一种双金属氰化物络合催化剂、其制法及聚丙二醇的制法的制作方法



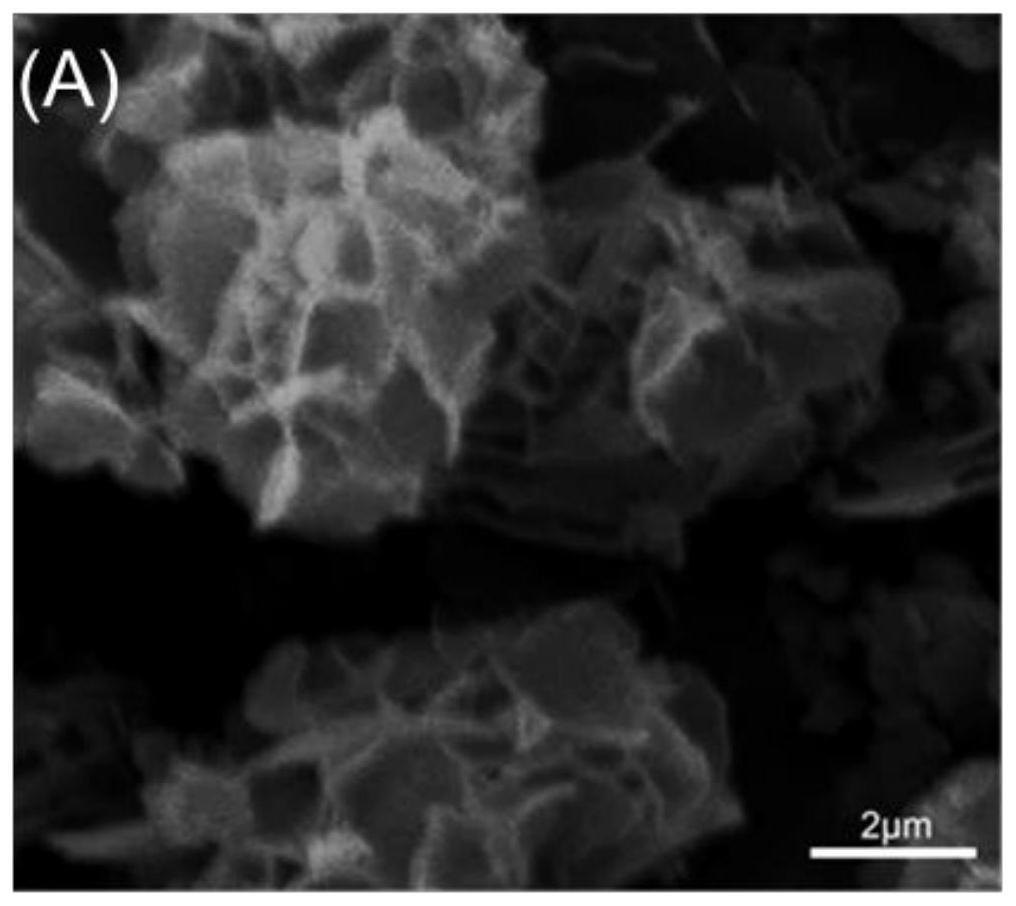
[0001]
本发明涉及一种催化剂、其制法及聚丙二醇的制法,尤其涉及一种双金属氰化物络合催化剂、其制法及聚丙二醇的制法。
背景技术:
[0002]
聚醚多元醇,又名聚氧化烯烃多元醇,是由各类含有活泼氢或胺类化合物作引发剂,与环氧烷烃开环聚合进行均聚或共聚而合成的。聚氨酯工业中,聚醚多元醇是塑料泡沫行业中用量最大的多元醇原料,俗称“白料”,是一类非常重要的非离子表面活性剂。目前聚醚多元醇合成所用催化剂主要有以下几种:(1)以金属na、k或csoh、koh等碱金属氢氧化物或ba(oh)2、sr(oh)2等碱土金属氢氧化物作为催化剂进行均相催化合成聚醚多元醇。(2)以碱土金属氧化物bao,水滑石类复合金属化合物为催化剂进行非均相催化合成聚醚多元醇。(3)以金属卟啉络合物、磷腈类催化剂、大环配合物催化剂等新型催化剂合成聚醚多元醇。(4)以双金属氰化物催化剂配位聚合合成聚醚多元醇。
[0003]
双金属氰化络合物是在1966年美国专利us3278457中由美国通用轮胎橡胶公司首次报道用于环氧丙烷均聚生成聚醚多元醇的一类高效非均相催化剂。目前双金属氰化物催化剂生产的聚醚产品与传统koh催化相比具有不饱和度低,催化活性高等特点,但还有一些亟待解决的问题:如dmc催化剂(双金属氰化物络合催化剂)很难直接引发小分子起始剂,可能的原因是两官能度及以上的小分子起始剂有多个相邻羟基,这些位置与活性中心结合时结合态比较牢固,难以进行单体链插入的引发反应,相邻羟基之间也存在一定的空间位阻效应。此外,目前公认叔丁醇作为有机配体时催化活性最高,但叔丁醇作配体时合成的聚醚往往分子量分布较宽,且叔丁醇在反应时易溶于聚合体系中作为引发剂而形成单官能度聚合物,降低了产物的官能度,严重影响了产品的下一步应用。
技术实现要素:
[0004]
发明目的:本发明的第一个目的是提供一种催化活性高并且能够引发小分子起始剂的双金属氰化物络合催化剂;
[0005]
本发明的第二个目的是提供一种双金属氰化物络合催化剂的制备方法;
[0006]
本发明的第三个目的是提供一种聚丙二醇的制备方法。
[0007]
技术方案:本发明的双金属氰化物络合催化剂,该催化剂满足以下通式:
[0008]
mcm@m
1a
[m
2b
(cn)
c
]
d
·
vm
1
(x)
e
·
wl
·
xh
2
o
·
yp
·
zs
[0009]
其中,mcm为介孔分子筛,m
1
为二价金属离子;m
2
为过渡金属离子;x为cl-、so
42-中的一个;a、b、c、d、e为正数;l为有机配体,p为共络合剂,s为过渡金属盐;v=0.5~3,w=0.1~2,x=0.1~2,y=0~0.1,z=0~0.01。
[0010]
优选的,所述有机配体为醚类和/或酯类;其中,所述醚类选自乙二醇丁醚和/或丙二醇丁醚,所述酯类选自乙酰乙酸甲酯和/或乙酰乙酸乙酯。
[0011]
优选的,所述共络合剂选自聚氧化丙烯氧化乙烯共聚物多元醇,分子量为2000~
8000。
[0012]
优选的,所述过渡金属盐为la(no
3
)
3
·
6h
2
o、cr(no
3
)
3
·
9h2o或ce(no
3
)
3
·
6h
2
o中的至少一种。
[0013]
优选的,所述过渡金属离子选自co
3+
和/或fe
2+
。
[0014]
上述双金属氰化物络合催化剂的制备方法,包括以下步骤:
[0015]
(1)配置金属氰化物络盐水溶液,命名为溶液a;在锌盐水溶液中加入过渡金属盐与有机配体,命名为溶液b;
[0016]
(2)将介孔分子筛载体与有机配体溶液混合,命名为溶液c;
[0017]
(3)在搅拌的情况下,将溶液a与溶液b同步滴加至溶液c中,然后加入有机配体和共络合剂,继续搅拌,得催化剂浆料;
[0018]
(4)将催化剂浆料进行过滤、分离、洗涤、干燥,得到所述双金属氰化物络合催化剂。
[0019]
优选的,步骤(1)中,所述金属氰化物络盐为钴氰化钾、铁氰化钾或镍氰化钾,所述锌盐为氯化锌、硫酸锌、醋酸锌或溴化锌。
[0020]
优选的,步骤(1)中,所述过渡金属盐的加入量为锌盐水溶液质量的0.5~3%。
[0021]
优选的,步骤(2)中,所述介孔分子筛载体与锌盐水溶液的质量比为1:5~15。
[0022]
优选的,步骤(3)中,所述共络合剂与锌盐水溶液的质量比为1:3~10。
[0023]
优选的,步骤(2)中,所述有机配体溶液中,溶液与有机配体l的体积比为1~3:1;其中,溶液优选为水。
[0024]
优选的,步骤(1)中,金属氰化物络盐水溶液的浓度为0.05~0.3mol/l;锌盐水溶液的浓度为2~6mol/l;
[0025]
优选的,步骤(2)中,在30~90℃油浴中,并在搅拌的情况下,将溶液a与溶液b同步滴加至溶液c中;所述溶液a与溶液b同步滴加的时间为20~60min,搅拌的转速控制在2000~5000r/min;继续搅拌0.5~2h;
[0026]
优选的,步骤(3)中,所述催化剂浆料过滤、分离后得到催化剂滤饼,所述催化剂滤饼用有机配体与水的混合溶液化浆洗涤3~5次,逐渐提高混合溶液中有机配体的比例直至用纯有机配体l进行化浆洗涤得到最终催化剂滤饼;将最终催化剂滤饼在50~80℃下真空干燥至恒重,磨碎得到催化剂粉末。
[0027]
上述双金属氰化物络合催化剂合成聚丙二醇的方法,包括以下步骤:将权利要求1所述的催化剂与起始剂投入反应器中,向反应器内通入惰性气体,向釜中加入环氧丙烷单体,所述环氧烷烃和起始剂的质量比为5~20:1;所述催化剂的加入量为原料加入量的100~1000ppm。
[0028]
优选的,控制起始压力0.1~1mpa、温度100~140℃、转速250~550r/min条件下聚合反应5~10h后,脱除未反应单体,经过滤分离产品与催化剂,得到聚丙二醇产品,所述聚丙二醇产品分子量分布较窄、醛值较低。
[0029]
有益效果:本发明与现有技术相比,取得如下显著效果:1、在介孔分子筛上负载活性组分双金属氰化物,催化剂结晶度低,在活性组分含量较低时仍有较高的催化活性;2、应用于聚丙二醇产品合成,分子量分布较窄、醛含量较低。3、本发明的催化剂易于引发小分子起始剂,一方面,由于本发明的催化活性高,另一方面,本发明的催化剂通过供电子有机配
体改性,削弱了引发剂与聚合单体之间配位能力的差距,从而能够顺利引发小分子起始剂。4、本发明的催化环氧丙烷开环聚合反应为配位聚合体系,该体系制备的聚丙二醇分子量分布较窄且催化剂用量低、反应条件温和,在氮气氛围下,环氧丙烷异构化现象较少,氧化反应也较少,故所制备的聚丙二醇产品分子量分布较窄、醛值较低。
附图说明
[0030]
图1为实施例1制备的dmc-1催化剂的sem图,其中,图1(a)、图1(b)分别为放大倍数15000倍和8000倍的sem图;
[0031]
图2为对比例1制备的zn
3
[co(cn)
6
]
2
·
12h
2
o和实施例1所制备的催化剂dmc-1的xrd谱图;
[0032]
图3为对比例1制备的zn
3
[co(cn)
6
]
2
·
12h
2
o和实施例1所制备的催化剂dmc-1的ftir谱图;
[0033]
图4为实施例1所制备催化剂dmc-1的局部ftir谱图;
[0034]
图5为实施例2与实施例3制备的聚丙二醇样品与标准样品的ftir图;
[0035]
图6为实施例3制备的聚丙二醇样品的
1
hnmr图。
具体实施方式
[0036]
下面结合说明书附图对本发明作进一步详细描述。
[0037]
实施例1
[0038]
本实施例公开了一种介孔分子筛承载的新型双金属氰化物络合催化剂的制备方法,其中,有机配体l为乙酰乙酸乙酯;共络合剂p为聚氧化丙烯氧化乙烯共聚物多元醇,分子量为3000,通过市售获得;过渡金属盐s选用la(no
3
)
3
·
6h
2
o;上述催化剂的具体制备步骤如下:
[0039]
(1)将3
×
10-3
mol钴氰化钾溶于18ml水中制得溶液a。将2.5
×
10-2
mol氯化锌溶于5ml水中得到氯化锌水溶液,再称取相当于氯化锌水溶液质量1%的la(no
3
)
3
·
6h
2
o和水体积一半的乙酰乙酸乙酯溶于氯化锌水溶液中制得溶液b。将0.8g介孔分子筛mcm-41加入30ml水与乙酰乙酸乙酯混合液中,其中,混合液中:水60%,乙酰乙酸乙酯40%;搅拌均匀制得溶液c。
[0040]
(2)80℃的油浴条件下,将溶液a与溶液b缓慢同步滴加至3000r/min的溶液c中,滴加时间为20min。再向溶液中加入10ml的水与乙酰乙酸乙酯的混合液、1.25g共络合剂p,继续搅拌混合30min;其中,水与乙酰乙酸乙酯的混合液中:水30%,乙酰乙酸乙酯70%。
[0041]
(3)搅拌完成后,将所得浆料冷却后过滤分离得到滤饼,所得滤饼用乙酰乙酸乙酯与水组成的混合溶液化浆洗涤3次,逐渐提高混合溶液中乙酰乙酸乙酯的比例直至用纯乙酰乙酸乙酯化浆洗涤得到最终催化剂滤饼。将最终的滤饼在50℃下真空干燥至恒重,磨碎后得到本催化剂,命名为dmc-1。
[0042]
催化剂组成的测定:结合电感耦合等离子体发射光谱icp、元素分析仪ea与热重分析tga,确定催化剂dmc-1中各组分含量如下表:
[0043]
表1催化剂dmc-1组成表
[0044][0045]
由表1推断dmc-1的近似组成为mcm-41@zn
3
[co(cn)
6
]
2
·
zncl
2
·
0.70eaa
·
0.76h
2
o
·
0.03p123
·
0.0006la(no
3
)
3
。
[0046]
对比例1
[0047]
钴氰化锌zn
3
[co(cn)
6
]
2
·
12h
2
o的制备:
[0048]
zn
3
[co(cn)
6
]
2
·
12h
2
o是在不加任何有机配体、共络合剂、过渡金属盐的条件下合成的。制备步骤如下:将1g钴氰化钾溶于18ml水中制得溶液a。将3.3g氯化锌溶于5ml水中制得溶液b。将溶液a缓慢滴加至溶液b中生成白色沉淀,经过滤干燥磨碎得到zn
3
[co(cn)
6
]
2
·
12h
2
o。
[0049]
实施例2
[0050]
ppg-1000以上的大分子量聚丙二醇的合成:
[0051]
本实施例以mn为550的小分子量聚丙二醇为起始剂合成大分子量聚丙二醇,具体步骤如下:将上述实施例1中制备的催化剂dmc-1应用于催化大分子量聚丙二醇的合成反应中。在高压反应釜中合成聚丙二醇,控制高压釜的搅拌速度和温度。将6g mn为550的聚丙二醇起始剂和0.02g实施例1制得的催化剂dmc-1投入高压反应釜中,采用氮气进行多次置换后,向釜中加入30g环氧丙烷。控制转速350r/min,起始压力0.1mpa,反应6h后,脱除未反应单体,经过滤分离产品与催化剂,得到聚丙二醇产品。改变不同的反应温度对聚丙二醇产品性能的影响如表2所示。
[0052]
产品检测:对产品的羟值、醛值、转化率、ph值进行检测。在反应过程中记录催化剂诱导时间,当反应釜测温升至反应设定温度后开始计时,以出现“温升压降”或压力明显下降现象时计为诱导时间。通过邻苯二甲酸酐法测定产品的羟值。用2,4-二硝基苯肼进行柱前衍生,通过高效液相色谱法测定聚丙二醇中甲醛、乙醛、丙烯醛的含量。
[0053]
表2反应温度对产品性能的影响
[0054][0055]
实施例3
[0056]
ppg-1000以下的小分子量聚丙二醇的合成:
[0057]
本实施例以甘油为起始剂合成小分子量聚丙二醇,具体步骤如下:将上述实施例1中制备的催化剂dmc-1应用于小分子量聚丙二醇的合成反应中。具体步骤如下:在高压反应釜中合成聚丙二醇,控制高压釜的搅拌速度和温度。将5g甘油起始剂和0.06g实施例1制得的催化剂dmc-1投入高压反应釜中,采用氮气进行多次置换后,向釜中加入50g环氧丙烷。控制转速350r/min,起始压力0.5mpa,反应6h后,脱除未反应单体,经过滤分离产品与催化剂,得到聚丙二醇产品。改变不同的反应温度对聚丙二醇产品性能的影响如表3所示,产品检测方式与实施例3相同。
[0058]
表3反应温度对产品性能的影响
[0059][0060]
结合表2、表3的结果综合分析反应温度对于产品各项性能的影响。实验结果表明当温度低于100℃时,反应过慢,诱导期较长,随着反应温度的升高,诱导期平缓下降。聚丙
二醇产品中的醛类物质含量随着反应温度的增加而提高。过高的温度会使产品在合成过程中氧化或发生副反应生成醛类物质,环氧丙烷在高温下歧化反应速率明显加快,从而导致醛类物质的生成。随着温度的升高,聚合反应速率明显加快,聚丙二醇产品的分子量逐渐增大,单体转化率逐渐提高,但当温度高于130℃时,聚合反应热效应严重,反应釜难以及时移除反应热,导致副反应明显增多,从而使得单体转化率降低,产品分子量降低。综上所述,控制反应温度在120~130℃时,本发明提出的催化剂在催化合成聚丙二醇产品时具有极高的催化活性,诱导期可缩短至10min,所得聚丙二醇产品分子量分布较窄、醛值较低、色泽好,有利于聚丙二醇产品的下一步应用。
[0061]
实施例4
[0062]
基本步骤与实施例1相同,不同的是:有机配体l为乙酰乙酸甲酯;共络合剂p的分子量为8000;过渡金属盐s选用cr(no
3
)
3
·
9h
2
o;
[0063]
(1)将9
×
10-4
mol钴氰化钾溶于18ml水中制得溶液a。将9
×
10-3
mol氯化锌溶于4.5ml水中得到氯化锌水溶液,再称取相当于氯化锌水溶液质量0.5%的cr(no
3
)
3
·
9h
2
o和水体积一半的乙酰乙酸甲酯溶于氯化锌水溶液中制得溶液b。其中,钴氰化钾与氯化锌的摩尔比为1:10。将0.38g介孔分子筛mcm-41加入30ml水与乙酰乙酸甲酯混合液中,混合液中:水50%,乙酰乙酸甲酯50%;搅拌均匀制得溶液c。介孔分子筛载体mcm-41与氯化锌水溶液的质量比为1:15。
[0064]
(2)80℃的油浴条件下,将溶液a与溶液b缓慢同步滴加至2000r/min的溶液c中,滴加时间为20min。再向溶液中加入10ml的水与乙酰乙酸甲酯的混合液、0.57g共络合剂p,继续搅拌混合30min;其中,水与乙酰乙酸甲酯的混合液中:水30%,乙酰乙酸甲酯70%。
[0065]
(3)搅拌完成后,将所得浆料冷却后过滤分离得到滤饼,所得滤饼用乙酰乙酸甲酯与水组成的混合溶液化浆洗涤3次,逐渐提高混合溶液中乙酰乙酸甲酯的比例直至用纯乙酰乙酸甲酯化浆洗涤得到最终催化剂滤饼。将最终的滤饼在80℃下真空干燥至恒重,磨碎后得到本催化剂,命名为dmc-2。共络合剂p与氯化锌水溶液的质量比为1:10。
[0066]
实施例5
[0067]
基本步骤与实施例1相同,不同的是:有机配体l为丙二醇丁醚;共络合剂p的分子量为5000,通过市售获得;过渡金属盐s选用ce(no
3
)
3
·
6h
2
o;
[0068]
(1)将5.4
×
10-3
mol铁氰化钾溶于18ml水中制得溶液a。将2.16
×
10-2
mol硫酸锌溶于3.6ml水中得到硫酸锌水溶液,再称取相当于硫酸锌水溶液质量3%的ce(no
3
)
3
·
6h
2
o和水体积一半的丙二醇丁醚溶于硫酸锌水溶液中制得溶液b。其中,铁氰化钾与硫酸锌的摩尔比为1:4。将1.41g介孔分子筛mcm-41加入30ml水与丙二醇丁醚混合液中,混合液中:水75%,丙二醇丁醚25%;搅拌均匀制得溶液c。介孔分子筛载体mcm-41与硫酸锌水溶液的质量比为1:5。
[0069]
(2)80℃的油浴条件下,将溶液a与溶液b缓慢同步滴加至5000r/min的溶液c中,滴加时间为20min。再向溶液中加入10ml的水与丙二醇丁醚的混合液、2.36g共络合剂p,继续搅拌混合30min;其中,水与丙二醇丁醚的混合液中:水30%,丙二醇丁醚70%。
[0070]
(3)搅拌完成后,将所得浆料冷却后过滤分离得到滤饼,所得滤饼用丙二醇丁醚与水组成的混合溶液化浆洗涤3次,逐渐提高混合溶液中丙二醇丁醚的比例直至用纯丙二醇丁醚化浆洗涤得到最终催化剂滤饼。将最终的滤饼在70℃下真空干燥至恒重,磨碎后得到
本催化剂,命名为dmc-2。共络合剂p与硫酸锌水溶液的质量比为1:3。
[0071]
实施例6
[0072]
基本步骤与实施例2相同,不同的是:将6g起始剂聚丙二醇(mn=550)和0.0036g实施例1制得的催化剂dmc-1投入高压反应釜中,采用氮气进行多次置换后,向釜中加入30g环氧丙烷。控制转速250r/min,起始压力1mpa,温度100℃反应10h后,脱除未反应单体,经过滤分离产品与催化剂,得到聚丙二醇产品。
[0073]
实施例7
[0074]
基本步骤与实施例2相同,不同的是:将6g起始剂聚丙二醇(mn=550)和0.126g实施例1制得的催化剂dmc-1投入高压反应釜中,采用氮气进行多次置换后,向釜中加入120g环氧丙烷。控制转速550r/min,起始压力0.5mpa,温度140℃反应5h后,脱除未反应单体,经过滤分离产品与催化剂,得到聚丙二醇产品。
[0075]
附图1为实施例1制备催化剂dmc-1的sem图,其中图1(a)为局部sem图,图1(b)为整体sem图,可以看到载体与活性组分良好的结合在一起。载体mcm-41分子筛是呈团聚状生长在一起,晶粒大小较为均匀,排列紧凑,在分子筛上生长了多个花瓣状的双金属氰化物催化剂。
[0076]
附图2为对比例1制备的zn
3
[co(cn)
6
]
2
·
12h
2
o和实施例1中制备催化剂dmc-1的xrd谱图,表明制备的dmc-1催化剂为无定形态与单斜晶共存的状态,主要为无定形态且结晶度极低。分子筛载体mcm-41、有机配体l和共络合剂p123的加入抑制了催化剂晶体的形成,使得dmc晶体由立方晶体转向单斜晶体与无定型态共存的状态。这是因为,zn
2+
在与[co(cn)
6
]
3-结合的同时,也会与分子筛表面上阴离子反应而形成化学键,有机配体l与共络合剂p123会与zn
2+
进行配位,这种配位作用会破坏zn
3
[co(cn)
6
]
2
·
12h
2
o晶体的结构,从而抑制催化剂晶体的生长。此外,la(no
3
)
3
·
6h
2
o的加入在未改变催化剂结构的同时使得谱图明显宽化,结晶度变低。研究表明dmc结晶度越低,催化活性越高,故本发明制备的催化剂在合成聚丙二醇时具有极高的催化活性。
[0077]
附图3为对比例1制备的zn
3
[co(cn)
6
]
2
·
12h
2
o和实施例1中制备催化剂dmc-1的ftir谱图,由图中可知,zn
3
[co(cn)
6
]
2
·
12h
2
o中—cn的伸缩振动峰与co—cn键的吸收峰均发生了蓝移,说明了催化剂结构中zn
2+-cn-co
3+
结构的产生。所制备催化剂dmc-1的co—cn与—cn的出峰位置与zn
3
[co(cn)
6
]
2
·
12h
2
o不同,因此可以判断催化剂中不含有立方晶结构。这是由于制备过程中有机配体l和共络合剂p123的加入,使催化剂由立方晶形态转向由无定形结构和单斜晶形态共存的形式,这与xrd分析相照应。
[0078]
附图4为实施例1制备催化剂dmc-1的局部ftir谱图,表明有机配体乙酰乙酸乙酯成功的与zn
2+
配位,增加了催化剂中与zn
2+
配位的氧原子数,进而增加了活性中心数量,提高了催化活性。所添加的酮类配体乙酰乙酸乙酯具有互变异构现象,配体乙酰乙酸乙酯以酮形式存在的吸收峰在1724cm-1
,烯醇形式的吸收峰位置处在1629cm-1
。
[0079]
附图5为实施例2(b)与实施例3(c)制备的聚丙二醇样品与标准样品(a)的ftir图,表明所合成的聚丙二醇样品与标准样品是一致的。图中在3400cm-1
出现末端羟基(—oh)的伸缩振动特征吸收峰,2970cm-1
与2873cm-1
以为甲基(-ch
3
)的反对称和对称伸缩振动吸收峰,1458cm-1
与1375.1cm-1
为甲基(-ch
3
)的不对称变形振动和对称变形振动吸收峰。在1100cm-1
出现的强吸收峰为醚键(c-o-c)反对称伸缩振动特征吸收峰,在聚醚主链中此基团
重复次数多,吸收强度大,这是鉴定聚醚类化合物的特征吸收谱带。在945cm-1
出现的吸收峰为醚键的对称伸缩振动吸收峰。此外,图中在1647cm-1
处出现了一个较弱的吸收峰,说明所合成的样品含有一定的不饱和度。这是反应过程中发生的副反应引起的。不饱和双键的吸收峰强度相对较弱,说明双键的含量较低,表明制备的聚丙二醇样品不饱和度很低。
[0080]
附图6为实施例3制备的聚丙二醇样品的
1
hnmr图。可以将图中的各峰分为两个区域,第一个区域(i区)为δ1.05-1.07处,第二个区域(ii区)为δ2.8-3.9处。i区为环氧丙烷链段上甲基质子的吸收峰,甲基与次甲基相连使得峰裂分为双峰。ii区则为聚醚多元醇分子中其余质子的吸收峰,包括环氧丙烷链段上亚甲基、次甲基中的氢核,端基甘油链段上亚甲基、次甲基中的氢核以及末端羟基中的氢核。
起点商标作为专业知识产权交易平台,可以帮助大家解决很多问题,如果大家想要了解更多知产交易信息请点击 【在线咨询】或添加微信 【19522093243】与客服一对一沟通,为大家解决相关问题。
此文章来源于网络,如有侵权,请联系删除



tips