一种表面散点式高耐磨陶瓷材料的制备工艺的制作方法



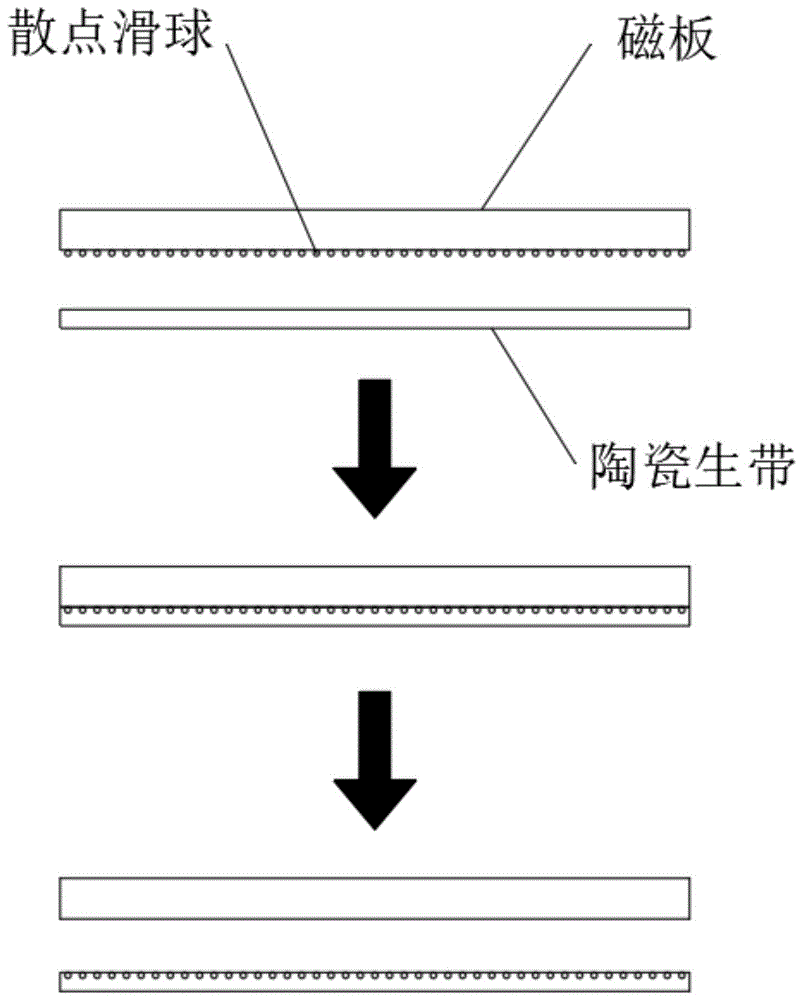
本发明涉及陶瓷制备技术领域,更具体地说,涉及一种表面散点式高耐磨陶瓷材料的制备工艺。
背景技术:
陶瓷是陶器与瓷器的统称,同时也是我国的一种工艺美术品,远在新石器时代,我国已有风格粗犷、朴实的彩陶和黑陶。陶与瓷的质地不同,性质各异。陶,是以粘性较高、可塑性较强的粘土为主要原料制成的,不透明、有细微气孔和微弱的吸水性,击之声浊。瓷是以粘土、长石和石英制成,半透明,不吸水、抗腐蚀,胎质坚硬紧密,叩之声脆。我国传统的陶瓷工艺美术品,质高形美,具有高度的艺术价值,闻名于世界。
陶瓷材料是指用天然或合成化合物经过成形和高温烧结制成的一类无机非金属材料。它具有高熔点、高硬度、高耐磨性、耐氧化等优点。可用作结构材料、刀具材料,由于陶瓷还具有某些特殊的性能,又可作为功能材料。
随着当代科学技术发展,人们在传统材料的基础上,根据当代科技的研究成果,开发出新材料,新材料是指新近发展或正在发展的具有优异性能的结构材料和有特殊性质的功能材料;新材料按组分为金属材料、无机非金属材料(如陶瓷、砷化镓半导体等)、有机高分子材料、先进复合材料四大类;按材料性能分为结构材料和功能材料:结构材料主要是利用材料的力学和理化性能,以满足高强度、高刚度、高硬度、耐高温、耐磨、耐蚀、抗辐照等性能要求的材料;功能材料主要是利用材料具有的电、磁、声、光热等效应,以实现某种功能,如半导体材料、磁性材料、光敏材料、热敏材料、隐身材料和制造原子弹、氢弹的核材料等,新材料在国防建设上作用重大;其中,现有技术领域中的陶瓷材料的耐磨性能还有待提高,尤其是在长时间的磨损下使用寿命会急剧下降。
技术实现要素:
1.要解决的技术问题
针对现有技术中存在的问题,本发明的目的在于提供一种表面散点式高耐磨陶瓷材料的制备工艺,可以在陶瓷原料内预埋散点滑球,并在加热固化的过程中触发连接动作,散点滑球上的热熔树脂膜衣受热熔化恢复流动相,热熔树脂膜衣内的自延伸棒恢复自由状态开始伸长,并推动预埋微磁球挤压半固化的陶瓷原料形成插接,在陶瓷原料完全固化后并排胶,最后烧结得到陶瓷材料成品,其在使用时利用石墨烯耐磨微球对热量的高效感知,在受到反复摩擦后可以将动能转化为热能对重新凝固后的热熔树脂膜衣再次加热熔化,并借由热熔树脂膜衣内的磁性润滑颗粒附着在石墨烯耐磨微球表面,改善摩擦现象,同时基于预埋微磁球的磁吸作用对磁性润滑颗粒进行回收防脱落,在摩擦结束后热熔树脂膜衣凝固重新对石墨烯耐磨微球进行固定,从而实现显著提高陶瓷材料的耐磨性。
2.技术方案
为解决上述问题,本发明采用如下的技术方案。
一种表面散点式高耐磨陶瓷材料的制备工艺,包括以下步骤:
s1、按配比称取烧滑石10-15份、氧化镁10-12份、二氧化硅10-20份、氧化铝12-15份、氮化硅10-20份、硼化硅5-10份、金属铬粉10-20份、二氧化锆15-25份、聚乙烯醇缩丁醛5-10份和聚丙烯树脂10-25份均匀混合进行球磨处理,得到陶瓷粉体;
s2、称取水10-20份、粘结剂10-20份、增塑剂2-5份和分散剂1-3份与陶瓷粉体均匀混合后得到陶瓷浆料;
s3、将陶瓷浆料进行真空脱泡处理后,在流延机上流延成型并加热干燥至半固化;
s4、预加工出相匹配的磁板,并吸附上多个均匀分布的散点滑球,然后与刚刚半固化且未冷却的陶瓷浆料进行压合,并触发连接动作;
s5、取下磁板对陶瓷浆料进行加热干燥处理至完全固化后后送入至窑炉内加热排胶,得到陶瓷坯体;
s6、将陶瓷坯体送入烧结设备内,在1000-1600℃的温度下烧结2-4h,冷却后得到高耐磨陶瓷材料。
进一步的,所述步骤s1中球磨采用湿法球磨的方式,并保证陶瓷粉体研磨后的粒径为5-10μm。
进一步的,所述粘结剂为聚乙烯醇缩丁醛,所述增塑剂为聚乙二醇,所述分散剂为三油酸甘油酯。
进一步的,所述散点滑球包括石墨烯耐磨微球和热熔树脂膜衣,且热熔树脂膜衣包裹于石墨烯耐磨微球外表面,所述热熔树脂膜衣内镶嵌有多个均匀分布的磁性润滑颗粒,石墨烯耐磨微球自身具有极高的强度和耐磨性能,镶嵌于陶瓷材料表面可以改善磨损现象,同时其可以将摩擦动能高效转化为热能对热熔树脂膜衣进行加热熔化,并借由热熔树脂膜衣内的磁性润滑颗粒附着在石墨烯耐磨微球表面,改善磨损现象。
进一步的,所述热熔树脂膜衣上镶嵌连接有多个均匀分布的自延伸棒,且自延伸棒一端与石墨烯耐磨微球连接,所述自延伸棒远离石墨烯耐磨微球一端连接于预埋微磁球,且预埋微磁球同样镶嵌于热熔树脂膜衣内,预埋微磁球暂时性的镶嵌于热熔树脂膜衣内可以方便散点滑球挤压半固化的陶瓷原料实现均匀可控的变形,然后在热熔树脂膜衣熔化后恢复自延伸棒的自由状态,在自延伸棒的弹力作用下推动预埋微磁球展开并插入至陶瓷原料内进行多点连接,同时预埋微磁球可以在陶瓷内施加磁力作用,始终对磁性润滑颗粒进行绑定回收避免在摩擦过程中出现脱落。
进一步的,所述自延伸棒包括滞留杆、防磨套和后熔包,所述防磨套包裹于滞留杆的一端,所述后熔包连接于防磨套与石墨烯耐磨微球之间,滞留杆一方面起到对石墨烯耐磨微球的支撑作用,避免其挤压熔融状态下的热熔树脂膜衣出现移位和漏料现象,另一方面可以对热熔树脂膜衣进行滞留,降低热熔树脂膜衣的流动性,从而防止其在石墨烯耐磨微球转动过程中出现倾泻现象,防磨套起到保护滞留杆的作用,避免其在与石墨烯耐磨微球之间的相对移动中出现严重磨损现象,后熔包起到临时性固定滞留杆的作用。
进一步的,所述滞留杆采用高弹性材料制成,所述防磨套采用塑性材料制成,所述后熔包和热熔树脂膜衣均采用热熔性树脂材料制成,且后熔包的熔点高于热熔树脂膜衣,后熔包在更高的温度下会熔化与热熔树脂膜衣混合,实现对滞留杆的自由解放。
进一步的,所述磁性润滑颗粒和预埋微磁球均包括耐高温层和磁性内芯,且磁性内芯填充于耐高温层内,所述耐高温层采用隔热材料制成,所述磁性内芯采用强磁性材料制成,耐高温层起到对磁性内芯的保护作用,避免高温对磁性内芯的磁场作用进行干扰和消除。
进一步的,所述步骤s5中加热排胶的温度为450-550℃,加热时间为1-1.5h。
进一步的,所述步骤s6中陶瓷坯体先在200-300℃的温度下烧结30-40min,再升温到600-800℃烧结40-60min,然后升温至1000℃以上烧结60-90min,接着降温至600-800℃保温30-50min,最后自然冷却至室温。
3.有益效果
相比于现有技术,本发明的优点在于:
(1)本方案可以在陶瓷原料内预埋散点滑球,并在加热固化的过程中触发连接动作,散点滑球上的热熔树脂膜衣受热熔化恢复流动相,热熔树脂膜衣内的自延伸棒恢复自由状态开始伸长,并推动预埋微磁球挤压半固化的陶瓷原料形成插接,在陶瓷原料完全固化后并排胶,最后烧结得到陶瓷材料成品,其在使用时利用石墨烯耐磨微球对热量的高效感知,在受到反复摩擦后可以将动能转化为热能对重新凝固后的热熔树脂膜衣再次加热熔化,并借由热熔树脂膜衣内的磁性润滑颗粒附着在石墨烯耐磨微球表面,改善摩擦现象,同时基于预埋微磁球的磁吸作用对磁性润滑颗粒进行回收防脱落,在摩擦结束后热熔树脂膜衣凝固重新对石墨烯耐磨微球进行固定,从而实现显著提高陶瓷材料的耐磨性。
(2)散点滑球包括石墨烯耐磨微球和热熔树脂膜衣,且热熔树脂膜衣包裹于石墨烯耐磨微球外表面,热熔树脂膜衣内镶嵌有多个均匀分布的磁性润滑颗粒,石墨烯耐磨微球自身具有极高的强度和耐磨性能,镶嵌于陶瓷材料表面可以改善磨损现象,同时其可以将摩擦动能高效转化为热能对热熔树脂膜衣进行加热熔化,并借由热熔树脂膜衣内的磁性润滑颗粒附着在石墨烯耐磨微球表面,改善磨损现象。
(3)热熔树脂膜衣上镶嵌连接有多个均匀分布的自延伸棒,且自延伸棒一端与石墨烯耐磨微球连接,自延伸棒远离石墨烯耐磨微球一端连接于预埋微磁球,且预埋微磁球同样镶嵌于热熔树脂膜衣内,预埋微磁球暂时性的镶嵌于热熔树脂膜衣内可以方便散点滑球挤压半固化的陶瓷原料实现均匀可控的变形,然后在热熔树脂膜衣熔化后恢复自延伸棒的自由状态,在自延伸棒的弹力作用下推动预埋微磁球展开并插入至陶瓷原料内进行多点连接,同时预埋微磁球可以在陶瓷内施加磁力作用,始终对磁性润滑颗粒进行绑定回收避免在摩擦过程中出现脱落。
(4)自延伸棒包括滞留杆、防磨套和后熔包,防磨套包裹于滞留杆的一端,后熔包连接于防磨套与石墨烯耐磨微球之间,滞留杆一方面起到对石墨烯耐磨微球的支撑作用,避免其挤压熔融状态下的热熔树脂膜衣出现移位和漏料现象,另一方面可以对热熔树脂膜衣进行滞留,降低热熔树脂膜衣的流动性,从而防止其在石墨烯耐磨微球转动过程中出现倾泻现象,防磨套起到保护滞留杆的作用,避免其在与石墨烯耐磨微球之间的相对移动中出现严重磨损现象,后熔包起到临时性固定滞留杆的作用。
(5)滞留杆采用高弹性材料制成,防磨套采用塑性材料制成,后熔包和热熔树脂膜衣均采用热熔性树脂材料制成,且后熔包的熔点高于热熔树脂膜衣,后熔包在更高的温度下会熔化与热熔树脂膜衣混合,实现对滞留杆的自由解放。
(6)磁性润滑颗粒和预埋微磁球均包括耐高温层和磁性内芯,且磁性内芯填充于耐高温层内,耐高温层采用隔热材料制成,磁性内芯采用强磁性材料制成,耐高温层起到对磁性内芯的保护作用,避免高温对磁性内芯的磁场作用进行干扰和消除。
附图说明
图1为本发明的流程示意图;
图2为本发明散点滑球正常状态下的结构示意图;
图3为本发明散点滑球连接状态下的结构示意图;
图4为本发明自延伸棒的结构示意图;
图5为本发明预埋微磁球和磁性润滑颗粒的结构示意图;
图6为本发明陶瓷材料部分摩擦状态下的结构示意图。
图中标号说明:
1石墨烯耐磨微球、2热熔树脂膜衣、3磁性润滑颗粒、4预埋微磁球、5自延伸棒、51滞留杆、52防磨套、53后熔包、10耐高温层、20磁性内芯。
具体实施方式
下面将结合本发明实施例中的附图,对本发明实施例中的技术方案进行清楚、完整地描述;显然,所描述的实施例仅仅是本发明一部分实施例,而不是全部的实施例,基于本发明中的实施例,本领域普通技术人员在没有做出创造性劳动前提下所获得的所有其他实施例,都属于本发明保护的范围。
在本发明的描述中,需要说明的是,术语“上”、“下”、“内”、“外”、“顶/底端”等指示的方位或位置关系为基于附图所示的方位或位置关系,仅是为了便于描述本发明和简化描述,而不是指示或暗示所指的装置或元件必须具有特定的方位、以特定的方位构造和操作,因此不能理解为对本发明的限制。此外,术语“第一”、“第二”仅用于描述目的,而不能理解为指示或暗示相对重要性。
在本发明的描述中,需要说明的是,除非另有明确的规定和限定,术语“安装”、“设置有”、“套设/接”、“连接”等,应做广义理解,例如“连接”,可以是固定连接,也可以是可拆卸连接,或一体地连接;可以是机械连接,也可以是电连接;可以是直接相连,也可以通过中间媒介间接相连,可以是两个元件内部的连通。对于本领域的普通技术人员而言,可以具体情况理解上述术语在本发明中的具体含义。
实施例1:
请参阅图1,一种表面散点式高耐磨陶瓷材料的制备工艺,包括以下步骤:
s1、按配比称取烧滑石10份、氧化镁10份、二氧化硅10份、氧化铝12份、氮化硅10份、硼化硅5份、金属铬粉10份、二氧化锆15份、聚乙烯醇缩丁醛5份和聚丙烯树脂10份均匀混合进行球磨处理,得到陶瓷粉体;
s2、称取水10份、粘结剂10份、增塑剂2份和分散剂1份与陶瓷粉体均匀混合后得到陶瓷浆料;
s3、将陶瓷浆料进行真空脱泡处理后,在流延机上流延成型并加热干燥至半固化;
s4、预加工出相匹配的磁板,并吸附上多个均匀分布的散点滑球,然后与刚刚半固化且未冷却的陶瓷浆料进行压合,并触发连接动作;
s5、取下磁板对陶瓷浆料进行加热干燥处理至完全固化后后送入至窑炉内加热排胶,加热排胶的温度为450℃,加热时间为1h,得到陶瓷坯体;
s6、将陶瓷坯体送入烧结设备内,在1000℃的温度下烧结2h,冷却后得到高耐磨陶瓷材料。
步骤s1中球磨采用湿法球磨的方式,并保证陶瓷粉体研磨后的粒径为5-10μm。
粘结剂为聚乙烯醇缩丁醛,增塑剂为聚乙二醇,分散剂为三油酸甘油酯。
请参阅图2-3,散点滑球包括石墨烯耐磨微球1和热熔树脂膜衣2,且热熔树脂膜衣2包裹于石墨烯耐磨微球1外表面,热熔树脂膜衣2内镶嵌有多个均匀分布的磁性润滑颗粒3,石墨烯耐磨微球1自身具有极高的强度和耐磨性能,镶嵌于陶瓷材料表面可以改善磨损现象,同时其可以将摩擦动能高效转化为热能对热熔树脂膜衣2进行加热熔化,并借由热熔树脂膜衣2内的磁性润滑颗粒3附着在石墨烯耐磨微球1表面,改善磨损现象。
热熔树脂膜衣2上镶嵌连接有多个均匀分布的自延伸棒5,且自延伸棒5一端与石墨烯耐磨微球1连接,自延伸棒5远离石墨烯耐磨微球1一端连接于预埋微磁球4,且预埋微磁球4同样镶嵌于热熔树脂膜衣2内,预埋微磁球4暂时性的镶嵌于热熔树脂膜衣2内可以方便散点滑球挤压半固化的陶瓷原料实现均匀可控的变形,然后在热熔树脂膜衣2熔化后恢复自延伸棒5的自由状态,在自延伸棒5的弹力作用下推动预埋微磁球4展开并插入至陶瓷原料内进行多点连接,同时预埋微磁球4可以在陶瓷内施加磁力作用,始终对磁性润滑颗粒3进行绑定回收避免在摩擦过程中出现脱落。
请参阅图4,自延伸棒5包括滞留杆51、防磨套52和后熔包53,防磨套52包裹于滞留杆51的一端,后熔包53连接于防磨套52与石墨烯耐磨微球1之间,滞留杆51一方面起到对石墨烯耐磨微球1的支撑作用,避免其挤压熔融状态下的热熔树脂膜衣2出现移位和漏料现象,另一方面可以对热熔树脂膜衣2进行滞留,降低热熔树脂膜衣2的流动性,从而防止其在石墨烯耐磨微球1转动过程中出现倾泻现象,防磨套52起到保护滞留杆51的作用,避免其在与石墨烯耐磨微球1之间的相对移动中出现严重磨损现象,后熔包53起到临时性固定滞留杆51的作用。
滞留杆51采用高弹性材料制成,防磨套52采用塑性材料制成,后熔包53和热熔树脂膜衣2均采用热熔性树脂材料制成,且后熔包53的熔点高于热熔树脂膜衣2,后熔包53在更高的温度下会熔化与热熔树脂膜衣2混合,实现对滞留杆51的自由解放。
请参阅图5,磁性润滑颗粒3和预埋微磁球4均包括耐高温层10和磁性内芯20,且磁性内芯20填充于耐高温层10内,耐高温层10采用隔热材料制成,磁性内芯20采用强磁性材料制成,耐高温层10起到对磁性内芯20的保护作用,避免高温对磁性内芯20的磁场作用进行干扰和消除。
步骤s6中陶瓷坯体先在200-300℃的温度下烧结30-40min,再升温到600-800℃烧结40-60min,然后升温至1000℃以上烧结60-90min,接着降温至600-800℃保温30-50min,最后自然冷却至室温。
实施例2:
请参阅图1,一种表面散点式高耐磨陶瓷材料的制备工艺,包括以下步骤:
s1、按配比称取烧滑石12份、氧化镁11份、二氧化硅15份、氧化铝13份、氮化硅15份、硼化硅8份、金属铬粉15份、二氧化锆20份、聚乙烯醇缩丁醛8份和聚丙烯树脂18份均匀混合进行球磨处理,得到陶瓷粉体;
s2、称取水15份、粘结剂15份、增塑剂3份和分散剂2份与陶瓷粉体均匀混合后得到陶瓷浆料;
s3、将陶瓷浆料进行真空脱泡处理后,在流延机上流延成型并加热干燥至半固化;
s4、预加工出相匹配的磁板,并吸附上多个均匀分布的散点滑球,然后与刚刚半固化且未冷却的陶瓷浆料进行压合,并触发连接动作;
s5、取下磁板对陶瓷浆料进行加热干燥处理至完全固化后后送入至窑炉内加热排胶,加热排胶的温度为500℃,加热时间为1.2h,得到陶瓷坯体;
s6、将陶瓷坯体送入烧结设备内,在1300℃的温度下烧结3h,冷却后得到高耐磨陶瓷材料。
其余部分与实施例1保持一致。
实施例3:
请参阅图1,一种表面散点式高耐磨陶瓷材料的制备工艺,包括以下步骤:
s1、按配比称取烧滑石15份、氧化镁12份、二氧化硅20份、氧化铝15份、氮化硅20份、硼化硅10份、金属铬粉20份、二氧化锆25份、聚乙烯醇缩丁醛10份和聚丙烯树脂25份均匀混合进行球磨处理,得到陶瓷粉体;
s2、称取水20份、粘结剂20份、增塑剂5份和分散剂3份与陶瓷粉体均匀混合后得到陶瓷浆料;
s3、将陶瓷浆料进行真空脱泡处理后,在流延机上流延成型并加热干燥至半固化;
s4、预加工出相匹配的磁板,并吸附上多个均匀分布的散点滑球,然后与刚刚半固化且未冷却的陶瓷浆料进行压合,并触发连接动作;
s5、取下磁板对陶瓷浆料进行加热干燥处理至完全固化后后送入至窑炉内加热排胶,加热排胶的温度为550℃,加热时间为1.5h,得到陶瓷坯体;
s6、将陶瓷坯体送入烧结设备内,在1600℃的温度下烧结4h,冷却后得到高耐磨陶瓷材料。
其余部分与实施例1保持一致。
本发明可以在陶瓷原料内预埋散点滑球,并在加热固化的过程中触发连接动作,散点滑球上的热熔树脂膜衣2受热熔化恢复流动相,热熔树脂膜衣2内的自延伸棒5恢复自由状态开始伸长,并推动预埋微磁球4挤压半固化的陶瓷原料形成插接,在陶瓷原料完全固化后并排胶,最后烧结得到陶瓷材料成品,其在使用时利用石墨烯耐磨微球1对热量的高效感知,在受到反复摩擦后可以将动能转化为热能对重新凝固后的热熔树脂膜衣2再次加热熔化,并借由热熔树脂膜衣2内的磁性润滑颗粒3附着在石墨烯耐磨微球1表面,改善摩擦现象,同时基于预埋微磁球4的磁吸作用对磁性润滑颗粒3进行回收防脱落,在摩擦结束后热熔树脂膜衣2凝固重新对石墨烯耐磨微球1进行固定,从而实现显著提高陶瓷材料的耐磨性。
以上所述,仅为本发明较佳的具体实施方式;但本发明的保护范围并不局限于此。任何熟悉本技术领域的技术人员在本发明揭露的技术范围内,根据本发明的技术方案及其改进构思加以等同替换或改变,都应涵盖在本发明的保护范围内。
起点商标作为专业知识产权交易平台,可以帮助大家解决很多问题,如果大家想要了解更多知产交易信息请点击 【在线咨询】或添加微信 【19522093243】与客服一对一沟通,为大家解决相关问题。
此文章来源于网络,如有侵权,请联系删除


