一种密闭循环模式下快速机械脱氧、充氮方法与流程



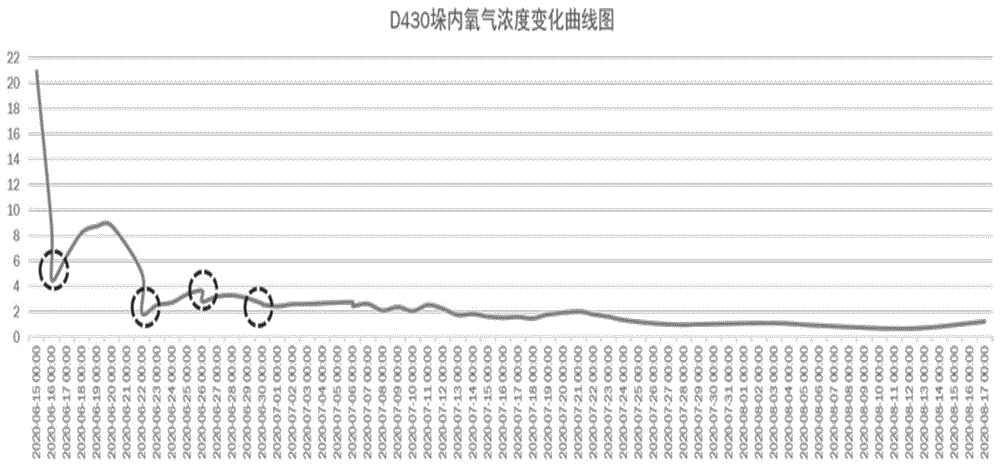
本发明属于农产品仓储害虫及密闭舱室有害生物机械充氮气调防治
技术领域:
,具体涉及一种密闭循环模式下快速机械脱氧、充氮的方法。
背景技术:
:机械充氮气调防虫是贮存粮食、中药材、烟草环保化防虫的重要手段,其基本原理是利用制氮机以空气为原料,将从空气中分离出来的高纯度氮气通过输气管道充入密闭仓间,氮气置换出贮存农产品的密闭仓间及船舱、飞机的密闭舱室(均简称为“密闭仓间”,以下同)中的氧气形成密闭仓间中的低氧气调环境,以达到抑制害虫活动的目的。目前市场上应用的制氮设备及存在的问题包括有:1)变压吸附制氮机。变压吸附(psa)制氮工艺是以以空气为原材料,使用碳分子筛为吸附剂,利用碳分子筛对氮和氧的选择性吸附性能把空气中的氮和氧分离出来,使用压缩机及压缩空气,利用碳分子筛的选择吸附特性,采用加压吸附、减压解吸的循环周期,使压缩空气交替进入吸附塔(也可以单塔完成)来实现空气分离,从而连续产出高纯度的产品氮气。制氮机运行一段时间后,分子筛对氧的吸附达到平衡,根据碳分子筛在不同压力下对吸附气体的吸附量不同的特性,降低压力使碳分子筛解除对氧的吸附,变压吸附法通常使用两塔并联,交替进行加压吸附和解压再生,从而获得连续的氮气流。psa制氮机基本工艺流程包括:空气经空压机压缩后,经过除尘、除油、干燥后,进入空气储罐,经过空气进气阀、左吸进气阀进入左吸附塔,塔压力升高,压缩空气中的氧分子被碳分子筛吸附,未吸附的氮气穿过吸附床,经过左吸出气阀、氮气产气阀进入氮气储罐。2)膜分离制氮机。利用不同气体组分在膜中的渗透、扩散速率不同,压缩空气经过过滤器进入膜分离器后,空气中的水蒸气、二氧化碳及氧气快速透过膜壁进入膜的另一侧被富集排空;氮气透过膜壁的相对速率慢而留在膜中,富集后的氮气被作为产品气输送至密闭仓间等应用使用场所。它由压缩机、贮罐、冷干机、过滤器、加热器、中空纤维膜及管、阀组成。上述变压吸附制氮、膜分离制氮设备以空气为原料制取氮气,单位时间内制取氮气效率高、氮气纯度大,但单一使用氮气气调杀虫的作用周期长,特别是在往密闭仓间注入氮气杀虫的过程,因为受制于仓间的气密性、环境温湿度条件等,机械充氮防虫的过程耗时长、过程监管难度大、能耗高。粮食、烟叶等仓贮养护物资的密实度高,一般需要一个月或者更长的时间才能将封闭气调环境中的氧气浓度调控降至2%以下并起到理想的防虫效果,这么长的密闭气调过程中会延缓仓贮粮食、烟叶的自然呼吸与醇化的进程;3)脱氧机。为了解决上述变压吸附制氮机和膜分离制氮机在使用中存在的问题,同时也是为了克服中、大型制氮机需要空压机和压力容器安全使用方面的压力,可以使用脱氧机对密闭仓间进行机械循环脱氧富集氮气防虫。脱氧机是采用低压风机进行循环脱氧,再使用真空泵解析活化,脱氧机与vsa制氮机原理相似,二者都采用真空解析,但由于脱氧机的动力源采用了压力更低、耗电量更小的风机,采用效率更高的半封闭式取气模式,所以脱氧机与vsa制氮机也存在一定的差别。真空低压吸附脱氧机采用活性碳或碳分子筛吸附再生的原理来吸附大气中的氧气并向库内注入高纯度氮气。脱氧机的使用大大提升了体量、规模大的密闭仓间脱氧富集氮气的速率,也不必再使用压缩机和大功率的风机,设备运行的能效比大大提高,设备的安全管控压力也大为缓解。脱氧机的应用也存在一些问题,需要两条管道与密闭仓间相连(进气和回气),是依靠在循环脱氧的模式中不断提高设备的输出氮气纯度,上述密闭循环脱氧制氮系统在将氮、氧分离并释放出氧气以后会在系统内部形成混合气体密度的降低及气压损失,为维持系统的正常运行,目前的脱氧机设备是依靠半开放式取气的模式,在脱氧机设备上增加一个空气进口以及时弥补系统内气体密度的降低及压力损失,但随着上述新补充的空气进入密闭循环系统中,也会同步稀释密闭循环系统中的氮气浓度。以武汉黄陂区前川烟叶仓库烟叶机械充氮气调为例,该批次烟叶堆垛使用厚度0.11毫米的pa/pe五层共挤尼龙复合膜进行六面密闭,机械充氮气调设计有6个主要的调控时间节点,先将所有密闭垛位的氧气浓度调控降至5%以下,然后再分组进行低氧浓度条件下的进一步调控;机械充氮设备使用天津捷盛科技有限公司的脱氧机,设备的氮气产量选择100m3/h、设备产成氮气纯度≥95%,烟叶堆垛的相关基本信息如表1、表2.表1、烟叶堆垛基本信息汇总垛位号年份产地等级数量(箱)d4012017江西710160d4022017江西710160d4032017广东522228d4062017广东521160d4072017广东521160d4222017江西710204d4292018云南fb3f208d4302018云南fb3f208d4332017广东522192图1是其中的d430烟叶堆垛内部氧气浓度变化曲线图,图1中的纵坐标方向代表氧气的体积百分比浓度、横坐标方向是调控日期与时间。图1显示,在密闭仓间内氧气浓度低于5%(或者脱氧机的原料气进口的氮气浓度越来越高、脱氧机的原料气进口的氮气浓度高于95%时),脱氧机上的空气进口补充进来的空气会明显地影响到脱氧机的制氮效率,脱氧机在低浓度氧气条件下的制氮效率会变得越来越低、流量越来越小,因此在纯度和流量都需兼顾的情况下,脱氧机的脱氧、制氮效果会表现出一定的局限性,低氧环境条件下的脱氧机运行能效比快速下降、氮气浓度达标的运行工作时间拖得太长。表2、烟叶堆垛机械调控开、关机时间开机时间关机时间调控时长同步调控垛位数2020-06-1512:302020-06-1517:30692020-06-1608:002020-06-1617:00992020-06-2212:002020-06-2217:00532020-06-2408:002020-06-2415:00732020-06-2608:002020-06-2615:00732020-07-0611:122020-07-0617:0233另外,船体的密闭舱室、飞机机舱内部也会有各种有害生物滋扰危害环境卫生状况,受制于密闭舱室、飞机机舱内部金属零部件较多的缘故,可供使用的防治手段不多,应用传统的机械充氮气调防治有害生物也存在时间太长(至少密闭15天以上)的问题,轮船、飞机没有充裕的时间允许上述防治技术和手段的落地应用。技术实现要素:为解决现有的仓贮农产品机械充氮防虫及密闭舱室内部机械充氮防治有害生物用时过长的问题,本发明的目的在于提供一种密闭循环模式下快速机械脱氧、充氮方法,该方法具有提升低氧环境条件下的脱氧、制氮设备运行的能效比的特点。该方法通过在密闭循环脱氧制氮系统中接入“机械充氮允压联动装置”,该装置有一个带有管道阀门8的补气端口,在该补气端口的一端(即管道阀门8的进气端口8a)对接一个脱氧制氮设备(氮气或二氧化碳气体发生装置)9,补气端口的另一端(即管道阀门8的排气端口8b)与密闭循环脱氧制氮系统(或称密闭循环管道系统、脱氧制氮循环管道系统)的正压管道段(密闭仓间的气体输入管道7或者是密闭仓间a)对接,通过该补气端口同步往密闭循环脱氧制氮系统中注入氮气或二氧化碳气体以补偿和缓解系统连续运行过程中因为脱除并排放出氧气而形成的负压状态,使密闭循环脱氧制氮系统运行过程中的内、外压力处于平衡状态,提升低氧环境条件下的脱氧、制氮设备运行的能效比。为实现上述目的,本发明所采取的技术方案是,一种密闭循环模式下快速机械脱氧、充氮方法,在密闭仓间a的任一对称的两侧面或其上顶、下底面的位点,分别引入气体输出管道(或称密闭仓间气体排出管道)1、气体输入管道7,将脱氧机3的原料气进口2与密闭仓间a相连的气体输出管道1接通(另一方案,脱氧机3的功能可以选择使用制氮机、制氧机来替代),将脱氧机3中的以氮气为主要组分的气体排出口6与密闭仓间a相连的气体输入管道7接通,脱氧机3上面的补气阀口5与环境大气接通用于往脱氧机内部补充气体以满足设备内外的压力平衡,上述密闭仓间a由气体输入管道7、气体输出管道(或称密闭仓间气体排出管道)1与脱氧机3之间相互连通构建成一个密闭循环脱氧制氮系统b,脱氧机3通过原料气进口2、气体输出管道1从密闭仓间a的内部抽提空气至脱氧机中进行氮气与氧气之间的分离处理,脱氧机分离空气形成的氮气组分通过脱氧机3的气体排出口6、气体输入管道7输入进密闭仓间a的内部,脱氧机3形成的以氧气为主要组分的尾气通过排气管4排放至环境大气中(脱氧机3上设有排气管4);在上述密闭循环脱氧制氮系统b中接入机械充氮允压联动装置c,机械充氮允压联动装置c由包含一个管道阀门8与一台脱氧制氮设备(氮气、二氧化碳气体发生设备,或者称之为空气分离设备,包含制氮机、脱氧机、制氧机)9组合而成,其中的管道阀门8的进气端口8a与脱氧制氮设备9的氮气排出口对接,管道阀门8的排气端口(或称出气端口)8b用于接通到密闭循环脱氧制氮系统b中的脱氧机3与密闭仓间a之间相互连通的正压管道通路(即气体输入管道7)中,或者是将管道阀门8的排气端口(或称出气端口)8b直接与密闭仓间a对接;脱氧制氮设备9的原料气进口10从密闭循环脱氧制氮系统b的外部环境中取气;机械充氮允压联动装置c中的脱氧制氮设备9通过原料气进口10从密闭循环脱氧制氮系统b的外部大气环境中取气并对其中的氮气和氧气进行分离处理,分离出来的氮气或者是氮气与二氧化碳的混合气体通过管道阀门8的进气端口8a、排气端口(或称出气端口)8b输入进密闭循环脱氧制氮系统b中,以补偿和缓解密闭循环脱氧制氮系统b连续运行时在密闭仓间a及密闭循环脱氧制氮系统b内部的气体流通管路中形成的负压状态(图2)。所述氮气与二氧化碳的混合气体的体积配比为:氮气1-99%、二氧化碳1-99%。按上述技术方案,机械充氮允压联动装置c往密闭循环脱氧制氮系统b中注入氮气或者是氮气与二氧化碳的混合气体(氮气与二氧化碳的体积配比为:氮气1-99%、二氧化碳1-99%),使得密闭循环脱氧制氮系统b内外的压力差得以平衡的情况下,完全关闭脱氧机3上面的补气阀5以减少进入密闭循环脱氧制氮系统中的空气对密闭循环脱氧制氮系统b内部高浓度氮气的稀释作用,提高密闭循环脱氧制氮系统b的脱氧制氮效率。按上述技术方案,机械充氮允压联动装置c中的脱氧制氮设备9使用制氮机,按照制氮机的工艺原理完成机械充氮允压联动装置c提供氮气源的功能,将机械充氮允压联动装置c中的管道阀门8的进气端口8a与制氮机的氮气排气出口对接,使用psa制氮机或膜分离制氮机通过原料气进口10抽提环境中的空气进入制氮机中进行氮气与氧气的分离处理,其中由制氮机分离出来的氮气经管道阀门8的进气端口8a、排气端口(或称出气端口)8b接入到密闭循环脱氧制氮系统b中、分离出来的氧气作为设备的尾气通过排气管11排放到大气环境中(制氮机上设有排气管11),通过上述往密闭循环脱氧制氮系统b中不断注入氮气的过程来缓解密闭循环脱氧制氮系统连续运行过程中形成的负压状态。按上述技术方案,机械充氮允压联动装置c中的脱氧制氮设备9使用脱氧机,按照脱氧机的工艺原理完成机械充氮允压联动装置c中提供氮气源的功能,将机械充氮允压联动装置c中的管道阀门8的进气端口8a与脱氧机的氮气排出口对接,通过原料气进口10抽提环境中的空气至脱氧机中进行氮气与氧气的分离处理,其中由脱氧机分离出来的氮气经氮气排出口、管道阀门8的进气端口8a、排气端口(或称出气端口)8b接入到密闭循环脱氧制氮系统b中,脱氧机分离出来的氧气组分作为尾气通过排气管11排放到大气环境中,上述往密闭循环脱氧制氮系统b中不断注入氮气的过程,可以缓解密闭循环脱氧制氮系统连续运行过程中形成的负压状态、创造一种密闭循环脱氧制氮系统运行过程中的内外压力平衡状态。按上述技术方案,机械充氮允压联动装置c中的脱氧制氮设备9使用制氧机,按照制氧机的工艺原理完成机械充氮允压联动装置c中提供氮气源的功能,将机械充氮允压联动装置c中的管道阀门8的进气端口8a与制氧机的氮气排出口对接,管道阀门8的排气端口(或称出气端口)8b接入到密闭循环脱氧制氮系统b中,通过原料气进口10抽提环境中的空气至制氧机中进行氮气与氧气的分离处理,其中由制氧机分离出来的氮气经氮气排出口、管道阀门8的的进气端口8a、排气端口8b接入到密闭循环脱氧制氮系统b中,制氧机分离出来的氧气作为设备的尾气经排气管11排放到大气环境中,上述往密闭循环系统中不断注入氮气和二氧化碳混合气的作业过程可以缓解系统连续运行过程中形成的负压状态、创造一种密闭循环脱氧制氮系统运行过程中的内外压力平衡状态。按上述技术方案的一种,使用制氮机来替代脱氧机3的功能,制氮机通过原料气进口2与气体输出管道1接通并从密闭仓间a的内部抽提空气至制氮机中进行分离处理,制氮机将空气进行分离处理以后形成的氮气组分通过气体排出口6、气体输入管道7输入进密闭仓间a的内部,制氮机形成的以氧气为主要组分的尾气通过排气管4排放至环境大气中(制氮机上设有排气管4)。按上述技术方案的一种,脱氧机3的功能可以选择使用制氧机来替代,制氧机通过原料气进口2与气体输出管道1接通并从密闭仓间a的内部抽提空气至制氧机中进行分离处理,制氧机将空气进行分离处理以后形成的氮气组分通过气体排出口6、气体输入管道7输入进密闭仓间a的内部,制氧机形成的以氧气为主要组分的尾气通过排气管4排放至环境大气中(制氧机上设有排气管4)。按上述技术方案的一种,将机械充氮允压联动装置c中的管道阀门8的进气端口8a与二氧化碳钢瓶气源的放气阀对接,管道阀门8的出气端口8b接入到密闭循环脱氧制氮系统b中,开启二氧化碳钢瓶气阀门往密闭循环脱氧制氮系统b中注入二氧化碳气以补偿系统连续运行过程中形成的负压力。按上述技术方案的一种,气体输入管道7、气体输出管道(或称气体排出管道)1通过并联或串联的形式对接2个以上(如2-100个)的密闭仓间(密闭舱室)a。按上述技术方案的一种,密闭仓间(密闭舱室)a内的氧气体积百分比浓度最佳为不断下降至3%以下。一种密闭循环模式下快速机械脱氧、充氮方法,在密闭循环脱氧制氮系统中接入的一个机械充氮允压联动装置c可以是一个简单的补气端口,该补气端口是密闭循环脱氧制氮系统与外界进行气体交流的进、出口,通过该补气端口与氮气、二氧化碳气源对接并完成氮气、二氧化碳等气体的注入,补气端口管道中可以设置控制阀,控制阀的开、闭根据密闭循环脱氧制氮系统中的压力进行联动响应。上述在密闭循环脱氧制氮系统中接入机械充氮允压联动装置c并根据密闭循环脱氧制氮系统中的压力进行联动响应的控制,是在当密闭循环脱氧制氮系统内部压力小于系统外部压力时要及时开启控制阀补气,在密闭循环脱氧制氮系统内部压力大于或等于系统外部压力时要关闭机械充氮允压联动装置c或控制阀8停止补气作业。上述技术方案中的术语及定义如下:脱氧制氮设备9:是制氧机、脱氧机(氧气脱除机)或制氮机的统称;主要是指运用变压吸附原理,利用各种吸附剂对氧气、氮气、二氧化碳气体的选择性吸附,以及不同压力下吸附剂对氧气、氮气、二氧化碳吸附量的差异,实现对氧气、氮气、二氧化碳气体的分离和提纯的机械设备。也可以选择使用膜分离技术,依靠膜对所有气体都可以渗透、只不过渗透的程度不同的特性,当混合气体在一定的驱动力(膜两侧的压力差或压力比)作用下,渗透速率快的气体组分较易透过膜并在膜的渗透侧被富集,而渗透速率相对慢的气体组分被滞留在膜的滞留侧被富集从而达到对混合气体分离的目的,根据分离条件中的压力不同,膜分离技术分成高压、低压两种不同的工艺流程;经过脱氧制氮设备对密闭仓间中的空气进行循环处理过程中,密闭仓间中的氧气成分被分离并脱除到外部环境中去、密闭仓间中的氮气和二氧化碳体积百分比浓度得以提升,直至达到防控害虫生长繁殖有效的低氧条件;密闭仓间:收获以后的粮食在仓库内部有散装存放和袋装贮存的形式,烟叶复烤成为片烟则使用包装箱之后再堆码贮存;对于散装贮存的粮食使用塑料薄膜对粮面进行严格地覆盖密闭(仓库墙体漏气或气密性达不到气调贮存标准的,要使用塑料薄膜对粮食堆垛进行上下、左右、前后进行六面密闭),确保覆盖塑料帐幕与四周墙体严格粘贴无缝隙;对于袋装粮、烟叶包装箱堆码成为一个个独立堆垛的,使用塑料薄膜帐幕将堆存的粮食、烟叶密封覆盖形成一种塑料帐幕覆盖下的密闭空间,其它的金属、混凝土结构的农产品仓库进行严格密封以后形成密闭性能良好的仓库,上述密闭空间及密闭仓库均简称为“密闭仓间”;上述“密闭仓间”的概念也包含船舱的密闭舱室、民用飞机的机舱等容易滋生繁殖有害生物(各种病毒、霉菌、苍蝇、蟑螂、蚊虫、老鼠等等)的密闭空间;气调防虫:人为改变密闭环境中的氧气、氮气、二氧化碳等气体的比例成分,达到形成不利于害虫生长活动、抑制害虫为害的一种气调调控技术;仓间气密性:表达密闭仓间(或舱室)环境的气密性水平,要求密闭仓间符合二级气密性的标准,使用压力衰减试验(pt试验)的办法可以对独立的密闭仓间进行气密性监测,参考中华人民共和国国家标准gb/t25229—2010《粮油储藏---平房仓气密性要求》的相关规定进行。气密性不够的,通过查漏补洞或更换密闭材料的办法解决。正压:在密闭循环管道系统内部的压力比大气环境中的压力(即一个大气压)还要大。负压:是密闭循环管道系统中低于常压(即一个大气压)的气体压力状态。进、出气端口:是设备与另一个设备或系统进行气体交换、气体流通的进出口。补气阀(口):脱氧机应用在密闭循环系统中进行脱氧制氮运行时,需要两条管道与密闭仓间相连(进气和回气),是在循环抽提气体进行反复的脱氧运行模式中不断提高设备的输出氮气纯度,上述密闭循环脱氧制氮系统在将氮、氧分离并释放出氧气以后会在系统内部形成混合气体密度的降低及气压损失,脱氧机设备上增加一个空气进口、补气阀(口)以及时弥补系统内气体密度的降低及压力损失。设备目标产成气、设备尾气:制氮机、脱氧机或制氧机在不同的应用场景下有不同的目标产成气(如制氧机应用在医疗卫生场所的目标产成气为氧气,此时设备生成的氮气则视作为废气),在本发明的技术体系中,脱氧机、制氮机或制氧机对抽提至设备内部的气体进行分离处理,设备运行处理要生成的目标产成气为均为氮气及氮气与二氧化碳的混合气,目标产成气被回输入到密闭仓间中发挥充氮气调防虫作用,上述过程中产生的氧气则作为设备的尾气(废气)成分排出到环境大气中,此时将三种设备的尾气排气管、排气口、排气阀等改为能够排放出氧气的通道,将三种设备的氮气排出通道改造为能够与管道对接的出气口即可。密闭循环系统运行过程中的内外压力:在由“密闭仓间a→气体输出管道1→脱氧机(脱氧制氮设备)3→气体输入管道7→密闭仓间a”共同构建的一种密闭循环系统,系统在连续运行以后会因为分离并释放出氧气而导致系统内、外气体密度的差异,进而导致系统内、外存在压力差或者是一种气压存在一种动态的失衡与平衡状态。与现有技术相比,本发明的优点在于:1)创新提出在密闭循环脱氧制氮系统(密闭循环机械脱氧系统、密闭循环机械充氮系统)内接入“机械充氮允压联动装置”,通过定向往密闭循环脱氧制氮系统内注入氮气或二氧化碳气体的方法使得系统因连续运行而形成的内外压力差能够及时得以平衡,该技术模式可以将传统机械充氮气调防虫时使用脱氧制氮设备依靠开放或半开放式取气模式真正改变为全封闭循环取气的脱氧制氮模式,这样可以大大降低设备系统的运行负荷和工艺管控难度;2)通过在密闭循环脱氧制氮系统(密闭循环机械脱氧系统、机械充氮系统)内接入“机械充氮允压联动装置”,制氮机应用在密闭循环脱氧制氮系统中可以不再依靠开放或半开放式取气模式,大大拓宽了传统制氮机的应用场景;3)本发明技术模式下的脱氧机的运行不再必须使用半开放取气模式,即使全密闭运行模式下也可以彻底关闭脱氧机或制氮机上面用来补偿自然空气的补气阀(口);4)创新提出应用制氧机、脱氧机等脱氧制氮设备制取目标产成气氮气或二氧化碳气的模式,并通过补气端口(即,管道阀门8的出气端口8b)将制取的氮气注入到密闭循环脱氧制氮系统中去的技术路径,摆脱既往机械充氮防虫单一依靠制氮机的模式,转而使用市场上供应的不同类别的空气(氮气、氧气)分离设备,大大拓宽了设备的选择范围和设备配置组合模式,可以使得设备配置成本更低,设备集成及操作更加便利;5)本发明易于工程实现、简单实用。附图说明图1是烟叶堆垛内部氧气浓度变化曲线图(或称垛内氧气浓度变化分析图)。图2是本发明在密闭循环脱氧制氮系统中接入“机械充氮允压联动装置”的工艺流程图。图2中:a-密闭仓间(密闭舱室)、1-气体输出管道、2-原料气进口、3-脱氧机、4-排气管、5-补气阀(口)、6-气体排出口(或称设备排放氮气出口、产气口)、7-气体输入管道、8-管道阀门(“机械充氮允压联动装置”中与系统对接的管道阀门)、8a-管道阀门8的进气端口、8b-管道阀门8的排气端口、9-脱氧制氮设备、10-脱氧制氮设备的原料气进口、11-脱氧制氮设备的排气管(尾气排放口)、b-密闭循环脱氧制氮系统、c-机械充氮允压联动装置;图中的箭头方向代表设备系统运行时密闭仓间(密闭舱室)内部、管道及设备端口的气流方向。具体实施方式以下结合附图和具体实施例对本发明提出的一种密闭循环模式下快速机械脱氧、充氮方法作进一步说明。附图采用简化的形式仅仅是为了方便、明晰地说明本发明的相关实施例。相关的简单描述和图示仅仅是实施例并且不旨在限制本发明,以下实施方式仅仅是为了说明本发明的原理而采用的示例性实施方式,然而本发明并不局限于此。对于本领域内的普通技术人员而言,在不脱离本发明的技术路线的情况下,可以做出各种变型和改进,这些变型和改进也视为本发明的保护范围。实施例1:收获以后的粮食在仓库中散存,使用塑料薄膜对粮面进行覆盖密闭(仓库墙体漏气或气密性达不到气调贮存标准的,使用塑料薄膜对粮食堆垛进行上下、左右、前后的六面密闭),确保覆盖塑料帐幕与四周墙体严格粘贴无缝隙;对于收获以后的袋装粮、箱装烟叶则堆码成为一个个独立的堆垛并按照堆垛尺寸制作塑料薄膜帐幕对其进行覆盖(可以使用塑料薄膜衬底),确保形成覆盖塑料帐幕以后的密闭堆垛严密无缝隙、无漏气;对上述使用塑料薄膜密封覆盖粮食、烟叶堆垛形成的密闭仓间(密闭空间)以及利用各种金属、砖瓦、钢筋混凝土制作成的密闭仓间(密闭仓体)或盛器的表面和四周进行封固以后的气密性进行监测,采用负压检测法测试密闭仓间的气密性,使得密闭仓间不低于二级气密性标准,密闭仓间的气密性监测应用压力衰减试验(pt试验)的办法进行,具体监测办法参考中华人民共和国国家标准gb/t25229—2010《粮油储藏---平房仓气密性要求》的相关规定进行,气密性不够的,通过查漏补洞或更换密闭材料的办法解决。如图2所示,一种密闭循环模式下快速机械脱氧、充氮方法,在上述仓库或塑料帐幕密封覆盖农产品而形成的密闭仓间(密闭舱室)a的任一对称的两侧面或其上顶、下底面的位点,分别引出1~10根气体输入管道7和1~10根密闭仓间气体输出管道1,上述气体输入管道7、气体输出管道1根据密闭仓间a空间体积的大小选择内径10~100mm的塑料、橡胶或金属管材的管道,气体输入管道7、气体输出管道(或称气体排出管道)1通过管道接头与密闭仓间及其上面的塑料帐幕表面相对接,管道接头使用武汉东昌仓贮技术有限公司生产的各种规格的塑料接头,对塑料密闭帐幕的表面和四周、管道与塑料密闭帐幕接合处进行查漏补洞工作,采用负压检测法测试密闭空间的气密性,使得密闭空间不低于二级气密性标准;将脱氧机3上面的以氮气为主要组分的气体排出口(或称设备排放氮气出口、产气口)6通过气体输入管道7与密闭仓间(密闭舱室)a接通,将脱氧机3的原料气进口2通过密闭仓间气体输出管道1与密闭仓间(密闭舱室)a的另一端接通,脱氧机3将密闭仓间a中的空气通过气体输出管道1(该管道也称之为设备系统的气体回流管道)、原料气进口2抽提吸入到脱氧机3中,脱氧机3将来自于密闭仓间a的空气中的氧气与其它气体组分分离脱除出来,分离脱除出来的氧气作为设备的尾气通过排气管4排放到密闭仓间a外部环境中去,经过脱除分离氧气之后余下的氮气作为设备的产成气体排出口(或称气体排出口、排放氮气出口)6、气体输入管道7被回输到密闭仓间a中去。上述气体输出管道1的一端与脱氧机3的原料气进口2对接、气体输入管道7的一端与脱氧机3的气体排出口6对接,气体输出管道1、气体输入管道7的另一端则通过管道接头与密闭仓间或者是塑料密闭帐幕的表面相对接,上述两组进、出气管道与密闭仓间或者是塑料密闭帐幕表面的对接点分别位于密闭仓间、塑料密闭帐幕表面相互对应的两个侧面上。密闭仓间(密闭舱室)a与气体输入管道7、气体输出管道1、脱氧机3之间相互连通构建成一个密闭的密闭循环脱氧制氮系统b,在密闭循环脱氧制氮系统b中接入机械充氮允压联动装置c,机械充氮允压联动装置c由包含一个管道阀门8与一台脱氧制氮设备9组合而成,其中的管道阀门8的进气端口8a与脱氧制氮设备9的氮气排出口对接,管道阀门8的排气端口8b用于接通到脱氧机3与密闭仓间a之间相互连通的正压管道通路(由于脱氧机3输出的氮气气流通过管道7流经至密闭仓间a,在系统运行时会在管道7中形成正压力)中,或者是将管道阀门(8)的排气端口(8b)直接与密闭仓间a对接,脱氧制氮设备9的原料气进口10从密闭循环脱氧制氮系统b的外部的大气环境中取气,脱氧制氮设备9对其中的氮气和氧气进行分离处理,分离出来的氮气或者是氮气与二氧化碳的混合气体通过管道阀门8的排气端口8b输入进密闭循环脱氧制氮系统b中,以补偿和缓解密闭循环脱氧制氮系统b连续运行时在密闭仓间a及密闭循环脱氧制氮系统b内部的气体流通管路中形成的负压状态(图2)。脱氧机3根据密闭仓间的大小灵活确定设备的功率负荷(如20℃,氮气产量选择100m3/h,设备产成氮气的体积纯度≥95%),可选择天津捷盛科技有限公司或者天津立喆舜保鲜科技有限公司的产品,“脱氧机”的商品名称也叫“氧气脱除机”,脱氧机或氧气脱除机内部的吸附塔中主要是装填碳分子筛作为固体吸附剂,在吸附精度不高的应用场所也可以装填使用活性炭、沸石分子筛作为固体吸附剂。机械充氮允压联动装置c中的脱氧制氮设备9使用制氮机,按照制氮机的工艺原理完成机械充氮允压联动装置c为密闭循环脱氧制氮系统b提供氮气源的功能,将机械充氮允压联动装置c中的管道阀门8的进气端口8a与制氮机的氮气排气出口对接,使用psa制氮机或膜分离制氮机抽提环境中的空气进行氮气与氧气的分离处理,其中由制氮机分离出来的氮气经管道阀门8的排气端口(或称出气端口、补气端口)8b注入到密闭循环脱氧制氮系统中,分离出来的氧气作为设备的尾气通过制氮机的排气管11排放到大气环境中,通过上述往密闭循环脱氧制氮系统中不断注入氮气的过程来缓解系统连续运行过程中形成的负压状态,提高机械充氮防虫效率。“机械充氮允压联动装置”中的制氮机(脱氧制氮设备9使用制氮机)的功率和产气量可略低于脱氧机3(如20℃,制氮机的氮气产量50m3/h,氮气纯度≥99.9%),“机械充氮允压联动装置”中的制氮机9可以与脱氧机3同步运行也可以较脱氧机3延后开机运行,其目的在于补充密闭循环脱氧制氮系统b中的脱氧机3在运行过程中因分离并排放出氧气带来的密闭循环脱氧制氮系统内部压力损失;使用安尔特气体设备(苏州)有限公司生产的变压吸附(psa)制氮机,制氮机是根据变压吸附原理,采用高品质的碳分子筛作为吸附剂,在一定的压力下,从原料气中制取氮气。经过纯化干燥的压缩原料气,在吸附器中进行加压吸附、减压脱附;也可以使用安尔特气体设备(苏州)有限公司生产的膜分离制氮机,设备依靠不同气体在膜中溶解和扩散系数的差异而具有不同的渗透速度来实现气体的分离。仍然以黄陂前川烟叶仓库为例,按照2020-06-15开始的对该批次烟垛的密闭方法、机械充氮调控时间节点和节奏对同一批次的烟垛进行二次调控实验,相关实验情况见表3、4:表3、烟叶堆垛基本信息汇总实验中使用的是天津捷盛科技有限公司100m3/h的脱氧机,“机械充氮允压联动装置”中的制氮机9选择50m3/h、氮气纯度≥99.9%,“机械充氮允压联动装置”中的制氮机(脱氧制氮设备9使用制氮机)在密闭仓间a内氧气浓度下降到5%以下时与脱氧机3同步运行,以同一个d430堆垛为氧气浓度变化监测比对点,结果是新的技术模式下不到10天的时间(2020-08-02日),即可以将d430烟叶堆垛内部及烟箱内部的氧气浓度稳定地降到2%以下;表4、烟叶堆垛机械调控开、关机时间开机时间关机时间调控时长调控垛位数2020-07-239:302020-07-2317:30692020-07-2408:002020-07-2417:00992020-07-3010:002020-07-3015:00532020-08-0209:002020-08-0211:00732020-08-1108:302020-08-1115:30732020-08-159:002020-08-1512:0033本实施例是针对收获以后进入贮存期的小麦或烟叶的贮存与养护的应用技术,对于轮船舱室及飞机机舱等场所均可以按照本实施例进行密闭处理、气密性检测并执行密闭循环模式下快速机械脱氧、充氮作业。实施例2:与实施例1基本相同,不同之处在于:应用机械充氮允压联动装置c往密闭循环脱氧制氮系统b中注入氮气或者是氮气与二氧化碳的混合气体(混合气体中:氮气与二氧化碳的体积配比为:氮气1-99%、二氧化碳1-99%),使得密闭循环脱氧制氮系统b内外的压力差得以平衡的情况下,完全关闭脱氧机3上面的补气阀5以杜绝外界的空气进入到密闭循环脱氧制氮系统b内部,进而防范密闭循环脱氧制氮系统内的高浓度氮气被稀释。实施例3:与实施例1、2基本相同,不同之处在于:机械充氮允压联动装置c中的脱氧制氮设备9使用脱氧机,按照脱氧机的工艺原理完成机械充氮允压联动装置c中脱氧制氮设备9提供氮气源的功能,将机械充氮允压联动装置c中的管道阀门8的进气端口8a与脱氧机的氮气排出口对接,环境中的空气被抽提至脱氧机中进行氮气与氧气的分离处理,其中由脱氧机分离出来的氮气经氮气排出口、管道阀门8的排气端口8b接入到密闭循环脱氧制氮系统中,脱氧机分离出来的氧气组分通过脱氧机的排气管11排放到大气环境中,上述往密闭循环脱氧制氮系统中不断注入氮气的过程,可以缓解系统连续运行过程中形成的负压状态、创造一种密闭系统运行过程中的内外压力平衡状态。“机械充氮允压联动装置”中脱氧机(脱氧制氮设备9使用脱氧机)的设备功率负荷可以略小于脱氧机3(如20℃,氮气产量选择50m3/h,设备产成氮气纯度≥95%),设备选择烟台意塞奥气调设备有限公司的产品,脱氧机或氧气脱除机内部的吸附塔中主要是装填碳分子筛作为固体吸附剂,在吸附精度不高的应用场所也可以装填使用活性炭或沸石分子筛作为固体吸附剂。相关的图示中未详细画出“机械充氮允压联动装置”中脱氧机的排气管的结构图,因为本发明选择的脱氧机的目标产成气是氮气,用于排放氧气等各种尾气的可以是排气管、排气口、排气阀等等,无需一一描述。实施例4:与实施例1、2基本相同,不同之处在于:机械充氮允压联动装置c中的脱氧制氮设备9使用制氧机,按照制氧机的工艺原理完成脱氧制氮设备9提供氮气源的功能,将机械充氮允压联动装置c中的管道阀门8的进气端口8a与制氧机的氮气与二氧化碳混合气的排放口对接,制氧机从空气中取气、脱氧并将分离出来的氮气与二氧化碳混合气经制氧机的排放口、管道阀门8的进气端口8a、管道阀门8的排气端口8b接入到密闭循环脱氧制氮系统中,制氧机分离生成的氧气通过制氧机的排气管排放到大气环境中,上述往密闭循环脱氧制氮系统中不断注入氮气和二氧化碳混合气的作业过程可以缓解密闭循环脱氧制氮系统连续运行过程中形成的负压状态、创造一种密闭系统运行过程中的内外压力平衡状态。制氧机有vpsa、psa制氧设备,其中的低压吸附真空解吸制氧设备(vpsa制氧设备)利用vpsa专用分子筛与干燥剂形成的混合床层选择性吸附空气中的氮气、二氧化碳和水等杂质,令氧在床层末端聚积并收集,在抽真空的条件下对吸附饱和状态的分子筛床层进行解吸,从而循环制得纯度较高的氧气(90~95%体积)。变压吸附制氧设备(psa制氧设备)以吸附剂分子筛为例,其原理是利用分子筛对不同气体分子“吸附”性能的差异而将气体混合物分开。它是以空气为原材料,利用一种高效能、高选择的固体吸附剂对氮和氧的选择性吸附的性能把空气中的氮和氧分离出来。沸石分子筛依据其晶体内部孔穴的大小对分子进行选择性吸附,也就是吸附一定大小的分子而排斥较大物质的分子。这样气相中就可以得到氧的富集成分。一段时间后,分子筛对氮的吸附达到平衡,根据沸石分子筛在不同压力下对吸附气体的吸附量不同的特性,降低压力使沸石分子筛解除对氮的吸附,这一过程称为再生。变压吸附法通常使用两塔并联,交替进行加压吸附和解压再生,从而获得连续的氧气流。可以采用广州市维通工业气体技术有限公司提供的psa制氧机,设备主要由空压机、冷干机、除油器、吸附系统、氧气缓冲罐、控制系统组成。空压机为整个系统提供原料空气,根据变压吸附制氧设备的产气量,选择符合设计条件的空压机进行供气;空压机对原料空气增压后,高温高压的压缩空气进入冷干机进行冷却、干燥、除杂,得到低温高压的压缩空气;低温高压的压缩空气从甲塔底部进入,当流经吸附剂层时,空气中的氮气,二氧化碳,水蒸气等被吸附,氧气则通过吸附床层汇集到吸附塔顶部作为产品气输出,与此同时,乙塔处于再生工况,当进行吸附的吸附塔快达到吸附饱和时,在控制系统的调节下,低温高压空气转而进到乙塔开始吸附产氧,甲、乙塔如此交替轮流实现连续产氧的目的。也可以采用昆山锦程气体设备有限公司的vpsa变压吸附气体分离工艺制氧机,制氧机依靠其中填充的吸附剂对空气中的氮气、氧气组分吸附能力的不同,可实现对混合气体中氧气的优先吸附而使其与空气中的其它组分得以分离提纯,利用空气中的不同组分在制氧机的吸附剂上的吸附容量随各种被吸附成分的分压上升而增加,可实现吸附剂在高压下吸附而在低压下解吸再生,从而构成吸附剂的吸附与再生循环,达到连续分离气体制取氧气的目的。制氧系统主要由鼓风机、真空泵、切换阀、吸附器和氧气缓冲罐组成。原料空气经吸入口10进入过滤器除掉灰尘颗粒,被罗茨鼓风机增压而进入其中一只吸附器内,吸附器内装填吸附剂,其中水分、二氧化碳、及少量其它气体组分在吸附器入口处被装填于底部的活性氧化铝所吸附,随后氮气被装填于活性氧化铝上部的沸石分子筛所吸附,而氧气为非吸附组分从吸附器顶部出口处(可以经过氧气缓冲罐)作为设备的尾气组分通过排气管11排放到环境大气中。当该吸附器吸附到一定程度,其中的吸附剂将达到饱和状态,此时通过切换阀,经过一均压降压过程,将吸附塔空间内的部分氧气回收(同样通过排气管11排放到环境大气中),同时将吸附塔压力降至微负压,再利用真空泵对之进行抽真空(与吸附方向相反),并将吸附剂吸附的氮气、水分、及二氧化碳气体组分抽出并通过设备的排气口接管道阀门8的进气端口8a、管道阀门8的排气端口8b接入到密闭循环脱氧制氮系统b中。也可以使用上海瑞气气体科技有限公司出品的膜分离制氧设备,膜分离制氧设备先将空气经过脱油、脱水、去杂处理,接着将处理以后的空气输入膜分离器连续制取氧气,在控制系统控制下实现连续稳定对氧气的分离处理,将脱除氧气之后余下的氮气、二氧化碳气体通过管道阀门8的进气端口8a、管道阀门8的排气端口8b接入到密闭循环脱氧制氮系统b或者是直接输入到密闭仓间a的内部;相关的图示中未详细画出制氧机(脱氧制氮设备9使用制氧机)的产成气氮气排气管的结构图,因为本发明选择的制氧机应用在医学、工业等其它场景时的目标产成气是氧气,而氮气则作为尾气通过排气管、排气口、排气阀等排出。制氧机应用在本发明提供的机械充氮允压联动装置c中时,将制氧机的目标产成气设定为氮气(及含有水分、二氧化碳的氮气混合气),此时将原制氧机用作排放尾气的排气管、排气口、排气阀或者是排气孔等等改为能够与管道阀门8的进气端口8a对接的出气口即可。实施例5:与实施例1、2、3或4基本相同,不同之处在于:使用带有管道阀门的三通管将二氧化碳钢瓶气源接入密闭仓间a的气体输入管道7中,使用10-25kg的钢瓶装二氧化碳气源,启动密闭循环脱氧制氮系统中的脱氧机3和开启二氧化碳气源同步进行,氮气和二氧化碳气体同步进入气体输入管道7中混合输入到密闭仓间a中,密闭仓间a内的混合气不断被脱氧机3回抽进行新的循环脱氧处理,直至密闭仓间a内的二氧化碳浓度逐步提升、氧气浓度≤8%(体积百分比浓度),停止人工注入二氧化碳作业以后,及时关停三通管上的管道控制阀。实施例6:与实施例1、2、3或4基本相同,不同之处在于:“机械充氮允压联动装置c”中的脱氧制氮设备9的氮气排出口或者是二氧化碳钢瓶的排气阀可通过连通管直接与密闭仓间a或者是密闭循环系统中的正压管段接通对接,以简单的方式满足系统连续运行过程中系统内、外压力的平衡。实施例6:与实施例1、2、3、4或5基本相同,不同之处在于:可以使用制氮机取代脱氧机3来执行密闭循环系统b中机械脱氧制氮的功能。将制氮机3上面的以氮气为主要组分的气体排出口(或称设备排放氮气出口、产气口)6通过气体输入管道7与密闭仓间(密闭舱室)a接通,将制氮机3的原料气进口2通过气体输出管道1与密闭仓间(密闭舱室)a的另一端接通,制氮机3将密闭仓间a中的空气通过气体输出管道1(该管道也称之为设备系统的气体回流管道)、原料气进口2抽提吸入到制氮机3中,制氮机3将来自于密闭仓间a中的空气中氧气与其它气体组分分离脱除出来,分离脱除出来的氧气作为设备的尾气通过排气管4排放到密闭仓间a外部环境中去,经过脱除分离氧气之后余下的氮气作为设备的产成气体通过气体排出口(排放氮气出口)6、气体输入管道7被回输到密闭仓间a中去。实施例7:与实施例1、2、3、4、5或6基本相同,不同之处在于:可以使用制氧机取代脱氧机3、按照制氧机的工艺原理来执行密闭循环系统中机械脱氧制氮的功能。此时,将制氧机上面的以氮气为主要组分的气体排出口(或称设备排放氮气出口、产气口)6通过气体输入管道7与密闭仓间(密闭舱室)a接通,将制氧机的原料气进口2通过气体输出管道1与密闭仓间(密闭舱室)a的另一端(指的是与气体输入管道7与密闭仓间对接点对应的密闭仓间的另一侧面)接通,制氧机(使用制氧机取代脱氧机3)将密闭仓间a中的空气通过气体输出管道1(该管道也称之为设备系统的气体回流管道)、原料气进口2抽提吸入到制氧机中,制氧机将来自于密闭仓间a的空气中的氧气与其它气体组分分离脱除出来,分离脱除出来的氧气作为制氧机应用在本发明技术应用场景下的设备尾气通过排气管4排放到密闭仓间a的外部环境中去,经过脱除分离氧气之后产生的氮气等其它组分作为设备应用在密闭循环脱氧制氮系统b的场景下的产成气体通过气体排出口(排放氮气出口)6、输入气管道7被回输到密闭仓间a中去。实施例8:与实施例1、2、3、4、5、6或7基本相同,不同之处在于:气体输入管道7、气体输出管道1可以通过并联或串联的形式对接2个以上(如2-100个)的密闭仓间a。实施例9:与实施例1、2、3、4、5、6、7或8基本相同,不同之处在于:为了提高一种密闭循环模式下快速机械脱氧、充氮方法的效率,进而可以根据密闭气调可以利用的时间来设定密闭循环模式下机械脱氧富氮的氧气浓度调控目标分别为3%、2%、1%或者是0.5%以下(体积百分比浓度),以不断提升机械气调防虫的速率。当前第1页1 2 3 
起点商标作为专业知识产权交易平台,可以帮助大家解决很多问题,如果大家想要了解更多知产交易信息请点击 【在线咨询】或添加微信 【19522093243】与客服一对一沟通,为大家解决相关问题。
此文章来源于网络,如有侵权,请联系删除



tips