一种去磨纹的硅蚀刻液的制作方法



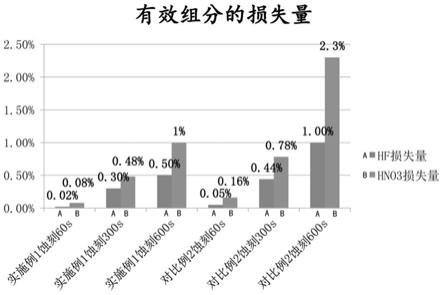
[0001]
本发明属于湿电子化学品和晶圆背面打毛加工交叉技术领域,具体涉及一种去磨纹的硅蚀刻液。
背景技术:
[0002]
在集成电路芯片的制造中,需要在硅片背面注入金属,此金属层可做为电极、接合、导热用的金属层,从而起到散热及降低电阻的效果。然而,在背面金属化制程之前需要对晶圆背面打毛处理,否则硅片表面太光滑,金属离子难以在表面附着、停留,金属层难以与基材紧密连结,则导致金属层剥离、电阻上升、影响半导体器件的可靠性。业界已有几款硅蚀刻液能够实现晶圆的背面打毛,例如专利文献1,专利文献2。专利文献1蚀刻速率较低,在单位时间里的去除量少,只适用于经化学晶圆减薄液处理过的硅片,无法满足深磨纹的机械研磨片的蚀刻。因此专利文献2先用10-16%的hf,20-30%hno
3
,15%-25%的h
2
so
4
,14-20%的h
3
po
4
和20%-30%的水的蚀刻混合物来进行损伤蚀刻,去除机械磨痕;然后再用3%-7%的hf,3%-7%的hno
3
,75%-85%的h
2
so
4
,5%-15%的水的蚀刻混合物来制造粗糙表面,如果只用去损伤蚀刻液处理硅片,由于其蚀刻速率过快难以控制,导致蚀刻表面不均匀,药液稳定性差,如果只用上述制造粗糙表面的蚀刻液蚀刻的话,蚀刻后仍有磨纹出现,因此必须经过两道工序。并且由于不同厂家研磨硅片的工艺设备有所差异,导致有的硅片磨纹很深,直接用打毛液去处理的话仍会留下很深的纹痕,因此在用背面打磨液之前一般都用晶圆减薄液处理机械磨纹,这样冗长复杂的工序必会增加制造的成本。
[0003]
因此开发一款去磨纹蚀刻液能够直接用于磨片的背面打毛工艺,蚀刻掉较深的机械磨纹,省略了抛光去磨纹工序,方能节约成本,提高生产效率。
[0004]
专利文献1:一种硅片打磨液cn 109913222 a专利文献2:粗蚀刻硅太阳能电池的工艺cn 1411612 a
技术实现要素:
[0005]
有鉴于此,本发明目的在于提供了一种高蚀刻速率的去磨纹蚀刻液,能够直接运用于磨纹很深的机械磨片上,缩短了工艺时间,节约了成本,同时获得蚀刻表面均匀平整,无机械磨纹残留的粗糙表面;本发明提供的一种高使用寿命的去磨纹蚀刻液,能够在蚀刻速率较快的情况下,补充有效组分的消耗,减少有效气体的挥发,维持稳定的蚀刻寿命。
[0006]
为实现上述目的,本发明技术方案提供一种去磨纹的硅蚀刻液,其含有硝酸、硝酸羟胺、氟磺酸、二氟化氢铵、二氟化氙、硫酸、增稠剂和去离子水,该蚀刻液被直接用于机械磨片的背面打毛工艺。
[0007]
其中,去磨纹的硅蚀刻液中硝酸的重量含量在3%~7%;硝酸羟胺的重量含量在0.01%~0.5%;氟磺酸的重量含量在0.1%~1%;二氟化氢铵的重量含量在4%~8%;二氟化氙的重量含量在0.1%~2%;硫酸的重量含量在75%~85%;增稠剂的重量含量在
0.01%~0.1%;去离子水的重量含量为余量。
[0008]
其中,去磨纹的硅蚀刻液中的增稠剂包括聚丙烯酰胺、己醇、辛醇、聚乙二醇、聚乙烯吡咯烷酮中的至少一种;并优选聚丙烯酰胺或聚乙二醇。
[0009]
本发明的技术方案中,硝酸为主氧化剂,硝酸羟胺和硝酸反应生成的亚硝酸,提高了硅的氧化速率,同时也补充了硝酸的消耗。
[0010]
所述的氟磺酸与硝酸羟胺反应生成羟胺-o-磺酸和氢氟酸,其反应如下:fho
3
s+nh
2
oh
→
nh
2
oso
2
oh+hf,增加了蚀刻液组合物中氢氟酸的浓度,能够抑制上述蚀刻液组合物的经时变化。
[0011]
所述的二氟化氢铵在蚀刻液中主要以二氟化物的形式存在,由于二氟化物有助于二氧化硅表面被质子化的羟基脱离以及由于hf
2-中,f-h-f的键角接近180
°
,使其氟比较容易进攻硅原子,从而导致二氧化硅的溶解速率大大提高。
[0012]
所述的二氟化氙在酸性环境下缓慢分解生成的氧气,作为助氧化剂增强了溶液的氧化性能,同时二氟化氙在酸性环境下缓慢分解生成氢氟酸,补充了蚀刻液组合物中氢氟酸的消耗,维持稳定的蚀刻速率。
[0013]
所述的硫酸一方面提供氧化反应活化能,使反应迅速开始,另一方面使腐蚀过程产生的气泡附着于硅片表面,形成掩蔽效应,进而形成了粗糙的磨砂表面。
[0014]
所述的增稠剂可以是聚丙烯酰胺、己醇、辛醇、聚乙二醇、聚乙烯吡咯烷酮等中的任意一种,该增稠剂增加了溶液的黏度,影响氮氧化物等生成气泡的大小与稳定性等,增加了反应活性气体的溶解性,减小了反应过程中有效组份的挥发,延长了蚀刻液的寿命。同时蚀刻液黏度的增加,其传质阻力变大,波峰的蚀刻速率远远大于波谷的蚀刻速率,从而导致蚀刻表面越来越平整。
[0015]
本发明的优点和有益效果在于:在本发明中,硝酸羟胺和硝酸反应生成的亚硝酸和二氟化氙在酸性环境下缓慢分解生成的氧气,提高了硅的氧化速率,二氟化氢铵在蚀刻液中主要以二氟化物的形式存在,导致二氧化硅的溶解速率大大提高,因此增加了蚀刻速率,提高了去除量,同时增稠剂增加了蚀刻液的黏度,使其传质阻力变大,波峰的蚀刻速率远远大于波谷的蚀刻速率,从而降低表面粗糙度,蚀刻表面越来越平整。因此能够直接用于磨片的背面打毛工艺,蚀刻掉较深的机械磨纹,省略了抛光去磨纹工序,节约了成本,提高了生产效率。此外,本发明中,硝酸羟胺和硝酸反应生成的亚硝酸,维持了硝酸的氧化性,硝酸强胺与氟磺酸反应生成氢氟酸与二氟化氙在酸性环境下缓慢分解生成氢氟酸,均增加蚀刻液组合物中的氢氟酸的浓度,避免hf被消耗而引起蚀刻速率大幅下降的问题,同时,该增稠剂增加了溶液的黏度,影响氮氧化物等生成气泡的大小与稳定性等,增加了反应活性气体的溶解性,减小了反应过程中硝酸、氮氧化物、氢氟酸等有效组份的挥发,维持了蚀刻液的长效稳定性。
附图说明
[0016]
图1为蚀刻前肉眼观察到的机械磨片的表面状态。
[0017]
图2为蚀刻前500倍显微镜下机械磨片的表面状态。
[0018]
图3为实施例1蚀刻后肉眼观察到的机械磨片的表面状态。
[0019]
图4为实施例1蚀刻后500倍显微镜下机械磨片的表面状态。
[0020]
图5为对比例1蚀刻后肉眼观察到的机械磨片的表面状态。
[0021]
图6为对比例1蚀刻后500倍显微镜下机械磨片的表面状态。
[0022]
图7为实施例1的蚀刻寿命。
[0023]
图8为实施例1和对比例2蚀刻过程中有效组分的损失量。
[0024]
图9为对比例2的蚀刻寿命。
具体实施方式
[0025]
为了更好地理解本发明,下面结合图表和实施例对本发明做进一步地详细说明,但是本发明要求保护的范围并不局限于下面的实施例。
[0026]
实施例1实施例1提供了一种去磨纹蚀刻液和蚀刻结果,具体为:硝酸的重量含量为5%;硝酸羟胺的重量含量为0.3%;氟磺酸的重量含量为0.6%;二氟化氢铵的重量含量为6%;二氟化氙的重量含量为1%;硫酸的重量含量为82%;聚丙烯酰胺的重量含量为0.05%;去离子水的重量含量为余量。
[0027]
将上述去磨纹的硅蚀刻液在25℃下,对机械研磨片(3cm
×
3cm)进行蚀刻实验,蚀刻方式为旋转喷淋蚀刻,蚀刻时间为1min,利用螺旋测微仪检测蚀刻前后硅片的厚度,并计算出蚀刻速率,蚀刻速率=(h
1-h
2
)/t,并用表面粗糙度仪检测蚀刻前后表面的roughness,ra1、ra2,并用肉眼和500倍显微镜观察表面磨纹的去除情况。
[0028]
h
1
为反应前硅片的厚度,h
2
为反应后硅片的厚度,t为反应时间,ra1为反应前的表面粗糙度,ra2为反应后的表面粗糙度。并将蚀刻效果记录于表1中,蚀刻前的表面状态如图1、图2所示,蚀刻后表面无磨纹,如图3、图4所示。
[0029]
将上述去磨纹的硅蚀刻液在25℃下,对机械研磨片进行蚀刻寿命的实验,蚀刻方式为旋转喷淋蚀刻,先用500ml的上述药液分别循环蚀刻60s、300s、600s后再蚀刻新的磨片1min,测量蚀刻速率,其蚀刻寿命如图7所示,并用氟离子电极和分光光度计检测循环蚀刻60s、300s、600s后药液中的hf和hno
3
的含量,其hf和hno
3
的损失情况如图8所示。
[0030]
实施例2一种去磨纹蚀刻液和蚀刻结果,具体为:硝酸的重量含量为6%;硝酸羟胺的重量含量为0.5%;氟磺酸的重量含量为1%;二氟化氢铵的重量含量为5%;二氟化氙的重量含量为2%;硫酸的重量含量为80%;聚乙二醇的重量含量为0.1%;去离子水的重量含量为余量。
[0031]
蚀刻效果的检测手段同实施例1,并将蚀刻效果记录于表1中。
[0032]
实施例3一种去磨纹蚀刻液和蚀刻结果,具体为:硝酸的重量含量为5%;硝酸羟胺的重量含量为0.5%;氟磺酸的重量含量为0.4%;二氟化氢铵的重量含量为6.5%;二氟化氙的重量含量为0.5%;硫酸的重量含量为82%;聚丙烯酰胺的重量含量为0.03%;去离子水的重量含量为余量。
[0033]
蚀刻效果的检测手段同实施例1,并将蚀刻效果记录于表1中。对比例1:对比例1提供了一种去磨纹蚀刻液和蚀刻结果,具体为:硝酸的重量含量为5%;二氟化氢铵的重量含量为6%;硫酸的重量含量为82%;去离子
水的重量含量为余量。
[0034]
蚀刻效果的检测手段同实施例1,并将蚀刻效果记录于表1中,蚀刻后表面仍有磨纹残留,如图5、图6所示。
[0035]
对比例2对比例2提供了一种去磨纹蚀刻液和蚀刻结果,具体为:硝酸的重量含量为8%;二氟化氢铵的重量含量为10%;硫酸的重量含量为76%;去离子水的重量含量为余量。
[0036]
蚀刻效果的检测手段同实施例1,并将蚀刻效果记录于表1中。
[0037]
将上述去磨纹的硅蚀刻液在25℃下,对机械研磨片进行蚀刻寿命的实验,蚀刻方式为旋转喷淋蚀刻,先用500ml的上述药液分别循环蚀刻60s、300s、600s后再蚀刻新的磨片1min,测量蚀刻速率,其蚀刻寿命如图9所示,并用氟离子电极和分光光度计检测循环蚀刻60s、300s、600s后药液中的hf和hno
3
的含量,其hf和hno
3
的损失情况如图8所示。
[0038]
实施例4一种去磨纹蚀刻液和蚀刻结果,具体为:硝酸的重量含量为6%;硝酸羟胺的重量含量为0.5%;氟磺酸的重量含量为1%;二氟化氢铵的重量含量为5%;硫酸的重量含量为80%;聚乙二醇的重量含量为0.1%;去离子水的重量含量为余量。
[0039]
蚀刻效果的检测手段同实施例1,并将蚀刻效果记录于表1中。
[0040]
实施例5一种去磨纹蚀刻液和蚀刻结果,具体为:硝酸的重量含量为6%;硝酸羟胺的重量含量为0.5%;氟磺酸的重量含量为1%;二氟化氢铵的重量含量为5%;二氟化氙的重量含量为2.4%;硫酸的重量含量为80%;聚乙二醇的重量含量为0.1%;去离子水的重量含量为余量。
[0041]
蚀刻效果的检测手段同实施例1,并将蚀刻效果记录于表1中。
[0042]
实施例6一种去磨纹蚀刻液和蚀刻结果,具体为:硝酸的重量含量为5%;硝酸羟胺的重量含量为0.5%;氟磺酸的重量含量为0.4%;二氟化氢铵的重量含量为9%;二氟化氙的重量含量为0.5%;硫酸的重量含量为80%;聚丙烯酰胺的重量含量为0.03%;去离子水的重量含量为余量。
[0043]
蚀刻效果的检测手段同实施例1,并将蚀刻效果记录于表1中。
[0044]
实施例7一种去磨纹蚀刻液和蚀刻结果,具体为:硝酸的重量含量为5%;硝酸羟胺的重量含量为0.5%;氟磺酸的重量含量为0.4%;二氟化氢铵的重量含量为3%;二氟化氙的重量含量为0.5%;硫酸的重量含量为82%;聚丙烯酰胺的重量含量为0.03%;去离子水的重量含量为余量。
[0045]
蚀刻效果的检测手段同实施例1,并将蚀刻效果记录于表1中。
[0046]
实施例8一种去磨纹蚀刻液和蚀刻结果,具体为:硝酸的重量含量为5%;氟磺酸的重量含量为0.6%;二氟化氢铵的重量含量为6%;二
氟化氙的重量含量为1%;硫酸的重量含量为82%;聚丙烯酰胺的重量含量为0.05%;去离子水的重量含量为余量。
[0047]
蚀刻效果的检测手段同实施例1,并将蚀刻效果记录于表1中。
[0048]
实施例9一种去磨纹蚀刻液和蚀刻结果,具体为:硝酸的重量含量为5%;硝酸羟胺的重量含量为1%;氟磺酸的重量含量为0.6%;二氟化氢铵的重量含量为6%;二氟化氙的重量含量为1%;硫酸的重量含量为82%;聚丙烯酰胺的重量含量为0.05%;去离子水的重量含量为余量。
[0049]
蚀刻效果的检测手段同实施例1,并将蚀刻效果记录于表1中。
[0050]
通过表1中的实验数据和图1-6可以得出,对比例1,蚀刻速率慢,蚀刻去除量少,传质效应变弱,蚀刻后表面有很深的磨纹残留,实施例1、2、3、通过添加了硝酸羟胺、二氟化氙及二氟化物使其蚀刻速率提高了近3倍,加上增稠剂的协同作用,增加了溶液的传质阻力,使得蚀刻后表面平整无磨纹。对比例2虽然通过增加硝酸和氢氟酸的含量提高了蚀刻速率,但是如图9所示,其蚀刻速率随着硝酸、氢氟酸的消耗挥发急剧下降。对比实施例1与实施例8、9,当不添加硝酸羟胺时,蚀刻速率较低,仍有较浅的磨纹存在,当添加1%的硝酸羟胺时,反应速率难以控制,有大量的棕色烟雾冒出,蚀刻后硅片表面出现褐色的斑点。对比实施例2与实施例4、5,当不加二氟化氙时,蚀刻速率较慢且寿命短,当加入过量的二氟化氙时,硅片表面生成点状黑色多孔硅。对比实施例3和实施例6、7,当加入过量的二氟化氢铵后,由于氢氟酸过量生成了黑色的多孔硅,而当二氟化氢铵只有3%含量时,蚀刻速率较慢,导致硅片边缘处仍有浅磨纹残留。如图7、8所示,实施例1通过添加硝酸羟胺、氟磺酸、二氟化氙补充了硝酸和氢氟酸的损失,同时增稠剂的加入增加了溶液的黏度,增加了反应活性气体的溶解性,减小了反应过程中有效组份的挥发,延长了蚀刻液的寿命。因此该去磨纹硅蚀刻液取得了显著的提升效果。
[0051]
表1实施例1至3及对比例1至8进行蚀刻实验的实验效果。
[0052]
起点商标作为专业知识产权交易平台,可以帮助大家解决很多问题,如果大家想要了解更多知产交易信息请点击 【在线咨询】或添加微信 【19522093243】与客服一对一沟通,为大家解决相关问题。
此文章来源于网络,如有侵权,请联系删除



tips