一种镀锌钢板用耐指纹表面处理剂及其制备方法与流程



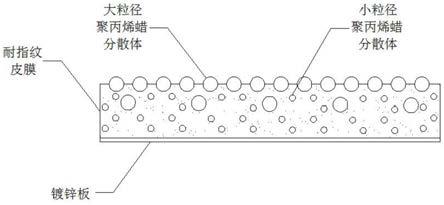
[0001]
本发明属于金属表面处理技术领域,具体涉及一种镀锌钢板用耐指纹表面处理剂及其制备方法。
背景技术:
[0002]
镀锌钢板被广泛用于汽车、建材、家电和机电行业。但是,使用以上金属材料的锌会在大气中被腐蚀或出现白锈,从而影响到金属材料的外观,更会造成涂装性能低下的不良影响。
[0003]
为了改善耐蚀性及涂装附着性催生了金属表面使用含有铬酸、重铬酸或其盐类为主的处理液,也就是我们通常所说的铬处理。但是,随着近年环保意识的不断提高,由于金属材料表面处理时使用的铬处理液中的6价铬对人体有害,铬处理逐渐被淘汰。另外,含有6价铬的排水须遵从水质污浊防止法的规定,须要进行特别的处理,这成为总成本过高的原因。再者,实施过铬处理的金属材料作为含铬产业废弃物不能再生利用的巨大缺点,成为社会问题。
[0004]
为解决上述问题,公开号为cn104073100b的中国发明专利公开了一种镀锌钢板用低温耐指纹表面处理剂及环保型表面处理镀锌钢板,采用特定的水系树脂、特定的磷化物、特定的有机硅化合物、钛化合物、钒化物、氧化聚乙烯颗粒组成的皮膜对镀锌钢板进行表面处理。但是在使用中,上述材料组成的皮膜具有抗划伤性性差、表面爽滑性不足的问题,使具有皮膜的镀锌钢板在进行二次加工时容易受损,影响镀锌钢板的质量。
技术实现要素:
[0005]
本发明的目的在于提供一种镀锌钢板用耐指纹表面处理剂,克服了现有技术的不足,提升耐指纹皮膜的抗划伤性和爽滑性,进而保障了镀锌钢板的二次加工质量。
[0006]
为解决上述问题,本发明所采取的技术方案如下:
[0007]
一种镀锌钢板用耐指纹表面处理剂,所述表面处理剂包括聚乙烯蜡分散体,且聚乙烯蜡分散体由粒径为0.5-0.8μm和4-6μm的乳液或分散体按照1:(1-2)的重量比组成。
[0008]
进一步,该表面处理剂由以下重量组分的原料组成:
[0009][0010]
进一步,所述阳离子聚氨酯树脂中至少含有一种选自伯氨基、仲胺基、叔氨基的阳离子性官能团。
[0011]
进一步,所述聚丙烯酸树脂选自具有一个或多个非离子性官能团的水溶性聚丙烯酸树脂。
[0012]
进一步,所述硅烷偶联剂选自含有活性氢的氨基或环氧基中的一种。
[0013]
进一步,所述二氧化硅化合物采用以正硅酸乙酯、水、乙醇和催化剂按照1:3:50:3的摩尔比进行反应制得的溶胶,其中催化剂采用氨水或者盐酸,所述溶胶中二氧化硅的粒径在10nm-50nm之间。
[0014]
进一步,所述有机硅化合物为直链含氢有机硅氧烷与烯丙基环氧乙烷和环氧丙烷化合物在铂催化剂下通过硅氢加成反应而成,其中烯丙基环氧乙烷与环氧丙烷的比例优选1:1。
[0015]
一种基于上述的镀锌钢板用耐指纹表面处理剂的制备方法,包括以下步骤:
[0016]
(1)按照上述配方称取原料,取一具有搅拌功能的反应釜,向反应釜内加入水,然后将阳离子聚氨酯树脂和聚丙烯酸树脂缓慢的加入到反应釜中,搅拌均匀,然后升温至40-60℃,再向反应釜内依次添加硅烷偶联剂、二氧化硅化合物、钒化合物和有机硅化合物,并搅拌均匀,得到混合物;
[0017]
(2)向步骤(1)得到的混合物中缓慢的加入粒径为0.5-0.8μm的聚乙烯蜡分散体,期间分2-5次加入,且每次加入后搅拌10-15min;待小粒径的聚乙烯蜡分散体加完后再分多次加入粒径为4-6μm的聚乙烯蜡分散体,持续搅拌5-10min;
[0018]
(3)在搅拌条件下,进行灌装,即得所述表面处理剂。
[0019]
进一步,所述步骤(1)中搅拌速度为100-120rpm,所述步骤(2)中搅拌速度为200-500rpm。
[0020]
本发明与现有技术相比较,具有以下有益效果:
[0021]
1、本发明通过添加不同粒径的聚乙烯蜡分散体,由于大粒径分散体具有较低的比重,可以漂浮于耐指纹皮膜的表面,起到抗划伤作用,由于小粒径的分散体的比重与混合物的比重接近,小粒径的分散体与混合物可以完全的混合均匀,使小粒径分散体贯穿整体皮
膜中,成膜时赋予整个膜层的爽滑性,通过不同粒径的聚乙烯蜡分散体的相互作用,赋予整个耐指纹皮膜的爽滑性和抗划伤性,进而保障了镀锌钢板的二次加工质量。
[0022]
2、本发明采用将小粒径分散体分次加入,并通过搅拌、停止搅拌再开启搅拌的循环操作,提高瞬间剪切力,使小粒径分散体充分分散在混合物中,成膜时进一步提升皮膜的爽滑度。
[0023]
3、本发明通过阳离子聚氨酯树脂和聚丙烯酸树脂为主成膜物质,对镀锌钢板表面起到主要的防腐蚀作用,硅烷偶合剂加水分解生成的硅烷醇基团脱水缩合形成连续皮膜;二氧化硅化合物具有补充表面成膜缺陷的作用,使耐指纹皮膜更加完整。
附图说明
[0024]
图1为本发明使用后表面处理皮膜的结构示意图。
具体实施方式
[0025]
下面将结合本发明实施例中的附图,对本发明实施例中的技术方案进行清楚、完整地描述,显然,所描述的实施例仅仅是本发明一部分实施例,而不是全部的实施例。基于本发明中的实施例,本领域普通技术人员在没有做出创造性劳动前提下所获得的所有其他实施例,都属于本发明保护的范围。
[0026]
实施例1
[0027]
本发明公开了一种镀锌钢板用耐指纹表面处理剂的制备方法,包括以下步骤:
[0028]
(1)按照质量百分比分别称取阳离子聚氨酯树脂15%、聚丙烯酸树脂10%、硅烷偶联剂1%、二氧化硅化合物1%、钒化合物1%、有机硅化合物0.1%、聚乙烯蜡分散体0.5%和水71.4%,其中聚乙烯蜡分散体由粒径为0.5-0.8μm和4-6μm的乳液或分散体按照1:1的重量比组成。
[0029]
(2)取一具有搅拌功能的反应釜,向反应釜内加入水,然后将阳离子聚氨酯树脂和聚丙烯酸树脂缓慢的加入到反应釜中,搅拌均匀,然后升温至40-60℃,再向反应釜内依次添加硅烷偶联剂、二氧化硅化合物、钒化合物和有机硅化合物,并按照100-120rpm的速度、搅拌均匀,得到混合物;
[0030]
(3)向步骤(2)得到的混合物中缓慢的加入粒径为0.5-0.8μm的聚乙烯蜡分散体,期间分2-5次加入,且每次加入后按照200-500rpm的速度、搅拌10-15min;待小粒径的聚乙烯蜡分散体加完后再加入粒径为4-6μm的聚乙烯蜡分散体,持续搅拌5-10min;
[0031]
(4)在搅拌条件下,进行灌装,即得表面处理剂。
[0032]
其中,阳离子聚氨酯树脂中至少含有一种选自伯氨基、仲胺基、叔氨基的阳离子性官能团;聚丙烯酸树脂选自具有一个或多个非离子性官能团的水溶性聚丙烯酸树脂;硅烷偶联剂选自含有活性氢的氨基或环氧基中的一种;二氧化硅化合物采用以正硅酸乙酯、水、乙醇和催化剂按照1:3:50:3的摩尔比进行反应制得的溶胶,其中催化剂采用氨水或者盐酸,溶胶中二氧化硅的粒径在10nm-50nm之间;有机硅化合物为直链含氢有机硅氧烷与烯丙基环氧乙烷和环氧丙烷化合物在铂催化剂下通过硅氢加成反应而成,其中烯丙基环氧乙烷与环氧丙烷的比例优选1:1。
[0033]
实施例2
[0034]
本发明公开了一种镀锌钢板用耐指纹表面处理剂的制备方法,包括以下步骤:
[0035]
(1)按照质量百分比分别称取阳离子聚氨酯树脂23%、聚丙烯酸树脂15%、硅烷偶联剂3%、二氧化硅化合物3%、钒化合物3%、有机硅化合物0.3%、聚乙烯蜡分散体2%和水50.7%,其中聚乙烯蜡分散体由粒径为0.5-0.8μm和4-6μm的乳液或分散体按照1:1的重量比组成。
[0036]
(2)取一具有搅拌功能的反应釜,向反应釜内加入水,然后将阳离子聚氨酯树脂和聚丙烯酸树脂缓慢的加入到反应釜中,搅拌均匀,然后升温至40-60℃,再向反应釜内依次添加硅烷偶联剂、二氧化硅化合物、钒化合物和有机硅化合物,并按照100-120rpm的速度、搅拌均匀,得到混合物;
[0037]
(3)向步骤(2)得到的混合物中缓慢的加入粒径为0.5-0.8μm的聚乙烯蜡分散体,期间分2-5次加入,且每次加入后按照200-500rpm的速度、搅拌10-15min;待小粒径的聚乙烯蜡分散体加完后再加入粒径为4-6μm的聚乙烯蜡分散体,持续搅拌5-10min;
[0038]
(4)在搅拌条件下,进行灌装,即得表面处理剂。
[0039]
其中,表面处理剂内的固体组分重量占表面处理剂重量的15-17%;阳离子聚氨酯树脂中至少含有一种选自伯氨基、仲胺基、叔氨基的阳离子性官能团;聚丙烯酸树脂选自具有一个或多个非离子性官能团的水溶性聚丙烯酸树脂;硅烷偶联剂选自含有活性氢的氨基或环氧基中的一种;二氧化硅化合物采用以正硅酸乙酯、水、乙醇和催化剂按照1:3:50:3的摩尔比进行反应制得的溶胶,其中催化剂采用氨水或者盐酸,溶胶中二氧化硅的粒径在10nm-50nm之间;有机硅化合物为直链含氢有机硅氧烷与烯丙基环氧乙烷和环氧丙烷化合物在铂催化剂下通过硅氢加成反应而成,其中烯丙基环氧乙烷与环氧丙烷的比例优选1:1。
[0040]
实施例3
[0041]
本发明公开了一种镀锌钢板用耐指纹表面处理剂的制备方法,包括以下步骤:
[0042]
(1)按照质量百分比分别称取阳离子聚氨酯树脂30%、聚丙烯酸树脂20%、硅烷偶联剂5%、二氧化硅化合物5%、钒化合物5%、有机硅化合物5%、聚乙烯蜡分散体5%和水25%,其中聚乙烯蜡分散体由粒径为0.5-0.8μm和4-6μm的乳液或分散体按照1:1的重量比组成。
[0043]
(2)取一具有搅拌功能的反应釜,向反应釜内加入水,然后将阳离子聚氨酯树脂和聚丙烯酸树脂缓慢的加入到反应釜中,搅拌均匀,然后升温至40-60℃,再向反应釜内依次添加硅烷偶联剂、二氧化硅化合物、钒化合物和有机硅化合物,并按照100-120rpm的速度、搅拌均匀,得到混合物;
[0044]
(3)向步骤(2)得到的混合物中缓慢的加入粒径为0.5-0.8μm的聚乙烯蜡分散体,期间分2-5次加入,且每次加入后按照200-500rpm的速度、搅拌10-15min;待小粒径的聚乙烯蜡分散体加完后再加入粒径为4-6μm的聚乙烯蜡分散体,持续搅拌5-10min;
[0045]
(4)在搅拌条件下,进行灌装,即得表面处理剂。
[0046]
其中,阳离子聚氨酯树脂中至少含有一种选自伯氨基、仲胺基、叔氨基的阳离子性官能团;聚丙烯酸树脂选自具有一个或多个非离子性官能团的水溶性聚丙烯酸树脂;硅烷偶联剂选自含有活性氢的氨基或环氧基中的一种;二氧化硅化合物采用以正硅酸乙酯、水、乙醇和催化剂按照1:3:50:3的摩尔比进行反应制得的溶胶,其中催化剂采用氨水或者盐酸,溶胶中二氧化硅的粒径在10nm-50nm之间;有机硅化合物为直链含氢有机硅氧烷与烯丙
基环氧乙烷和环氧丙烷化合物在铂催化剂下通过硅氢加成反应而成,其中烯丙基环氧乙烷与环氧丙烷的比例优选1:1。
[0047]
实施例4
[0048]
本实施例的原料配比和制备方法与实施例2基本一致,唯有区别的是:聚乙烯蜡分散体由粒径为0.5-0.8μm和4-6μm的乳液或分散体按照1:1.5的重量比组成。
[0049]
实施例5
[0050]
本实施例的原料配比和制备方法与实施例2基本一致,唯有区别的是:聚乙烯蜡分散体由粒径为0.5-0.8μm和4-6μm的乳液或分散体按照1:2的重量比组成。
[0051]
对比例1
[0052]
本对比例的原料配比和制备方法与实施例2基本一致,唯有区别的是:聚乙烯蜡分散体采用粒径为0.5-0.8μm的小粒径乳液或分散体。
[0053]
对比例2
[0054]
本对比例的原料配比和制备方法与实施例2基本一致,唯有区别的是:聚乙烯蜡分散体采用粒径为4-6μm的大粒径乳液或分散体。
[0055]
对比例3
[0056]
本对比例的原料配比和制备方法与实施例2基本一致,唯有区别的是:步骤(2)中将小粒径的聚乙烯蜡分散体一次性加入到反应釜内,再搅拌10-15min。
[0057]
验证实验:
[0058]
选取相同大小、形状的九组镀锌钢板,分别采用等量的实施例1-5、对比例1-3和cn104073100b专利申请中实施例3的方法(对照组)生产的表面处理剂对镀锌钢板进行处理,获得九组经过表面处理的镀锌钢板,并采用以下方法进行评价;
[0059]
1、耐碱性
[0060]
在所提供的表面处理镀锌钢板的表面滴下1%苛性苏打水溶液10μl、放置30秒后,用水冲洗肉眼观察表面外观变化。评价标准如下:
[0061]ⅰ级:皮膜表面完全没有痕迹;
[0062]ⅱ级:皮膜表面具有肉眼可观察的痕迹;
[0063]ⅲ级:皮膜表面有明显的白痕迹,且皮膜开始溶解。
[0064]
2、耐溶剂性
[0065]
试剂使用乙醇及80%乙醇和20%水的混合溶液、甲基乙基酮、二甲苯,分别用纱布浸渍后在表面处理镀锌钢板的表面用力来回摩擦50次后,目视观察评价表面外观变化。评价标准如下:
[0066]ⅰ级:擦拭部分完全没有痕迹;
[0067]ⅱ级:擦拭部分有肉眼可观察的痕迹;
[0068]ⅲ级:擦拭部分有明显的白痕迹,且皮膜开始溶解。
[0069]
3、耐腐蚀性
[0070]
通过盐水喷雾试验(jis z 2371)、目视测定耐白锈性,对白锈面积达到5%的时间进行评价。
[0071]
4、抗划伤性
[0072]
采用具有500g荷重的钢丝绒分别对表面处理镀锌钢板的表面来回摩擦100次,目
视观察评价表面外观变化。评价标准如下:
[0073]ⅰ级:摩擦部分完全没有痕迹;
[0074]ⅱ级:摩擦部分有肉眼可观察的痕迹;
[0075]ⅲ级:摩擦部分有明显的白痕迹,并出现裂痕。
[0076]
5、爽滑性
[0077]
分别对提供的表面处理镀锌钢板的表面进行摩擦系数的测试。
[0078]
具体的检测结果见下表:
[0079][0080]
根据上表可知,本发明通过在添加不同粒径的聚乙烯蜡分散体和采用分次添加搅拌的方法生产出的表面处理剂相较于现有技术,在耐碱性、划伤性和爽滑性上有着明显的提升,能够保障镀锌钢板的二次加工。
[0081]
对于本领域技术人员而言,显然本发明不限于上述示范性实施例的细节,而且在不背离本发明的精神或基本特征的情况下,能够以其他的具体形式实现本发明。因此,无论从哪一点来看,均应将实施例看作是示范性的,而且是非限制性的,本发明的范围由所附权利要求而不是上述说明限定,因此旨在将落在权利要求的等同要件的含义和范围内的所有变化囊括在本发明内。不应将权利要求中的任何附图标记视为限制所涉及的权利要求。
起点商标作为专业知识产权交易平台,可以帮助大家解决很多问题,如果大家想要了解更多知产交易信息请点击 【在线咨询】或添加微信 【19522093243】与客服一对一沟通,为大家解决相关问题。
此文章来源于网络,如有侵权,请联系删除



tips