一种超高压射流研磨装置及熔喷模微孔抛光用研磨系统的制作方法



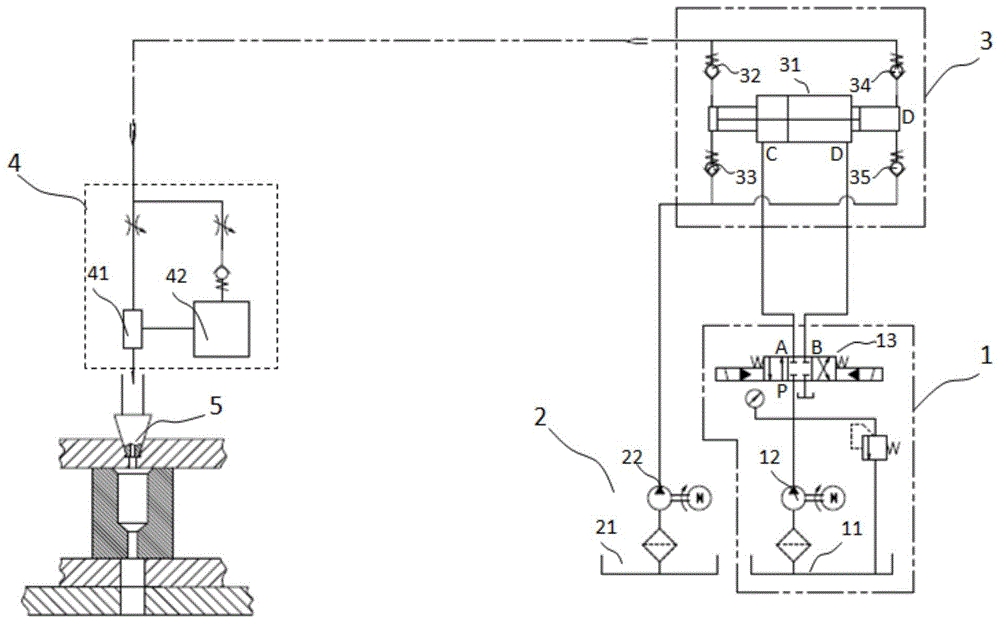
本实用新型涉及液压设备制造领域,特别涉及一种超高压射流研磨装置及熔喷模微孔抛光用研磨系统。
背景技术:
通过熔喷模具成型无纺网在本领域内众所周知。熔喷模具内形成有物料挤压腔,熔融的热塑性聚合物材料被压入至挤压腔内,并经挤压腔端部的微孔喷出以形成线状或丝状体。线状或丝状体被高速热气流加热并吹至滚筒等凝聚面上,从而形成随机分散的熔喷纤维的无纺布。
熔喷模具的微孔加工质量直接决定了无纺布的成型质量。熔喷模具锻造过程中,在完成微孔钻孔成型后,需要对微孔进行抛光以去除孔壁上的毛刺。现有技术中,一般采用射流研磨装置对微孔进行抛光处理,即射流研磨装置将研磨料喷入至熔喷模具的微孔内,高速研磨料经过微孔时研磨微孔孔壁从而实现对微孔的抛光处理。传统的射流研磨装置的增压性能较差,导致研磨料的喷出速度过低,最终导致微孔的抛光效果不佳。
技术实现要素:
为解决上述技术问题,本实用新型第一方面提供了一种超高压射流研磨装置,其技术方案如下:
一种超高压射流研磨装置,包括液压油供油部、射流液供液部、增压部、混合部及磨料喷射部、其中:
所述液压油供油部包括油箱、第一液压泵及电磁换向阀,所述电磁换向阀的进油口经管路连接至所述油箱,所述第一液压泵连接在所述油箱和所述电磁换向阀之间的管路上;
所述增压部包括双出杆驱动油缸、第一单向阀、第二单向阀、第三单向阀、第四单向阀,其中:所述双出杆驱动油缸包括左侧增压缸、左侧油缸、右侧油缸及右侧增压缸,所述第一单向阀的进液端连接所述左侧增压缸的出液口,所述第二单向阀的出液端连接所述左侧增压缸的进液口,所述第三单向阀的进液端连接所述右侧增压缸的出液口,所述第四单向阀出液端连接所述右侧增压缸的进液口,所述左侧油缸的工作油口经管路连接至所述电磁换向阀的一个工作油口,所述右侧油缸的工作油口经管路连接至所述电磁换向阀的的另一个工作油口;
所述供液部经管路分别连接所述第二单向阀和所述第四单向阀的进液端;
所述混合部包括混合腔和磨料供料腔,其中:所述混合腔包括混合腔进液口、混合腔出液口和磨料进料口,所述混合腔进液口经管路分别连接所述第一单向阀和所述第三单向阀的出液端,所述磨料供料腔的出料口与所述磨料进料口连通;
所述磨料喷射部连接在所述混合腔出液口处。
在一些实施例中,所述磨料供料腔经管路分别连接所述第一单向阀和所述第三单向阀的出液端。
在一些实施例中,所述混合腔和所述磨料供料腔为一体式结构,所述磨料供料腔的顶部敞开。
在一些实施例中,所述混合腔的混合腔进液口处设置有进液喷嘴,所述进液喷嘴经管路分别连接所述第一单向阀和所述第三单向阀的出液端。
在一些实施例中,所述供液部包括储液箱及第二液压泵,所述第二液压泵的进口经管路连接储液箱,所述第二液压泵的出口经管路分别连接所述第二单向阀和所述第四单向阀的进液端。
在一些实施例中,所述磨料喷射部为高压喷嘴。
在一些实施例中,所述电磁换向阀为三位四通换向阀。
本实用新型第一方面提供的超高压射流研磨装置,其核心增压部件为双出杆驱动油缸和电磁换向阀,通过双出杆驱动油缸与电磁换向阀的配合,本实用新型能够实现对研磨液的连续超高压射流果,最终提升了熔喷模微孔的研磨效率及研磨速度。
本实用新型第二方面提供了一种熔喷模微孔抛光用研磨系统,其包括本实用新型第一方面任一项所提供的超高压射流研磨装置及熔喷模夹具,其中:所述熔喷模夹具被配置为夹持待研磨抛光的熔喷模;所述超高压射流研磨装置的磨料喷射部的喷射口朝向所述熔喷模夹具。
通过超高压射流研磨装置和熔喷模夹具的配合,本实用新型第二方面提供的熔喷模微孔抛光用超高压射流研磨系统能够实现对熔喷模微孔的研磨抛光,并提升了抛光效果。
附图说明
为了更清楚地说明本实用新型实施例的技术方案,下面将对实施例描述中所述需要使用的附图进行简单描述,显而易见地,下面描述中的附图仅为本实用新型的一些实施例,对于本领域普通技术人员来讲,在不付出创造性劳动的前提下,还可以根据这些附图获得其他的附图。其中:
图1为本实用新型第一实施例提供的超高压射流研磨装置的结构示意图;
图2为图1中的双出杆驱动油缸的结构示意图;
图3为本实用新型第二实施例提供的超高压射流研磨装置的结构示意图。
具体实施方式
为使本实用新型的上述目的、特征和优点能够更加明显易懂,下面结合附图和具体实施方式对本实用新型作进一步详细的说明。
鉴于现有的射流研磨装置增压性能较差,研磨料的喷出速度过低的技术问题。本实用新型首先提供了一种超高压射流研磨装置,其能够实现对研磨液的连续增压以提升增压效果,最终提升了研磨料的喷出速度。下文将用两个实施例对本实用新型的超高压射流研磨装置的具体结构及工作原理进行适应性描述。
实施例1
如图1至图2所述,本实施例中的超高压射流研磨装置包括液压油供油部1、射流液供液部2、增压部3、混合部4及磨料喷射部5。其中:
液压油供油部1包括油箱11、第一液压泵12及电磁换向阀13,电磁换向阀13的进油口p经管路连接至油箱11,第一液压泵12连接在油箱11和电磁换向阀13之间的管路上。第一液压泵12启动后,油箱11内的油在第一液压泵12的驱动下流向电磁换向阀13的进油口p。
增压部3包括双出杆驱动油缸31、第一单向阀32、第二单向阀33、第三单向阀34、第四单向阀35。其中:双出杆驱动油缸31内设置一活塞杆及连接在活塞杆上的左端活塞、中间活塞和右端活塞,三个活塞将双出杆驱动油缸31的内腔分隔为左侧增压缸311、左侧油缸312、右侧油缸313及右侧增压缸314。第一单向阀32的进液端连接左侧增压缸311的出液口,第二单向阀33的出液端连接左侧增压缸311的进液口,第三单向阀34的进液端连接右侧增压缸314的出液口,第四单向阀35出液端连接右侧增压缸314的进液口,左侧油缸312的工作油口c经管路连接至电磁换向阀13的一个工作油口a,右侧油缸313的工作油口d经管路连接至电磁换向阀13的另一个工作油口b。
供液部2经管路分别连接第二单向阀33和第四单向阀35的进液端。供液部2内存储的研磨液(水、油或乳化液等)能够分别经第二单向阀33、第四单向阀35进入至左侧增压缸311、右侧增压缸314内。通过双出杆驱动油缸31与电磁换向阀13的配合,双出杆驱动油缸31能够实现对研磨液的连续增压。
混合部4包括混合腔41和磨料供料腔42,其中:混合腔41包括混合腔进液口、混合腔出液口和磨料进料口,混合腔进液口经管路分别连接第一单向阀32和第三单向阀34的出液端,磨料供料腔42的出料口与磨料进料口连通。经增压部3增压后的研磨液经第一单向阀32或第三单向阀34进入至混合腔,磨料供料腔42内的颗粒状磨料同时进入混合腔,研磨液和磨料在高压混合腔内混合从而形成固液均匀的研磨料。
磨料喷射部5连接在混合腔出液口处,混合均匀的研磨料以射流的方式经磨料喷射部5喷出。
本实施例中,双出杆驱动油缸31与电磁换向阀13的配合增压原理如下:
当电磁换向阀13处于第一换向位置时,电磁换向阀13内的油经工作油口a流出(此时工作油口b为回油口),并经双出杆驱动油缸31上的工作油口c流入至双出杆驱动油缸31的左侧油缸312,此时双出杆驱动油缸31上的工作油口d为回油口。随着油不断地流入至左侧油缸312,双出杆驱动油缸31内的三个活塞在活塞杆的带动下同步向右移动,右侧增压缸314的液体在右端活塞的推动下被增压并从第三单向阀34(同时第四单向阀35关闭)流出,最终流至混合腔41内。同时,随着左端活塞的右移,左侧增压缸311内产生负压,第二单向阀33被打开(同时第一单向阀32关闭),供液部2供应的研磨液被吸入至左侧增压缸311内,实现研磨液的补充。当活塞杆向右移动至预定的右侧高压极限位置时,电磁换向阀13换向至第二换向位置。
可选的,右侧增压缸314的右端设置有一右侧接近传感器,当活塞杆右移至右侧高压极限位置时,右侧接近传感器产生感应信号并将感应信号传送给电磁换向阀13,电磁换向阀13收到感应信号后触发换向。
电磁换向阀13处于第二换向位置时,电磁换向阀13内的油经工作油口b流出(此时工作油口a为回油口),并经双出杆驱动油缸31上的工作油口d流入至双出杆驱动油缸31的右侧油缸313,此时双出杆驱动油缸31上的工作油口c为回油口。随着油不断地流入至右侧油缸313,双出杆驱动油缸31内的三个活塞在活塞杆的带动下同步向左移动,左侧增压缸311内的研磨液在左端活塞的推动下被增压并从第一单向阀32(同时第二单向阀33关闭)流出,最终流至混合腔41内。同时,随着右端活塞的左移,右侧增压缸314内产生负压,第四单向阀35被打开(同时第三单向阀34关闭),供液部2供应的研磨液被吸入至右侧增压缸314内,实现研磨液的补充。当活塞杆向左移动至预定的左侧高压极限位置时,电磁换向阀13重新换向至第一换向位置。如此反复运动,实现对研磨液的连续增压。
可选的,左侧侧增压缸311的左端设置有一左侧接近传感器,当活塞杆左移至左侧高压极限位置时,左侧接近传感器产生感应信号并将感应信号传送给电磁换向阀13,电磁换向阀13收到感应信号后触发换向。
本实施例中,如图1所示,磨料供料腔42和混合腔41为分体式结构。其中,磨料供料腔42上设置有进液口。磨料供料腔42的进液口经管路分别连接第一单向阀32和第三单向阀34的出液端。即:经增压部3增压后的研磨液部分流入至磨料供料腔42内进行预先混合,经预先混合后的研磨料接着进入至混合腔内的研磨液完成充分混合,从而进一步提升混合均匀性。
可选的,如图1所示,供液部2包括储液箱21及第二液压泵22,第二液压泵22的进口经管路连接储液箱21,第二液压泵22的出口经管路分别连接第二单向阀33和第四单向阀35的进液端。第二液压泵22启动后,储液箱21内的研磨液(水、油或乳化液等)在第二液压泵22的驱动下经第二单向阀33/第四单向阀35进入至左侧增压缸311/右侧增压缸314内。
可选的,磨料喷射部5采用高压喷嘴结构;电磁换向阀13采用三位四通换向阀。
实施例2
如图2所示,本实施例中的超高压射流研磨装置的结构与实施例1中的结构基本一致,其存在的唯一区别在于混合部4的结构。为了描述间接,本说明书仅对该混合部4的结构进行针对性描述。
如图2所示,本实施例中,混合腔41和所述磨料供料腔42为一体式结构,磨料供料腔42直接成型在混合腔41的侧壁上,磨料供料腔42的顶部敞开形成加料口,经加料口能够随时将颗粒状磨料补入至磨料供料腔42内。
可选的,本实施例中,混合腔41的混合腔进液口处可设置一喷嘴43,喷嘴43经管路分别连接第一单向阀32和第三单向阀34的出液端。经增压部3增压后的研磨液最终经喷嘴喷入至混合腔内,以进一步提升混合效果。
继续参考图1和图3所示,本实用新型还提供了一种熔喷模微孔抛光用研磨系统,其包括超高压射流研磨装置及熔喷模夹具6,其中:熔喷模夹具6被配置为夹持待研磨抛光的熔喷模100;超高压射流研磨装置采用上述任一实施例的超高压射流研磨装置,超高压射流研磨装置的磨料喷射部5朝向熔喷模夹具6,从而实现对夹持于熔喷模夹具6上的熔喷模100的研磨抛光。
上文对本实用新型进行了足够详细的具有一定特殊性的描述。所属领域内的普通技术人员应该理解,实施例中的描述仅仅是示例性的,在不偏离本实用新型的真实精神和范围的前提下做出所有改变都应该属于本实用新型的保护范围。本实用新型所要求保护的范围是由所述的权利要求书进行限定的,而不是由实施例中的上述描述来限定的。
起点商标作为专业知识产权交易平台,可以帮助大家解决很多问题,如果大家想要了解更多知产交易信息请点击 【在线咨询】或添加微信 【19522093243】与客服一对一沟通,为大家解决相关问题。
此文章来源于网络,如有侵权,请联系删除


