所述合股线含有金属纤维、无机纤维和有机纤维。优选地,按重量份数计,所述合股线中含有2~30份的金属纤维,20~60份的无机纤维,5~40份的有机纤维。2)制备编织布:采用整体编织法,将步骤1)制备得到的合股线制成编织布;优选地,所述编织布密度为1.0~1.3g/cm3;所述编织布采用半交叉整体编织法或全交叉整体编织法制备得到。3)浸渍树脂:将步骤2)制备得到的编织布浸入树脂中,捞出待树脂自然滴干后,烘干得到坯体;优选地,所述树脂为液态酚醛树脂或液态改性酚醛树脂,浸渍时间为30~100分钟,烘干温度为60~160℃,烘干时间为30~100分钟。4)热压固化:按照摩擦片尺寸,将步骤3)制备得到的坯体裁成所需形状后,将裁好的坯体置于热压机模具中进行热压固化,得到半成品;优选地,所述热压固化的温度为100~200℃,压力为10~30mpa,时间为30~120分钟。5)热处理:将步骤4)制备得到的半成品置于烘箱中进行热处理,使摩擦片树脂完全固化;优选地,所述热处理温度为100~200℃,时间为0.5~24h。6)机加工:对步骤5)热处理后得到的半成品进行机加工,得到成品。优选地,所述机加工包括对半成品表面进行车削、磨削等加工,进一步包括车削内外锥形弧面、磨削内外锥形弧面、钻安装孔等步骤。本发明的有益效果:现有的摩擦材料采用纤维线或单层纤维布浸胶后经热压而成,其硬度过大,不易钻孔影响安装,易划伤对偶面,并且层压材料易分层,传动力矩衰退严重造成打滑,严重影响冲孔桩机等设备的正常使用。针对上述问题,本发明提供了一种整体编织型热压摩擦材料的制备方法。该方法将金属纤维、无机纤维和/或有机纤维制成合股线,通过多层整体编织法将其编织成布,浸渍树脂后干燥得到坯体,坯体裁剪后置于热压模具内,热压固化得到半成品,再经热处理、机加工等工序得到成品。由于该摩擦材料以整体编织布为骨架,其纤维含量高,树脂含量低。成品强度大、硬度低,并具有一定的柔韧性,解决了现有摩擦材料存在的问题。附图说明图1为本发明半交叉整体编织法得到编织布的结构示意图;其中,1-1为经线;1-2为纬线;1-3为混合线。图2为本发明全交叉整体编织法得到编织布的结构示意图;其中,2-1为经线;2-2为纬线。图3为现有的冲孔桩机离合片结构示意图;其中,3-1为纤维线;3-2为纤维线断面。图4为另一现有的冲孔桩机离合片结构示意图;其中,4-1为纤维布;4-2为纤维布层。具体实施方式为使本发明的目的、技术方案和优点更加清楚,下面将对本发明的技术方案进行详细的描述。显然,所描述的实施例仅仅是本发明一部分实施例,而不是全部的实施例。基于本发明中的实施例,本领域普通技术人员在没有做出创造性劳动的前提下所得到的所有其它实施方式,都属于本发明所保护的范围。本发明实施例涉及一种整体编织型摩擦材料的制备方法,包括以下步骤:1)制备合股线:将金属纤维、无机纤维和/或有机纤维进行合股,制成合股线;在本发明的一个实施例中,所述金属纤维选自铜丝、锌丝、银丝中的至少一种;所述无机纤维为玻璃纤维和/或玄武岩纤维;所述有机纤维选自涤纶、腈纶、锦纶、丙纶、芳纶纤维、棉线中的至少一种。上述纤维中,金属纤维具有良好的导热性,同时具有一定硬度作为支撑材料,要求金属的硬度不能过大,否则无法与其它纤维合股。无机纤维具有良好的耐热性能、机械性能和耐磨性能。芳纶等高分子有机纤维相对质轻,比表面积大,耐磨损,与树脂的相容性好。相比之下棉线虽然不耐磨,但是其低温静摩擦系数大,与树脂相容性好,并且在合股线中存在金属纤维作为支撑,少量的棉线对材料整体的耐磨性影响不大。在本发明的一个实施例中,所述合股线含有金属纤维、无机纤维和有机纤维。优选按重量份数计,所述合股线中含有2~30份的金属纤维,20~60份的无机纤维,5~40份的有机纤维。优选金属纤维、无机纤维和有机纤维的质量比为1:(2~5):(2~5)。通常合股线中金属纤维的用量低于单一的无机纤维和有机纤维,原因是金属价格较高,且金属过多摩擦材料在使用时容易产生噪音。2)制备编织布:采用整体编织法,将步骤1)制备得到的合股线制成编织布;在本发明的一个实施例中,所述编织布密度为1.0~1.3g/cm3;所述编织布采用半交叉整体编织法或全交叉整体编织法制备得到。其中,半交叉整体编织法得到的编织布结构如图1所示。半交叉整体编织法采用的编织线包括经线1-1、纬线1-2和混合线1-3。混合线1-3从编织布的上表面穿到下表面,起到捆扎的作用,将编织布的各层捆扎在一起。同时混合线1-3由上表面垂直穿到下表面,导热距离短,利于混合线1-3的铜丝或其它导热线把摩擦面的热量导到非摩擦面,并均匀扩散于钢背上,有利于摩擦材料性能的稳定。全交叉整体编织法得到的编织布结构如图2所示。全交叉整体编织法采用的编织线仅有经线2-1和纬线2-2,与半交叉整体编织法相比没有混合线1-3。经线2-1从编织布的上表面斜穿到下表面,导热距离长,与半交叉整体编织法相比散热稍差。但是层间结合更紧密,使用过程中不易分层。3)浸渍树脂:将步骤2)制备得到的编织布浸入树脂中,捞出待树脂自然滴干后,烘干得到坯体;在本发明的一个实施例中,所述树脂为液态酚醛树脂或液态改性酚醛树脂,浸渍时间为30~100分钟,烘干温度为60~160℃,烘干时间为30~100分钟。4)热压固化:按照摩擦片尺寸,将步骤3)制备得到的坯体裁成所需形状后,将裁好的坯体置于热压机模具中进行热压固化,得到半成品;在本发明的一个实施例中,所述热压固化的温度为100~200℃,压力为10~30mpa,时间为30~120分钟。5)热处理:将步骤4)制备得到的半成品置于烘箱中进行热处理,使摩擦片树脂完全固化;需要说明,如果步骤4)在模具中完全固化需要的时间比较长,生产效率低。一般是在模具中进行初步固化,产品取出后放入烘箱进一步热处理,使其完全固化。在本发明的一个实施例中,所述热处理温度为100~200℃,时间为0.5~24h。6)机加工:对步骤5)热处理后得到的半成品进行机加工,得到成品。在本发明的一个实施例中,所述机加工包括对半成品表面进行车削、磨削等加工,进一步包括车削内外锥形弧面、磨削内外锥形弧面、钻安装孔等步骤。实施例1一种整体编织型摩擦材料,其制备方法包括以下步骤:1)制备合股线:将20份铜丝、50份玻璃纤维和30份棉线进行合股,制成合股线;2)制备编织布:采用编织机及半交叉整体编织法,将步骤1)制备得到的合股线制成编织布,密度为1.2g/cm3;3)浸渍树脂:将步骤2)制备得到的编织布浸入液态酚醛树脂中,浸渍时间为60分钟,捞出待树脂自然滴干后,置于烘箱中在120℃烘干50分钟得到坯体;4)热压固化:按照离合片尺寸,将步骤3)制备得到的坯体裁成所需形状后,置于热压机模具中进行热压固化,热压固化的温度为130℃,压力为13mpa,时间为60分钟,得到半成品;5)热处理:将步骤4)制备得到的半成品置于烘箱中进行热处理,热处理温度为150℃,时间为12h,使离合片树脂完全固化;6)机加工:对步骤5)热处理后得到半成品的内外弧表面进行机磨削加工,得到成品。改变实施例1中的实验参数,得到实施例2~6和对比例1~3。除表中参数以外,其它实验过程均与实施例相同,具体设置见表1。其中,对比例2中的摩擦材料通过将纤维线浸树脂后烘干,再放入模具热压成型制备得到,其结构示意图如图3所示,其中纤维线3-1在摩擦材料中分布散乱,从摩擦材料的截面中可见纤维线断面3-2。对比例3中的摩擦材料先用经线和纬线制备二维纤维布4-1,再将多层纤维布4-1粘接得到纤维布层4-2,其结构示意图如图4所示。表1实施例/对比例改变的实验参数实施例1步骤1)中,合股线中含有20份铜丝、50份玻璃纤维和30份棉线实施例2步骤1)中,合股线中含有2份铜丝、20份玻璃纤维和5份棉线实施例3步骤1)中,合股线中含有10份铜丝、10份芳纶纤维和10份棉线实施例4步骤1)中,合股线中含有2份铜丝和5份玻璃纤维实施例5步骤1)中,合股线中含有2份铜丝和5份棉线实施例6步骤2)中,采用全交叉整体编织法得到编织布对比例1未进行步骤5)的热处理对比例2将纤维线浸树脂后烘干,再放入模具热压成型制备得到的摩擦材料对比例3采用cn103342985b具体实施方式中方法制备的摩擦材料测试例将实施例和对比例按照国家标准要求机加工成拉伸样条(gb/t1040.4-2006)、压缩样块(gb/t1041-2008)剪切样块(gb/t26739-2011)、摩擦性能测试样块(gb/t11834-2011)。其中压缩样块长度为10mm±0.1mm,宽度为10mm±0.1mm,厚度为10mm±0.2mm。剪切样块的长度为20±0.1mm,宽度为20±0.1mm,厚度为10±0.1mm。摩擦性能测试样块为边长为25mm±0.1的正方形样块,厚度为6-8mm。按国标标准对上述样件进行力学性能测试和摩擦性能测试,测试结果见表2。表2从表2数据可知,实施例1~6的硬度相差不大,说明采用不同的合股线材料对摩擦材料的硬度影响较小。其中实施例1~3的硬度略低于实施例4和5,说明合股线中的金属含量对硬度有一定影响,同时含有金属纤维、有机纤维和无机纤维的摩擦材料具有较好的机械性能和较低的硬度。实施例4不含有机纤维,其硬度较高,其原因是金属和玻纤均具有较高的硬度。实施例5不含无机纤维,硬度较低,但摩擦系数较低,其原因是棉线的耐温性较差,摩擦系数高温衰减严重。实施例6与实施例1相比,机械性能相近,仅摩擦系数略低于实施例1,说明编织方法对摩擦材料耐温性能有一定的影响。实施例6的摩擦材料采用全交叉整体编织法,上下两面的导热距离与实施例1采用半交叉整体编织法得到的摩擦材料相比变长,散热变差,摩擦系数略有降低。对比例1的摩擦系数较低,说明后期的热处理对于摩擦材料的摩擦性能影响较大,原因是树脂未完全固化,有些化学反应未完全进行,在使用过程中摩擦生热引起未反应完全的化学反应继续进行,造成摩擦材料摩擦系数降低。对比例2通过纤维线浸入树脂烘干后放入模具热压而成,由于纤维线浸树脂后热压过于致密,硬度偏高。再加上目前市面上的纤维线使用高比例的无机纤维,而仅加入极少量的金属纤维或有机纤维,造成目前市面上的纤维线摩擦材料硬度极高,安装钻孔极其困难。且无机纤维和树脂含量比例高导致散热性差,树脂高温碳化造成摩擦系数低。对比例3通过cn103342985b具体实施方式中方法制备,其为单层布浸入树脂后叠层热压,与纤维线浸树脂后热压类似,材料过度致密,导致硬度偏高,安装钻孔困难,并且由于树脂含量偏高,摩擦系数偏低。以上所述,仅为本发明的具体实施方式,但本发明的保护范围并不局限于此,任何熟悉本
技术领域:
的技术人员在本发明揭露的技术范围内,可轻易想到变化或替换,都应涵盖在本发明的保护范围之内。因此,本发明的保护范围应以所述权利要求的保护范围为准。当前第1页1 2 3 
起点商标作为专业知识产权交易平台,可以帮助大家解决很多问题,如果大家想要了解更多知产交易信息请点击 【在线咨询】或添加微信 【19522093243】与客服一对一沟通,为大家解决相关问题。
此文章来源于网络,如有侵权,请联系删除



tips