一种纳米级氧化钇粉末的制备方法与流程



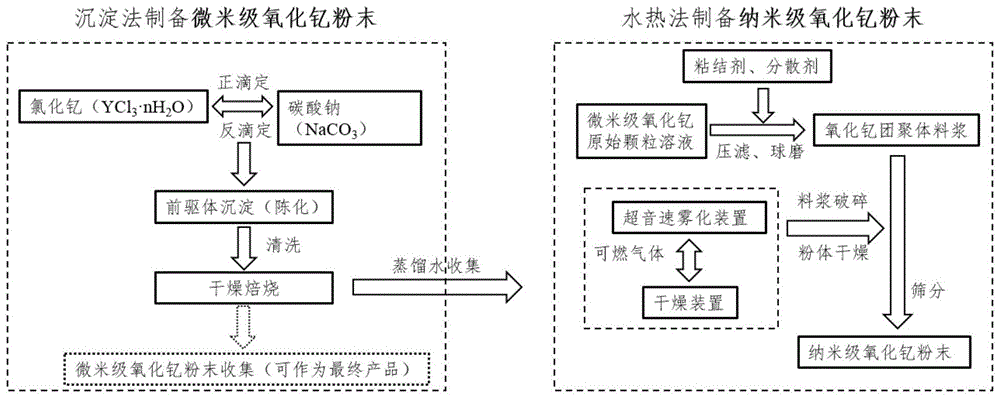
本发明涉及化工粉体制备技术领域,特别提供一种纳米级氧化钇粉末的制备方法。
背景技术:
氧化钇(y2o3)具有耐热、耐腐蚀、高温稳定性好、介电常数高等一系列优良的物理和化学性能,可作为功能材料应用于航空、航天、电子、原子能和高技术陶瓷等行业。其中,纳米氧化钇粉末因其在光、电、物理化学反应等领域表现出优异的性能而备受关注。例如近年来用热喷涂的方法在刻蚀机反应室和静电卡盘的表面上制备陶瓷层取代阳极氧化铝涂层的技术发展迅速,由于氧化钇涂层具有更好的抗等离子体冲蚀的性能和更长的使用寿命,已成为目前已知的等离子刻蚀机内反应室铝质零件涂层的最佳选择。然而,目前具有产业化规模生产热喷涂用高纯纳米氧化钇粉末的供应商均出自国外,产品成本与售价都很高,并且供货非常紧张。
主要传统制备纳米氧化钇粉末包括溶胶-凝胶法、气相沉积法、微乳液法和水热法。目前制备氧化钇粉体大多直接采用草酸沉淀工艺,制备的氧化钇粒径为2.5-6.0μm,颗粒尺寸大且分布不均匀,生产过程中均有大量废水产生,对环境影响大,且得到的粉体易团聚,表观粒度较大,难以满足市场需求。另一方面,国内的真空脱水设备落后且氧化钇的烧结致密化温度高达1600℃以上,烧结过程中存在着颗粒之间的烧结,烧结后还需进行破碎、分级,因此导致产率很低。专利号cn108751247a中公开了一种具有稳定bet的纳米氧化钇的制备方法,采用化学沉淀法获得了稳定、颗粒均匀的纳米级氧化钇;专利申请号cn201910639121.3中公开了一种纳米氧化钇粉体的制备方法,同样采用化学沉淀法获得了粒径小且分布较窄的纳米级氧化钇。然而现有技术中向钇盐溶液中滴定沉淀剂易导致反应体系浓度不均匀,实际生产操作中钇离子的生长速度难以定量控制,制备的氧化钇粉体产率不高,如果需要提高产率,又会导致制备的氧化钇粉体粒径较大且粒径分布较宽。
本发明将传统的沉淀制备法与水热法结合,制备出高纯纳米氧化钇粉末,并在后续的雾化干燥工艺中引入可燃气体,极大提高了粉末产率与质量。
技术实现要素:
本发明的目的是解决传统的纳米氧化钇粉末制备过程中,颗粒尺寸大且分布不均匀,生产过程中均有大量废水产生,对环境影响大等问题,提供一种经济、环保、适于产业化规模生产的纳米氧化钇粉末的制备方法。
本发明是通过如下技术方案实现上述目的的:
一种纳米级氧化钇粉末的制备方法,先用沉淀法制备微米级氧化钇粉末,随后用水热法制备纳米级氧化钇粉末,包括如下步骤:
(1)采用碳酸钠水溶液作为沉淀剂,氯化钇水溶液作为料液,控制反应温度为70-90℃,搅拌速度250-350转/分钟,经陈化处理、过滤、无水乙醇洗涤、真空干燥,得到蓬松的白色粉末状碳酸钇前驱体;
(2)将碳酸钇前驱体置于马弗炉中,在650-750℃下焙烧1-2h,制得微米级氧化钇原始颗粒,并通过蒸馏水收集得微米级氧化钇原始颗粒溶液;
(3)对步骤(2)收集的微米级氧化钇原始颗粒溶液进行压滤,随后加入粘结剂、分散剂进行调浆、球磨制得氧化钇团聚体料浆;
(4)采用可燃气体对步骤(3)的料浆进行雾化干燥制粒;
(5)最后筛分得到致密的高纯纳米级氧化钇粉末。
优选的,所述纳米级氧化钇粉末的制备方法步骤(1)所用的氯化钇料液为工业级,纯度≥99.95%。
优选的,所述纳米级氧化钇粉末的制备方法步骤(1)配制的氯化钇水溶液的料液浓度为0.05-0.2mol/l,碳酸钠水溶液的溶液浓度为0.1-0.2mol/l,两者摩尔浓度比为1:1.4-1:1.5,反应过程ph控制在5.9-6.0,陈化时间6~12小时。
优选的,所述纳米级氧化钇粉末的制备方法步骤(1)中的真空干燥温度范围为60~100℃,干燥时间为2~6小时。
优选的,所述纳米级氧化钇粉末的制备方法步骤(2)中制备的微米级氧化钇粉末的粒度小于5μm,粒度分布小于1。步骤(2)制备的微米级氧化钇粉末可直接用于要求微米级粉末的场合。
优选的,所述纳米级氧化钇粉末的制备方法步骤(3)中调浆后氧化钇团聚体料浆中微米级氧化钇原始颗粒与水的质量比为1:1-1:2;粘结剂为聚乙烯醇或聚乙烯吡咯烷酮,分散剂为乙醇或丙二醇或聚乙二醇,粘结剂与分散剂之和与微米级氧化钇原始颗粒的质量比为2:98~5:95。
优选的,所述纳米级氧化钇粉末的制备方法步骤(4)中雾化干燥所用的可燃气体燃烧后仅产生水和挥发性气体,包括但不限于甲烷。
优选的,所述纳米级氧化钇粉末的制备方法步骤(4)中雾化干燥的进口温度为150-350℃,出口温度为100-250℃。
优选的,所述纳米级氧化钇粉末的制备方法步骤(5)中筛分后的纳米级氧化钇粉末的粒度优选范围为20-60μm,它由尺寸小于80nm的高纯氧化钇晶粒组成。专利号cn108751247a采用的工艺需控制碳酸钇的装钵量以及灼烧温度和时间,实际生产中工艺难以有效控制;另一方面,该专利灼烧后过筛得纳米稀土氧化钇,长期使用,筛网与粉料接触过程中,粉料中容易引入金属杂质且粉体分级较为宽泛。
本发明的设计思想是提高纳米级氧化钇粉末的产率及品质,先制备微米级氧化钇粉末,进一步地采用水热法制备纳米级氧化钇粉末。改变传统的草酸盐沉淀法制备稀土氧化物的工艺,采用碳酸钠作为第一步沉淀工艺的沉淀剂,进一步地在传统水热工艺的基础上采用可燃性气体作为雾化干燥气体。
本发明的优点及有益效果是:本发明的纳米级氧化钇粉末制备方法由于不需要氧化钇粉末作为原料,因此具有原料成本低,设备要求低的优点,采用碳酸钇作为氧化钇焙烧前驱体,相比传统的草酸钇或碳酸氢钇,生成的氧化钇粉末不易团聚,且焙烧过程生成二氧化碳和水蒸气并逸出,这些气体抑制了焙烧过程中粒子的团聚。另一方面,第一步制备的微米级氧化钇同样可用于市场。本发明同时解决了传统方法脱水效率低下、团聚体烧结致密化困难以及产率低等问题,制备的纳米级氧化钇粉末纯度≥99.9%,晶粒尺寸≤80nm,适于产业化规模生产。
附图说明
图1为本发明制备纳米级氧化钇粉末的工艺流程图;
图2为本发明实施例1制备纳米级氧化钇粉末的sem图。
图3为本发明实施例2制备微米级氧化钇粉末的sem图。
图4为本发明实施例3制备纳米级氧化钇粉末的sem图。
图5为本发明对比实施例1制备纳米级氧化钇粉末的sem图。
具体实施方式
下面结合附图和实施例对本发明作进一步的详细说明。可以理解的是,此处所描述的具体实施例仅仅用于解释本发明,而非对本发明的限定。
在更加详细地讨论示例性实施例之前应当提到的是,一些示例性实施例被描述成作为流程图描绘的处理或方法。虽然流程图将各步骤描述成顺序的处理,但是其中的许多步骤可以被并行地、并发地或者同时实施。此外,各步骤的顺序可以被重新安排。当其操作完成时所述处理可以被终止,但是还可以具有未包括在附图中的附加步骤。
实施例1
如图1所示,本实施例制备纳米级氧化钇粉末的步骤如下:
(1)取10kg纯度≥99.95%的工业高纯氯化钇原料,溶于蒸馏水,控制氯化钇料液浓度0.1mol/l,控制反应温度为80℃,搅拌速度300转/分钟,随后用浓度为0.15mol/l的碳酸钠溶液调节混合溶液ph值在5.9-6范围,并不断搅拌直至形成白色沉淀;将此沉淀陈化8小时,过滤后用无水乙醇洗涤3遍,随后于80℃真空干燥4小时,得到蓬松的白色粉末状碳酸钇前驱体。
(2)将碳酸钇置于马弗炉中,在700℃下焙烧1h,制得微米级氧化钇原始颗粒,并通过蒸馏水收集得微米级氧化钇原始颗粒溶液;
(3)对步骤(2)收集的微米级氧化钇原始颗粒溶液进行压滤,调节微米级氧化钇原始颗粒与水的质量比为1:1.5,然后加入聚乙烯醇粘结剂,聚乙二醇分散剂进行调浆,粘结剂与分散剂之和与微米级氧化钇原始颗粒的质量比为4:96;对料浆进行机械球磨3小时,得到氧化钇团聚体料浆;
(4)水热法粉末采用离心式超音速雾化和粉末干燥,进口温度为300℃,出口温度为180℃,通过雾化装置设置的喷枪喷出的可燃气体,使氧化钇团聚体瞬时烧结致密化、球化,最后并通过粉末收集装置收集;避免了现有技术中向钇盐溶液中滴定沉淀剂易导致反应体系浓度不均匀,从而在实际生产操作中钇离子的生长速度难以定量控制的问题,烧结制备的氧化钇粉体较均匀,从而在不增加粒径分布的基础上提高产率。
(5)筛分后的纳米级氧化钇粉末的粒度优选范围为20-60μm,经测试粉体d50为2.54μm,粒度分布[(d90-d10)/2d50]为0.52,团聚较少,它由尺寸小于80nm的高纯氧化钇晶粒组成,其晶粒为圆形,大小均匀,如图2所示。
实施例2
本实施例制备纳米级氧化钇粉末的步骤如下:
(1)取5kg纯度≥99.95%的工业高纯氯化钇原料,溶于蒸馏水,控制氯化钇料液浓度0.15mol/l,控制反应温度为70℃,搅拌速度300转/分钟,随后用浓度为0.2mol/l的碳酸钠溶液调节混合溶液ph值在5.9-6范围,并不断搅拌直至形成白色沉淀;将此沉淀陈化8小时,过滤后用无水乙醇洗涤3遍,随后于80℃真空干燥4小时,得到蓬松的白色粉末状碳酸钇前驱体。
(2)将碳酸钇置于马弗炉中,在700℃下焙烧2h,制得微米级氧化钇粉末,通过粉末收集装置收集。步骤(2)制备的微米级氧化钇粉末可直接用于要求微米级粉末的场合,粉末如图3所示。
实施例3
本实施例制备纳米级氧化钇粉末的步骤如下:
(1)取10kg纯度≥99.95%的工业高纯氯化钇原料,溶于蒸馏水,控制氯化钇料液浓度0.1mol/l,控制反应温度为70℃,搅拌速度300转/分钟,随后用浓度为0.15mol/l的碳酸钠溶液调节混合溶液ph值在5.9-6范围,并不断搅拌直至形成白色沉淀;将此沉淀陈化8小时,过滤后用无水乙醇洗涤3遍,随后于80℃真空干燥4小时,得到蓬松的白色粉末状碳酸钇前驱体。
(2)将碳酸钇置于马弗炉中,在750℃下焙烧2h,制得微米级氧化钇粉末,并通过蒸馏水收集;
(3)对步骤(2)收集的微米级氧化钇原始颗粒溶液进行压滤,调节微米级氧化钇原始颗粒与水的质量比为1:1.8,然后加入聚乙烯吡咯烷酮粘结剂,丙二醇分散剂进行调浆,粘结剂与分散剂之和与微米级氧化钇原始颗粒的质量比为4:96;对料浆进行机械球磨3小时,得到氧化钇团聚体料浆;
(4)水热法粉末采用离心式超音速雾化和粉末干燥,进口温度为250℃,出口温度为150℃,通过雾化装置设置的喷枪喷出的可燃气体,使氧化钇团聚体瞬时烧结致密化、球化,并通过粉末收集装置收集;
(5)筛分后的纳米级氧化钇粉末的粒度优选范围为20-60μm,经测试粉体d50为2.62μm,粒度分布[(d90-d10)/2d50]为0.67,团聚较少,它由尺寸小于80nm的高纯氧化钇晶粒组成,其晶粒为圆形,大小均匀,如图4所示。
实施例4
本实施例制备纳米级氧化钇粉末的步骤如下:
(1)取10kg纯度≥99.95%的工业高纯氯化钇原料,溶于蒸馏水,控制氯化钇料液浓度0.1mol/l,控制反应温度为70℃,搅拌速度350转/分钟,随后用浓度为0.15mol/l的碳酸钠溶液调节混合溶液ph值在5.9-6范围,并不断搅拌直至形成白色沉淀;将此沉淀陈化8小时,过滤后用无水乙醇洗涤3遍,随后于80℃真空干燥4小时,得到蓬松的白色粉末状碳酸钇前驱体。
(2)将碳酸钇置于马弗炉中,在750℃下焙烧2h,制得微米级氧化钇粉末,并通过蒸馏水收集;
(3)对步骤(2)收集的微米级氧化钇原始颗粒溶液进行压滤,调节微米级氧化钇原始颗粒与水的质量比为1:1.8,然后加入聚乙烯吡咯烷酮粘结剂,乙醇分散剂进行调浆,粘结剂与分散剂之和与微米级氧化钇原始颗粒的质量比为4:96;在砂磨机中加入0.3-0.5mm的锆珠研磨2h,得到氧化钇团聚体料浆;
(4)水热法粉末采用离心式超音速雾化和粉末干燥,进口温度为250℃,出口温度为150℃,通过雾化装置设置的喷枪喷出的可燃气体,使氧化钇团聚体瞬时烧结致密化、球化,并通过粉末收集装置收集;
(5)筛分后的纳米级氧化钇粉末的粒度优选范围为20-60μm,经测试粉体d50为2.82μm,粒度分布[(d90-d10)/2d50]为0.51,团聚较少,它由尺寸小于80nm的高纯氧化钇晶粒组成,其晶粒为圆形,大小均匀筛分后的纳米级氧化钇粉末的粒度优选范围为20-60μm,它由尺寸小于80nm的高纯氧化钇晶粒组成。
对比实施例1
本对比实施例制备纳米级氧化钇粉末的步骤如下:
(1)取10kg纯度≥99.95%的工业高纯氯化钇原料,溶于蒸馏水,控制氯化钇料液浓度0.1mol/l,控制反应温度为70℃,搅拌速度350转/分钟,随后用浓度为0.15mol/l的碳酸钠溶液调节混合溶液ph值在5.9-6范围,并不断搅拌直至形成白色沉淀;将此沉淀陈化8小时,过滤后用无水乙醇洗涤3遍,随后于80℃真空干燥4小时,得到蓬松的白色粉末状碳酸钇前驱体。
(2)将碳酸钇置于马弗炉中,在750℃下焙烧2h,制得微米级氧化钇粉末,并通过蒸馏水收集;
(3)对步骤(2)收集的微米级氧化钇原始颗粒溶液进行压滤,调节微米级氧化钇原始颗粒与水的质量比为1:1.8,然后加入聚乙烯吡咯烷酮粘结剂,乙醇分散剂进行调浆,粘结剂与分散剂之和与微米级氧化钇原始颗粒的质量比为4:96;在砂磨机中加入0.3-0.5mm的锆珠研磨2h,得到氧化钇团聚体料浆;
(4)水热法粉末采用离心式超音速雾化和粉末干燥,进口温度为250℃,出口温度为150℃,本对比实施例仅利用水平方向作高速旋转的圆盘给予溶液以离心力,使其以高速甩出,形成微米级氧化钇原始颗粒溶液薄膜、细丝或液滴,受到地心吸力而下落,并通过粉末收集装置收集;
(5)筛分后的纳米级氧化钇粉末的粒度优选范围为20-60μm,球形,大小不均匀,分散不好,有团聚,它由尺寸小于80nm的高纯氧化钇晶粒组成,如图5所示。
本对比实施例可表明,本发明中通过雾化装置设置的喷枪喷出的可燃气体,使氧化钇团聚体瞬时烧结致密化、球化的工艺对粉末均匀度有明显影响,增加该步骤可使制备出的纳米级氧化钇粉末不易团聚且粒度较好。
综上所述,本发明以具体实施例如上,但上述实施例并非用以限制本发明,本领域的普通技术人员,在不脱离本发明的精神和范围内,均可作各种更动与润饰,因此本发明的保护范围以权利要求界定发范围为准。
起点商标作为专业知识产权交易平台,可以帮助大家解决很多问题,如果大家想要了解更多知产交易信息请点击 【在线咨询】或添加微信 【19522093243】与客服一对一沟通,为大家解决相关问题。
此文章来源于网络,如有侵权,请联系删除


