烟用制丝环节智能化控制系统及方法与流程



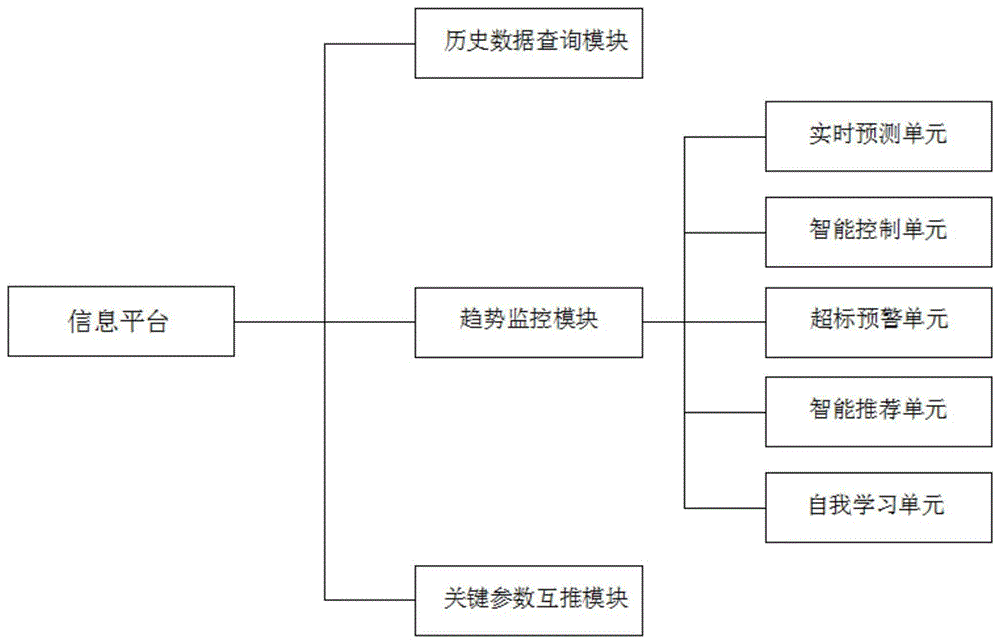
本发明涉及烟草行业,具体涉及制丝流水线的智能化控制领域,尤其涉及一种烟用制丝环节智能化控制系统及方法。
背景技术:
:在烟草生产过程中,制丝生产过程是非常重要的一个环节,它是根据烟叶原料的理化特性,按照一定的程序逐步经过多种加工工序,把烟叶制成合格烟丝的过程。在卷烟生产过程中,制丝的工艺流程最长、工序最繁杂、设备种类也最多。现有的制丝车间生产作业为流水线式,其包含的重点设备有真空回潮机、松散回潮机、暂存柜、加料回潮机、热风润叶机、切丝机、烘丝机等。目前,国内各大烟草企业的生产计划和调度仍由操作员凭借经验手工完成,上述的各设备均由人工或半自动化操作,使得产品批次间质量差异较大,不利于产品的同质化。即,制丝环节存在着大量的人工协调和资源平衡问题,有限的人力难以保证协调和平衡的准确性,生产的停顿和供料的中断将大大影响企业的生产质量,因此对烟草制丝过程的智能化控制将对企业的生产成本和经济效益产生较大影响。公开号:cn111103854a的发明申请公开了一种用于提升烟草烘丝机生产稳定性的系统及方法,属于烟草制丝生产
技术领域:
。该系统包括数据采集模块、数据处理模块、稳定性评价模块、预警与优化模块、稳态实时分析评价模块、非稳态自动控制判定模块、非稳态实时分析评价模块等结构。本发明以工业大数据、人工智能等新一代信息技术为支撑,减少非稳态时间并提高稳态控制质量,进而有效地提升烘丝机整个生产过程的质量稳定性。公告号:cn105759764a的发明专利公开了一种卷烟生产工艺参数控制系统及其控制方法。该系统由mc2烟支物理检测仪、物理指标采集装置、卷烟机电控系统、工艺参数采集装置、应用服务器、实时历史/关系数据库、数据分析服务器、现场操作终端、工艺参数控制服务器和工业以太网组成,实时历史/关系数据库由关系数据库服务器和实时历史数据库服务器构成;本发明形成一套包含采集、分析、控制的完整闭环系统,真正实现卷烟生产工艺参数的智能控制。公开号:cn101488024a的发明申请公开了一种烟草加工过程参数的在线质量评估与实时智能控制方法,包括:通过数据管理系统,预先设置原料加工设备运行参数与加工后产品内在质量之间的参数值;通过数据管理采集系统,实时进行在线采集;通过数据管理层智能控制系统,将实时在线采集的参数与预先设置的参数值进行比较;通过调整plc控制系统运行参数及pid开闭环自动化控制参数设定值,控制设备上的阀门、风机、风门执行元件,以及烘丝回潮、润叶机筒体转速的参数调节,实现烟草在线加工过程中的原料质量变化趋势的精确、动态的控制,保证产品内在质量能够实时控制在优质、稳定范围内。上述专利文献通过对烟草加工或制丝环节的数据参数的采集,并对所采集的数据参数进行分析与比对,以提高烟草加工过程的质量稳定性,并实现工艺参数的智能控制。但其智能控制仍停留在较为初级的阶段,无法实现工艺参数的预测、预警、推荐及学习,且工艺参数之间互动性差,无法实现对烘丝入口水分的精确控制,进而从源头上提高产品同质化水平。技术实现要素:为克服上述现有技术中的不足,本申请提供了一种烟用制丝环节智能化控制系统及方法。本发明依托信息平台中汇集的海量历史生产数据,借鉴数据模型理念,通过对历史生产数据挖掘分析,将多元回归分析方法、神经网络算法等运算方法集合,分阶段建立生产参数预测模型,再通过模型求解,得出不同因素影响下,关键参数的正向、反向预测,从而实现对制丝工艺烘丝入口水分的精确控制和生产趋势监控;建立智能控制模型、参数互推模型,通过建模—验证—应用—优化的流程,最终实现在线质量预警、关联比较、实时预测、趋势预测、防范差错、上游预测下游、下游反馈上游、智能推荐等功能。本发明旨在解决产品同质化水平,以提高烟丝水分控制的精确性、减少操作人员数量,实现制丝流水线“真正”的智能控制。本发明解决其技术问题所采用的技术方案为:烟用制丝环节智能化控制系统,包括信息平台,其内存储有历史生产数据,所述历史生产数据包括历史批次参数与参数关系,所述系统还包括与信息平台通信连接的趋势监控模块,包括实时预测单元、智能控制单元、超标预警单元、智能推荐单元及自我学习单元;关键参数互推模块,其以历史批次参数为基础,通过参数关系建立有参数互推模型,针对关键参数进行预测互推,对关键参数生产正确性进行验证、通过参数反推查找异常参数;历史数据查询模块,其内存储有历史预测数据与实际参数数据,并可在需要查询相应批次时进行直接查阅;其中:所述趋势监控模块基于历史生产数据,结合多元回归分析算法、神经网络算法,依照工序工段分阶段建立嵌套式生产参数预测模型,对相应生产参数进行预测,再基于生产参数预测值,通过神经网络算法,依照工序工段分阶段建立智能控制模型,对相应控制参数进行预测,基于控制参数预测值对各工序工段设备进行智能控制。作为上述技术方案的改进,所述嵌套式生产参数预测模型包括通过多元回归分析算法、神经网络算法分别构建的线性方程预测模型、神经网络预测模型,其中:批次标偏≤0.2的生产参数通过线性方程预测模型进行预测;批次标偏>0.2的生产参数通过神经网络预测模型进行预测。作为上述技术方案的改进,所述参数互推模型为基于实时预测单元的生产参数预测值、参数关系,通过多元回归分析算法构建的关键参数的线性或非线性互推模型。作为上述技术方案的改进,所述超标预警单元设置有参数标准上下限,其用于判别超出工艺范围的生产参数及控制参数,并予以报警。作为上述技术方案的改进,所述智能推荐单元采用相似度匹配算法,通过卷烟生产过程条件、历史生产数据的关联与集成,通过构建、匹配、优选、推荐步骤,实现制丝工艺全流程控制参数的智能化实时推荐。作为上述技术方案的改进,所述自我学习单元依据历史生产数据的不断积累,通过自我学习提高模型预测精度。作为上述技术方案的改进,所述工序工段包括松散回潮工段、润叶加料工段、热风润叶工段。作为上述技术方案的改进,所述智能控制单元的智能控制模型设置有反馈回路,所述反馈回路连接有监测传感器。本发明同时提供了一种烟用制丝环节智能化控制方法,所述方法应用于上述任一项所述的烟用制丝环节智能化控制系统,其包括以下步骤:步骤一,数据采集数据来源:制丝线信息管理系统中相应历史生产数据;步骤二,预测模型建立结合多元回归分析算法、神经网络算法,依照工序工段分阶段建立嵌套式生产参数预测模型,对各工段生产参数进行预测;步骤三,控制模型建立基于步骤二预测值,通过神经网络算法,依照工序工段分阶段建立智能控制模型,对各工段控制参数进行预测,基于控制参数预测值对各工序工段设备进行智能控制;步骤四,关键参数互推基于步骤二预测值,以历史批次参数为基础,通过参数关系建立参数互推模型,针对关键参数进行预测互推;通过参数互推模型可对关键参数生产正确性进行验证、通过参数反推查找异常关键参数;步骤五,控制参数实时推荐采用相似度匹配算法,通过卷烟生产过程条件、历史生产数据的关联与集成,通过构建、匹配、优选、推荐步骤,实现制丝工艺全流程控制参数的智能化实时推荐;步骤六,超标预警基于参数标准上下限,对生产参数预测值、控制参数推荐值,进行自动判别,对超出工艺范围的参数予以报警;步骤七,自我学习依据历史生产数据的不断积累,通过自我学习不断优化模型,提高模型预测精度;步骤八,趋势监控与历史数据查询将当前时段预测数据汇总成预测曲线,用于生产趋势监控;将历史预测数据与实际参数数据汇总成数据曲线,并在需要查询相应批次时进行直接查阅。作为上述技术方案的改进,步骤三中:所述智能控制模型连接反馈回路,实时依据反馈数据优化控制参数,实现智能精准控制。本发明带来的有益效果有:较之于现有技术,本申请至少具有以下优点:(1)本发明的实时预测功能能够保证制丝生产过程中各工序工段水分显示点与控制工序时间点相匹配,使预测、控制与反馈同步,增加智能控制系统的精准性;(2)本发明的智能控制功能基于上述实时预测功能,建立智能控制模型,依据预测数据、反馈数据实时计算、不断优化对应工段的控制参数,实现制丝工艺烟丝水分的智能精准控制;(3)本发明通过设立超标预警单元,能够防止生产过程中烟丝水分不稳定和批次差异,可提前预见生产异常并进行异常预警,报警历史可在超标预警单元的报警区显示,操作人员可依据报警提示进行预处理,使生产参数符合工艺标准;(4)智能推荐单元采用相似度匹配算法,通过构建、匹配、优选、推荐等关键步骤的操作模式优化,实现全流程最优控制参数的智能化实时推荐,优化系统的智能控制方式和能力;(5)通过设立自我学习单元,能够根据历史生产数据,如,总结生产过程中全年不同温湿度环境下烘丝入口水分的历史预测值和历史实测值,通过自我学习,提高模型预测精度,实现模型预测能力的升级;(6)本发明具体实施进程中,遵循is-pdca方法论,通过建模—验证—应用—优化的流程,最终可实现在线质量预警、关联比较、实时预测、趋势预测、防范差错、上游预测下游、下游反馈上游、智能推荐等功能。附图说明下面结合附图及具体实施例对本发明作进一步说明,附图1是本发明的系统模块图;附图2是本发明的智能控制单元可行的一种工艺流程图;附图3是本发明的超标预警单元可行的一种工艺流程图。具体实施方式下面将结合本发明实施例中的附图,对本发明实施例中的技术方案进行清楚、完整地描述,显然,所描述的实施例仅仅是本发明一部分实施例,而不是全部的实施例。基于本发明中的实施例,本领域普通技术人员在没有做出创造性劳动前提下所获得的所有其他实施例,都属于本发明保护的范围。在本发明中,除非另有明确的规定和限定,术语“设置”、“安装”、“相连”、“连接”、“固定”等术语应做广义理解,例如,可以是固定连接,也可以是可拆卸连接;可以是机械连接;可以是直接相连,也可以通过中间媒介间接相连。对于本领域的普通技术人员而言,可以根据具体情况理解上述术语在本发明中的具体含义。实施例1参照图1,本实施例为一种烟用制丝环节智能化控制系统,包括信息平台,其内存储有历史生产数据:历史生产数据包括历史批次参数、参数关系、关键参数(生产关键性指标,如加料回潮出口水分、热风润叶出口水分、烘丝入口水分等)及历史预测数据、实际参数数据(通过监测传感器,如水分仪、流量计、电子秤等取得的实测数据)、随时辰、季节变化的环境温湿度等影响因素及其它可用于智能化控制系统中的相关历史生产数据。该系统还包括与信息平台通信连接的趋势监控模块、关键参数预测模块和历史数据查询模块,其中:趋势监控模块,包括实时预测单元、智能控制单元、超标预警单元、智能推荐单元及自我学习单元;趋势监控模块基于历史生产数据,结合多元回归分析算法、神经网络算法,依照工序工段分阶段建立嵌套式生产参数预测模型,对相应生产参数进行预测,再基于生产参数预测值,通过神经网络算法,依照工序工段分阶段建立智能控制模型,对相应控制参数进行预测,基于控制参数预测值对各工序工段设备进行智能控制;关键参数互推模块,其以历史批次参数为基础,通过参数关系建立有参数互推模型,针对关键参数进行预测互推,还可对关键参数生产正确性进行验证、通过参数反推查找异常参数;历史数据查询模块,其内存储有历史预测数据与实际参数数据,并可在需要查询相应批次时进行直接查阅。本实施例中:依照工序工段分阶段建立的嵌套式生产参数预测模型,用于对相应工段生产参数进行预测。各工序工段包括依照制丝流水线定义的(但不限于)松散回潮工段、润叶加料工段、热风润叶工段。上述的多模块嵌套式生产参数预测模型是通过多元回归分析算法、神经网络算法分别构建的线性方程预测模型、神经网络预测模型,其中:批次标偏≤0.2的生产参数通过线性方程预测模型进行预测;批次标偏>0.2的生产参数通过神经网络预测模型进行预测。具体的,标偏=(实测值-预测值)/预测值;批次标偏≤0.2的生产参数,如:松散回潮出口温度、松散回潮出口水分、热风润叶出口水分等;批次标偏>0.2的生产参数,如:松散回潮热风温度、松散回潮循环风温流速、加料回潮出口水分、加料回潮循环风温、加料回潮循环风温流速、热风润叶入口水分等。以松散回潮工段出口水分预测模型为例进行说明:松散回潮工段出口水分预测模型以松散回潮入口水分(x1)、总打水量(x3)、补偿蒸汽开度(x4)、真空回潮至松散回潮时长(x5)为影响因子、以松散回潮出口水分(x2)为因变量建立的多元回归线性方程预测模型。各影响因子系数见表1:表1:松散回潮水分仪校验模型影响因子系数依据各影响因子系数,建立回归方程:y(松散回潮出口水分x2)=2.802x1+0.351x3-0.024x4+0.003x5-0.922该公式拟合优度为0.903。采用该公式,结合已知参数(历史生产数据均值或实测值、智能推荐值)即可进行该工序出口水分预测。预测结果用于智能控制模型的构建。以加料回潮出口水分预测模型为例进行说明:加料回潮水分仪校验模型是以加料回潮入口水分为输入,加料回潮出口水分为输出,暂存柜储存时间、补偿蒸汽开度、加料回潮排潮开度为影响因子建立的神经网络预测模型。各影响因子系数见表2:表2:加料回潮水分仪校验模型神经网络结构信息在表2中:v17-暂存柜储存时间;v20-加料回潮入口水分;v22-加料回潮出口水分;v24-加料回潮补偿蒸汽开度;v26-加料回潮排潮开度。上述各影响因子重要性见表3:表3:加料回潮水分仪校验模型各影响因子重要性nodesimportanceimportancev22v260.1040.1040.104v170.16510.16510.1651v240.24690.24690.2469v200.4840.4840.484利用该神经网络预测模型,结合已知参数即可进行该工序出口水分预测。预测结果用于智能控制模型的构建。基于各工段生产参数预测值,通过神经网络算法,建立对应工段的智能控制模型,对相应控制参数进行预测,即可基于控制参数预测值对该工段设备进行智能控制。进一步地:趋势监控模块包括实时预测单元、智能控制单元、超标预警单元、智能推荐单元及自我学习单元:实时预测单元通过数学建模的方法建立生产参数预测模型,在线、实时推算各生产参数预测值,实时预测功能能够保证制丝生产过程中各工序工段水分显示点与控制工序时间点相匹配,使预测、控制与反馈同步,从而增加智能控制系统的精准性;智能控制单元基于实时预测单元的预测值建立智能控制模型,智能控制模型设置有反馈回路,反馈回路连接有监测传感器,实时依据反馈数据计算、优化控制参数,实现智能精准控制;以热风润叶工段为例:参照图2,热风润叶机工段基于其预测模型建立智能控制模型。该智能控制模型主要是基于历史生产数据和预测值,运用热风润叶入口水分、热风润叶出口水分/烘丝入口水分,通过神经网络算法所构建,以智能控制热风润叶机补偿蒸汽阀开度,使烘丝入口水分稳定:当物料到达热风润叶入口时,智能控制模型先依据历史生产数据预设补偿蒸汽开度,在物料到达热风润叶出口前,线性方程预测模型运行,根据生产条件及其它影响因素,对热风润叶出口水分作出预测,智能控制模型依据该预测值,对补偿蒸汽开度进行实时的调整,以使出口水分趋近该预测值;当物料到达热风润叶出口,智能控制模型根据该位置水分仪实测值,与预测值、关键参数历史生产数据进行关联比较,生成反馈数据,通过反馈回路反馈控制参数的设定是否合适,并对不合适的控制参数作出实时调整,以智能控制热风润叶补偿蒸汽开度,使烘丝入口水分趋于稳定,提高烘丝来料水分的稳定性、一致性,进而提高产品同质化水平。超标预警单元以“基于标准,严于标准”的原则,设置有各参数标准上下限,用于自动判别超出工艺范围的生产过程参数,并予以报警。参照图3,超标预警单元设置于各工段实时预测单元、智能控制单元之间。基于实时预测单元的预测值及历史生产数据,当该预测值与同时段历史生产数据(如烘丝入口水分均值、烘丝入口水分标准值)之间超出所设定的标准上下限时,表明制丝生产线工艺范围内的某一/某些生产参数、控制参数出现异常,本单元提前预见到该异常问题,可避免生产质量事故的发生,随之进行异常预警,提醒操作人员作出应急处理。为准确找到该异常参数,可通过参数关系(如线性/非线性关系、逻辑关系、数据关联等),结合各工段预测模型和水分预测值通过上游追溯、参数反推,以及时查找异常参数。超标预警单元也可对超出对应标准上下限的各工段水分实测值、工艺范围内的各生产参数值、预测曲线异常等进行超标预警,以使各参数符合工艺标准。智能推荐单元采用相似度匹配算法,通过卷烟生产过程条件(如来料水分、松散回潮打水量)、历史生产数据的关联与集成,通过参数推荐模型构建、相似参数匹配、参数优选、最优参数推荐步骤,实现制丝工艺全流程最优操作参数的智能化实时推荐。如,智能推荐单元在智能控制单元对热风润叶机补偿蒸汽阀开度这一控制参数作出实时预测与控制时,基于该控制参数与其它某一控制参数之间的线性关系(或相似度),对该控制参数也实时作出推荐。自我学习单元依据历史生产数据的不断积累,通过自我学习提高模型预测精度。自我学习单元和智能推荐单元相辅相成,均可视为模型优化单元。如,其能够根据历史生产数据,智能总结生产过程中全年不同温湿度环境下烘丝入口水分的历史预测值和历史实测值,消除因季节变化带来的环境温湿度的影响,使预测模型更加精确完善。进一步地:关键参数互推模块以历史批次参数为基础,通过参数关系建立参数互推模型,针对关键参数进行预测互推,还可对关键参数生产正确性进行验证、通过参数反推查找异常参数。参数互推模型为基于实时预测单元的生产参数预测值、参数关系,通过多元回归分析算法构建的关键参数的线性或非线性互推模型。如,当上述的智能推荐单元无法对非线性参数进行参数相似度匹配与智能推荐时,可通过参数互推模型实现该功能。如,基于加料回潮出口水分预测模型得到该工段出口水分预测值,基于该水分值的历史生产数据,借助下一工段热风润叶出口水分值与之间的参数关系,对热风润叶出口水分进行参数互推(“预”预测),并基于该推荐值,可对热风润叶工段的生产趋势进行预测或监测,对关键参数生产正确性进行验证;如,当基于热风润叶机工段的智能控制模型,对其补偿蒸汽开度进行实时预测、控制、调整时,基于补偿蒸汽开度与其它某一控制参数之间的非线性关系(可通过历史生产数据分析得到),对该控制参数实时作出互推。借助参数互推模型,基于关键参数、参数关系,可通过参数反推、上游追溯及时查找到异常关键参数。本实施例中:历史数据查询模块内存储有历史预测数据与实际参数数据,可汇总成曲线,并可在需要查询相应批次时进行直接查阅。实时预测单元的预测值汇总成的预测曲线、智能控制单元控制参数的调整历史、各工段如烘丝入口水分实测值汇总成的实际曲线、关键参数的生产趋势等,均可存储于该模块,并随时查阅。实施例2烟用制丝环节智能化控制方法,本方法应用于实施例1所述的烟用制丝环节智能化控制系统,其包括以下步骤:步骤一,数据采集数据来源:制丝线信息管理系统中相应历史生产数据;步骤二,预测模型建立结合多元回归分析算法、神经网络算法,依照工序工段分阶段建立嵌套式生产参数预测模型,对各工段生产参数进行预测;步骤三,控制模型建立基于步骤二预测值,通过神经网络算法,依照工序工段分阶段建立智能控制模型,对各工段控制参数进行预测,基于控制参数预测值对各工序工段设备进行智能控制;智能控制模型连接反馈回路,实时依据反馈数据优化控制参数,实现智能精准控制;步骤四,关键参数互推基于步骤二预测值,以历史批次参数为基础,通过参数关系建立参数互推模型,针对关键参数进行预测互推;通过参数互推模型可对关键参数生产正确性进行验证、通过参数反推查找异常关键参数;步骤五,控制参数实时推荐采用相似度匹配算法,通过卷烟生产过程条件、历史生产数据的关联与集成,通过构建、匹配、优选、推荐步骤,实现制丝工艺全流程控制参数的智能化实时推荐;步骤六,超标预警基于参数标准上下限,对生产参数预测值、控制参数推荐值,进行自动判别,对超出工艺范围的参数予以报警;步骤七,自我学习依据历史生产数据的不断积累,通过自我学习不断优化模型,提高模型预测精度;步骤八,趋势监控与历史数据查询将当前时段预测数据汇总成预测曲线,用于生产趋势监控;将历史预测数据与实际参数数据汇总成数据曲线,并在需要查询相应批次时进行直接查阅。最后应说明的是:以上所述仅为本发明的优选实施例而已,并不用于限制本发明,尽管参照前述实施例对本发明进行了详细的说明,对于本领域的技术人员来说,其依然可以对前述各实施例所记载的技术方案进行修改,或者对其中部分技术特征进行等同替换,凡在本发明的精神和原则之内,所作的任何修改、等同替换、改进等,均应包含在本发明的保护范围之内。当前第1页1 2 3 
起点商标作为专业知识产权交易平台,可以帮助大家解决很多问题,如果大家想要了解更多知产交易信息请点击 【在线咨询】或添加微信 【19522093243】与客服一对一沟通,为大家解决相关问题。
此文章来源于网络,如有侵权,请联系删除



tips