塔内反应精馏与膜耦合的方法与装置与流程



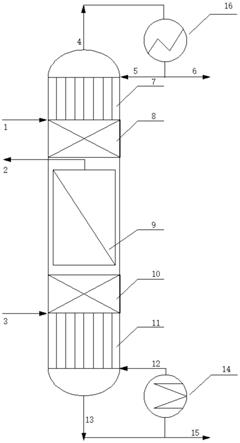
[0001]
本发明属于化工生产工艺及设备技术领域,涉及一种可用于受限于平衡或形成共沸的有机反应,如部分酯化反应及水解反应的塔内反应精馏与膜耦合的工艺方法及装置。
背景技术:
[0002]
在化工生产过程中,精馏是常用的传统分离手段,其原理是根据混合物中各组分的沸点不同达到分离的目的;反应精馏是近年来十分热门的新兴技术,其原理在于将可逆反应过程与精馏相结合,在反应的同时利用精馏不断的分离产物和反应物,从而推动反应正向进行,提高转化率。
[0003]
然而,常规的精馏手段在处理共沸体系时效果很差,需要很高的能耗才能勉强分离,因此,如果可逆反应的产物与反应物之间存在共沸,精馏往往不能很好的分离产物,反应精馏的优势也就大打折扣;此外,其在处理严重受限于反应平衡的有机反应体系(例如精细化工领域)时效果也不理想。相比较而言,膜分离技术在这些领域更有优势。正因如此,近年来涌现了很多将膜分离和精馏,甚至反应精馏相结合的工艺。
[0004]
膜以及其支撑结构一同构成了膜组件,膜的材质有分子筛膜、无定形二氧化硅膜、壳聚糖膜、pva膜或海藻酸钠膜,膜组件按照膜的形式或排列方式可以归类为管式、中空纤维式、板框式或螺旋卷式等,按照分离气相体系或者液相体系又可以分为蒸汽渗透膜组件或者渗透汽化膜组件,单个膜组件或多个相同形式或不同形式的膜组件以串联、并联、混联等方式组成的集合可以统称为膜分离簇,或称为膜分离段,或者膜分离机组、膜分离装置等。
[0005]
膜分离与精馏或者反应精馏相结合的具体实施方式实则为合适的膜组件或者多个膜组件形成的膜分离段与精馏塔或反应精馏塔以一定的方式构成的连接,文章中通常将组件二字省去或者不指名具体形式的膜组件,是因为膜组件的形式有多种,指定一种特定的膜组件会限制专利的应用范围,本专利适用于多种种类的膜以及不同形式的膜组件。
[0006]
cn110078598a公开了一种多段反应精馏合成工艺装置,工艺装置包括多段反应精馏塔和蒸汽渗透膜组件,但其蒸汽渗透组件是安装在塔外冷凝器之前,并不能及时在反应之后脱水以推动反应正向进行。cn109776314a公开了一种酯的制备方法,在包含渗透汽化装置和精馏塔的反应精馏设备中酯化体系在二元催化剂作用下发生酯化反应。其中渗透汽化膜组件被安装在塔外,用于进一步脱水,同样未能有效推动反应正向进行。cn202289520u公开了一种含有催化与渗透汽化膜组件的精馏耦合过程,将催化剂负载在了膜的表面,让膜兼具分离和催化的作用,也能在反应过程中脱水。但其仍存在以下缺陷:首先,其对反应精馏塔的设计过于粗陋,在反应精馏塔中,反应并不发生在全塔,而是主要发生在反应段中,其将膜管分布在全塔实际上是一种浪费;其次,其可行性存在很大问题,目前为止还很少有能负载催化剂又同时具有很好分离效果的膜,并且在反应精馏塔中高密度的装载膜管很容易造成液泛,而塔内的流体流动也容易损坏膜;最后,其成本会非常高,很难放大,像这种结构,会需要消耗大量的膜,成本极高。目前大部分工艺中,膜组件基本都耦合在反应精
馏塔之外,大部分只是通过膜组件分离共沸物,并不能充分发挥反应精馏塔的优势,偶有侧线采出膜分离后回流的,也由于采出量无法规定而缺乏实际价值。
技术实现要素:
[0007]
根据现有技术的不足,本发明提出一种将膜组件有效耦合于反应精馏塔内,在反应的同时不断脱除产物以打破原有化学平衡,推动反应正向进行的方法和装置。
[0008]
本发明建立一套将膜组件耦合于反应精馏塔内反应段,通过膜分离及时脱除反应产生的产物,包括传统精馏难以分离的共沸产物,以打破化学平衡,推动反应不断正向进行的设备。
[0009]
具体而言,原料由进料口进入塔内,塔内气相经过提馏段之后进入反应段发生反应,再经过膜分离段脱除目标组分,由此促进反应的正向进行,而后再经由反应段继续反应,反应-分离的不断循环进行有效地提高了原料的转化率,最后通过精馏段冷凝器部分回流,部分成为塔顶产物;液相则是直接依次通过精馏段,反应段和提馏段,部分成为塔底产物,部分通过再沸器气化回流。
[0010]
本发明为提高受限于平衡或形成共沸的如部分酯化反应与水解反应等有机反应的反应精馏转化率开辟了新的方法。
[0011]
本发明的技术方案如下:
[0012]
一种塔内反应精馏与膜耦合的方法,将膜组件耦合于反应精馏塔内反应段,通过膜分离及时脱除反应产生的产物,推动反应不断正向进行的方法;原料由进料口进入塔内,塔内气相经过提馏段之后进入反应段发生反应,再经过膜分离段脱除目标组分,由此促进反应的正向进行,而后再经由反应段继续反应,通过精馏段冷凝器部分回流,部分成为塔顶产物;液相直接一次通过精馏段、反应段、膜分离段和提馏段,部分成为塔底产物,部分通过再沸器汽化回流。
[0013]
本发明在于位于膜分离段的膜组件被固定于反应精馏塔内部,由于膜组件的膜区域是裸露于反应精馏塔内的,因此膜组件的滞留侧为反应精馏塔的塔内,渗透侧为膜组件内部,渗透侧为负压操作,压力范围为100-600pa,传质推动力为膜组件内外的压力差,目标组分从分离物采出口(2)采出。
[0014]
本发明多个原料分开进料时进料的位置应依据原料组分的轻重而定,重组分反应精馏塔上方进料口进料,轻组分反应精馏塔下方进料口进料。
[0015]
本发明的提出的一种塔内反应精馏与膜耦合的装置,包括反应精馏塔由上至下分别有精馏段(7)、上反应段(8)、膜分离段(9)、下反应段(10)、提馏段(11);以及塔顶冷凝器(16)、塔底再沸器(14)、塔顶气相采出口(4)、塔顶冷凝器液相返塔管(5)、塔顶冷凝器采出管(6)、塔底液相采出口(13)、塔底再沸器液相采出管(15)、塔底再沸器气相返塔管(12);其特征在于塔顶气相采出口(4)与冷凝器(16)通过管线连接,塔顶冷凝器出口通过塔顶冷凝器液相返塔管(5)与塔顶连接;塔底液相采出口(13)与塔底再沸器(14)连接,塔底再沸器出口通过塔底再沸器气相采出管(12)与反应精馏塔塔底相连接,单个膜组件或多个相同形式或不同形式的膜组件组成了膜分离段,安装并固定于反应精馏塔的反应段之间;反应精馏塔上设置进料口,在膜分离段上面设置分离物采出口(2)。
[0016]
所述反应精馏塔上应设置一个或多个进料口,一个进料口时应设置在反应精馏塔
的上部,原料应混合进料;两个进料口时应设置为上进料口(1)、下进料口(3),原料分开进料或混合进料;多个进料口时则应在塔的径向均匀设置,并由上至下均匀归类为上进料口(1)、中进料口(40)、下进料口(3),原料分开进料或混合进料。
[0017]
所述的膜的材质有分子筛膜、无定形二氧化硅膜、壳聚糖膜、pva膜或海藻酸钠膜,膜组件按照膜的形式或排列方式可以归类为管式、中空纤维式、板框式或螺旋卷式等,按照分离气相体系或者液相体系又可以分为蒸汽渗透膜组件或者渗透汽化膜组件,单个膜组件或多个相同形式或不同形式的膜组件以串联、并联、混联等方式组成的集合可以统称为膜分离簇,或称为膜分离段,或者膜分离机组、膜分离装置等。;若为蒸汽渗透膜组件,则需要在膜分离段安装侧边液相导流装置;用于塔内反应精馏的膜组件的特征主要在于起分离作用的膜区域裸露在气相反应体系中,达到反应体系直接接触的效果。
[0018]
所述的膜分离段位于反应段之间,膜分离段中的膜组件的数量为1个到100个,多个膜组件以串联、并联或混联方式安装于塔内的反应段之间,膜组件所形成的膜分离段的最大外圈直径应小于或等于反应精馏塔的内径,否则应对该反应精馏塔节做变径处理,膜组件所形成的的膜分离段的最大垂直长度应小于反应精馏塔的长度。
[0019]
本发明反应体系为受限于平衡或形成共沸的有机反应,如部分酯化反应及水解反应,不同的反应体系需要相应的膜组件,如酯化反应可选择具有脱水作用的分子筛膜。
[0020]
本发明反应精馏塔的工作压力优选为绝压1atm,也可加压操作。
[0021]
本发明将蒸汽渗透膜组件安装在反应精馏塔反应段,从而不断分离反应生成的产物以打破原本的平衡,提高转化率。传统的反应精馏虽然同样反应与分离同时进行,提高了反应转化率,然而,许多重要的化工体系存在着共沸、浓度夹点、相对挥发度等问题,在反应精馏过程中难以达到很高的转化率,产物不能有效分离。例如,常见的有机溶剂如乙醇、异丙醇、乙二醇醚等会与水形成共沸物,在普通的反应精馏过程中,一方面无法有效地破坏分离共沸物,另一方面共沸物的存在始终抑制着反应的进行,因而无法得到高纯度的产品。反应精馏与膜的塔外耦合虽然在一定程度上解决了这些问题,但是,反应精馏与膜分离过程的分开进行并不能及时的解决共沸等问题,反应精馏过程中仍然存在着平衡限制的因素,因而不能根本上提高反应的转化率。因此,我们提出了塔内反应精馏与膜的耦合,将反应精馏与膜分离放置于同一空间进行,可以在共沸发生的同时将其打破并原位移除,从根源上解决限制反应的因素,从而有效地提高了反应的转化率。
[0022]
使用本方法提供的该工艺及装置具有工艺流程简单、设备投资较低、反应物转化率高、能耗较低、能一步处理共沸体系等优点。
[0023]
本发明的方法及装置具有以下优点:
[0024]
1.由于膜组件分离共沸组分相比于精馏具有天然优势,故本装置相较于传统反应精馏更加节能,成本更低。
[0025]
2.将膜组件耦合在两反应段之间,能及时脱去产生的共沸组分,打破原有平衡,有效推动反应正向进行,显著提升转化率。
[0026]
3.目前设计的是膜组件作为塔节安装,拆装便捷灵活。
[0027]
4.可选用的膜组件很多,基本所有满足条件的体系都有合适的膜组件可用,适用范围非常广。
附图说明
[0028]
图1为塔内反应精馏膜耦合装置主视图。
[0029]
图2-a为所设计的管式膜组件示意图,图2-b为管式膜组件的膜管排布方式示意图。
[0030]
图3-a为所设计的中空纤维式膜组件示意图,图3-b为中空纤维式膜元件示意图,图3-c为中空纤维式膜元件仰视图。
[0031]
图4-a为所设计的弓形折流板配合中空纤维式膜组件安装于反应精馏塔的示意图,图4-b为所设计的弓形折流板示意图。
[0032]
图5-a为所设计的外孔形折流板与内孔形折流板配合中空纤维式膜组件安装于反应精馏塔的示意图,图5-b为所设计的外孔形折流板示意图,图5-c为所设计的內孔形折流板示意图。
[0033]
图6-a为两个膜分离段分布在反应精馏塔的反应段之间的装置示意图,图6-b为49个膜分离段分布在反应精馏塔的反应段之间的装置示意图。
[0034]
图7-a为49个膜组件以串联方式安装于反应精馏塔中示意图,图7-b为49个膜组件以并联方式安装于反应精馏塔中示意图,图7-c为49个膜组件以混联方式安装于反应精馏塔中示意图。
[0035]
图8-a为安装有侧边液相导流装置的塔内反应精馏与膜耦合装置示意图,图8-b为塔内液相导流装置俯视图。
[0036]
图9为由于膜分离段外径过大而对反应精馏塔的膜分离段的塔节做变径处理的示意图。
[0037]
其中,1、上进料口;2、分离物采出口;3、下进料口;4、塔顶气相采出口;5、塔顶冷凝器液相返塔管;6、塔顶冷凝器采出管;7、精馏段;8、上反应段;9、膜分离段;10、下反应段;11、提馏段;12、塔底再沸器气相返塔管;13、塔底液相采出口;14、塔底再沸器;15、塔底再沸器液相采出管;16、塔顶冷凝器;17、膜管上部封头;18、膜管;19、膜管下部封头;20、膜组件中心待装填料区;21、膜管底部开口;22、真空室;23、多孔盖板;24、基座;25、膜管顶部开孔;26、弓形折流板;27、弓形折流板开孔;28、反应精馏塔塔壁;29、外孔形折流板;30、內孔形折流板;31、外大孔;32、内小孔;33、内大孔;34、外小孔;35、上膜分离段;36、下膜分离段;37、中反应段;38、上分离物采出口;39、下分离物采出口;40、中进料口;41、侧边液相导流口;42、密封板;43、溢流堰;44、通风板;45、变径后的塔节;46、真空封头;47、环形底座;48、o型圈。
具体实施方式
[0038]
下面通过具体实施方式对本发明作进一步详细说明。但本领域技术人员将会理解,下列实施例仅用于说明本发明,而不应视为限定本发明的范围。实施例中未注明具体技术或条件者,按照本领域内的文献所描述的技术或条件或者按照产品说明书进行。
[0039]
在本说明书中所述及到的实施方式,指的是结合该实施例描述的具体特征、结构或者包括在本申请概括性描述的至少一个实施例中。在说明书中多个地方出现同种表述不是一定指的是同一个实施例。进一步来说,结合任一实施例描述一个具体特征、结构或者特点时,所要主张的是结合其他实施例来实现这种特征、结构或者特点也落在本申请所要保
护的范围内。
[0040]
本装置的膜分离段所使用的的膜组件可以有管式、中空纤维式、板框式或者螺旋卷式,膜材质选自分子筛膜、无定形二氧化硅膜、壳聚糖膜、pva膜或海藻酸钠膜。
[0041]
本专利分别为管式、中空纤维式设计了膜组件:
[0042]
管式膜组件包括分离物采出口(2)、膜管上部封头(17)、膜管(18)、膜管下部封头(19)、膜组件中心待装填料区(20)、膜管底部开口(21);膜管下部封头(19)与开口的膜管底部连接,膜管上部封头(17)与密闭的膜管顶部连接,分离物采出口(2)与膜管下部封头(19)通过管线连接;膜组件中心的柱形空白区域(20)可以加装填料催化剂等,下部封头(19)为环形圆柱体空腔,膜管底部与环形圆柱体空腔相通,膜管顶部密封,目标组分在传质推动力的作用下由膜管(18)渗透进入空腔区,由分离物采出口(2)抽至塔外。该组件的特点在于反应与分离几乎同时并且原位发生,是一种较为理想的管式膜组件。
[0043]
中空纤维式膜组件包括分离物采出口(2)、真空封头(46)、环形底座(47)、o型圈(48)、真空室(22)、多孔盖板(23)、基座(24)以及膜管顶部开口(25);其特征在于内置的中空纤维膜元件通过o型圈(48)与真空封头(46)与环形底座(47)密封,分离物采出口(2)与真空室(22)相连,膜管顶部开口与多孔盖板(23)连接,膜管底部密封与基座(24)连接;
[0044]
当膜组件或膜组件形成的膜分离段的外径小于反应精馏塔的内径时,应在膜组件与反应精馏塔内壁之间安装折流板,本专利使用了用于可中空纤维膜组件的弓形折流板以及内外孔形折流板。弓形折流板如图4-b所示,所设计的弓形折流板为弓形圆片,中间有许多供膜管穿过的孔洞(27),孔径大小与膜管相同或者略大,以如图4-a所示方式配合膜组件固定于反应精馏塔上,折流板应在膜管径向位置均匀设置,数量大于1个,该折流板可引导塔内气体多次穿过膜管,增加气体与膜管外壁的接触时间,从而有效提高分离效率。孔形折流板如图5-b、5-c所示,包括外孔形折流板与內孔形折流板,其特征在于所设计的外孔形折流板为外圈大孔通气,内圈小孔通膜管的圆片,內孔形折流板为外圈小孔通膜管,内圈大孔通气的圆片,大孔孔径大于膜管孔径,塔内气体可通过此孔,小孔孔径等于或略大于膜管直径,气体难以通过该孔,因此当气体依次通过外孔形折流板、內孔形折流板时,会多次穿过膜管,增加了气体与膜管外壁的接触时间,从而有效的提高了分离效率,同样,两种样式的折流板应在膜管径向位置均匀并且交替设置,数量大于2个。
[0045]
本装置所采用的膜分离段的数量可以有多个,并且膜分离段中的膜组件的数量以及膜组件相互之间的连接方式可以有多种,本专利使用了多个膜分离段在塔内反应段之间均匀分布的形式,如图6-a、6-b所示,其特征在于它含有多个膜分离段,膜分离段都位于两个反应段中间,其中6-b有着49个膜分离段,50个反应段,50个进料口,上反应段包括由上至下的1-20号反应段,中反应段包括由上至下的21-30号反应段,下反应段包括由上至下的31-50号反应段,同理,上进料口包括由上至下的1-20号进料口,中进料口包括由上至下的21-30号进料口,下进料口包括由上至下的31-50号进料口,49个膜分离段夹在50个反应段之间。多个膜分离段的引入可层层脱除目标组分,多个膜分离段与反应段的交叉更进一步的促进了反应的进行,提高了反应的转化率。本专利使用了多个膜组件以不同的连接方式组成膜分离段的形式,如图7-a、7-b、7-c所示,分别为多个膜组件的串联、并联、混联示意图,多个膜组件的串联使分离出的目标组分的纯度得到提高,有利于对其进一步的回收利用,多个膜组件的并联提高了膜分离段的总膜面积,弥补了单个膜组件的分离面积不足的
缺点,多个膜组件的混联则可以在一定的情形下,兼顾两者优势。
[0046]
本装置对膜分离段的液相进行了不同的处理方法,若膜分离段所用膜的性质为渗透蒸发膜,则可以让液相直接通过膜分离段,若膜分离段所用膜的性质为蒸汽渗透膜,则需要将液相进行导流,本专利所设计的一种液相导流装置如图8-a所示,在溢流堰(43)有一定高度以引导液相通过侧边液相导流口(41)流入下方的反应段中,通风板(44)为一斜面,它阻隔了由上至下的液相,同时,由下至上的气相可以通过,密封板(42)则与反应精馏塔塔壁紧密贴合。
[0047]
本装置对由于膜组件外圈直径大于反应精馏塔内径的情况设计了一种如图9所示的变径处理,变径处理可以有效地解决现有的膜组件与反应精馏塔尺寸不匹配的问题,在实际的工业生产中可以有效地节约设备成本。
[0048]
塔内反应精馏与膜耦合是通过如下技术方案实现的:原料由进料点进入塔内,塔内气相经过提馏段之后进入反应段发生反应,再经过膜组件脱除目标组分,由此促进反应的正向进行,而后再经由反应段继续反应,反应-分离的不断循环进行有效地提高了原料的转化率,最后通过精馏段以及冷凝器部分回流,部分成为塔顶产物;液相则是直接依次通过精馏段,反应段和提馏段,部分成为塔底产物,部分通过再沸器气化回流。
[0049]
将实施例结合上述具体反应精馏装置与膜组件形式说明(上述设计的类型都应当在对应实施例中有体现,实施例用到了图1)
[0050]
实施例1:选用乙醇和乙酸合成乙酸乙酯体系,体系内存在乙醇水共沸,故选用脱水中空纤维膜,所用装置为图1所示的反应精馏装置,包括上进料口(1)、分离物采出口(2)、下进料口(3)、塔顶气相采出口(4)、塔顶冷凝器液相返塔管(5)、塔顶冷凝器采出管(6)、精馏段(7)、上反应段(8)、膜分离段(9)、下反应段(10)、提馏段(11)、塔底再沸器气相返塔管(12)、塔底液相采出口(13)、塔底再沸器(14)、塔底再沸器液相采出管(15)、塔顶冷凝器(16),具体操作条件如下:全塔压力3bar,膜内压力300pa,全塔温度250℃,进料乙醇纯度99.9wt%,摩尔流率30kmol/h,乙酸纯度99.99wt%,摩尔流率30kmol/h,回流比(摩尔比)1.6,再沸器热负荷260kw,选用板式塔,共35块板,其中提馏段5块板,精馏段5块板,反应段25块板,催化剂选择硫酸固体酸催化剂,膜组件选用图3-a的中空纤维式膜组件,内装填3-b所示的中空纤维式膜元件,安装在第15到16块板之间,折流板选用图4-b所示的弓形折流板,采用图4-a所示的方法安装于反应精馏塔内。乙醇转化率和膜面积关系如下:
[0051][0052]
实施例2:选用乳酸甲酯水解产乳酸的体系,该体系在如下的操作条件原本无法达到比较高的转化率,而通过加膜可以打破原有的平衡。选用图1所示的反应精馏装置,包括上进料口(1)、分离物采出口(2)、下进料口(3)、塔顶气相采出口(4)、塔顶冷凝器液相返塔
管(5)、塔顶冷凝器采出管(6)、精馏段(7)、上反应段(8)、膜分离段(9)、下反应段(10)、提馏段(11)、塔底再沸器气相返塔管(12)、塔底液相采出口(13)、塔底再沸器(14)、塔底再沸器液相采出管(15)、塔顶冷凝器(16),具体操作条件如下:全塔压力2.5bar,膜内压力300pa,全塔温度320℃,混合进料中各组分质量分数:乳酸甲酯8.5%、乳酸25.0%、甲醇4.9%、水61.6%,摩尔流率60kmol/h,回流比(摩尔比)1.8,再沸器热负荷345kw,选用填料塔,催化剂选择离子交换树脂催化剂,膜组件选用图3-a的中空纤维式膜组件,安装在反应段正中间,折流板采用图5-b所示的外孔形折流板以及图5-c所示的內孔形折流板交错排列,采用图5-a所示的方式安装于反应精馏塔内。乙醇转化率和膜面积关系如下:
[0053][0054]
实施例3:选用甲酸与无水乙醇反应生成乳酸乙酯的体系,甲醇进料为412g/h,乙醇进料为579g/h,所用装置为图7-c所示的49个单管naa分子筛膜组件混联,或者选用图7-a所示的膜组件串联,或者选用图7-b所示的膜组件并联。该装置包括上进料口(1)、分离物采出口(2)、下进料口(3)、塔顶气相采出口(4)、塔顶冷凝器液相返塔管(5)、塔顶冷凝器采出管(6)、精馏段(7)、上反应段(8)、膜分离段(9)、下反应段(10)、提馏段(11)、塔底再沸器气相返塔管(12)、塔底液相采出管(13)、塔底再沸器(14)、塔底再沸器液相采出管(15)、塔顶冷凝器(16),膜面积为0.046m
2
,并且采用图8-a中的液相导流装置以防止液相对膜性能的影响,反应精馏塔高度为4m、塔径100mm,填充有4mm*4mm的θ环填料,膜分离段(9)高度为250mm,上反应段(8)高度为0.9m,下反应段(10)高度为0.85m,精馏段(7)与提馏段(11)各1m,塔釜温度为82℃,所用催化剂为强酸性离子交换树脂krd001,膜组件的渗透侧的压力控制在300pa,反应精馏塔为常压,待进出料质量、温度、塔釜塔顶组成稳定好停止实验,通过气相色谱检验产品中甲酸乙酯的含量,计算收率为98.7%。
[0055]
实施例4:选用己酸与无水乙醇反应生成己酸乙酯的体系,己酸进料为464g/h,乙醇进料为460g/h,所用装置为图6-b所示的49个膜分离段分布在反应段之间的反应精馏装置,或者选用图6-a所示的包含两个膜分离段的反应精馏装置。该装置包括塔顶气相采出口(4)、塔顶冷凝器液相返塔管(5)、塔顶冷凝器采出管(6)、精馏段(7)、提馏段(11)、塔底再沸器气相返塔管(12)、塔底液相采出口(13)、塔底再沸器(14)、塔底再沸器液相采出管(15)、塔顶冷凝器(16)以及50个反应段、50个进料口以及49个膜分离段,49个膜分离段皆由一个长度100mm、最大外径120mm的柱形膜组件构成,柱形膜组件所用折流板为图4-b中的弓形折流板,所用膜为t形分子筛膜管,总膜面积为0.126m
2
,反应精馏塔高7m,精馏段(7)与提馏段(11)各0.5m,反应段总高度为1.1m,所填装催化剂为amberlyst 15树脂催化剂,塔内径为100mm,膜分离段如图9做136mm的变径处理,填充有3mm*0.5mm规格的弹簧填料,采用图8-a所示的液相导流装置消除液相干扰,膜组件的渗透侧压力控制在267pa,反应精馏塔压力为
1.5bar,待进出料质量、温度、塔釜塔顶组成稳定好停止实验,通过气相色谱检验产品中己酸乙酯的含量,计算收率为93.3%。
[0056]
实施例5:选用乳酸(含水约20%)与无水乙醇反应生成乳酸乙酯的体系,乳酸进料为90g/h,乙醇进料为138g/h,所用装置为图1所示的反应精馏装置,包括上进料口(1)、分离物采出口(2)、下进料口(3)、塔顶气相采出口(4)、塔顶冷凝器液相返塔管(5)、塔顶冷凝器采出管(6)、精馏段(7)、上反应段(8)、膜分离段(9)、下反应段(10)、提馏段(11)、塔底再沸器气相返塔管(12)、塔底液相采出口(13)、塔底再沸器(14)、塔底再沸器液相采出管(15)、塔顶冷凝器(16),膜分离段为一个如图2-a所示的管式膜组件,包括膜管上部封头(17)、膜管(18)、膜管下部封头(19)、膜组件中心待装填料区(20)、膜管顶部开口(21),膜管为naa分子筛膜,反应精馏塔高度为2m、塔径50mm,填充有4mm*4mm的θ环填料,膜分离段(9)高度为250mm,上反应段(8)高度为0.5m,下反应段(10)高度为0.25m,精馏段(7)与提馏段(11)各0.5m,塔釜温度为120℃,所用催化剂为强酸性离子交换树脂krd001,膜组件的渗透侧的压力控制在300pa,反应精馏塔为常压,不采用液相导流装置,环形圆柱体中心处(20)填装θ环,待进出料质量、温度、塔釜塔顶组成稳定好停止实验,通过气相色谱检验产品中乳酸乙酯的含量,计算纯度为79%,收率为78.7%。
[0057]
本发明公开和提出的技术方案,本领域技术人员可通过借鉴本文内容,适当改变条件路线等环节实现,尽管本发明的方法和制备技术已通过较佳实施例子进行了描述,相关技术人员明显能在不脱离本发明内容、精神和范围内对本文所述的方法和技术路线进行改动或重新组合,来实现最终的制备技术。特别需要指出的是,所有相类似的替换和改动对本领域技术人员来说是显而易见的,他们都被视为包括在本发明精神、范围和内容中。
起点商标作为专业知识产权交易平台,可以帮助大家解决很多问题,如果大家想要了解更多知产交易信息请点击 【在线咨询】或添加微信 【19522093243】与客服一对一沟通,为大家解决相关问题。
此文章来源于网络,如有侵权,请联系删除



tips