一种磁性磨料及其制备方法与流程



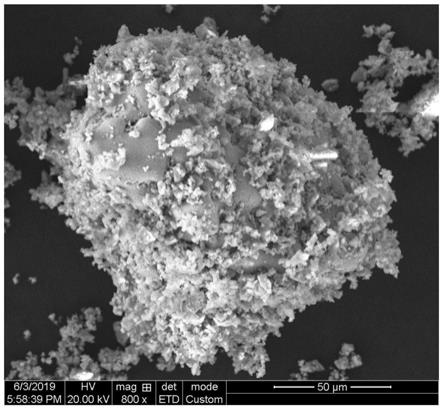
[0001]
本发明属于磁性磨料制备技术领域,尤其涉及一种磁性磨料及其制备方法。
背景技术:
[0002]
磁力研磨技术是通过磁场力驱动磁性磨料对加工件表面进行持续磨削,来实现对异形构件表面的高效、高精度加工,提高构件的耐久性。该方法在技术上具有优异的自适应性、自锐性和可控性,温升小、无须进行工具磨损补偿的特点,能够实现三维复杂曲面的研磨光整加工,并解决自动化问题,能降低零件的制造成本。因而在国内外引起了广泛的关注和研究,并已在平面、外圆面、内圆面和成型复杂型面以及微小结构零件和去毛刺等的研磨光整加工中得到了应用。
[0003]
磁性磨料作为磁力研磨技术的磨具,在磁力研磨技术中起着关键性的作用。磁性磨料的研磨性能和使用寿命与它的制备技术密切相关,因而磁性磨料的制备技术成为磁力研磨技术发展的核心问题。
[0004]
目前已报道的磁力磨料的制备工艺主要有:粘结法、机械混合法、雾化法和烧结法。其中,机械混合法制备磁性磨料中硬质相与铁磁相的界面结合强度差,容易分离飞散,导致加工效率较低;烧结法制备的磁性磨料中硬质相与铁磁相的界面存在fe、si和c原子的互相扩散现象,导致硬质相与铁磁相的界面结合强度差、硬质相在铁磁相表面分布不均匀。
技术实现要素:
[0005]
鉴于此,本发明的目的在于提供一种磁性磨料及其制备方法。本发明提供的制备方法制得的磁性磨料中硬质相与铁磁相的界面结合强度高。
[0006]
为了实现上述发明目的,本发明提供了以下技术方案:
[0007]
本发明提供了一种磁性磨料的制备方法,包括以下步骤:
[0008]
将碳化硅进行氧化处理,得到表面氧化碳化硅;
[0009]
将所述表面氧化碳化硅和铁磁相混合,得到混合料;
[0010]
将所述混合料进行热处理,得到磁性磨料;
[0011]
所述热处理的温度为800~1200℃,时间为2~4h。
[0012]
优选地,所述氧化处理的温度为800~1400℃,时间为8~12h。
[0013]
优选地,升温至所述氧化处理的温度的升温速率为5~10℃/min。
[0014]
优选地,所述混合的方式为球磨;所述球磨的转速为150~300rpm,时间为3~5h。
[0015]
优选地,所述球磨的球料比为(8~10):1,装填系数为0.4~0.6。
[0016]
优选地,所述碳化硅的粒径为10~20μm。
[0017]
优选地,所述铁磁相的粒径为100~150μm。
[0018]
优选地,所述铁磁相包括羰基铁、铁硅合金、铁铝合金或铁镍合金。
[0019]
优选地,所述铁磁相和表面氧化碳化硅的质量比为(2~5):1。
[0020]
本发明还提供了上述技术方案所述制备方法制得的磁性磨料,包括铁磁相核芯和
包括铁磁相核芯和镶嵌于所述铁磁相核芯表面的表面氧化碳化硅层。
[0021]
本发明提供的制备方法,包括以下步骤:将碳化硅进行氧化处理,得到表面氧化碳化硅;将所述表面氧化碳化硅和铁磁相混合,得到混合料;将所述混合料进行热处理,得到磁性磨料;所述热处理的温度为800~1200℃,时间为2~4h。本发明将碳化硅进行氧化处理后,在碳化硅表面形成的氧化膜可作为反应阻挡层,隔离碳化硅与铁磁相的直接接触,阻挡化学性质活泼的fe、si和c原子间的互相扩散,抑制界面反应的发生,提高界面稳定性;碳化硅表面形成的氧化膜可以阻隔两相界面反应,从而改善润湿性,提高界面结合强度,进而提高磁性磨料的加工性能,延长磁性磨料的使用寿命;通过热处理使铁磁相变为熔而不化的状态,表面氧化碳化硅均匀的镶嵌于铁磁相表面,增大表面氧化碳化硅与铁磁相的界面接触面积,提高表面氧化碳化硅与铁磁相之间界面的结合强度以及磁性磨料的相对磁导率,进一步提高了磁性磨料的加工性能以及加工效率。且本发明提供的制备方法实现了硬质相和铁磁相之间由机械结合至冶金结合的转变。
附图说明
[0022]
图1为本发明制备磁性磨料的原理示意图;
[0023]
图2为实施例1得到的磁性磨料的sem图;
[0024]
图3为对比例1得到的磁性磨料的sem图。
具体实施方式
[0025]
本发明提供了一种磁性磨料的制备方法,包括以下步骤:
[0026]
将碳化硅进行氧化处理,得到表面氧化碳化硅;
[0027]
将所述表面氧化碳化硅和铁磁相球磨,得到混合料;
[0028]
将所述混合料进行热处理,得到磁性磨料。
[0029]
在本发明中,若无特殊说明,所采用的原料均为本领域常规市售产品。
[0030]
本发明将碳化硅进行氧化处理,得到氧化碳化硅。
[0031]
在本发明中,所述氧化处理的温度优选为800~1400℃,进一步优选为1000~1200℃;所述氧化处理的时间优选为8~12h,进一步优选为10~11h;升温至所述氧化处理的温度的升温速率优选为5~10℃/min,具体优选为5℃/min。本发明优选将所述碳化硅放置在坩埚内,并放置在加热炉中进行氧化处理。在本发明中,所述氧化处理优选在静态空气中进行。
[0032]
本发明优选将所述氧化碳化硅冷却至室温,所述冷却的方式优选为随炉冷却,所述冷却至室温的降温速率优选为5~10℃/min,具体优选为5℃/min。
[0033]
在本发明中,所述碳化硅的粒径优选为10~20μm。
[0034]
本发明通过对碳化硅进行氧化处理,在碳化硅表面形成一层氧化膜,这层氧化膜作为反应阻挡层,可有效隔离碳化硅与铁磁相之间的接触,阻挡化学活性高的fe、si和c原子之间的互相扩散,抑制界面反应的发生,提高界面稳定性,改善碳化硅与和铁磁相之间的润湿性,提高界面结合强度,进而提高磁性磨料的加工性能,延长其使用寿命。
[0035]
在本发明中,所述表面氧化碳化硅的表面氧化膜中包括二氧化硅;所述表面氧化膜的厚度优选为50~150nm,进一步优选为100nm。
[0036]
得到表面氧化碳化硅后,本发明将表面氧化碳化硅和铁磁相混合,得到混合料。
[0037]
本发明优选将所述表面氧化碳化硅先进行筛分后,再进行水洗,再与铁磁相混合。
[0038]
在本发明中,所述筛分后表面氧化碳化硅的粒径优选为10~20μm。本发明对所述筛分的方式没有特殊的限定,采用本领域技术人员熟知的筛分方式即可。在本发明中,所述水洗的方式优选为超声水洗,本发明对所述超声水洗的方式没有特殊的限定,能够有效去除其他污染物质即可。在本发明中,所述污染物质来源于加热炉内和坩埚内的污染物质。
[0039]
在本发明中,所述表面氧化碳化硅和铁磁相的质量比优选为1:(2~5),进一步优选为1:4。在本发明中,所述铁磁相优选包括羰基铁、铁硅合金、铁铝合金或铁镍合金,在本发明实施例中进一步优选为羰基铁。在本发明中,所述铁磁相的粒径优选为100~150μm。
[0040]
本发明优选将所述表面氧化碳化硅和铁磁相机械搅拌30~60min后,再进行混合。在本发明中,所述机械搅拌的速率优选为30~50rpm,具体优选为50rpm。在本发明中,所述混合的方式优选为球磨;所述球磨的介质优选为钢球,所述钢球的粒径优选为8~10mm;所述球磨的球料比优选为(8~10):1,即所述表面氧化碳化硅和铁磁相的混合物的质量与所述钢球的质量比优选为(8~10):1。在本发明中,所述球磨的装填系数优选为0.4~0.6;所述球磨的转速优选为150~300rpm,进一步优选为175~220rpm;所述球磨的时间优选为3~5h。在本发明中,所述球磨优选在球磨机中进行。本发明优选将所述球磨机抽真空后,再进行球磨。在本发明中,所述抽真空后的真空度优选为10-2
~10-3
pa。
[0041]
本发明通过球磨改善混合料的颗粒分布均匀性,增强表面氧化碳化硅和铁磁相之间界面的结合强度,使表面氧化碳化硅均匀地包覆在铁磁相的外表层。
[0042]
得到混合料后,本发明将所述混合料进行热处理,得到磁性磨料。
[0043]
在本发明中,所述热处理的温度为800~1200℃,优选为900~1100℃,进一步优选为1000℃;所述热处理的时间为2~4h,优选为2.5h;升温至所述热处理的温度的速率优选为5℃/min。在本发明中,所述热处理优选在真空烧结炉中进行。在本发明中,所述真空烧结炉的真空度优选为10-3
~10-4
pa。
[0044]
本发明通过控制热处理的温度和时间,使铁磁相为熔而不化的状态,表面氧化碳化硅镶嵌在铁磁相的表面,提高磁性磨料的结合强度,增大表面氧化碳化硅和铁磁相界面接触面积,提高了磁性磨料的相对磁导率。
[0045]
所述热处理完成后,本发明优选将热处理得到的产物冷却至室温,得到磁性磨料。在本发明中,所述冷却的方式优选为随炉冷却。
[0046]
图1为本发明制备磁性磨料的原理示意图,如图1所示,将氧化处理得到的表面氧化碳化硅颗粒与铁磁相混合,表面氧化碳化硅均匀包裹在铁磁相表面,经热处理后,表面氧化碳化硅镶嵌于铁磁相基体表面,提高界面结合强度。
[0047]
本发明还提供了上述技术方案所述制备方法制得的磁性磨料包括铁磁相核芯和包括铁磁相核芯和镶嵌于所述铁磁相核芯表面的表面氧化碳化硅层。在本发明中,所述磁性磨料中铁磁相核芯的质量百分含量优选为60~80%;所述磁性磨料中表面氧化碳化硅的质量百分含量优选为20~40%。在本发明中,所述表面氧化碳化硅层的厚度优选为50~150nm,进一步优选为100nm;所述表面氧化碳化硅镶嵌于所述铁磁相核芯表面的深度优选为500~1500nm。
[0048]
下面结合实施例对本发明提供的磁性磨料及其制备方法进行详细的说明,但是不
能把它们理解为对本发明保护范围的限定。
[0049]
实施例1
[0050]
将碳化硅置于加热炉中,在静态空气气氛中,将200g碳化硅(粒径为20μm),以5℃/min的升温速率升温至1200℃,进行氧化处理10h后,随炉冷却至室温,降温速率为5℃/min,得到表面氧化碳化硅;
[0051]
将得到的表面氧化碳化硅筛分,得到粒径为20μm表面氧化碳化硅后,进行超声水洗,去除杂质;
[0052]
按质量比为4:1的比例,将200g粒径为20μm表面氧化碳化硅和800g粒径为150μm的羰基铁混合,在50rpm的转速下,充分搅拌30min后,进行球磨,球磨介质为钢球,所述钢球的粒径为8~10mm,球料比为10:1,装填系数为0.4,转速为175rpm,球磨5h后,得到混合料;
[0053]
将得到的混合料放入真空烧结炉中,以5℃/min的升温速率升温至1200℃,进行热处理2.5h后,得到磁性磨料,磁性磨料包括羰基铁核芯和嵌入羰基铁核芯中的表面氧化碳化硅层。
[0054]
在下述研磨条件下测试所得磁性磨料的性能:磨料为本实施例所得磁性磨料;磁性磨料的填充量为3g;被加工工件为直径为10mm、壁厚为1mm的tc4钛管;研磨参数包括:转速为1500r/min,加工间隙为2mm,进给速度为100mm/min。
[0055]
通过测试所得磁性磨料的最佳研磨时间来确定磁性磨料中羰基铁基体和表面氧化碳化硅层之间的结合强度,所得结果为:本实施例所得磁性磨料的最佳研磨时间为30min;即所得磁性磨料在上述研磨条件下的使用寿命。
[0056]
通过测试所得磁性磨料在上述研磨条件下对被加工工件的表面粗糙度变化情况来测试磁性磨料的加工效率,测试结果为:在加工5min后,tc4钛管外壁初始粗糙度ra=1.10
±
0.01μm下降至ra=0.238
±
0.01μm。
[0057]
对比例1
[0058]
采用本领域熟知的常压烧结法制备的磁性磨料:
[0059]
按质量比为1:4的比例,将200g粒径为20μm表面氧化碳化硅和800g粒径为150μm的羰基铁混合,机械混合4h后,加入30g pva搅拌均匀,压制成块;
[0060]
将压制后的样品放入真空干燥箱中,在100℃条件下进行干燥,10h后取出,在真空管式炉中进行烧结,以5℃/min的升温速率升温至烧结温度1200℃,保温时间为2h,随炉冷却后机械破碎,破碎后的粒径为170μm。
[0061]
采用与实施例1相同的研磨条件测试本对比例所得磁性磨料的性能,所得结果为:本对比例所得磁性磨料的最佳研磨时间为20min;在加工5min后,tc4钛管外壁初始粗糙度ra=1.10
±
0.01μm下降至ra=0.62
±
0.01μm。
[0062]
图2为实施例1得到的磁性磨料的sem图,从图中可以看出,本发明制备得到的磁性磨料中表面氧化碳化硅镶嵌在铁磁相表面,且表面氧化碳化硅的分布均匀。图3为对比例1得到的磁性磨料的sem图,图中磨料黑色部分为硬质相,白色部分为铁磁相,从图3中可以看出,传统烧结法制备的磁性磨料硬质相在烧结过程中钝化,且分布不均,硬质相发生团聚现象,出现铁磁相与硬质相分离的情况,没有形成良好的包覆核壳结构。结合实施例1和对比例制备得到的磁性磨料中羰基铁基体和表面氧化碳化硅层之间的结合强度的测试结果分析可知,本发明提供的制备方法能够有效的提高磁性磨料中铁磁相基体与硬质相间份结合
强度。
[0063]
实施例2
[0064]
本实施例与实施例1的区别仅在于:将得到的混合料放入真空烧结炉中,在1200℃的条件下进行热处理,2h后,得到磁性磨料,磁性磨料包括羰基铁核芯和嵌入羰基铁核芯中的表面氧化碳化硅层。
[0065]
采用与实施例1相同的研磨条件测试本实施例所得磁性磨料的性能,所得结果为:本实施例所得磁性磨料的最佳研磨时间为25min;在加工5min后,tc4钛管外壁初始粗糙度ra=1.10
±
0.01μm下降至ra=0.274
±
0.01μm。
[0066]
实施例3
[0067]
本实施例与实施例1的区别仅在于:将得到的混合料放入真空烧结炉中,在800℃的条件下进行热处理,4h后,得到磁性磨料,磁性磨料包括羰基铁核芯和嵌入羰基铁核芯中的表面氧化碳化硅层。
[0068]
采用与实施例1相同的研磨条件测试本实施例所得磁性磨料的性能,所得结果为:本实施例所得磁性磨料的最佳研磨时间为15min;在加工5min后,tc4钛管外壁初始粗糙度ra=1.10
±
0.01μm下降至ra=0.361
±
0.01μm。
[0069]
对比例2
[0070]
本对比例与实施例1的区别仅在于:将得到的混合料放入真空烧结炉中,在700℃的条件下进行热处理,5h后,得到磁性磨料,磁性磨料包括羰基铁核芯和嵌入羰基铁核芯中的表面氧化碳化硅层。
[0071]
采用与实施例1相同的研磨条件测试本对比例所得磁性磨料的性能,所得结果为:本对比例所得磁性磨料的最佳研磨时间为16min;在加工5min后,tc4钛管外壁初始粗糙度ra=1.10
±
0.01μm下降至ra=0.378
±
0.01μm。
[0072]
对比例3
[0073]
本对比例与实施例1的区别仅在于:将得到的混合料放入真空烧结炉中,在1300℃的条件下进行热处理,1h后,得到磁性磨料,磁性磨料包括羰基铁核芯和嵌入羰基铁核芯中的表面氧化碳化硅层。
[0074]
采用与实施例1相同的研磨条件测试本对比例所得磁性磨料的性能,所得结果为:本对比例所得磁性磨料的最佳研磨时间为18min;在加工5min后,tc4钛管外壁初始粗糙度ra=1.10
±
0.01μm下降至ra=0.281
±
0.01μm。
[0075]
应用例
[0076]
对于初始粗糙度为ra=1.10
±
0.01μm的钛合金管壁,分别采用实施例1、对比例1、对比例2和对比例3制备的磁性磨料进行磁力研磨加工;所述研磨加工的参数包括:转速1000r/min,加工间隙2mm,进给速度:80mm/min,加工样品分别标记为r1(实施例1样品)、r2(对比例1样品)、r3(对比例2样品)和r4(对比例3样品),加工时间8min,加工长度30mm,分别对上述磁力研磨加工后的钛合金管壁的粗糙度进行测试,测试结果分别为:r1样品的粗糙度为ra=0.238
±
0.01μm、r2样品的粗糙度为ra=0.62
±
0.01μm、r3样品的粗糙度为ra=0.378
±
0.01μm和r4样品的粗糙度为ra=0.281
±
0.01μmμm;说明本发明提供的制备方法制得的磁性磨料具有良好的加工性能。
[0077]
以上所述仅是本发明的优选实施方式,应当指出,对于本技术领域的普通技术人
员来说,在不脱离本发明原理的前提下,还可以做出若干改进和润饰,这些改进和润饰也应视为本发明的保护范围。
起点商标作为专业知识产权交易平台,可以帮助大家解决很多问题,如果大家想要了解更多知产交易信息请点击 【在线咨询】或添加微信 【19522093243】与客服一对一沟通,为大家解决相关问题。
此文章来源于网络,如有侵权,请联系删除
相关标签: 硬质氧化



tips