氢、磷、氮掺杂单晶硅及其制备方法、太阳能电池与流程



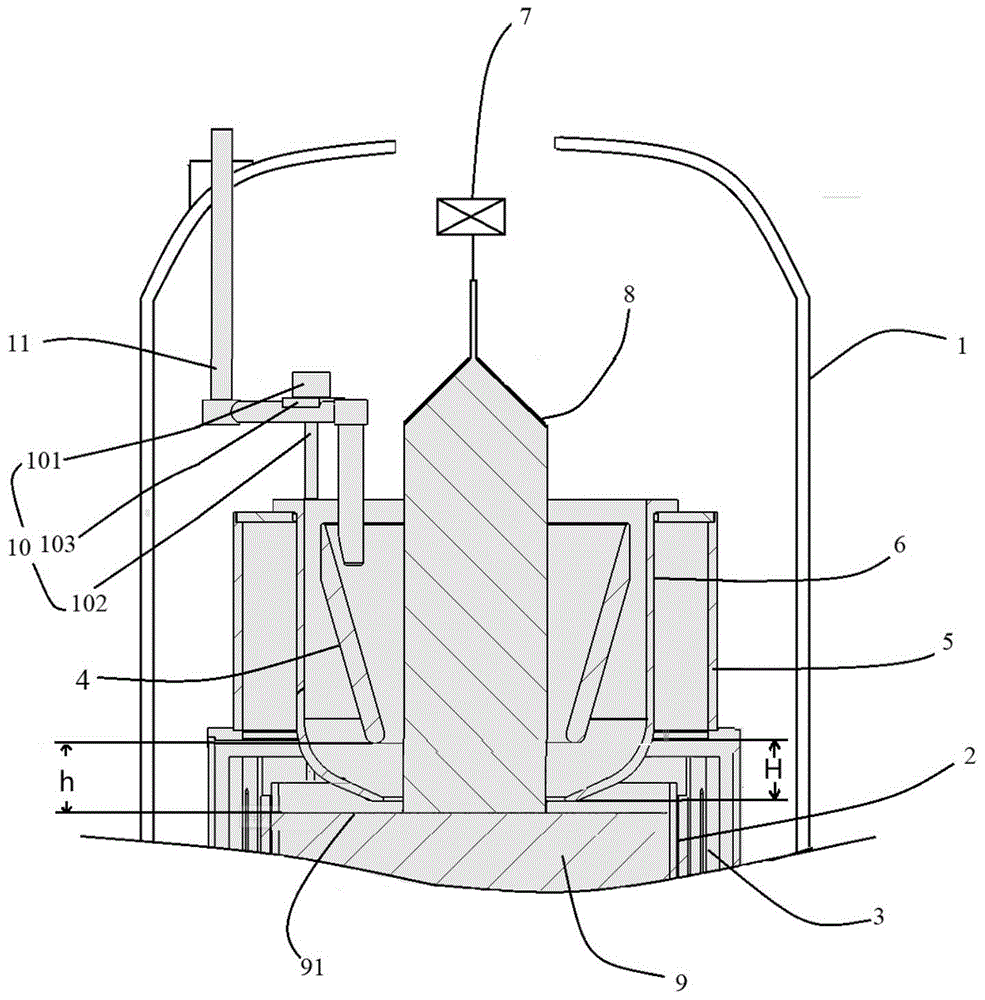
本申请涉及光伏电池技术领域,具体地讲,涉及氢、磷、氮掺杂单晶硅及其制备方法、太阳能电池。
背景技术:
目前,作为太阳能光电利用中发展最快的领域之一,晶体硅电池的技术发展颇受瞩目,提高太阳能电池的转换效率是目前亟需解决的问题。在现有的单晶硅生产过程中,直拉单晶硅容易出现中点缺陷、位错缺陷及金属缺陷等,这些缺陷的存在容易降低单晶硅的少子寿命,降低太阳能电池的转换效率。
技术实现要素:
鉴于此,本申请提出氢、磷、氮掺杂单晶硅及其制备方法、太阳能电池,可以有效提升单晶硅中的少子寿命,有利于提升电池钝化效果,提升硅片机械强度,提高太阳能电池的转换效率。
本申请提供一种氢、磷、氮掺杂单晶硅,所述氢、磷、氮掺杂单晶硅中的氢掺杂浓度为1×105~1×1016atoms/cm3,磷掺杂浓度为1×1015~5×1017atoms/cm3,氮掺杂浓度为0.1×1012~1×1016atoms/cm3;所述氢、磷、氮掺杂单晶硅的电阻率为0.1~10ω·cm。
在一种可行的实施方式中,所述方法包括以下步骤:
将多晶硅原料以及磷掺杂剂放入石英坩埚中;
将所述石英坩埚置于单晶炉抽真空,并在惰性气体保护下熔化多晶硅原料,得到硅熔体;
当所述硅熔体温度稳定后,往所述单晶炉内加入氢源及氮源,将晶种浸入所述硅熔体中开始引晶;
引晶结束后,开始放肩过程,使得晶体的直径逐步增大至预设宽度,再进行等径生长;
等径生长完成后,进入收尾阶段,使得所述晶体的直径逐步缩小直至与所述硅熔体分离;
生长完成的所述晶体冷却至室温后取出,得到氢、磷、氮掺杂单晶硅。
在一种可行的实施方式中,所述氢源为含氢气体,所述氮源为含氮气体,所述往所述单晶炉内加入氢源及氮源的具体步骤包括:
将所述含氢气体、所述含氮气体与所述惰性气体混合形成混合气体,并将所述混合气体通入所述单晶炉内。
在一种可行的实施方式中,所述含氢气体在所述混合气体中的体积占比为0.1%~10%,所述含氮气体在所述混合气体中的体积占比为1%~20%。
在一种可行的实施方式中,所述含氢气体包括氢气、硅烷中的至少一种;和/或,所述含氮气体包括氮气、氨气中的至少一种;和/或,所述惰性气体包括氦气、氩气中的至少一种。
在一种可行的实施方式中,所述氢源为富含氢的多晶硅原料,所述氮源为含氮气体,所述往所述单晶炉内加入氢源及氮源的具体步骤包括:
将所述富含氢的多晶硅原料加入所述硅熔体中,将所述含氮气体与所述惰性气体混合形成混合气体并通入所述单晶炉内。
在一种可行的实施方式中,所述含氮气体在所述混合气体中的体积占比为1%~20%;和/或,
所述富含氢的多晶硅原料中的氢含量大于1×1016atoms/cm3。
在一种可行的实施方式中,所述氢源与所述氮源为富含氢、氮的多晶硅原料,所述往所述单晶炉内加入氢源及氮源的具体步骤包括:
将所述富含氢、氮的多晶硅原料加入所述硅熔体中;其中,所述富含氢、氮的多晶硅原料中的氢含量大于1×1016atoms/cm3,且所述富含氢、氮的多晶硅原料中的氮含量大于1×1016atoms/cm3。
本申请实施例还提供一种太阳能电池,所述太阳能电池包括所述太阳能电池包括由上至下依次排布的正面电极、正面钝化层、硼扩散层、半导体衬底、隧穿氧化层、掺杂多晶硅层、背面钝化层、背面电极,
其中,所述半导体衬底包括氢、磷、氮掺杂单晶硅,所述氢、磷、氮掺杂单晶硅中的氢掺杂浓度为1×105~1×1016atoms/cm3,磷掺杂浓度为1×1015~5×1017atoms/cm3,氮掺杂浓度为0.1×1012~1×1016atoms/cm3;所述氢、磷、氮掺杂单晶硅的电阻率为0.1~10ω·cm。
在一种可行的实施方式中,所述半导体衬底的中心区域的氢含量大于边缘区域的氢含量。
本申请的技术方案至少具有以下有益的效果:
本申请提供的氢、磷、氮掺杂单晶硅,掺入的氢原子,氢原子能够和硅中的其他杂质、点缺陷形成复合体或沉淀,去除杂质的电活性,起到钝化作用,从而可以大幅降低掺磷单晶硅晶体中的点缺陷、位错缺陷以及金属缺陷的活性,掺入的氮原子可以钉扎位错的滑移、有利于控制位错缺陷,可以有效提升掺磷单晶硅中的少子寿命,提高单晶硅品质;在制备过程中,加入适量的氮源与氢源,使得微量氢原子与氮原子融入硅熔体中,来实现氢、氮元素掺杂,制备方法简单,制备得到的氢、磷、氮掺杂单晶硅可以有效提高少子寿命,提高太阳能电池的转换效率。
附图说明
为了更清楚的说明本申请实施例或现有技术的技术方案,下面将对实施例或现有技术描述中所需要使用的附图作简单的介绍,显而易见地,下面描述中的附图仅仅是本申请的一些实施例,对于本领域普通技术人员来讲,在不付出创造性劳动的前提下,还可以根据这些附图获得其他的附图。
图1a为本实施例提供的一种单晶炉的一种结构示意图;
图1b为本实施例提供的一种单晶炉的另一种结构示意图;
图2为本实施例提供的一种氢、磷、氮掺杂单晶硅的制备方法的流程示意图;
图3为本实施例提供的一种太阳能电池的结构示意图。
具体实施方式
为了更好的理解本申请的技术方案,下面结合附图对本申请实施例进行详细描述。
应当明确,所描述的实施例仅仅是本申请一部分实施例,而不是全部的实施例。基于本申请中的实施例,本领域普通技术人员在没有作出创造性劳动前提下所获得的所有其它实施例,都属于本申请保护的范围。
在本申请实施例中使用的术语是仅仅出于描述特定实施例的目的,而非旨在限制本申请。在本申请实施例和所附权利要求书中所使用的单数形式的“一种”、“所述”和“该”也旨在包括多数形式,除非上下文清楚地表示其它含义。
应当理解,本文中使用的术语“和/或”仅仅是一种描述关联对象的关联关系,表示可以存在三种关系,例如,a和/或b,可以表示:单独存在a,同时存在a和b,单独存在b这三种情况。另外,本文中字符“/”,一般表示前后关联对象是一种“或”的关系。
本申请实施例提供的一种氢、磷、氮掺杂单晶硅,掺入的氢原子能够和硅中的其他杂质、点缺陷形成复合体或沉淀,去除杂质的电活性,起到钝化作用,从而可以大幅降低掺磷单晶硅晶体中的点缺陷、位错缺陷以及金属缺陷的活性,掺入的氮原子可以钉扎位错的滑移、有利于控制位错缺陷,可以有效提升掺磷单晶硅中的少子寿命,提高单晶硅品质。
所述氢、磷、氮掺杂单晶硅中的氢掺杂浓度为1×105~1×1016atoms/cm3,例如可以是1×105atoms/cm3、1×106atoms/cm3、1×107atoms/cm3、1×108atoms/cm3、1×109atoms/cm3、1×1010atoms/cm3、1×1012atoms/cm3、1×1013atoms/cm3、1×1014atoms/cm3、1×1015atoms/cm3或1×1016atoms/cm3等,当然也可以是此范围内的其它数值,在此不做限定。
单晶硅中的磷掺杂浓度为1×1015~5×1017atoms/cm3,例如可以是1×1015atoms/cm3、5×1015atoms/cm3、1×1016atoms/cm3、2×1016atoms/cm3、4×1016atoms/cm3、5×1016atoms/cm3、1×1017atoms/cm3、2×1017atoms/cm3或5×1017atoms/cm3等,当然也可以是此范围内的其它数值,在此不做限定。
单晶硅中的氮掺杂浓度为0.1×1012~1×1016atoms/cm3,例如可以是0.1×1012atoms/cm3、1×1013atoms/cm3、1×1014atoms/cm3、1×1015atoms/cm3或1×1016atoms/cm3等,当然也可以是此范围内的其它数值,在此不做限定。
所述氢、磷、氮掺杂单晶硅的电阻率为0.1~10ω·cm,例如可以是0.1ω·cm、0.5ω·cm、1.4ω·cm、3.7ω·cm、5.2ω·cm、8.5ω·cm或10ω·cm等,当然也可以是此范围内的其它数值,在此不做限定。
可以理解地,将氢、磷、氮的掺杂浓度控制在上述范围内,能够使得后续制成的硅片可以满足太阳能电池的性能需求,并且,掺杂了氢、磷、氮后的单晶硅,可以大幅降低掺磷单晶硅晶体中的点缺陷、位错缺陷以及金属缺陷的活性,有利于控制位错缺陷,提升单晶硅的机械强度,在后续生产中降低硅片的不良率,有利于降低单晶硅制备成本。
本申请实施例还提供一种氢、磷、氮掺杂单晶硅的制备方法,采用单晶炉,单晶炉的部分结构如图1a~1b所示,单晶炉包括炉体1、石英坩埚2、加热器3、水冷热屏4、保温筒5、导流筒6、晶体提拉装置7及晶体8。晶体提拉装置7用于提拉晶体8。
单晶炉还包括连接件10及水冷热屏提拉杆11,连接件10用于连接水冷热屏提拉杆11与导流筒6,水冷热屏提拉杆11用于提拉水冷热屏4。
在一种实施方式中,连接件10包括提升限位部101、支撑杆102及提拉卡扣103。支撑杆102的两端分别与提升限位部101、导流筒6相连,提拉卡扣103的一端固定连接在水冷热屏提拉杆11,另一端卡套于支撑杆102上。需要说明的是,加热器3用于加热石英坩埚2内的多晶硅原料以及磷掺杂剂,使得多晶硅原料熔化形成硅熔体9。水冷热屏4可以降低晶体8表面的温度,加大晶体8内部的温度梯度,可以提高晶体的生长速度。
图2为本申请实施例提供的一种氢、磷、氮掺杂单晶硅的制备方法的流程图,如图2所示,所述制备方法包括以下步骤:
将多晶硅原料以及磷掺杂剂放入石英坩埚中;
将石英坩埚置于单晶炉抽真空,并在惰性气体保护下熔化多晶硅原料,得到硅熔体;
当所述硅熔体温度稳定后,往所述单晶炉内加入氢源及氮源,将晶种浸入所述硅熔体中开始引晶;
引晶结束后,开始放肩过程,使得晶体的直径逐步增大至预设宽度,再进行等径生长;
等径生长完成后,进入收尾阶段,使得所述晶体的直径逐步缩小直至与所述硅熔体分离;
生长完成的所述晶体冷却至室温后取出,得到氢、磷、氮掺杂单晶硅。
在本方案中,在引晶过程中,加入氮源与氢源,使得微量氢原子与氮原子融入硅熔体中,来实现氢、氮元素掺杂,掺入的氢原子,可以大幅降低掺磷单晶硅晶体中点缺陷、位错缺陷以及金属缺陷的活性,掺入的氮原子可以钉扎位错的滑移、有利于控制位错缺陷,可以有效提升掺磷单晶少子寿命,提高单晶硅品质。
下面,将结合本发明实施例中的附图,对本发明实施例中的技术方案进行清楚、完整地描述,显然,所描述的实施例仅仅是本发明一部分实施例,而不是全部的实施例。基于本发明的实施例,本领域普通技术人员在没有做出创造性劳动前提下所获得的所有其他实施例,都属于本发明保护的范围。
步骤(1),将多晶硅原料以及磷掺杂剂放入石英坩埚中。
在一种实施方式中,多晶硅原料可以是原生多晶硅料,磷掺杂剂为掺磷母合金,掺磷母合金的电阻率为0.001~0.05ω·cm。磷掺杂剂的添加量可以根据最后制得的单晶硅中磷的浓度进行配制。可选地,按照每立方厘米单晶硅材料中的原子个数,磷的掺杂浓度为1×1015~5×1017atoms/cm3,以此为根据称取适量的磷掺杂剂,加入石英坩埚中。
在其他实施方式中,也可以采用磷掺杂的多晶硅原料。
步骤(2),将石英坩埚置于单晶炉抽真空,并在惰性气体保护下熔化多晶硅原料,得到硅熔体;
具体地,惰性气体例如可以是氩气、氦气中的至少一种。
在熔料过程中,控制单晶炉内的温度为1420~1570℃。例如可以是1450℃、1480℃、1500℃、1520℃、1540℃、1560℃,优选地,单晶炉内的温度为1520℃,以得到熔融的液态硅。
步骤(3),当所述硅熔体温度稳定后,往所述单晶炉内加入氢源及氮源,将晶种浸入所述硅熔体中开始引晶。
所述硅熔体温度稳定的成晶液面温度在1420~1480℃,此时,石英坩埚内硅液温度稳定,可以往惰性气体中加入氢源及氮源,使得氢原子、氮原子掺杂入硅熔体中。
在一种实施方式中,所述氢源为含氢气体,所述氮源为含氮气体,所述往所述单晶炉内加入氢源及氮源的具体步骤包括:
将所述含氢气体、所述含氮气体与所述惰性气体混合形成混合气体,并将所述混合气体通入所述单晶炉内。
具体地,含氢气体包括氢气、硅烷中的至少一种。含氮气体包括氮气、氨气中的至少一种。惰性气体包括氩气、氦气中的至少一种。
从进入引晶阶段开始,控制含氢气体在混合气体中的体积占比为0.1%~10%,例如可以是0.1%、0.5%、1%、2%、3%、4%、5%、8%或10%,当然也可以是此范围内的其它数值,在此不做限定。
从进入引晶阶段开始,控制含氮气体在混合气体中的体积占比为1%~20%,例如可以是1%、3%、5%、8%、10%、13%、15%、18%或20%,当然也可以是此范围内的其它数值,在此不做限定。
在具体实施例中,将含氢气体与含氮气体在通入炉体内前与惰性气体合并至同一管路内,优选地,可以在管路上安装一个气体混合阀,使得气体混合的更加均匀。
在另一种实施方式中,所述氢源为富含氢的多晶硅原料,所述氮源为含氮气体,所述往所述单晶炉内加入氢源及氮源的具体步骤包括:
将所述富含氢的多晶硅原料加入所述硅熔体中,将所述含氮气体与所述惰性气体混合形成混合气体并通入所述单晶炉内。
所述富含氢的多晶硅原料中的氢含量大于1×1016atoms/cm3。需要说明的是,当采用富含氢的多晶硅原料时,在后续引晶、放肩、等径生长及收尾过程中,无需再加入含氢气体。
所述含氮气体在所述混合气体中的体积占比为1%~20%,例如可以是1%、3%、5%、8%、10%、13%、15%、18%或20%,当然也可以是此范围内的其它数值,在此不做限定。
在另一种实施方式中,所述氢源与所述氮源为富含氢、氮的多晶硅原料,所述往所述单晶炉内加入氢源及氮源的具体步骤包括:
将所述富含氢、氮的多晶硅原料加入所述硅熔体中。
所述富含氢、氮的多晶硅原料中的氢含量大于1×1016atoms/cm3,所述富含氢、氮的多晶硅原料中的氮含量大于1×1016atoms/cm3,需要说明的是,当采用富含氢、氮的多晶硅原料时,在后续引晶、放肩、等径生长及收尾过程中,无需再加入含氢气体和含氮气体。
在引晶过程中,控制水冷热屏的水流量为40~160slpm,石英坩埚的转速为4~10r/min,单晶炉内温度为1420~1480℃,单晶炉内压强为1000~3000pa,混合气体的流量为50~200slpm,引晶速度为40-400mm/h。
可选地,水冷热屏的水流量例如可以是40slpm、60slpm、80slpm、100slpm、120slpm、140slpm或160slpm,当然也可以是此范围内的其它数值,在此不做限定。
可选地,石英坩埚的转速例如可以是4r/min、5r/min、6r/min、7r/min、8r/min、9r/min或10r/min,当然也可以是此范围内的其它数值,在此不做限定。
可选地,单晶炉内温度例如可以是1420℃、1440℃、1460℃或1480℃,当然也可以是此范围内的其它数值,在此不做限定。
可选地,单晶炉内压强例如可以是1000pa、1500pa、2000pa、2500pa或3000pa,当然也可以是此范围内的其它数值,在此不做限定。
可选地,混合气体的流量为50slpm、80slpm、100slpm、120slpm、150slpm、180slpm或200slpm,当然也可以是此范围内的其它数值,在此不做限定。
可选地,引晶速度例如可以是40mm/h、80mm/h、100mm/h、150mm/h、200mm/h、250mm/h、300mm/h、350mm/h或400mm/h,在此不做限定。
需要说明的是,在上述炉内温度、压力、水冷热屏的水流量、惰性气体的流量、石英坩埚的转速、引晶速度范围内,有助于提高引晶成功率。
在本实施例中,如图1a所示,在引晶过程中,水冷热屏提拉杆11往远离所述硅熔体表面方向提升水冷热屏4,导流筒6在连接件10的作用下随水冷热屏提拉杆11上升,使得所述水冷热屏底部与所述硅熔体表面91之间的距离h调整至第一预设距离。可选地,第一预设距离为25~60mm。所述第一预设距离的设定可以使得在引晶阶段,水冷热屏远离高温的硅溶体,以免造成温度的波动,生长界面温度稳定,具有较高的引晶成功率。
步骤(4),引晶结束后,开始放肩过程,使得晶体的直径逐步增大至预设宽度,再进行等径生长;
在放肩过程中,控制水冷热屏的水流量为40~160slpm,石英坩埚的转速为4~10r/min,单晶炉内温度为1420~1460℃,单晶炉内压强为1000~3000pa,混合气体的流量为50~200slpm。
所述晶体的第一提拉速度为40-80mm/h,使得所述晶体的直径逐步增大至10-305mm。可选地,第一提拉速度例如可以是40mm/h、55mm/h、65mm/h、80mm/h等,所述晶体的直径逐步增大至40mm、100mm、150mm、225mm、245mm、285mm、295mm或305mm等,在此不做限定。可以理解地,放肩过程中,晶体内部温度梯度小,为保证拉晶稳定性,晶体的生长速度较慢,晶体提拉速度也较慢。并且,在整个放肩过程中,单晶炉内的温度可以逐渐下降,不可升温。
晶体的直径范围可根据电池片对硅片的尺寸要求进行设计控制,在此不做限定。
在放肩过程中,可以减小水冷热屏底部与硅熔体表面之间的距离h,提升水冷热屏对晶体棒吸热的能力。
可选地,等径生长过程中,控制水冷热屏的水流量为40~160slpm,石英坩埚的转速为4~10r/min,单晶炉内温度为1420~1460℃,单晶炉内压强为1000~3000pa,混合气体的流量为50~200slpm。
所述晶体的第二提拉速度为70~140mm/h,例如可以是70mm/h、80mm/h、90mm/h、100mm/h、110mm/h、120mm/h、130mm/h或140mm/h等,在此不做限定。可以理解地,在等径生长阶段,晶体已开始进入水冷热屏区域或完全进入水冷热屏区域,水冷热屏可快速将晶体热量吸收,使得晶棒温度梯度变大,此阶段为保证生长效率,晶体生长速度加大,可提高晶体的提拉速度。
如图1b所示,在等径生长过程中,水冷热屏提拉杆11往靠近所述硅熔体表面方向下降所述水冷热屏4,导流筒6也随之下降直至导流筒6的翻边与保温筒5相抵接时,水冷热屏4继续往靠近硅熔体表面方向下降,使得所述水冷热屏4底部与所述硅熔体表面91之间的距离h调整至第二预设距离。可选地,所述第二预设距离为10~40mm。此时,水冷热屏4相对于导流筒6下降,使得水冷热屏4底部与硅熔体表面距离进一步减小,提升了水冷热屏对晶体棒吸热的能力,实现变温度梯度拉晶。
在本实施例中,所述第一预设距离与所述第二预设距离之间的高度差为15~50mm。
步骤(5),等径生长完成后,进入收尾阶段,使得所述晶体的直径逐步缩小直至与所述硅熔体分离。
在该过程中,控制水冷热屏的水流量为40~160slpm,石英坩埚的转速为4~10r/min,单晶炉内温度为1420~1460℃,单晶炉内压强为1000~3000pa,混合气体的流量为50~200slpm。
晶体的第三提拉速度为70-130mm/h,例如可以是75mm/h、85mm/h、95mm/h、100mm/h、115mm/h或120mm/h;在收尾阶段,单晶炉内的温度快速提升。
步骤(6),生长完成的所述晶体冷却至室温后取出,得到氢、磷、氮掺杂单晶硅。
所述氢、磷、氮掺杂单晶硅中的氢掺杂浓度为1×105~1×1016atoms/cm3,磷掺杂浓度为1×1015~5×1017atoms/cm3,氮掺杂浓度为0.1×1012~1×1016atoms/cm3;所述氢、磷、氮掺杂单晶硅的电阻率为0.1~10ω·cm。
本申请的实施例还提供一种太阳能电池,该太阳能电池可以采用上述所述氢、磷、氮掺杂单晶硅制作形成。
太阳能电池包括由上至下依次排布的正面电极、正面钝化层、硼扩散层、半导体衬底、隧穿氧化层、掺杂多晶硅层、背面钝化层、背面电极。
如图3所示,在一种实施例中,太阳能电池为具有topcon结构的太阳能电池,其结构包括:
半导体衬底100,半导体衬底100包括上述的氢、磷、氮掺杂单晶硅衬底,可以由上述制得单晶硅棒切片形成硅片,所述硅片可以用作半导体衬底。其中,所述氢、磷、氮掺杂单晶硅中的氢掺杂浓度为1×105~1×1016atoms/cm3,磷掺杂浓度为1×1015~5×1017atoms/cm3,氮掺杂浓度为0.1×1012~1×1016atoms/cm3,所述氢、磷、氮掺杂单晶硅的电阻率为0.1~10ω·cm。
在电池制备过程中,所述硅片会经过高温处理(例如高温退火处理),所述硅片中的氢原子在高温下会产生一定的逃逸,在一些实施例中,相比于所述硅片的中心区域,其边缘区域的氢更容易发生逃逸,使得所述半导体衬底的中心区域的氢含量大于边缘区域的氢含量。在某种程度下,所述逃逸的氢原子有助于半导体衬底的缺陷钝化,进而提升电池的转换效率。
在一些实施例中,所述太阳能电池在制备过程中,所述半导体衬底100的内部可以形成h-p键或h-n键,用于固定所述氢原子以免发生过多的逃逸。
在本实施例中,半导体衬底100包括相对设置的正面和背面,所述半导体衬底100中的氢含量不均匀分布,例如,所述半导体衬底100的中心区域的氢含量大于其边缘区域的氢含量。可以理解的是,所述边缘区域可以指位于所述衬底表面(例如,正面、背面和/或侧面)以内的一定深度的区域,例如10nm以内。所述中心区域可以指非边缘区域的特定部分区域或全部区域。
位于半导体衬底100正面的硼扩散层13,例如可以对半导体衬底的正面进行硼扩散,形成p型硼扩散层。
位于硼扩散层13上表面的正面钝化层12,在一些实施例中,正面钝化层12与正面电极之间还可以形成减反层;
位于正面钝化层12上表面的正面电极111,正面电极111穿过正面钝化层12与硼扩散层13形成欧姆接触;
位于所述半导体衬底100背面的隧穿氧化层14,隧穿氧化层14例如可以是氧化硅层;
位于所述隧穿氧化层14背面的掺杂多晶硅层15;
位于掺杂多晶硅层15背面的背面钝化层16。
位于背面钝化层16背面的背面电极112,其中,背面电极112穿过背面钝化层16与掺杂多晶硅层15形成欧姆接触,掺杂多晶硅层15与隧穿氧化层14组成topcon结构。
本发明实施例中不限定正面钝化层12、背面钝化层16的具体类型,例如可以为氮化硅层、氮氧化硅层、氧化铝/氮化硅叠层结构中的任意一种或多种的组合,能够对硅衬底产生良好的钝化效果,有助于提高电池的转换效率。
本发明实施例中不限定正面电极111和背面电极112的具体材质。例如,正面电极111为银电极或银/铝电极,背面电极112为银电极。
本发明实施例中,可以采用丝网印刷技术在半导体衬底的表面印刷导电浆料,并烧结烘干,形成栅线状电极结构。所述形成的栅线电极通过掺杂层的重掺区域与半导体衬底形成电连接。所述导电浆料包括但不限于银浆和/或铝浆等。
在其他实施例中,半导体衬底的正面和/或背面都可以形成电极结构。
还需说明的是,本发明实施例对于上述太阳能电池中各层结构的厚度不作限定,可由本领域技术人员根据实际情况而调控。
以上所述仅为本申请的优选实施例而已,并不用于限制本申请,对于本领域的技术人员来说,本申请可以有各种更改和变化。凡在本申请的精神和原则之内,所作的任何修改、等同替换、改进等,均应包含在本申请的保护范围之内。
起点商标作为专业知识产权交易平台,可以帮助大家解决很多问题,如果大家想要了解更多知产交易信息请点击 【在线咨询】或添加微信 【19522093243】与客服一对一沟通,为大家解决相关问题。
此文章来源于网络,如有侵权,请联系删除


