一种厚板聚氨酯底漆及其制备方法与流程



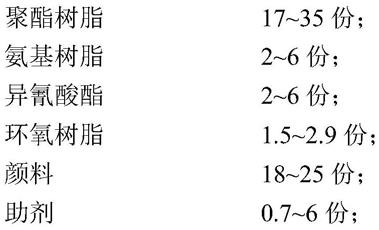
一种厚板聚氨酯底漆及其制备方法
[0001]
本申请是申请日2016年1月29日,申请号201610068468.3,发明名称为“一种厚板聚氨酯底漆及其制备方法”的分案申请。
技术领域
[0002]
本发明涉及涂料技术领域,尤其涉及一种厚板聚氨酯底漆及其制备方法。
背景技术:
[0003]
近年来,我国预涂卷材应用的领域不断扩大,由以往的建筑领域(如外墙、室内装潢等)扩大到家电行业(如冰箱、微波炉等)、甚至交通运输领域。预涂卷材已涂装好,可直接进行各种加工成型工艺,因此,要求其具有高强度和良好的机械加工性能。另外,预涂卷材应用到建筑、家电、交通运输领域时,应用条件比较苛刻,因此,需要具备良好的抗腐蚀性能和物理屏蔽性能。
[0004]
对于预涂卷材的复合涂层而言,底漆是基础,在很大程度上影响整体涂层的性能,对底材的附着力、防腐性能、t弯及杯突等机械性能都有影响。传统底漆一般应用于薄板,如环氧底漆和聚酯-氨基底漆(简称聚酯底漆)。环氧底漆对基板的附着力良好,耐化学腐蚀性能佳,但其柔韧性较差。聚酯底漆与底材的附着力好,柔韧性优,但对潮湿环境较敏感,耐化学腐蚀性不及环氧底漆。若基材较厚,加工过程中尤其弯曲过程中所产生的内应力较薄板强,表面积变化大,为防止弯曲处涂料的脱落,对涂料的柔韧性及对基板附着力提出了更为严苛的要求。
[0005]
有鉴于此,有必要提供一种具有更好t弯、附着力效果的聚酯底漆,以满足预涂卷材生产与发展的需求。
技术实现要素:
[0006]
为了克服现有技术中底漆性能差的缺陷,本发明的目的是提供一种厚板聚氨酯底漆,该底漆t弯能达到0t无裂纹、附着力优、耐盐雾1000小时无异常的技术效果。
[0007]
本发明的另一个目的是提供一种上述厚板聚氨酯底漆的制备方法。
[0008]
为了实现上述目的,本发明的一个方面采用的技术方案如下:
[0009]
一种厚板聚氨酯底漆,包括以下重量份的组分:
[0010][0011][0012]
所述厚板聚氨酯底漆的聚酯氨基比为2~5,聚酯异氰酸酯比为3~6,环氧树脂比
为0.08~0.12,颜基比为1.0~1.8。
[0013]
所述聚酯树脂的分子量为10000~60000,羟值为4~8mgkoh/g,酸值为0~13mgkoh/g;例如:韩国sk集团的skybon es 420等。
[0014]
所述氨基树脂是完全甲醚化三聚氰胺树脂或者是完全甲醚化三聚氰胺树脂和部分甲醚化氨基树脂的混合物或者是完全甲醚化三聚氰胺树脂和高亚氨基甲醚化三聚氰胺树脂的混合物;所述氨基树脂的固体份≥80%;例如:氰特树脂cymel 303、首诺公司的717、上海元邦化工的氨基树脂yp5603。
[0015]
所述异氰酸酯为封闭型异氰酸酯,例如德国拜尔公司的desmodur 3175sn、desmodur rl1265、desmodur bl3272。
[0016]
所述环氧树脂可选用江苏鸿业公司的hg树脂、荷兰壳牌的epikote 828el。
[0017]
所述颜料为体质颜料或着色颜料,优选为硫酸钡、钛白粉、煅烧高岭土、锶铬黄等中的至少一种。
[0018]
所述助剂是包括以下重量份的组分:
[0019]
酸催化剂
ꢀꢀꢀꢀꢀꢀꢀꢀꢀꢀꢀ
0.2~0.5份;
[0020]
有机锡类催化剂
ꢀꢀꢀꢀꢀ
0.5~2份。
[0021]
所述酸催化剂为对甲苯磺酸及其封闭型酸、二壬基萘磺酸及其封闭型酸中的至少一种;例如,金氏公司的nacure 1051、德国毕克化学公司的byk-450、南京盛大化工的酸催化剂catalyst 6000等。
[0022]
所述有机锡类催化剂为封闭型聚氨酯催化剂;优选为性价比较高的二月桂酸二丁基锡;例如,上海德音化学公司生产的dy-12、上海雨田化工生产的dbtl等。
[0023]
所述助剂还包括以下重量份的组分:
[0024]
防沉剂
ꢀꢀꢀꢀꢀꢀꢀꢀꢀꢀꢀꢀꢀ
0.1~1份;
[0025]
附着力促进剂
ꢀꢀꢀꢀꢀꢀꢀ
0.5~1份;
[0026]
流平消泡剂
ꢀꢀꢀꢀꢀꢀꢀꢀꢀ
0.5~1.5份。
[0027]
所述防沉剂为气相二氧化硅或膨润土中的至少一种,例如金昊纳米材料公司的xhf、cab-o-sil m-5。
[0028]
所述附着力促进剂为上海维海贸易有限公司的tz-8805或宜兴方铭化工生产的pae 206。
[0029]
所述流平消泡剂为丙烯酸类消泡剂或氟改性丙烯酸消泡剂;例如立邦涂料(中国)有限公司的leveler s(ex);巴斯夫(中国)有限公司(basf)的efka 3600。
[0030]
所述助剂还进一步包括0.1~1份的分散剂。
[0031]
所述分散剂为受控絮凝型润湿分散剂;例如德国毕克化学公司的byk-p104、at-204、r-5310 resin。
[0032]
所述溶剂为s-100#芳烃溶剂或三甲苯溶剂、s-150#芳烃溶剂或均四甲苯溶剂、环己酮、异氟尔酮、异丁醇、尼龙酸甲酯(dbe)、乙二醇丁醚中的至少一种。
[0033]
本发明的另一个方面提供了一种上述厚板聚氨酯底漆的制备方法,包括以下步骤:
[0034]
(1)将聚酯树脂13~25份、颜料18~25份混合,加入溶剂4~10份,研磨得到浆料;
[0035]
(2)在浆料中加入聚酯树脂4~10份、异氰酸酯2~6份、有机锡类催化剂0.5~2份
混合;然后再加入氨基树脂2~6份、酸催化剂0.2~0.5份、环氧树脂1.5~2.9份、溶剂4~10份,混合后过滤得到所述厚板聚氨酯底漆;
[0036]
或者:
[0037]
(1)将聚酯树脂13~25份、颜料18~25份、防沉剂0.1~1份混合,加入溶剂4~10份,研磨得到浆料;
[0038]
(2)在浆料中加入聚酯树脂4~10份、异氰酸酯2~6份、有机锡类催化剂0.5~2份混合;然后再加入氨基树脂2~6份、酸催化剂0.2~0.5份、环氧树脂1.5~2.9份、流平消泡剂0.5~1.5份、附着力促进剂0.5~1.0份、溶剂4~10份,混合后过滤得到所述厚板聚氨酯底漆;
[0039]
或者:
[0040]
(1)将聚酯树脂13~25份、颜料18~25份、防沉剂0.1~1份、分散剂0.1~1份混合,加入溶剂4~10份,研磨得到浆料;
[0041]
(2)在浆料中加入聚酯树脂4~10份、异氰酸酯2~6份、有机锡类催化剂0.5~2份混合;然后再加入氨基树脂2~6份、酸催化剂0.2~0.5份、环氧树脂1.5~2.9份、流平消泡剂0.5~1.5份、附着力促进剂0.5~1.0份、溶剂4~10份,混合后过滤得到所述厚板聚氨酯底漆。
[0042]
所述厚板聚氨酯底漆的最低成膜温度为200℃。
[0043]
所述研磨的细度不大于15μm。
[0044]
所述过滤是使用80μm的滤袋过滤。
[0045]
所述厚板聚氨酯底漆的粘度为120~140s/涂-4#杯在20℃条件下测定,或调节至500-600mpa.s。
[0046]
由于采用上述技术方案,本发明具有以下优点和有益效果:
[0047]
本发明提供的厚板聚氨酯底漆t弯能达到0t无裂纹,柔韧性好,避免在加工过程中出现掉漆现象;耐盐雾性能高,配合一般性能的聚酯面漆,盐雾实验1000小时达到1级;基板附着力与面漆附着力均优于传统的环氧底漆和聚酯底漆。本发明提供的厚板聚氨酯底漆相比传统的底漆,兼备更优的附着力、柔韧性及耐化学腐蚀性。
具体实施方式
[0048]
为了更清楚地说明本发明,下面结合优选实施例对本发明做进一步的说明。本领域技术人员应当理解,下面所具体描述的内容是说明性的而非限制性的,不应以此限制本发明的保护范围。
[0049]
本发明中使用助剂有助于加速原材料反应并维持涂料稳定,酸催化剂能够促进氨基树脂交联,一般为强酸。使用封闭型酸时,涂料的储存稳定性更好。
[0050]
本发明中的术语:
[0051]
本发明中聚酯氨基比指聚酯树脂的固体份与氨基树脂的固体份的重量比。
[0052]
聚酯异氰酸酯比指聚酯树脂的固体份与异氰酸酯的固体份的重量比。
[0053]
环氧树脂比指环氧树脂的固体份与基料(基料包括聚酯树脂、氨基树脂、环氧树脂、异氰酸酯)的固体份的重量比。
[0054]
颜基比指颜料(包括体质颜料)与基料(基料包括聚酯树脂、氨基树脂、环氧树脂和
异氰酸酯)固体份的重量比。
[0055]
实施例1
[0056]
一种厚板聚氨酯底漆的制备方法,包括以下步骤:
[0057]
1)将聚酯树脂skybon es 420 20份、颜料钛白粉r-996 20份、硫酸钡precipitated barium sulfate 5份、防沉剂cab-o-sil m-5 0.2份混合,加入溶剂s-100#芳烃溶剂3份、异氟尔酮5份,研磨至细度不大于15μm,得到浆料;所述聚酯树脂为大分子量饱和聚酯树脂,分子量16000,羟值4~8mgkoh/g,酸值0~13mgkoh/g。采用高分子量的线性或部分支链聚酯树脂,能保证涂料高的柔韧性、加工性和附着力。聚酯树脂的羟基值过高,则反应基团不能完全反应,影响成膜后的耐水性;羟基值过低,则反应基团不够,影响成膜后的加工性,聚酯树脂可通过市售购买得到。先加入聚酯树脂和防沉剂,再投颜料,此时体系的粘度较高,聚酯树脂能充分润湿颜料,发挥分散效果。
[0058]
2)在浆料中加入聚酯树脂skybon es 420 10份、异氰酸酯desmodur 3175sn 4份、有机锡类催化剂dbtl 1份混合;加入氨基树脂yp5603 6份,加入酸催化剂catalyst 6000 0.4份、环氧树脂epikote 828el 2份、流平消泡剂efka 3600 1份、附着力促进剂tz-8805 0.8份,加入溶剂s-100#芳烃溶剂2份、异氟尔酮3份、环己酮1份、异丁醇1份,混合后过滤得到所述厚板聚氨酯底漆,过滤是使用80μm的滤袋过滤。厚板聚氨酯底漆的最低成膜温度为200℃,粘度为120~140s/涂-4#杯在20℃条件下测定,或调节至500-600mpa.s。
[0059]
本实施例中的氨基树脂为完全甲醚化三聚氰胺树脂,能提供更快的反应速度和固化硬度,在其他实施方式中可以根据工艺需要或者根据用户的要求来选定最终使用的氨基树脂。
[0060]
本实施例中的异氰酸酯为封闭型异氰酸酯,能保证单组份面漆涂料的经时稳定性及耐酸性、耐盐雾性。本实施例中的环氧树脂为改性环氧树脂,适量加入能提高漆膜的附着力及耐盐雾性能。由于助剂与基料(聚酯树脂、氨基树脂、异氰酸酯、环氧树脂)相容性不会太好,在基料较少情况下加入,可能会浑浊,析出晶体,影响面漆效果。因此,本实施例中,将基料先加入,再加入其它助剂时得到涂料更稳定。
[0061]
本实施例中的聚酯树脂固体份为48%,氨基树脂固体份为97%,异氰酸酯固体份为75%,环氧树脂固体份为99%;聚酯氨基比为2.5,聚酯异氰酸酯比为4.8,环氧树脂比为0.08,颜基比为1.0。
[0062]
本实施例制备得到的所述厚板聚氨酯底漆在金属板温224
±
5℃下固化,基板厚度2.5mm,底漆干涂膜厚10μm,配以性能一般的聚酯面漆,干涂膜厚15μm下的性能请参阅下文的表1所示。
[0063]
实施例2
[0064]
一种厚板聚氨酯底漆的制备方法,包括以下步骤:
[0065]
1)将聚酯树脂skybon es 420 17份、颜料钛白粉r-996 19份、硫酸钡precipitated barium sulfate 5份、防沉剂cab-o-sil m-5 0.2份、溶剂s-100#芳烃溶剂2份、异氟尔酮4份,混合,研磨至细度不大于15μm,得到浆料;所述聚酯树脂分子量16000,羟值4~8mgkoh/g,酸值0~13mgkoh/g。
[0066]
2)在浆料中加入聚酯树脂skybon es 420 8份、异氰酸酯desmodur 3175sn 4份、有机锡类催化剂dbtl 1份混合;加入氨基树脂yp5603 6份、酸催化剂catalyst 6000 0.4
份、环氧树脂epikote 828el 2.9份、流平消泡剂efka 3600 1份、附着力促进剂tz-8805 0.8份,加入溶剂s-100#芳烃溶剂2份、异氟尔酮3份、环己酮1份、异丁醇1份,混合后过滤得到所述厚板聚氨酯底漆;过滤是使用80μm的滤袋过滤,厚板聚氨酯底漆的最低成膜温度为200℃,粘度为120~140s/涂-4#杯在20℃条件下测定,或调节至500-600mpa.s。
[0067]
本实施例中的聚酯树脂固体份为48%,氨基树脂固体份为97%,异氰酸酯固体份为75%,环氧树脂固体份为99%;聚酯氨基比为2.1,聚酯异氰酸酯比为4.0,环氧树脂比为0.12,颜基比为1.0。
[0068]
本实施例制备得到的所述厚板聚氨酯底漆在金属板温224
±
5℃下固化,基板厚度2.5mm,底漆干涂膜厚10μm,配以性能一般的聚酯面漆,干涂膜厚15μm下的性能请参阅下文的表1所示。
[0069]
实施例3
[0070]
一种厚板聚氨酯底漆的制备方法,包括以下步骤:
[0071]
1)将聚酯树脂skybon es 420 14份、颜料钛白粉r-996 14份、硫酸钡precipitated barium sulfate 5份、防沉剂cab-o-sil m-5 0.2份、溶剂s-100#芳烃溶剂3份、异氟尔酮5份,混合,研磨至细度不大于15μm,得到浆料;所述聚酯树脂分子量16000,羟值4~8mgkoh/g,酸值0~13mgkoh/g。
[0072]
2)在浆料中加入聚酯树脂skybon es 420 4份、异氰酸酯desmodur 3175sn 3份,有机锡类催化剂dbtl 1份,混合;加入氨基树脂yp5603 2份、酸催化剂catalyst 6000 0.4份、环氧树脂epikote 828el1.6份、流平消泡剂efka 3600 1份、附着力促进剂tz-8805 0.8份,加入溶剂s-100#芳烃溶剂2份、异氟尔酮3份、环己酮1份、异丁醇1份,混合后过滤得到所述厚板聚氨酯底漆;过滤是使用80μm的滤袋过滤,厚板聚氨酯底漆的最低成膜温度为200℃,粘度为120~140s/涂-4#杯在20℃条件下测定,或调节至500-600mpa.s。
[0073]
本实施例中的聚酯树脂固体份为48%,氨基树脂固体份为97%,异氰酸酯固体份为75%,环氧树脂固体份为99%;聚酯氨基比为4.4,聚酯异氰酸酯比为3.8,环氧树脂比为0.11,颜基比为1.3。
[0074]
本实施例制备得到的所述厚板聚氨酯底漆在金属板温224
±
5℃下固化,基板厚度2.5mm,底漆干涂膜厚10μm,配以性能一般的聚酯面漆,干涂膜厚15μm下的性能请参阅下文的表1所示。
[0075]
实施例4
[0076]
一种厚板聚氨酯底漆的制备方法,包括以下步骤:
[0077]
1)将聚酯树脂skybon es 420 14份、颜料钛白粉r-996 18份、硫酸钡precipitated barium sulfate 5份、防沉剂cab-o-sil m-5 0.2份、溶剂s-100#芳烃溶剂2份、异氟尔酮4份,混合,研磨至细度不大于15μm,得到浆料;所述聚酯树脂分子量16000,羟值4~8mgkoh/g,酸值0~13mgkoh/g。
[0078]
2)在浆料中加入聚酯树脂skybon es 420 4份、异氰酸酯desmodur 3175sn 4份、有机锡类催化剂dbtl 1份混合;加入氨基树脂yp5603 3份、酸催化剂catalyst 6000 0.4份、环氧树脂epikote 828el 1.5份、流平消泡剂efka 3600 1份、附着力促进剂tz-8805 0.8份,加入溶剂s-100#芳烃溶剂2份、异氟尔酮3份、环己酮1份、异丁醇1份,混合后过滤得到所述厚板聚氨酯底漆;过滤是使用80μm的滤袋过滤,厚板聚氨酯底漆的最低成膜温度为
200℃,粘度为120~140s/涂-4#杯在20℃条件下测定,或调节至500-600mpa.s。
[0079]
本实施例中的聚酯树脂固体份为48%,氨基树脂固体份为97%,异氰酸酯固体份为75%,环氧树脂固体份为99%;聚酯氨基比为2.8,聚酯异氰酸酯比为5.4,环氧树脂比为0.11,颜基比为1.6。
[0080]
本实施例制备得到的所述厚板聚氨酯底漆在金属板温224
±
5℃下固化,基板厚度2.5mm,底漆干涂膜厚10μm,配以性能一般的聚酯面漆,干涂膜厚15μm下的性能请参阅下文中的表1所示。
[0081]
实施例5
[0082]
一种厚板聚氨酯底漆的制备方法,包括以下步骤:
[0083]
1)将聚酯树脂skybon es 420 16份、颜料钛白粉r-996 20份、硫酸钡precipitated barium sulfate 5份、防沉剂cab-o-sil m-5 0.2份、溶剂s-100#芳烃溶剂2份、异氟尔酮4份,混合,研磨至细度不大于15μm,得到浆料;所述聚酯树脂分子量16000,羟值4~8mgkoh/g,酸值0~13mgkoh/g。
[0084]
2)在浆料中加入聚酯树脂skybon es 420 5份、异氰酸酯desmodur 3175sn 3份、有机锡类催化剂dbtl 1份混合;加入氨基树脂yp5603 3份、酸催化剂catalyst 6000 0.4份、环氧树脂epikote 828el 2份、流平消泡剂efka 3600 1份、附着力促进剂tz-8805 0.8份,加入溶剂s-100#芳烃溶剂2份、异氟尔酮3份、环己酮1份、异丁醇1份,混合后过滤得到所述厚板聚氨酯底漆;过滤是使用80μm的滤袋过滤,厚板聚氨酯底漆的最低成膜温度为200℃,粘度为120~140s/涂-4#杯在20℃条件下测定,或调节至500-600mpa.s。
[0085]
本实施例中的聚酯树脂固体份为48%,氨基树脂固体份为97%,异氰酸酯固体份为75%,环氧树脂固体份为99%;聚酯氨基比为3.5,聚酯异氰酸酯比为5.4,环氧树脂比为0.11,颜基比为1.5。
[0086]
本实施例制备得到的所述厚板聚氨酯底漆在金属板温224
±
5℃下固化,基板厚度2.5mm,底漆干涂膜厚10μm,配以性能一般的聚酯面漆,干涂膜厚15μm下的性能请参阅下文中的表2所示。
[0087]
实施例6
[0088]
一种厚板聚氨酯底漆的制备方法,包括以下步骤:
[0089]
1)将聚酯树脂skybon es 420 25份、颜料钛白粉r-996 20份、硫酸钡precipitated barium sulfate 5份、防沉剂cab-o-sil m-5 0.2份、溶剂s-100#芳烃溶剂2份、异氟尔酮4份,混合,研磨至细度不大于15μm,得到浆料;所述聚酯树脂分子量16000,羟值4~8mgkoh/g,酸值0~13mgkoh/g。
[0090]
2)在浆料中加入聚酯树脂skybon es 420 8份、异氰酸酯desmodur 3175sn 6份、有机锡类催化剂dbtl 1份混合;加入氨基树脂yp5603 3份、酸催化剂catalyst 6000 0.4份、环氧树脂epikote 828el 2份、流平消泡剂efka 3600 1份、附着力促进剂tz-8805 0.8份,加入溶剂s-100#芳烃溶剂2份、异氟尔酮3份、环己酮1份、异丁醇1份,混合后过滤得到所述厚板聚氨酯底漆;过滤是使用80μm的滤袋过滤,厚板聚氨酯底漆的最低成膜温度为200℃,粘度为120~140s/涂-4#杯在20℃条件下测定,或调节至500-600mpa.s。
[0091]
本实施例中的聚酯树脂固体份为48%,氨基树脂固体份为97%,异氰酸酯固体份为75%,环氧树脂固体份为99%;聚酯氨基比为5.4,聚酯异氰酸酯比为3.5,环氧树脂比为
0.08,颜基比为1.0。
[0092]
本实施例制备得到的所述厚板聚氨酯底漆在金属板温224
±
5℃下固化,基板厚度2.5mm,底漆干涂膜厚10μm,配以性能一般的聚酯面漆,干涂膜厚15μm下的性能请参阅下文中的表2所示。
[0093]
实施例7
[0094]
一种厚板聚氨酯底漆的制备方法,包括以下步骤:
[0095]
1)将聚酯树脂skybon es 420 13份、颜料钛白粉r-996 14份、硫酸钡precipitated barium sulfate 4份、防沉剂cab-o-sil m-5 0.2份、溶剂s-100#芳烃溶剂2份、异氟尔酮4份,混合,研磨至细度不大于15μm,得到浆料;所述聚酯树脂分子量16000,羟值4~8mgkoh/g,酸值0~13mgkoh/g。
[0096]
2)在浆料中加入聚酯树脂skybon es 420 5份、异氰酸酯desmodur 3175sn 3.5份、有机锡类催化剂dbtl 1份混合;加入氨基树脂yp5603 3份、酸催化剂catalyst 6000 0.4份、环氧树脂epikote 828el 2份、流平消泡剂efka 3600 1份、附着力促进剂tz-8805 0.8份,加入溶剂s-100#芳烃溶剂2份、异氟尔酮3份、环己酮1份、异丁醇1份,混合后过滤得到所述厚板聚氨酯底漆;过滤是使用80μm的滤袋过滤,厚板聚氨酯底漆的最低成膜温度为200℃,粘度为120~140s/涂-4#杯在20℃条件下测定,或调节至500-600mpa.s。
[0097]
本实施例中的聚酯树脂固体份为48%,氨基树脂固体份为97%,异氰酸酯固体份为75%,环氧树脂固体份为99%;聚酯氨基比为3.0,聚酯异氰酸酯比为3.3,环氧树脂比为0.12,颜基比为1.1。
[0098]
本实施例制备得到的所述厚板聚氨酯底漆在金属板温224
±
5℃下固化,基板厚度2.5mm,底漆干涂膜厚10μm,配以性能一般的聚酯面漆,干涂膜厚15μm下的性能请参阅下文中的表2所示。
[0099]
表1
[0100][0101]
表2
[0102][0103]
从表1和表2的数据可以看出:
[0104]
1、实施例1-7所得所述厚板聚氨酯底漆的性能均为合格,但存在差异。
[0105]
2、实施例1-7所得所述厚板聚氨酯底漆的性能差异在于:实施例3、4、5的t弯优于其他,可达到0t无裂纹,实施例3、4、5的共同点为环氧树脂比为0.11。
[0106]
据此测定,决定所述厚板聚氨酯底漆t弯的一个关键因素是“环氧树脂比”,且最优比值为0.11。以下实施例选择不同环氧树脂比进行进一步阐明。
[0107]
实施例8
[0108]
同实施例5,区别在于环氧树脂epikote 828el为1.7份,计算得环氧树脂比为0.1,所得性能请参阅表3所示。
[0109]
实施例9
[0110]
同实施例5,区别在于环氧树脂epikote 828el为1.6份,计算得环氧树脂比为0.09,所得性能请参阅表3所示。
[0111]
实施例10
[0112]
同实施例5,区别在于环氧树脂epikote 828el为2.2份,计算得环氧树脂比为0.12,所得性能请参阅表3所示。
[0113]
表3
[0114][0115]
从表3的数据可以看出,只有实施例5的t弯最优,达到0t,其余均有下降,因此,性
能最佳的“环氧树脂比”为0.11,偏离该比值时t弯均有下降。
[0116]
实施例11
[0117]
同实施例1,区别在于:氨基树脂是完全甲醚化三聚氰胺树脂和高亚氨基甲醚化三聚氰胺树脂的混合物(体积比为1:1)。聚酯树脂的分子量为10000~12000,羟基值5~8mgkoh/g。
[0118]
本实施例制备得到的所述厚板聚氨酯底漆在金属板温224
±
5℃下固化,基板厚度2.5mm,底漆干涂膜厚10μm,配以性能一般的聚酯面漆,干涂膜厚15μm下的性能请参阅表4所示。
[0119]
实施例12
[0120]
同实施例1,区别在于:酸催化剂为二壬基萘磺酸封闭型酸。
[0121]
本实施例制备得到的所述厚板聚氨酯底漆在金属板温224
±
5℃下固化,基板厚度2.5mm,底漆干涂膜厚10μm,配以性能一般的聚酯面漆,干涂膜厚15μm下的性能请参阅表4所示。
[0122]
实施例13
[0123]
同实施例1,区别在于:酸催化剂为对甲苯磺酸、对甲苯磺酸封闭型酸和二壬基萘磺酸的混合物(体积比为1:2:2)。
[0124]
本实施例制备得到的所述厚板聚氨酯底漆在金属板温224
±
5℃下固化,基板厚度2.5mm,底漆干涂膜厚10μm,配以性能一般的聚酯面漆,干涂膜厚15μm下的性能请参阅表4所示。
[0125]
实施例14
[0126]
同实施例1,区别在于,溶剂其中的s-100改为s-150。
[0127]
本实施例制备得到的所述厚板聚氨酯底漆在金属板温224
±
5℃下固化,基板厚度2.5mm,底漆干涂膜厚10μm,配以性能一般的聚酯面漆,干涂膜厚15μm下的性能请参阅表4所示。
[0128]
实施例15
[0129]
同实施例1,区别在于:步骤1)还包括加入分散剂(r-5310resin)1份。本实施例制备得到的所述厚板聚氨酯底漆在金属板温224
±
5℃下固化,基板厚度2.5mm,底漆干涂膜厚10μm,配以性能一般的聚酯面漆,干涂膜厚15μm下的性能请参阅表4所示。
[0130]
表4
[0131][0132]
从表4的数据可以看出,选择实验中提供的原料,对所述厚板聚氨酯底漆性能并无明显影响。
[0133]
其中,具体测试方式为:
[0134]
voc:挥发有机物,通过测试背面漆的比重和固含量计算得到;
[0135]
反向冲击:无剥落;
[0136]
弯曲试验:无剥落;
[0137]
杯突试验:无剥落;
[0138]
耐(甲基乙基酮,丁酮)mek:2公斤力往返次数;
[0139]
耐酸试验:10%hcl溶液浸泡24h无异常;
[0140]
耐碱试验:10%naoh溶液浸泡24h无异常;
[0141]
划格后耐沸水煮:刀片划格后沸水煮2h无异常;
[0142]
盐雾试验:10%nacl溶液喷淋,板面划叉及边缘处锈蚀范围≤2mm(3级标准)。
[0143]
对比例1
[0144]
同实施例1,区别在于所添加聚酯树脂为es-600,分子量7000,羟值16~20mgkoh/g。所得厚板聚氨酯底漆t弯为4t,明显差于实施例1。
[0145]
对比例2
[0146]
同实施例1,区别在于所添加聚酯树脂skybon es 420总和为17份,氨基树脂yp5603为7份。
[0147]
计算得聚酯氨基比为1.2,聚酯异氰酸酯比为2.7。由于聚酯过少、氨基过多,导致氨基自交联过多,成膜后的漆膜过脆,所得厚板聚氨酯底漆t弯为4t,耐盐雾1000h级别为4级,性能不合格。
[0148]
对比例3
[0149]
同实施例1,区别在于所添加异氰酸酯desmodur 3175sn 1份,环氧树脂epikote 828el 1.4份。
[0150]
计算得聚酯异氰酸酯比为19.2,环氧树脂比为0.06。由于异氰酸酯过少,树脂未能充分交联,柔韧性远差于添加异氰酸酯的底漆,所得厚板聚氨酯底漆t弯为4t,mek为80来回,性能不合格。
[0151]
对比例4
[0152]
同实施例1,区别在于聚酯树脂skybon es 420总和为36份,环氧树脂epikote 828el 3份,颜料钛白粉r-996 21份、硫酸钡precipitated barium sulfate 5份。计算得颜基比为0.9;由于颜基比过低,所得厚板聚氨酯底漆耐盐雾1000h级别为5级,不合格,硬度亦不及实施例1。
[0153]
对比例5
[0154]
同实施例1,区别在于聚酯树脂skybon es 420总和为36份,氨基树脂yp5603为1份,异氰酸酯desmodur 3175sn 7份。
[0155]
计算得聚酯氨基比为8.8。由于聚酯过多,不能充分交联,所得厚板聚氨酯底漆mek明显变差,为70来回。
[0156]
由实施例与对比例的结果比较可知:
[0157]
1、各树脂及颜料的加入比例在合理范围内(聚酯氨基比为2~5,聚酯异氰酸酯比为3~6,环氧树脂比为0.08~0.12,颜基比为1.0~1.8),性能达到标准要求。超出本范围,部分性能不达标。
[0158]
2、环氧树脂比的合格范围为0.08~0.12,在下限处耐化学药品性差,上限处耐化学药品性有所提高,但t弯明显下降,综合各性能,得出性能最优的环氧树脂比为0.11。
[0159]
3、使用小分子量的聚酯树脂,并不能在厚板上满足t弯要求(考核柔韧性),而大分子量的饱和聚酯树脂skybon es 420应用于厚板底漆,可达到0t无剥落要求。
[0160]
本发明提供的厚板聚氨酯底漆t弯能达到0t无裂纹,柔韧性好,避免在加工过程中出现掉漆现象;耐盐雾性能高,配合一般性能的聚酯面漆,盐雾实验1000小时达到1级;基板附着力与面漆附着力均优于传统的环氧底漆和聚酯底漆。本发明提供的厚板聚氨酯底漆相比传统的底漆,兼备更优的附着力、柔韧性及耐化学腐蚀性。
[0161]
显然,本发明的上述实施例仅仅是为清楚地说明本发明所作的举例,而并非是对本发明的实施方式的限定,对于所属领域的普通技术人员来说,在上述说明的基础上还可以做出其它不同形式的变化或变动,本发明所例举的实施例无法对所有的实施方式予以穷尽,凡是属于本发明的技术方案所引伸出的显而易见的变化或变动仍处于本发明的保护范围之列。在本发明中提及的所有文献都在本申请中引用作为参考,就如同一篇文献被单独引用为参考那样。
起点商标作为专业知识产权交易平台,可以帮助大家解决很多问题,如果大家想要了解更多知产交易信息请点击 【在线咨询】或添加微信 【19522093243】与客服一对一沟通,为大家解决相关问题。
此文章来源于网络,如有侵权,请联系删除



tips