一种利用电石渣制备微粉碳酸钙的装置的制作方法



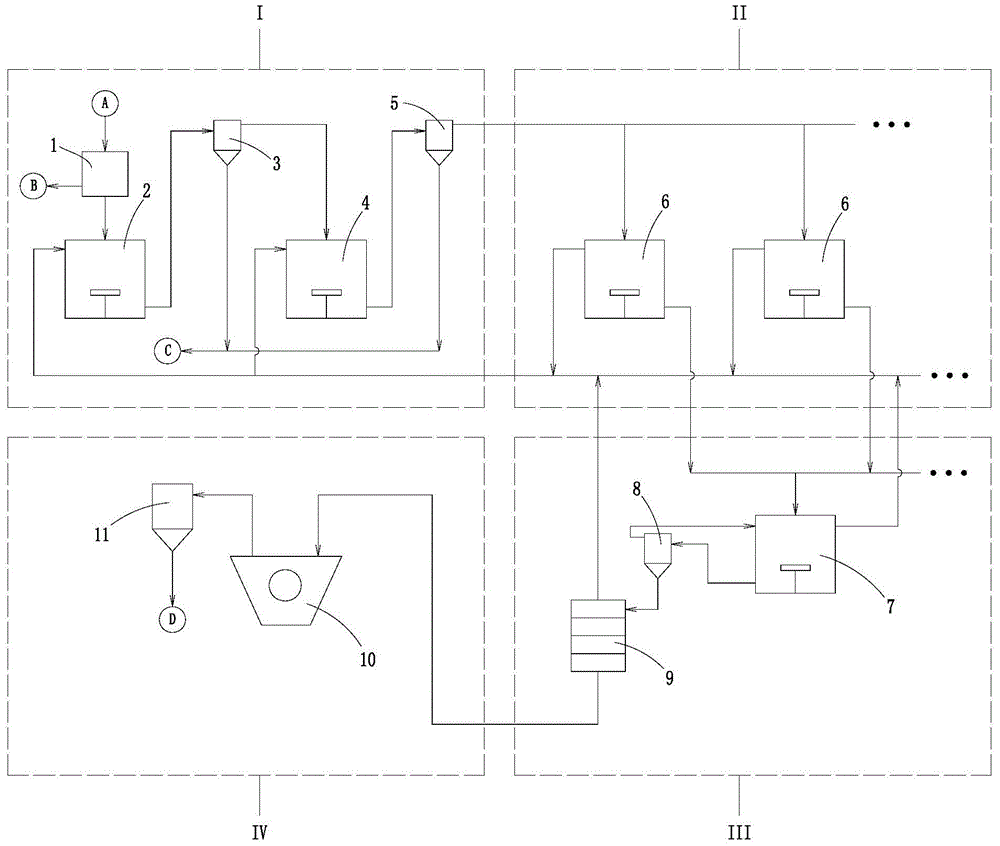
本实用新型属于化工技术领域,特别是涉及一种利用电石渣制备微粉碳酸钙的装置。
背景技术:
据统计,我国现有电石产能在2600万吨左右,同时每年产生的电石渣超过3500万吨,而电石渣中的主要矿物成分为ca(oh)2,其在电石渣的占比达到70%~85%。现阶段,只有少部分的电石渣被用于制造低附加值的水泥,剩余的绝大部分电石渣都没有实现循环再利用,这部分电石渣不但会占用大量的土地,而且还会由于电石渣的碱液和残留电石的水解,进而造成生态环境、地下水以及土壤等污染。因此,解决电石渣循环再利用难的问题十分必要。
为此,申请号为200610031408.0的中国专利公开了一种由电石渣制备高纯轻质碳酸钙微粉的方法,申请号为201310691661.9的中国专利公开了一种以电石渣为原料制取纳米碳酸钙的方法,尽管上述两个专利申请中都涉及了电石渣循环再利用的方法,一个利用电石渣制备碳酸钙微粉,另一个是利用电石渣制取纳米碳酸钙。但是,上述两个专利申请中的方法都存在着问题。第一,中间产物都存在氨水,而氨水属于化学危险品,其储存条件和使用要求较高;第二,都没有提及到如何脱除电石渣中的铁化物和残碳,而铁化物和残碳又是影响微粉碳酸钙质量和白度的主要因素;第三,都存在工艺流程长、过程复杂、产品杂质含量高、产品质量差等缺点。
技术实现要素:
针对现有技术存在的问题,本实用新型提供一种利用电石渣制备微粉碳酸钙的装置,中间产物中没有氨水的存在,通过脱除电石渣中的铁化物和残碳,有效提高了微粉碳酸钙的质量和白度,同时具有工艺流程简单、操作容易、能耗低的特点。
为了实现上述目的,本实用新型采用如下技术方案:一种利用电石渣制备微粉碳酸钙的装置,包括精制单元、碳化单元、增浓压滤单元及干燥单元;所述精制单元包括强磁磁选机、混合搅拌槽、第一水力旋流器、浮选搅拌槽及浮选机;所述碳化单元包括至少两组碳化槽;所述增浓压滤单元包括浓缩机、第二水力旋流器及压滤机;所述干燥单元包括烘干打散机及产品收集器;所述强磁磁选机的进料口用于输入电石渣原料,强磁磁选机的第一出料口用于排放磁选出的铁化物,强磁磁选机的第二出料口用于输出去除铁化物的电石渣原料,强磁磁选机的第二出料口与混合搅拌槽的顶部进料口相连通,混合搅拌槽的底部出料口与第一水力旋流器的顶部进料口相连通,第一水力旋流器的底部排渣口用于排出固态杂质,第一水力旋流器的顶部浆液出口用于排出电石渣浆料;所述第一水力旋流器的顶部浆液出口与浮选搅拌槽的顶部进料口相连通,浮选搅拌槽的底部出料口与浮选机的顶部进料口相连通,浮选机的排渣口用于排出固态杂质,浮选机的浆液出口用于排出电石渣浆料;所述浮选机的浆液出口与碳化槽的顶部进料口相连通,碳化槽的底部出料口用于排出碳酸钙浆液,碳化槽的顶部澄清液出口与混合搅拌槽及浮选搅拌槽的顶部进料口相连通;所述碳化槽的底部出料口与浓缩机的顶部进料口相连通,浓缩机的顶部澄清液出口与混合搅拌槽及浮选搅拌槽的顶部进料口相连通,浓缩机的底部出料口与第二水力旋流器的顶部进料口相连通,第二水力旋流器的顶部低浓度浆液出口与浓缩机的顶部进料口相连通,第二水力旋流器的底部高浓度浆液出口与压滤机的进料口相连通,压滤机的滤出液出口与混合搅拌槽及浮选搅拌槽的顶部进料口相连通,压滤机的出料口与烘干打散机的进料口相连通,烘干打散机的出料口与产品收集器的进料口相连通,产品收集器的出料口用于排出微粉碳酸钙。
一种利用电石渣制备微粉碳酸钙的方法,采用了所述的利用电石渣制备微粉碳酸钙的装置,包括如下步骤:
步骤一:精制
步骤①:将电石渣原料经计量后输入强磁磁选机内,通过强磁磁选机将电石渣原料内的铁化物分离排出,使电石渣原料中的铁化物含量降到0.15%以下;
步骤②:将脱除了铁化物的电石渣原料输入混合搅拌槽内,同时向混合搅拌槽内输入热水,在混合搅拌槽内制备出质量浓度为30%~40%的电石渣浆料;
步骤③:将制备好的电石渣浆料输入第一水力旋流器内,通过第一水力旋流器将电石渣浆料中的固态杂质分离排出;
步骤④:将脱除了固态杂质的电石渣浆料输入浮选搅拌槽内,同时向浮选搅拌槽内输入定量的捕捉剂、起泡剂和ph值调节剂,使电石渣浆料的ph值处于7.0~7.5之间;
步骤⑤:将调整好ph值的电石渣浆料输入浮选机内,同时向浮选机内输入脱硅浮选剂,并且进行三次反浮选脱硅,使电石渣原料中的硅含量降到1.7%以下,脱硅过程中产生的固态杂质直接分离排出;
步骤⑥:当电石渣浆料完成三次反浮选脱硅后,再向浮选机内输入脱碳浮选剂,而且只进行一次浮选脱碳,使电石渣原料中的碳含量降到0.7%以下,脱碳过程中产生的固态杂质直接分离排出;
步骤二:碳化
步骤①:将脱除了硅和碳的电石渣浆料输入碳化槽内,同时向碳化槽内输入热水,使电石渣浆料的质量浓度降到10%~15%,并且将电石渣浆料的温度调整到50℃~80℃;
步骤②:向碳化槽内输入二氧化碳气体,通过搅拌使电石渣浆料与二氧化碳气体发生反应,反应时间为2h~10h,直至在碳化槽内形成碳酸钙浆液;
步骤三:增浓压滤
步骤①:将碳酸钙浆液输入浓缩机内,通过浓缩机将碳酸钙浆液的质量浓度提高到45%~50%;
步骤②:将浓缩后的碳酸钙浆液输入第二水力旋流器内,通过第二水力旋流器将碳酸钙浆液进行进一步增浓,直到将碳酸钙浆液的质量浓度提高到70%~75%;
步骤③:将增浓后的碳酸钙浆液输入压滤机内,通过压滤机对碳酸钙浆液进行脱水,直到形成含水率为12%~17%的碳酸钙滤饼;
步骤四:干燥
步骤①:将脱水后的碳酸钙滤饼输入烘干打散机内,通过烘干打散机对碳酸钙滤饼进行干燥和打碎,干燥温度为70℃~120℃,直至形成含水率<1%的微粉碳酸钙;
步骤②:将微粉碳酸钙输入产品收集器内进行存储。
本实用新型的有益效果:
本实用新型的利用电石渣制备微粉碳酸钙的装置,中间产物中没有氨水的存在,通过脱除电石渣中的铁化物和残碳,有效提高了微粉碳酸钙的质量和白度,同时具有工艺流程简单、操作容易、能耗低的特点。
附图说明
图1为本实用新型的一种利用电石渣制备微粉碳酸钙的装置的结构原理图;
图中,i—精制单元,ii—碳化单元,iii—增浓压滤单元,iv—干燥单元,1—强磁磁选机,2—混合搅拌槽,3—第一水力旋流器,4—浮选搅拌槽,5—浮选机,6—碳化槽,7—浓缩机,8—第二水力旋流器,9—压滤机,10—烘干打散机,11—产品收集器,a—电石渣原料,b—铁化物,c—固态杂质,d—微粉碳酸钙。
具体实施方式
下面结合附图和具体实施例对本实用新型做进一步的详细说明。
如图1所示,一种利用电石渣制备微粉碳酸钙的装置,包括精制单元i、碳化单元ii、增浓压滤单元iii及干燥单元iv;所述精制单元i包括强磁磁选机1、混合搅拌槽2、第一水力旋流器3、浮选搅拌槽4及浮选机5;所述碳化单元ii包括至少两组碳化槽6;所述增浓压滤单元iii包括浓缩机7、第二水力旋流器8及压滤机9;所述干燥单元iv包括烘干打散机10及产品收集器11;所述强磁磁选机1的进料口用于输入电石渣原料a,强磁磁选机1的第一出料口用于排放磁选出的铁化物b,强磁磁选机1的第二出料口用于输出去除铁化物b的电石渣原料a,强磁磁选机1的第二出料口与混合搅拌槽2的顶部进料口相连通,混合搅拌槽2的底部出料口与第一水力旋流器3的顶部进料口相连通,第一水力旋流器3的底部排渣口用于排出固态杂质c,第一水力旋流器3的顶部浆液出口用于排出电石渣浆料;所述第一水力旋流器3的顶部浆液出口与浮选搅拌槽4的顶部进料口相连通,浮选搅拌槽4的底部出料口与浮选机5的顶部进料口相连通,浮选机5的排渣口用于排出固态杂质c,浮选机5的浆液出口用于排出电石渣浆料;所述浮选机5的浆液出口与碳化槽6的顶部进料口相连通,碳化槽6的底部出料口用于排出碳酸钙浆液,碳化槽6的顶部澄清液出口与混合搅拌槽2及浮选搅拌槽4的顶部进料口相连通;所述碳化槽6的底部出料口与浓缩机7的顶部进料口相连通,浓缩机7的顶部澄清液出口与混合搅拌槽2及浮选搅拌槽4的顶部进料口相连通,浓缩机7的底部出料口与第二水力旋流器8的顶部进料口相连通,第二水力旋流器8的顶部低浓度浆液出口与浓缩机7的顶部进料口相连通,第二水力旋流器8的底部高浓度浆液出口与压滤机9的进料口相连通,压滤机9的滤出液出口与混合搅拌槽2及浮选搅拌槽4的顶部进料口相连通,压滤机9的出料口与烘干打散机10的进料口相连通,烘干打散机10的出料口与产品收集器11的进料口相连通,产品收集器11的出料口用于排出微粉碳酸钙d。
本实施例中,电石渣原料a的粒度≤0.1mm,电石渣原料a的含水率为13%~16%,电石渣原料a中的铁化物b含量为0.5%,电石渣原料a中的硅含量为4%~5%,电石渣原料a中的碳含量为2%;浮选剂分为脱硅浮选剂和脱碳浮选剂,脱硅浮选剂采用六偏磷酸钠和十二胺,脱碳浮选剂采用煤油和12#油;碳化槽6数量为两个,一个用于进行常规碳化反应,另一个用于澄清液的增浓,且两个碳化槽6交替使用;碳化槽6的顶部澄清液、浓缩机7的顶部澄清液、压滤机9的滤出液均直接返回精制单元i的混合搅拌槽2及浮选搅拌槽4中进行循环利用;第二水力旋流器8的顶部低浓度浆液直接返回浓缩机7中进行循环利用。
一种利用电石渣制备微粉碳酸钙的方法,采用了所述的利用电石渣制备微粉碳酸钙的装置,包括如下步骤:
步骤一:精制
步骤①:将电石渣原料a经计量后输入强磁磁选机1内,通过强磁磁选机1将电石渣原料a内的铁化物b分离排出,使电石渣原料a中的铁化物b含量降到0.15%以下;
步骤②:将脱除了铁化物b的电石渣原料a输入混合搅拌槽2内,同时向混合搅拌槽2内输入热水,在混合搅拌槽2内制备出质量浓度为30%~40%的电石渣浆料;
步骤③:将制备好的电石渣浆料输入第一水力旋流器3内,通过第一水力旋流器3将电石渣浆料中的固态杂质c分离排出;
步骤④:将脱除了固态杂质c的电石渣浆料输入浮选搅拌槽4内,同时向浮选搅拌槽4内输入定量的捕捉剂、起泡剂和ph值调节剂,使电石渣浆料的ph值处于7.0~7.5之间;
步骤⑤:将调整好ph值的电石渣浆料输入浮选机5内,同时向浮选机5内输入脱硅浮选剂,并且进行三次反浮选脱硅,使电石渣原料a中的硅含量降到1.7%以下,脱硅过程中产生的固态杂质c直接分离排出;
步骤⑥:当电石渣浆料完成三次反浮选脱硅后,再向浮选机5内输入脱碳浮选剂,而且只进行一次浮选脱碳,使电石渣原料a中的碳含量降到0.7%以下,脱碳过程中产生的固态杂质c直接分离排出;
步骤二:碳化
步骤①:将脱除了硅和碳的电石渣浆料输入碳化槽6内,同时向碳化槽6内输入热水,使电石渣浆料的质量浓度降到10%~15%,并且将电石渣浆料的温度调整到50℃~80℃;
步骤②:向碳化槽6内输入二氧化碳气体,通过搅拌使电石渣浆料与二氧化碳气体发生反应,反应时间为2h~10h,直至在碳化槽6内形成碳酸钙浆液;
步骤三:增浓压滤
步骤①:将碳酸钙浆液输入浓缩机7内,通过浓缩机7将碳酸钙浆液的质量浓度提高到45%~50%;
步骤②:将浓缩后的碳酸钙浆液输入第二水力旋流器8内,通过第二水力旋流器8将碳酸钙浆液进行进一步增浓,直到将碳酸钙浆液的质量浓度提高到70%~75%;
步骤③:将增浓后的碳酸钙浆液输入压滤机9内,通过压滤机9对碳酸钙浆液进行脱水,直到形成含水率为12%~17%的碳酸钙滤饼;
步骤四:干燥
步骤①:将脱水后的碳酸钙滤饼输入烘干打散机10内,通过烘干打散机10对碳酸钙滤饼进行干燥和打碎,干燥温度为70℃~120℃,直至形成含水率<1%的微粉碳酸钙d;
步骤②:将微粉碳酸钙d输入产品收集器11内进行存储。
实施例中的方案并非用以限制本实用新型的专利保护范围,凡未脱离本实用新型所为的等效实施或变更,均包含于本案的专利范围中。
起点商标作为专业知识产权交易平台,可以帮助大家解决很多问题,如果大家想要了解更多知产交易信息请点击 【在线咨询】或添加微信 【19522093243】与客服一对一沟通,为大家解决相关问题。
此文章来源于网络,如有侵权,请联系删除


