利用制盐废液生产光卤石的方法与流程



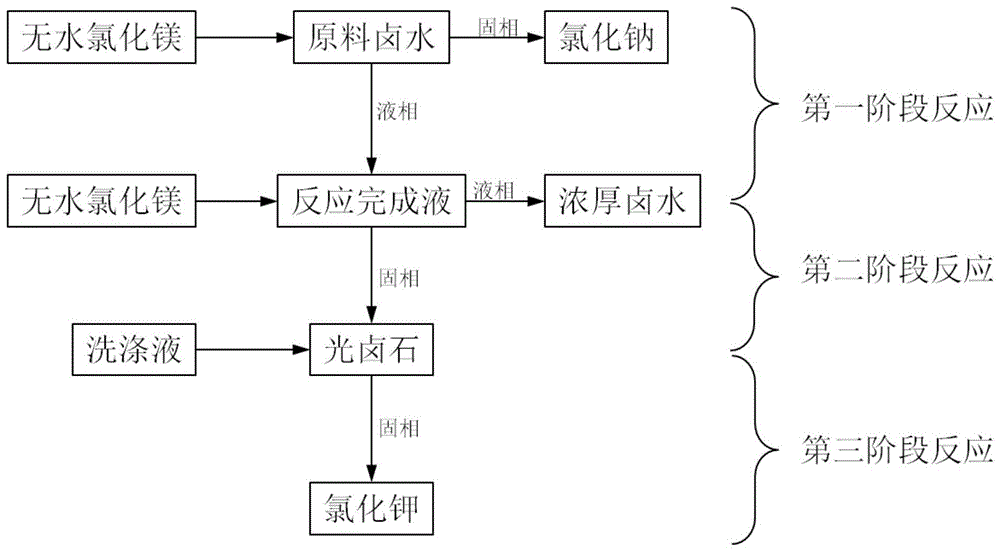
本发明属于制盐废液综合利用领域,具体涉及一种利用制盐废液生产光卤石的方法。
背景技术:
:制盐废液是海水制盐副产的卤水,俗称苦卤,其中含有大量k+、mg2+、so42-、cl-等无机离子,如若直接舍弃苦卤,即对环境造成污染,又会造成其中所含大量k+、mg2+、so42-、cl-等无机离子资源的浪费,而将苦卤作为生产氯化钾、氯化镁及硫酸镁等的原料成为苦卤处理再利用的有效方案。目前,我国大部分盐化工企业采用成熟的兑卤蒸发法生产光卤石工艺,该工艺先将苦卤蒸发浓缩,保温沉降后去除氯化钠,进而冷却结晶获得光卤石。该工艺消耗大量蒸汽和电,生产成本高,企业长期处于亏损状态。技术实现要素:本发明是为了克服现有兑卤蒸发法生产光卤石工艺中存在的高能耗的缺点而提出的,其目的是提供一种利用制盐废液生产光卤石的方法。本发明是通过以下技术方案实现的:一种利用制盐废液生产光卤石的方法,包括以下步骤:(ⅰ)分离氯化钠将氯化镁缓慢加入原料卤水中,使其析出氯化钠,并控制反应完成液的波美度,固液分离,固相即为氯化钠;(ⅱ)获取光卤石将氯化镁缓慢加入步骤(ⅰ)的反应完成液中,析出光卤石,并控制反应完成液的波美度,固液分离,固相即为光卤石;(ⅲ)光卤石分解洗涤将步骤(ⅱ)所得光卤石加入洗涤液中,控制洗涤液加入量,分解洗涤,固液分离,即得氯化钾。所述氯化镁为无水氯化镁。在上述技术方案中,所述无水氯化镁为碎块状或粉状。在上述技术方案中,所述原料卤水为制盐废液。在上述技术方案中,所述制盐废液中氯化钾含量为25g/l以上。在上述技术方案中,所述步骤(ⅰ)中反应完成液的波美度为32°bé~35.5°bé。在上述技术方案中,所述步骤(ⅱ)中反应完成液的波美度为35.5°bé~38°bé。在上述技术方案中,所述步骤(ⅲ)中的洗涤液为氯化钾溶液。在上述技术方案中,所述氯化钾溶液中氯化钾的浓度≤100g/l。在上述技术方案中,所述步骤(ⅱ)中洗涤液加入量为每100g光卤石加入75ml~100ml洗涤液。本发明的有益效果是:本发明提供了一种利用制盐废液生产光卤石的方法,以苦卤及无水氯化镁为原料,利用同离子效应以及氯化钾、氯化镁、氯化钠在不同组分下共饱和点的不同,分两阶段向苦卤中加入无水氯化镁,获得氯化钠、光卤石和浓厚卤,光卤石经分解洗涤后,获得氯化钾,对比行业内兑卤蒸发法生产光卤石工艺,极大地降低了产品能耗和成本。附图说明图1是本发明利用制盐废液生产光卤石的方法的流程示意图。具体实施方式为了使本
技术领域:
的人员更好地理解本发明技术方案,下面结合说明书附图并通过具体实施方式来进一步说明本发明利用制盐废液生产光卤石的方法的技术方案。如图1所示,一种利用制盐废液生产光卤石的方法,包括以下步骤:(ⅰ)分离氯化钠(第一阶段反应)将碎块状或粉状的无水氯化镁缓慢加入氯化钾含量为25g/l以上的制盐废液中,使其析出氯化钠,并控制反应完成液的波美度在32°bé~35.5°bé之间,固液分离,固相即为氯化钠,液相即反应完成液进入第二阶段反应;(ⅱ)获取光卤石(第二阶段反应)将碎块状或粉状的无水氯化镁缓慢加入步骤(ⅰ)的反应完成液中,析出光卤石,并控制反应完成液的波美度在35.5°bé~38°bé之间,固液分离,固相即为光卤石,液相浓厚卤留存处理;(ⅲ)光卤石分解洗涤(第三阶段反应,光卤石后处理)将步骤(ⅱ)所得光卤石加入浓度≤100g/l的氯化钾溶液中,控制洗涤液加入量为每100g光卤石加入75ml~100ml,分解洗涤,固液分离,即得氯化钾。实施例1一种利用制盐废液生产光卤石的方法,包括以下步骤:(ⅰ)分离氯化钠(第一阶段反应)将粉状无水氯化镁缓慢加入500ml原料卤水a中,反应结束后,反应完成液为33.4°bé,析出氯化钠,固液分离后,液相进入第二阶段反应,固相为氯化钠。(ⅱ)第二阶段反应将粉状无水氯化镁缓慢加入第一阶段反应完成液中,反应结束后,反应完成液为36.8°bé,析出光卤石,固液分离后,获得光卤石a。(ⅲ)光卤石分解洗涤(第三阶段反应,光卤石后处理)配制70g/l氯化钾溶液为洗涤液,将光卤石a加入洗涤液中,控制洗涤液加入量为75ml,充分分解洗涤,固液分离后,获得氯化钾a。实施例2一种利用制盐废液生产光卤石的方法,包括以下步骤:(ⅰ)分离氯化钠(第一阶段反应)将块状无水氯化镁缓慢加入500ml原料卤水b中,反应结束后,反应完成液为33.5°bé,析出氯化钠,固液分离后,液相进入第二阶段反应,固相为氯化钠。(ⅱ)获取光卤石(第二阶段反应)将块状无水氯化镁缓慢加入第一阶段反应完成液中,反应结束后,反应完成液为36.5°bé,析出光卤石,固液分离后,获得光卤石b。(ⅲ)光卤石分解洗涤(第三阶段反应,光卤石后处理)配制75g/l氯化钾溶液为洗涤液,将光卤石b加入洗涤液中,控制洗涤液加入量为56ml,充分分解洗涤,固液分离后,获得氯化钾b。实施例3一种利用制盐废液生产光卤石的方法,包括以下步骤:(ⅰ)分离氯化钠(第一阶段反应)将粉状无水氯化镁缓慢加入5000ml原料卤水c中,反应结束后,反应完成液为33.5°bé,析出氯化钠,固液分离后,液相进入第二阶段反应,固相为氯化钠。(ⅱ)获取光卤石(第二阶段反应)将无水氯化镁缓慢加入第一阶段反应完成液中,反应结束后,反应完成液为36.9°bé,析出光卤石,固液分离后,获得光卤石c。(ⅲ)光卤石分解洗涤(第三阶段反应,光卤石后处理)配制70g/l氯化钾溶液为洗涤液,将光卤石c加入洗涤液中,控制洗涤液加入量750ml,充分分解洗涤,固液分离后,获得氯化钾c。实施例4一种利用制盐废液生产光卤石的方法,包括以下步骤:(ⅰ)分离氯化钠(第一阶段反应)将块状无水氯化镁缓慢加入10000ml原料卤水d中,反应结束后,反应完成液为33.5°bé,析出氯化钠,固液分离后,液相进入第二阶段反应,固相为氯化钠。(ⅱ)获取光卤石(第二阶段反应)将无水氯化镁缓慢加入第一阶段反应完成液中,反应结束后,反应完成液为36°bé,析出光卤石,固液分离后,获得光卤石d。(ⅲ)光卤石分解洗涤(第三阶段反应,光卤石后处理)配制80g/l氯化钾溶液为洗涤液,将光卤石d加入洗涤液中,控制洗涤液加入量为1500ml,充分分解洗涤,固液分离后,获得氯化钾d。实施例1~4中所采用的原料卤水的组成如表1所示。表1实施例1~4的原料卤水的组成分析。实施例波美度(°bé)kcl(g/l)mgcl2(g/l)mgso4(g/l)nacl(g/l)苦卤a30.847.35232.2644.1561.39苦卤b30.632.06250.0537.3152.77苦卤c30.640.03232.8158.3865.31苦卤d31.039.24231.4151.3758.5对实施例1~4通过不同体积及组分原料卤水添加无水氯化镁,控制第一阶段和第二阶段反应的条件,获得的光卤石进行分析,结果如下表2。表2实施例1~4所获得光卤石产量及组分分析实施例产量(g)kcl(%)mgcl2(%)mgso4(%)nacl(%)光卤石a86.521.1831.270.609.81光卤石b62.820.4830.450.6310.25光卤石c87020.0930.001.1510.36光卤石d174018.7829.621.1610.45通过表2的数据可知,采用本发明方法条件生产的光卤石收率高,质量稳定,氯化钾含量为18%~22%,氯化镁含量为28%~31%,氯化钠含量为8%~11%。对实施例1~4所得光卤石进行分解洗涤后获得氯化钾产品的组分分析如表3所示。表3实施例1~4所获得光卤石进行分解洗涤后获得氯化钾产品的组分分析。实施例kcl(%)mgcl2(%)mgso4(%)nacl(%)氯化钾a92.251.530.07未检出氯化钾b91.751.660.07未检出氯化钾c90.971.510.761.56氯化钾d92.561.65未检出0.12通过表3的数据分析可知,采用本发明工艺条件生产的氯化钾产品质量稳定,氯化钾含量在90%以上。本发明提供了一种利用制盐废液生产光卤石的方法,以苦卤及无水氯化镁为原料,利用同离子效应以及氯化钾、氯化镁、氯化钠在不同组分下共饱和点的不同,分两阶段向苦卤中加入无水氯化镁,获得氯化钠、光卤石和浓厚卤,光卤石经分解洗涤后,获得氯化钾,对比行业内兑卤蒸发法生产光卤石工艺,极大地降低了产品能耗和成本。需要说明的是,在不冲突的情况下,本发明中的实施例及实施例中的特征可以相互组合。申请人声明,以上所述仅为本发明的具体实施方式,但本发明的保护范围并不局限于此,所属
技术领域:
的技术人员应该明了,任何属于本
技术领域:
的技术人员在本发明揭露的技术范围内,可轻易想到的变化或替换,均落在本发明的保护范围和公开范围之内。当前第1页1 2 3 
起点商标作为专业知识产权交易平台,可以帮助大家解决很多问题,如果大家想要了解更多知产交易信息请点击 【在线咨询】或添加微信 【19522093243】与客服一对一沟通,为大家解决相关问题。
此文章来源于网络,如有侵权,请联系删除



tips