一种超疏水涂料及其制备方法与应用与流程



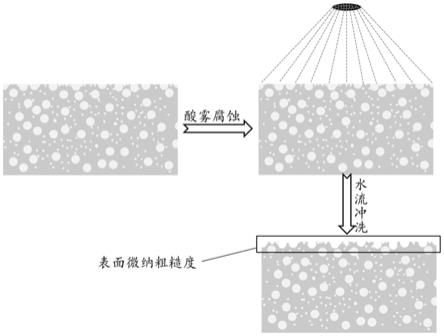
[0001]
本发明涉及超疏水涂料技术领域,具体涉及一种超疏水涂料及其制备方法与应用。
背景技术:
[0002]
公开该背景技术部分的信息仅仅旨在增加对本发明的总体背景的理解,而不必然被视为承认或以任何形式暗示该信息构成已经成为本领域一般技术人员所公知的现有技术。
[0003]
超疏水材料是一种表面与水的接触角大于150
°
、滚动角小于10
°
的材料,具有优异的防水、自清洁、防腐蚀性能,在医学、国防、日常生活以及其他工业领域具有广阔的应用前景。
[0004]
目前来说,对超疏水材料的研究已经取得了很大的进展,但是仍存在着很大的不足。比如说制备超疏水表面所需的设备昂贵,步骤繁琐,反应条件复杂。化学刻蚀法是制备超疏水材料的一种相对简单高效的方法,其通过酸溶液或碱溶液对材料的表面进行腐蚀,从而构造出合适的粗糙度。
[0005]
但是,目前化学刻蚀法多用于金属材料,有一定的局限性。金属材料材质较硬,没有弹性,构造出的微纳粗糙度容易在外力磨损下丧失。而且金属材料本身表面能较高,构造出表面粗糙度以后还需要进行低表面能处理才能获得超疏水表面。
技术实现要素:
[0006]
针对上述的不足,本发明提供一种超疏水涂料及其制备方法与应用,本发明不仅能够制备出粗糙度优异的超疏水表面,而且超疏水表面具有耐磨性强、稳定性好的优点。为实现上述目的,本发明的技术方案如下所示:
[0007]
在本发明的第一方面,提供一种超疏水涂料,其原料组成包括如下组分:含有碳酸钙的组分、有机高分子弹性体、固化剂、纳米碳酸钙(二氧化硅全部换成纳米碳酸钙),还包括酸溶液。
[0008]
进一步地,以重量份计,所述含有碳酸钙的组分为0.5-4份、有机高分子弹性体为10-20份、固化剂为0.13-2份、纳米碳酸钙为0.1-0.5份。
[0009]
进一步地,所述含有碳酸钙的组分包括石灰岩粉、石灰石粉(或碳酸钙粉)、贝壳粉、含纳米碳酸钙的锯泥等中的至少一种。优选地,所述含有碳酸钙的组分为含纳米碳酸钙的锯泥;优选地,所述含有碳酸钙的组分的粒径范围为0.1-100um,该范围有助于以制备出粗糙度优异的超疏水表面。
[0010]
锯泥是一种石材加工过程中产生的石粉与水和少量切削液的混合物,由于石粉质地细腻,不仅干燥后容易起尘,造成空气污染,其堆放还占用了大量的土地资源,是一种难处理的固体废弃物,对生态环境影响较大。在本发明中,将锯泥掺加到有机高分子弹性体中,不仅提高了有机高分子弹性体的力学性能,降低了成本,而且便于利用酸性溶液对进行
刻蚀制备粗糙度优异的超疏水表面。
[0011]
进一步地,所述有机高分子弹性体包括羟基封端、乙烯基封端或烷氧基封端的聚二甲基硅氧烷,氟硅树脂,氟碳树脂等中的至少一种。本发明以有机高分子弹性体为超疏水涂基体,具有耐酸碱性好,表面能低的特点。
[0012]
进一步地,所述固化剂的种类视所述有机高分子弹性体的种类而定,例如,有机高分子弹性体为羟基封端的聚二甲基硅氧烷时以γ-氨丙基三乙氧基硅烷为固化剂,有机高分子弹性体为氟硅树脂时,固化剂为六亚甲基二异氰酸酯。在本发明中,固化剂的主要作用是加快有机硅弹性体的固化速度。
[0013]
进一步地,所述纳米碳酸钙粒径为10-100nm。在本发明中,区别于所述含有碳酸钙的组分,纳米碳酸钙的主要作用是在涂层表面构造纳米级别的粗糙度。
[0014]
进一步地,所述酸溶液为能够溶解碳酸钙的物质,例如,盐酸、硫酸、醋酸等中的任意一种或几种,优选地,所述酸溶液的浓度为0.05-1mol/l。在本发明中,酸溶液的主要作用是溶解基体表面中的碳酸钙,使表面出现蚀坑,制备出粗糙度优异的超疏水表面,因此,酸溶液的添加量可根据需要使用,本发明不做具体限定。
[0015]
在本发明的第二方面,提供所述超疏水涂料的制备方法,包括步骤:
[0016]
(1)将有机高分子弹性体、纳米碳酸钙和含有碳酸钙的组分混合均匀,然后加入固化剂,待反应完成后得到前驱体涂料,备用。
[0017]
(2)在所述前驱体涂料表面施加酸溶液,反应后将表面残留的酸性溶液和反应产物洗涤干净,得具有优异超疏水表面的涂层。
[0018]
进一步地,在步骤(1)中,在1000-2000rpm转速下搅拌10-15min使有机高分子弹性体、纳米碳酸钙和含有碳酸钙的组分混合均匀,以便于将含有碳酸钙的组分均匀分布在后续反应后得到的涂料基体中。
[0019]
进一步地,在步骤(1)中,所述反应时间为3-5min,通过反应使有机高分子弹性体反应形成涂料基体。同时,在本步骤不参与反应的含有碳酸钙的组分被均匀分布在基体中,而基体表面中的碳酸钙成为后续制备粗糙度优异的超疏水表面的基础。
[0020]
进一步地,在步骤(2)中,采用喷雾瓶将酸溶液喷洒在前驱体涂料表面,优选为喷洒2-3遍,以便于充分去除前驱体涂料表面中的碳酸钙。
[0021]
进一步地,在步骤(2)中,所述反应时间为30-45min,然后用水将表面残留的酸性溶液和反应产物洗涤干净,即得。
[0022]
进一步地,在步骤(2)中,当含有碳酸钙的组分为锯泥时,先用水将锯泥洗涤,然后将锯泥烘干,最后粉磨,完成后与有机高分子弹性体混合进行后续工序。可选地,将锯泥水洗2-3遍后在100-130℃的烘箱内烘干12-24h,然后粉磨至过800目筛。锯泥的主要成分为碳酸钙,与盐酸、硫酸、醋酸等反应后生成co2和水溶性钙盐,钙盐在用水洗涤后即可去除,使涂层表面呈现出优异的粗糙度,同时,也使锯泥组分更加纯净。
[0023]
在本发明的第三方面,公开所述超疏水涂料、所述方法制备的超疏水涂料在建筑业、工农业生产、管道运输、国防军事等领域中的应用。例如,用于海洋工程中混凝土的外表面,减缓水进入混凝土的速率,提高混凝土的耐久性。
[0024]
相较于现有技术,本发明提供的技术方案至少具有以下有益效果:
[0025]
(1)本发明超疏水表面涂层的制备方法简单高效,其制备过程不需要特殊的设备、
反应条件及原料,有利于超疏水表面涂层的工业化、规模化制备。
[0026]
(2)本发明利用碳酸钙可以被容易刻蚀的特点,将碳酸钙掺入低表面能的有机高分子弹性体中,不仅提高了有机高分子弹性体的力学性能,降低了成本。又可通过酸性溶液将涂层表面的碳酸钙刻蚀掉,赋予表面足够的微纳粗糙度,制备超疏水表面。
[0027]
(3)本发明使用的基材为有机高分子弹性体,其表面能低,弹性好,卸去外力后仍能恢复成原来的状态,耐磨性强,稳定性好;因为有机高分子弹性体在遭受外力磨损过程中,撤去外力仍可恢复到原来的状态,表面的微纳结构不会像金属材料表面一样很容易就遭到破坏,保证了超疏水表面的稳定性。
[0028]
(4)锯泥的主要成分为碳酸钙,将其作为一种无机填料掺加到有机高分子弹性体中,不仅提高了有机高分子弹性体的力学性能,降低了成本。又可使用酸性溶液将表面的锯泥刻蚀掉,赋予表面足够的微纳粗糙度,制备超疏水表面。而且有利于实现锯泥废料的资源化利用,减少了锯泥对环境造成的不利影响。
附图说明
[0029]
构成本发明的一部分的说明书附图用来提供对本发明的进一步理解,本发明的示意性实施例及其说明用于解释本发明,并不构成对本发明的不当限定。以下,结合附图来详细说明本发明的实施方案,其中:
[0030]
图1为本发明实施例中利用锯泥制备超疏水涂层的原理示意图。
[0031]
图2为本发明第一实施例、第二实施例、第一至第四试验例利用锯泥制备的超疏水涂层的接触角测试图。
具体实施方式
[0032]
下面结合具体实施例,进一步阐述本发明。应理解,这些实施例仅用于说明本发明而不用于限制本发明的范围。下列实施例中未注明具体条件的实验方法,通常按照常规条件或按照制造厂商所建议的条件。
[0033]
除非另行定义,本发明中所使用的所有专业与科学用语与本领域熟练人员所熟悉的意义相同。本发明所使用的试剂或原料均可通过常规途径购买获得,如无特殊说明,本发明所使用的试剂或原料均按照本领域常规方式使用或者按照产品说明书使用。此外,任何与所记载内容相似或均等的方法及材料皆可应用于本发明方法中。本发明中所述的较佳实施方法与材料仅作示范之用。
[0034]
下列实施例中,所述锯泥原料来自重庆新伟奇石材有限公司,其主要为大理石锯泥、石灰岩锯泥、方解石锯泥、花岗岩锯泥中的一种或几种的混合物,主要成分为碳酸钙。
[0035]
下列实施例中,所述酸液为采用高浓度市售产品自行稀释配置而来。
[0036]
下列实施例中,所述有机高分子弹性体、纳米碳酸钙、石灰岩粉、石灰石粉、贝壳粉均为市售产品。
[0037]
第一实施例
[0038]
一种超疏水涂料的制备方法,包括如下步骤:
[0039]
(1)锯泥的预处理:用蒸馏水将锯泥原料洗涤3遍,洗涤后的锯泥在100℃的烘箱内烘干20h,粉磨至过800目筛。
[0040]
(2)前驱体涂层的制备:将羟基封端的聚二甲基硅氧烷18重量份、步骤(1)干燥后的锯泥2.5重量份、0.3重量份纳米碳酸钙置于搅拌机中,在2000rpm转速下搅拌10min,混合均匀后加入0.36重量份γ-氨丙基三乙氧基硅烷,再次搅拌5min,得到前驱体涂层。
[0041]
(3)超疏水涂层的制备(参考图1):用喷雾瓶将浓度0.5mol/l的盐酸溶液喷洒在步骤(2)制备的涂层上,喷洒3遍,以便于涂层表面中的碳酸钙与盐酸反应,反应40min后用蒸馏水将涂层表面残留的盐酸溶液和反应产物洗涤干净,即得到超疏水涂层。
[0042]
第二实施例
[0043]
一种超疏水涂料的制备方法,包括如下步骤:
[0044]
(1)锯泥的预处理:用蒸馏水将锯泥原料洗涤2遍,洗涤后的锯泥在100℃的烘箱内烘干24h,粉磨至过800目筛。
[0045]
(2)前驱体涂层的制备:将氟硅树脂10重量份、步骤(1)干燥后的锯泥0.5重量份、0.1重量份纳米碳酸钙置于搅拌机中,在1800rpm转速下搅拌12min,混合均匀后加入1重量份六亚甲基二异氰酸酯,再次搅拌3min,得到前驱体涂层。
[0046]
(3)超疏水涂层的制备(参考图1):用喷雾瓶将浓度1mol/l的醋酸溶液喷洒在步骤(2)制备的涂层上,喷洒2遍,以便于涂层表面中的碳酸钙与盐酸反应,反应30min后用蒸馏水将涂层表面残留的盐酸溶液和反应产物洗涤干净,即得到超疏水涂层。
[0047]
第三实施例
[0048]
一种超疏水涂料的制备方法,包括如下步骤:
[0049]
(1)锯泥的预处理:用蒸馏水将锯泥原料洗涤2遍,洗涤后的锯泥在130℃的烘箱内烘干12h,粉磨至过800目筛。
[0050]
(2)前驱体涂层的制备:将氟碳树脂12重量份、步骤(1)干燥后的锯泥1.5重量份、0.15重量份纳米碳酸钙置于搅拌机中,在1000rpm转速下搅拌15min,混合均匀后加入1.2重量份六亚甲基二异氰酸酯,再次搅拌4min,得到前驱体涂层。
[0051]
(3)超疏水涂层的制备(参考图1):用喷雾瓶将浓度0.05mol/l的盐酸溶液喷洒在步骤(2)制备的涂层上,喷洒3遍,以便于涂层表面中的碳酸钙与盐酸反应,反应45min后用蒸馏水将涂层表面残留的盐酸溶液和反应产物洗涤干净,即得到超疏水涂层。
[0052]
第四实施例
[0053]
一种超疏水涂料的制备方法,包括如下步骤:
[0054]
(1)锯泥的预处理:用蒸馏水将锯泥原料洗涤3遍,洗涤后的锯泥在110℃的烘箱内烘干15h,粉磨至过800目筛。
[0055]
(2)前驱体涂层的制备:将乙烯基封端的聚二甲基硅氧烷20重量份、步骤(1)干燥后的锯泥4重量份、0.5重量份纳米碳酸钙置于搅拌机中,在1000rpm转速下搅拌15min,混合均匀后加入2重量份甲基氢硅氧烷二甲基硅氧烷,再次搅拌4min,得到前驱体涂层。
[0056]
(3)超疏水涂层的制备(参考图1):用喷雾瓶将浓度0.05mol/l的硫酸溶液喷洒在步骤(2)制备的涂层上,喷洒3遍,以便于涂层表面中的碳酸钙与盐酸反应,反应45min后用蒸馏水将涂层表面残留的盐酸溶液和反应产物洗涤干净,即得到超疏水涂层。
[0057]
第五实施例
[0058]
一种超疏水涂料的制备方法,包括如下步骤:
[0059]
(1)锯泥的预处理:用蒸馏水将锯泥原料洗涤3遍,洗涤后的锯泥在120℃的烘箱内
烘干18h,粉磨至过800目筛。
[0060]
(2)前驱体涂层的制备:将氟硅树脂15重量份、步骤(1)干燥后的锯泥3重量份、0.25重量份纳米碳酸钙置于搅拌机中,在1500rpm转速下搅拌12min,混合均匀后加入1.5重量份六亚甲基二异氰酸酯,再次搅拌5min,得到前驱体涂层。
[0061]
(3)超疏水涂层的制备(参考图1):用喷雾瓶将浓度0.1mol/l的盐酸溶液喷洒在步骤(2)制备的涂层上,喷洒3遍,以便于涂层表面中的碳酸钙与盐酸反应,反应35min后用蒸馏水将涂层表面残留的盐酸溶液和反应产物洗涤干净,即得到超疏水涂层。
[0062]
第六实施例
[0063]
一种超疏水涂料的制备方法,包括如下步骤:
[0064]
(1)前驱体涂层的制备:将羟基封端的聚二甲基硅氧烷16重量份、过800目筛的碳酸钙粉3重量份、0.27重量份纳米碳酸钙置于搅拌机中,在1500rpm转速下搅拌10min,混合均匀后加入0.32重量份γ-氨丙基三乙氧基硅烷,再次搅拌5min,得到前驱体涂层。
[0065]
(2)超疏水涂层的制备(参考图1):用喷雾瓶将浓度0.5mol/l的盐酸溶液喷洒在步骤(1)制备的涂层上,喷洒3遍,以便于涂层表面中的碳酸钙与盐酸反应,反应35min后用蒸馏水将涂层表面残留的盐酸溶液和反应产物洗涤干净,即得到超疏水涂层。
[0066]
第七实施例
[0067]
一种超疏水涂料的制备方法,包括如下步骤:
[0068]
(1)前驱体涂层的制备:将氟碳树脂13重量份、过800目筛的贝壳粉1重量份、0.22重量份纳米碳酸钙置于搅拌机中,在1500rpm转速下搅拌10min,混合均匀后加入0.13重量份六亚甲基二异氰酸酯再次搅拌4min,得到前驱体涂层。
[0069]
(2)超疏水涂层的制备(参考图1):用喷雾瓶将浓度0.1mol/l的硫酸溶液喷洒在步骤(1)制备的涂层上,喷洒3遍,以便于涂层表面中的碳酸钙与盐酸反应,反应40min后用蒸馏水将涂层表面残留的盐酸溶液和反应产物洗涤干净,即得到超疏水涂层。
[0070]
第八实施例
[0071]
一种超疏水涂料的制备方法,包括如下步骤:
[0072]
(1)前驱体涂层的制备:将氟碳树脂20重量份、过800目筛的石灰岩粉3重量份、0.3重量份纳米碳酸钙置于搅拌机中,在1800rpm转速下搅拌15min,混合均匀后加入2重量份六亚甲基二异氰酸酯再次搅拌5min,得到前驱体涂层。
[0073]
(2)超疏水涂层的制备(参考图1):用喷雾瓶将浓度1mol/l的醋酸溶液喷洒在步骤(1)制备的涂层上,喷洒3遍,以便于涂层表面中的碳酸钙与盐酸反应,反应30min后用蒸馏水将涂层表面残留的盐酸溶液和反应产物洗涤干净,即得到超疏水涂层。
[0074]
第一试验例
[0075]
一种超疏水涂料的制备方法,包括如下步骤:
[0076]
(1)锯泥的预处理:用蒸馏水将锯泥原料洗涤3遍,洗涤后的锯泥在100℃的烘箱内烘干20h,粉磨至过800目筛。
[0077]
(2)涂层的制备:将羟基封端的聚二甲基硅氧烷18重量份、步骤(1)干燥后的锯泥2.5重量份、0.3重量份纳米碳酸钙置于搅拌机中,在2000rpm转速下搅拌10min,混合均匀后加入0.36重量份γ-氨丙基三乙氧基硅烷,再次搅拌5min,反应40min后用蒸馏水将涂层表面洗涤干净,即得涂层。
[0078]
第二试验例
[0079]
一种超疏水涂料的制备方法,包括如下步骤:
[0080]
(1)锯泥的预处理:用蒸馏水将锯泥原料洗涤2遍,洗涤后的锯泥在100℃的烘箱内烘干24h,粉磨至过800目筛。
[0081]
(2)前驱体涂层的制备:将氟硅树脂10重量份、步骤(1)干燥后的锯泥0.5重量份、0.1重量份纳米碳酸钙置于搅拌机中,在1800rpm转速下搅拌12min,混合均匀后加入1重量份六亚甲基二异氰酸酯,再次搅拌3min,反应30min后用蒸馏水将涂层表面洗涤干净,即得到超疏水涂层。
[0082]
第三试验例
[0083]
一种超疏水涂料的制备方法,包括如下步骤:
[0084]
(1)前驱体涂层的制备:将羟基封端的聚二甲基硅氧烷18重量份置于搅拌机中,在2000rpm转速下搅拌10min,然后加入0.36重量份γ-氨丙基三乙氧基硅烷,再次搅拌5min,得到前驱体涂层。
[0085]
(2)涂层的制备:用喷雾瓶将浓度0.5mol/l的盐酸溶液喷洒在步骤(1)制备的涂层上,喷洒3遍,40min后用蒸馏水将涂层表面洗涤干净,即得。
[0086]
第四试验例
[0087]
一种超疏水涂料的制备方法,包括如下步骤:
[0088]
(1)前驱体涂层的制备:将氟硅树脂10重量份置于搅拌机中,在1800rpm转速下搅拌12min,混合均匀后加入1重量份六亚甲基二异氰酸酯,再次搅拌3min,得到前驱体涂层。
[0089]
(2)涂层的制备:用喷雾瓶将浓度1mol/l的醋酸溶液喷洒在步骤(1)制备的涂层上,喷洒2遍,30min后用蒸馏水将涂层表面洗涤干净,即得。
[0090]
性能测试
[0091]
采用量角法、jc2000型号的接触角测量仪仪器对上述实施例制备的超疏水涂层的疏水性能进行测试,采用dd-3086型号的电动铅笔硬度计对上述实施例制备的超疏水涂层的力学性能进行测试,结果如表1所示。
[0092]
表1
[0093]
[0094][0095]
从表1中可以看出,涂层的铅笔硬度和抗冲击强度主要受选择的基材的影响,由于使用的基材均为有机高分子弹性体,实施例和试验例的铅笔硬度和抗冲击强度差异不大。但将实施例和试验例进行对比可以看出,试验例均不具备超疏水性能,其中第三试验例和第四试验例接触角最小(参考图1),为所用有机高分子弹性体本身的接触角,这是因为所选用的有机高分子弹性体对酸溶液有较强的耐受能力,经酸刻蚀后无法改变表面的粗糙度,因此不具备超疏水性能。第一试验例和第二部试验例未经过酸刻蚀,表面微纳结构未得到优化,因此也不具备超疏水性能,但是由于添加了锯泥颗粒,在表面构造了一定的粗糙度,相对于未掺加锯泥的试验例,接触角略大一些(参考图2)。从以上实施例和试验例可以看出,只有添加了含有碳酸钙成分的样品才能够被酸溶液刻蚀,进而产生具有足够微纳粗糙度的表面,具有超疏水性能。
[0096]
以上所述仅为本发明的优选实施例而已,并不用于限制本发明,尽管参照前述实施例对本发明进行了详细的说明,对于本领域的技术人员来说,其依然可以对前述各实施例所记载的技术方案进行修改,或者对其中部分技术特征进行等同替换。凡在本发明的精神和原则之内,所作的任何修改、等同替换、改进等,均应包含在本发明的保护范围之内。
起点商标作为专业知识产权交易平台,可以帮助大家解决很多问题,如果大家想要了解更多知产交易信息请点击 【在线咨询】或添加微信 【19522093243】与客服一对一沟通,为大家解决相关问题。
此文章来源于网络,如有侵权,请联系删除



tips