冷氢化工艺中的渣浆回收利用方法及所使用的回收利用系统与流程



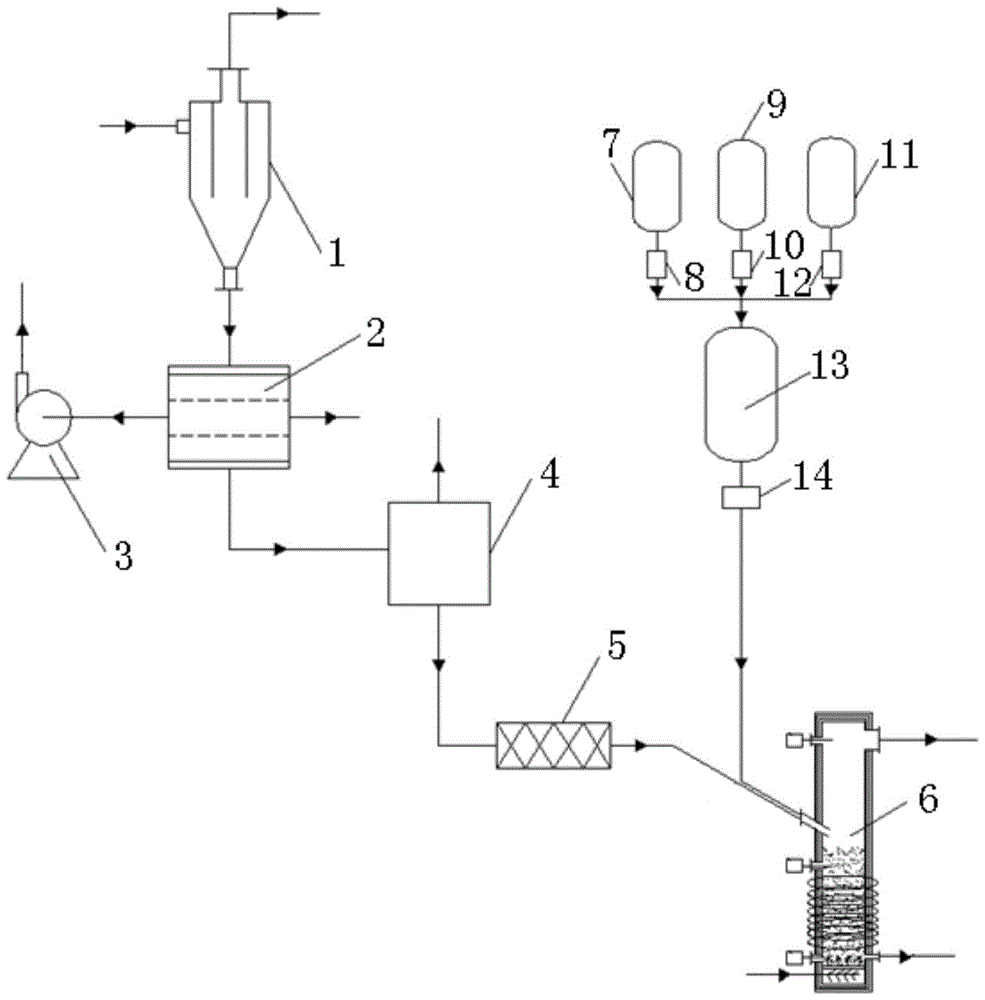
本发明属于多晶硅生产技术领域,具体涉及一种冷氢化工艺中的渣浆回收利用方法及所使用的回收利用系统。
背景技术:
冷氢化技术由于其能耗低、产能大成为目前三氯氢硅生产的主流工艺。在冷氢化反应过程中,为了提高四氯化硅的转化率,反应过程中还要加入过渡金属催化剂如铜基或镍基催化剂。在反应过程中,催化剂和硅粉随氯硅烷被带出反应器,此外,在冷氢化反应中,会不可避免的生成一定量的氯硅烷高沸物。这类高沸物和硅粉、催化剂一起进入后端的冷却系统,并在急冷塔中被捕集下来形成渣浆。
目前大部分的多晶硅生产企业对渣浆的处理都是将其中最容易回收的三氯氢硅和四氯化硅通过加热挥发的方式进行回收,而对于固体料渣中剩余的氯硅烷以及硅粉和催化剂,则用碱中和后直接进行填埋。此种处理方式不仅减少了氯硅烷的回收利用率,增加了生产成本,还会产生大量的工业三废,给企业造成很大的环保成本。现有技术中对于冷氢化产生的渣浆,主要是回收渣浆中的氯硅烷液,没有考虑渣浆中硅粉、催化剂的回收利用,造成资源的极大浪费。
技术实现要素:
本发明所要解决的技术问题是针对现有技术中存在的上述不足,提供一种冷氢化工艺中的渣浆回收利用方法及所使用的回收利用系统,采用绿色、经济的方式将渣浆中的氯硅烷、硅元素、催化剂实现全部回收和再利用,提高了渣浆的综合利用率。
解决本发明技术问题所采用的技术方案是提供一种冷氢化工艺中的渣浆回收利用方法,包括以下步骤:
将冷氢化工艺中的渣浆进行固液分离,分别得到分离开的固体、分离开的液体,固体包括:硅和金属氯化物,金属氯化物包括催化剂氯化亚铜和/或氯化镍;液体包括氯硅烷;
优选的是,固体包括30~60mas%的硅,35~55mas%的金属氯化物,其中金属氯化物包括催化剂氯化亚铜和/或氯化镍,催化剂氯化亚铜和/或氯化镍占固体总质量的15~25mas%。
将分离开的固体与锆英砂、碳质还原剂、氯气加热,锆英砂、碳质还原剂、氯气在固体中的氯化亚铜的催化下反应生成四氯化锆、四氯化硅、一氧化碳,固体中的硅与氯气反应生成四氯化硅,该反应放热为整个系统补充热量。
优选的是,所述将冷氢化工艺中的渣浆进行固液分离的步骤具体为:
将冷氢化工艺中的渣浆进行悬液分离,分别得到分离开的高浓渣浆、分离开的氯硅烷液体,再对高浓渣浆真空过滤,再对真空过滤得到的固体进行干燥得到分离开的固体。
优选的是,锆英砂、碳质还原剂与分离开的固体的质量比为26:(7~8.4):(7~15)。
优选的是,所述步骤将分离开的固体与锆英砂、碳质还原剂、氯气加热反应时,还包括加入补热剂的步骤,其中,补热剂与分离开的固体的质量比为(0.15~0.3):1。
优选的是,加热的温度为1100~1250℃。
优选的是,所述的冷氢化工艺中的渣浆回收利用方法,还包括以下步骤:
将所述固液分离步骤得到的分离开的液体通过精馏进行分离,得到高纯度的三氯氢硅、四氯化硅。高纯度的三氯氢硅作为原料生产多晶硅,高纯度的四氯化硅继续作为冷氢化工艺的原料。
优选的是,所述的冷氢化工艺中的渣浆回收利用方法,还包括以下步骤:
将反应生成的物料进行多级冷却分离,分别得到分离开的四氯化锆、四氯化硅、氯化亚铜、和/或氯化镍、其他金属氯化物杂质。多级冷却分离根据各物质沸点的不同进行分离,其中四氯化锆的沸点为331℃,四氯化硅的沸点为57.6℃,氯化亚铜的熔点为426℃、沸点为1490℃。
本发明还提供一种上述的冷氢化工艺中的渣浆回收利用方法所使用的回收利用系统,包括:
固液分离装置,用于将冷氢化工艺中的渣浆进行固液分离,分别得到分离开的固体、分离开的液体,固体包括硅和催化剂氯化亚铜和/或氯化镍,液体包括氯硅烷;
优选的是,固体包括30~60mas%的硅,35~55mas%的金属氯化物,其中金属氯化物包括催化剂氯化亚铜和/或氯化镍,催化剂氯化亚铜和/或氯化镍占固体总质量的15~25mas%。
氯化反应器,与固液分离装置连接,氯化反应器用于加热分离开的固体与锆英砂、碳质还原剂、氯气,在氯化反应器内锆英砂、碳质还原剂、氯气在固体中的氯化亚铜的催化下反应生成四氯化锆、四氯化硅、一氧化碳,固体中的硅与氯气反应生成四氯化硅,该反应放热为整个系统补充热量。
优选的是,固液分离装置包括:
悬液分离器,用于将冷氢化工艺中的渣浆进行悬液分离,分别得到分离开的高浓渣浆、分离开的氯硅烷液体;
转鼓过滤器,与悬液分离器连接,转鼓过滤器包括:转鼓过滤机、与转鼓过滤机连接的用于对其进行抽真空的真空泵,转鼓过滤器用于对高浓渣浆真空过滤;
干燥机,与转鼓过滤器连接,干燥机用于对真空过滤得到的固体进行干燥得到分离开的固体。
优选的是,所述的回收利用系统,还包括:
进料装置,与氯化反应器连接,进料装置用于对氯化反应器进料,进料装置包括:第一储罐,用于存储锆英砂;
第一计量器,与第一储罐连接,第一计量器用于计量第一储罐流出的物料;
第二储罐,用于存储碳质还原剂;
第二计量器,与第二储罐连接,第二计量器用于计量第二储罐流出的物料;
进料缓冲罐,分别于第一计量器、第二计量器连接,进料缓冲罐用于对经过第一计量器、第二计量器流入的物料缓冲;
计量器,计量器的入口与进料缓冲罐连接,计量器的出口与氯化反应器连接,计量器用于计量进料缓冲罐流出的物料。
优选的是,所述的回收利用系统,还包括:
精馏装置,与固液分离装置连接,精馏装置用于将固液分离得到的分离开的液体通过精馏进行分离,得到高纯度的三氯氢硅、四氯化硅。高纯度的三氯氢硅作为原料生产多晶硅,高纯度的四氯化硅继续作为冷氢化工艺的原料。
优选的是,所述的回收利用系统,还包括:
多级冷却分离装置,与氯化反应器连接,多级冷却分离装置用于将反应生成的物料进行多级冷却分离,分别得到分离开的四氯化锆、四氯化硅、氯化亚铜、和/或氯化镍、其他金属氯化物杂质。多级冷却分离根据各物质沸点的不同进行分离,其中四氯化锆的沸点为331℃,四氯化硅的沸点为57.6℃,氯化亚铜的熔点为426℃、沸点为1490℃。
本发明将冷氢化工艺中的渣浆应用于四氯化锆生产过程,一方面采用绿色、经济的方式将渣浆中的氯硅烷、硅元素、催化剂实现全部回收和再利用,提高了渣浆的综合利用率,降低了三氯氢硅生产过程中的硅单质的损耗及催化剂的消耗,另一方面实现了四氯化锆氯化反应的补热,降低了能耗,降低了三氯氢硅、四氯化锆的生产成本,降低劳动强度,杜绝了环境污染,改善了环境。
附图说明
图1是本发明实施例2中的冷氢化工艺中的渣浆回收利用方法所使用的回收利用系统的结构示意图。
图中:1-悬液分离器;2-转鼓过滤机;3-真空泵;4-干燥机;5-螺旋输送器;6-氯化反应器;7-第一储罐;8-第一计量器;9-第二储罐;10-第二计量器;11-第三储罐;12-第三计量器;13-进料缓冲罐;14-计量器。
具体实施方式
为使本领域技术人员更好地理解本发明的技术方案,下面结合附图和具体实施方式对本发明作进一步详细描述。
下面详细描述本专利的实施例,所述实施例的示例在附图中示出,其中自始至终相同或类似的标号表示相同或类似的元件或具有相同或类似功能的元件。下面通过参考附图描述的实施例是示例性的,仅用于解释本专利,而不能理解为对本专利的限制。
实施例1
本实施例提供一种冷氢化工艺中的渣浆回收利用方法,包括以下步骤:
将冷氢化工艺中的渣浆进行固液分离,分别得到分离开的固体、分离开的液体,固体包括硅和催化剂氯化亚铜和/或氯化镍,液体包括氯硅烷;
将分离开的固体与锆英砂、碳质还原剂、氯气加热,锆英砂、碳质还原剂、氯气在固体中的氯化亚铜的催化下反应生成四氯化锆、四氯化硅、一氧化碳,固体中的硅与氯气反应生成四氯化硅。
本实施例还提供一种上述的冷氢化工艺中的渣浆回收利用方法所使用的回收利用系统,包括:
固液分离装置,用于将冷氢化工艺中的渣浆进行固液分离,分别得到分离开的固体、分离开的液体,固体包括硅和催化剂氯化亚铜和/或氯化镍,液体包括氯硅烷;
氯化反应器,与固液分离装置连接,氯化反应器用于加热分离开的固体与锆英砂、碳质还原剂、氯气,在氯化反应器内锆英砂、碳质还原剂、氯气在固体中的氯化亚铜的催化下反应生成四氯化锆、四氯化硅、一氧化碳,固体中的硅与氯气反应生成四氯化硅。
本实施例中的冷氢化工艺中的渣浆回收利用方法及所使用的回收利用系统,将冷氢化工艺中的渣浆应用于四氯化锆生产过程,一方面采用绿色、经济的方式将渣浆中的氯硅烷、硅元素、催化剂实现全部回收和再利用,提高了渣浆的综合利用率,降低了三氯氢硅生产过程中的硅单质的损耗及催化剂的消耗,另一方面实现了四氯化锆氯化反应的补热,降低了能耗,降低了三氯氢硅、四氯化锆的生产成本,降低劳动强度,杜绝了环境污染,改善了环境。
实施例2
如图1所示,本实施例提供一种冷氢化工艺中的渣浆回收利用方法所使用的回收利用系统,包括:
固液分离装置,用于将冷氢化工艺中的渣浆进行固液分离,分别得到分离开的固体、分离开的液体,固体包括:硅和金属氯化物,金属氯化物包括催化剂氯化亚铜和/或氯化镍,液体包括氯硅烷;其中,固体包括30~60mas%的硅,35~55mas%的金属氯化物,其中金属氯化物包括催化剂氯化亚铜和/或氯化镍,催化剂氯化亚铜和/或氯化镍占固体总质量的15~25mas%。
需要说明的是,本实施例中的固液分离装置包括:
悬液分离器1,用于将冷氢化工艺中的渣浆进行悬液分离,分别得到分离开的高浓渣浆、分离开的氯硅烷液体;
转鼓过滤器,与悬液分离器1连接,转鼓过滤器包括:转鼓过滤机2、与转鼓过滤机2连接的用于对其进行抽真空的真空泵3,转鼓过滤器用于对高浓渣浆真空过滤;
干燥机4,与转鼓过滤机2连接,干燥机4用于对真空过滤得到的固体进行干燥得到分离开的固体。
本实施例中的冷氢化工艺中的渣浆回收利用方法所使用的回收利用系统,还包括:
螺旋输送器5,与干燥机4连接,螺旋输送器5用于输送干燥得到的分离开的固体;
氯化反应器6,与螺旋输送器5连接,氯化反应器6用于加热分离开的固体与锆英砂、碳质还原剂、氯气,在氯化反应器6内锆英砂、碳质还原剂、氯气在固体中的氯化亚铜的催化下反应生成四氯化锆、四氯化硅、一氧化碳,固体中的硅与氯气反应生成四氯化硅。
需要说明的是,本实施例中的回收利用系统,还包括:
进料装置,与氯化反应器6连接,进料装置用于对氯化反应器6进料,进料装置包括:第一储罐7,用于存储锆英砂;
第一计量器8,与第一储罐7连接,第一计量器8用于计量第一储罐7流出的物料;
第二储罐9,用于存储碳质还原剂;
第二计量器10,与第二储罐9连接,第二计量器10用于计量第二储罐9流出的物料;
第三储罐11,用于存储补热剂;
第三计量器12,与第三储罐11连接,第三计量器12用于计量第三储罐11流出的物料;
进料缓冲罐13,分别于第一计量器8、第二计量器10、第三计量器12连接,进料缓冲罐13用于对经过第一计量器8、第二计量器10、第三计量器12流入的物料缓冲;
计量器14,计量器14的入口与进料缓冲罐13连接,计量器14的出口与氯化反应器6连接,计量器14用于计量进料缓冲罐13流出的物料。
需要说明的是,本实施例中的回收利用系统,还包括:
精馏装置,与固液分离装置连接,精馏装置用于将固液分离得到的分离开的液体通过精馏进行分离,得到高纯度的三氯氢硅、四氯化硅。高纯度的三氯氢硅作为原料生产多晶硅,高纯度的四氯化硅继续作为冷氢化工艺的原料。具体的,精馏装置与悬液分离器1连接,通过悬液分离器1分离开的氯硅烷液体通入到精馏装置内通过精馏进行分离。精馏装置还与转鼓过滤机2连接,通过转鼓过滤机2真空过滤得到的氯硅烷液体通入到精馏装置内通过精馏进行分离。
需要说明的是,本实施例中的回收利用系统,还包括:
多级冷却分离装置,与氯化反应器6连接,多级冷却分离装置用于将反应生成的物料进行多级冷却分离,分别得到分离开的四氯化锆、四氯化硅、氯化亚铜、和/或氯化镍、其他金属氯化物杂质。多级冷却分离根据各物质沸点的不同进行分离,其中四氯化锆的沸点为331℃,四氯化硅的沸点为57.6℃,氯化亚铜的熔点为426℃、沸点为1490℃。
当冷氢化反应器运行一段时间以后,冷氢化急冷塔底部富集大量的渣浆,定期将冷氢化急冷塔底部塔釜的渣浆进行排放回收利用。
本实施例提供一种使用上述系统进行的冷氢化工艺中的渣浆回收利用方法,包括以下步骤:
(1)将冷氢化工艺中的渣浆进行固液分离,分别得到分离开的固体、分离开的液体,固体包括:硅和金属氯化物,金属氯化物包括催化剂氯化亚铜和/或氯化镍,液体包括氯硅烷;固体包括30~60mas%的硅,35~55mas%的金属氯化物,其中金属氯化物包括催化剂氯化亚铜和/或氯化镍,催化剂氯化亚铜和/或氯化镍占固体总质量的15~25mas%。将冷氢化工艺中的渣浆悬液分离器1进行固液分离的步骤具体为:将冷氢化工艺中的渣浆通入悬液分离器1进行悬液分离,分别得到分离开的高浓渣浆、分离开的氯硅烷液体,再通过转鼓过滤器对高浓渣浆真空过滤,具体的,转鼓过滤器为预涂层转鼓真空过滤器,在使用过程中,在转鼓过滤机2上预涂50~200mm厚度的硅藻土,抽真空后再连续进料过滤,固体被截留在转鼓过滤机2表面,用作滤渣阻碍过滤,真空度增大到一定数值后,刮刀手动进刀0.5~2mm左右将物料刮下,使得滤面常新,连续过滤。再通过干燥机4通过蒸汽加热方式对真空过滤得到的固体进行加热干燥,将其中残余的氯硅烷液体蒸发为气态,再通过后端的冷凝器使得氯硅烷液体冷凝下来,实现残余氯硅烷液体的分离,干燥完毕得到分离开的固体。
(2)将通过悬液分离器1分离开的氯硅烷液体通入到精馏装置内通过精馏进行分离;通过转鼓过滤机2真空过滤得到的氯硅烷液体通入到精馏装置内通过精馏进行分离。
(3)将分离开的固体通过螺旋输送器5输送到氯化反应器6内,将第一储罐7内的锆英砂、第二储罐9内的碳质还原剂、第三储罐11内的补热剂通入进料缓冲罐13,将进料缓冲罐13内的物料通入氯化反应器6,向氯化反应器6内通入氯气,通过氯化反应器6对分离开的固体与锆英砂、碳质还原剂、补热剂、氯气加热,加热的温度为1100~1250℃,在氯化反应器6内锆英砂、碳质还原剂、氯气在固体中的氯化亚铜的催化下反应生成四氯化锆、四氯化硅、一氧化碳,固体中的硅与氯气反应生成四氯化硅,该反应放热为整个系统补充热量,固体中的氯化亚铜与氯气进一步反应生成氯化铜气体,cucl+cl2(g)=cucl2,反应放热使得氯化反应器6内的温度升高,该反应为动态平衡过程,低温时,反应向右进行,当反应温度达到1000℃以上时,氯化铜分解为氯化亚铜及氯气。其中,锆英砂、碳质还原剂与分离开的固体的质量比为26:7:15,补热剂与分离开的固体的质量比为0.3:1。
(4)反应生成的物料包括:四氯化锆、四氯化硅、金属氯化物杂质(包括氯化铁、氯化铝)、一氧化碳。将氯化反应器6内反应生成的物料通入多级冷却分离装置进行多级冷却分离,分别得到分离开的四氯化锆、四氯化硅、氯化亚铜、和/或氯化镍、其他金属氯化物杂质。多级冷却分离根据各物质沸点的不同进行分离,其中四氯化锆的沸点为331℃,四氯化硅的沸点为57.6℃,氯化亚铜的熔点为426℃、沸点为1490℃。其中,分离出的四氯化硅可以继续用作冷氢化反应的原料,分离出的氯化亚铜和/或氯化镍可以用作生产用的催化剂。
采用本实施例中的渣浆回收利用方法,三氯氢硅生产过程的硅单耗下降了20mas%(节省0.05吨硅/吨三氯氢硅),催化剂的回收效率达到了90%以上,四氯化锆生产过程中补热剂(单质硅粉)的消耗量下降了70mas%。
本实施例中的冷氢化工艺中的渣浆回收利用方法及所使用的回收利用系统,将冷氢化工艺中的渣浆应用于四氯化锆生产过程,一方面采用绿色、经济的方式将渣浆中的氯硅烷、硅元素、催化剂实现全部回收和再利用,提高了渣浆的综合利用率,降低了三氯氢硅生产过程中的硅单质的损耗及催化剂的消耗,另一方面实现了四氯化锆氯化反应的补热,降低了能耗,降低了三氯氢硅、四氯化锆的生产成本,降低劳动强度,杜绝了环境污染,改善了环境。
实施例3
本实施例提供一种使用实施例2中的系统进行的冷氢化工艺中的渣浆回收利用方法,与实施例2中的系统的区别为:
加热的温度为1100~1200℃
锆英砂、碳质还原剂与分离开的固体的质量比为26:8.4:7。补热剂与分离开的固体的质量比0.2:1
实施例4
本实施例提供一种使用实施例2中的系统进行的冷氢化工艺中的渣浆回收利用方法,与实施例2中的系统的区别为:
锆英砂、碳质还原剂与分离开的固体的质量比为26:7.8:10。补热剂与分离开的固体的质量比为0.15:1
可以理解的是,以上实施方式仅仅是为了说明本发明的原理而采用的示例性实施方式,然而本发明并不局限于此。对于本领域内的普通技术人员而言,在不脱离本发明的精神和实质的情况下,可以做出各种变型和改进,这些变型和改进也视为本发明的保护范围。
起点商标作为专业知识产权交易平台,可以帮助大家解决很多问题,如果大家想要了解更多知产交易信息请点击 【在线咨询】或添加微信 【19522093243】与客服一对一沟通,为大家解决相关问题。
此文章来源于网络,如有侵权,请联系删除


