一种镍钴溶液净化除硅的方法与流程



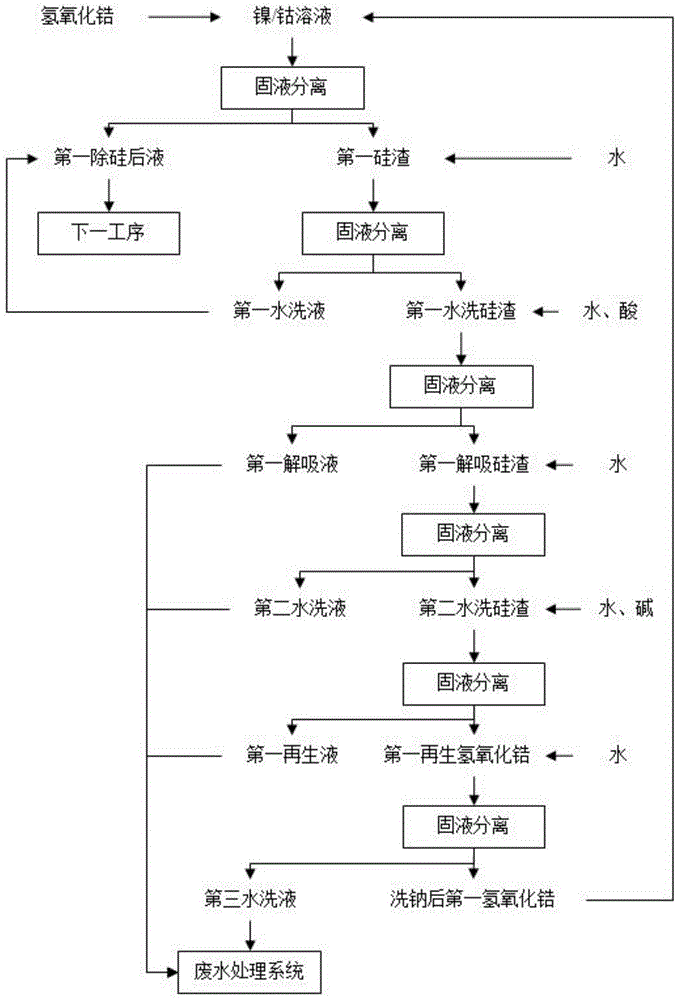
本发明属于溶液除杂技术领域,具体涉及一种镍钴溶液净化除硅的方法。
背景技术:
在当前全球面临的资源枯竭、节能减排的双重压力下,大力发展新能源,走低碳化经济发展道路,已经成为国际能源发展和经济转型的基本共识。随着电池行业三元前驱体的快速发展,市场对镍钴系列产品的需求预期乐观,主要产品硫酸镍、硫酸钴等可用于电池、电镀领域。
硫酸镍、硫酸钴生产工艺通常包括以下工序:含镍钴原料的溶解(通常为酸溶)、化学沉淀除杂或萃取除杂中的一种或两种、除油、蒸发结晶等。其中镍钴溶液中硅含量通常(以sio2计)高达0.1-0.5g/l,为避免系统中硅的累积造成设备结垢、对下一工序产生影响(如:萃取时产生第三相导致难于分相)以及对产品质量的影响,根据文献报道,对于含硅水溶液,根据体系酸碱度不同,除硅方法主要为中和法、物理或化学混凝法、引晶法、吸附法、超滤法等,上述方法主要为水处理领域和造纸行业的深度或非深度除硅技术。目前对镍钴溶液体系中硅的去除大多采用碱性物质进行中和除杂,所用碱性物质主要为石灰乳/石灰石/生石灰/碳酸钠/碳酸氢钠/氢氧化钠/氢氧化镍/氢氧化钴/氢氧化铜/氢氧化锌中的一种或多种,上述方法通常需在加热条件下进行、反应缓慢(通常反应时间为3-10h)、引入新的杂质离子导致后续除杂困难(如引入钙离子,使得在萃取时钙渣堵塞管道,降低生产效率)、产渣量大、主金属的直收率较低,且除硅试剂不可再生再使用。
对于镍钴溶液除硅的相关专利文献报道主要为金川集团申请号为cn201610709019.2的《一种镍溶液深度净化除硅的方法》和cn201911014207.3的《一种镍溶液吸附除硅的方法》,两项专利均以自制氢氧化镍进行深度除硅,该方法需要加热、氢氧化镍用量较大,而且氢氧化镍可重复利用次数仅为3-4次,与本发明相比,本发明提供一种能耗低、产渣量少、主金属损失量小、且不引入杂质离子的除硅试剂,且除硅试剂可多次再生再利用。另有申请号为201210120102.8的《一种精制硫酸镍的方法》,采用化学沉淀法结合萃取法进行除杂,其工艺流程较为复杂,且除杂时引入氟化物增加后续除杂负担,同时对环境影响较大;申请号为201310098137.0的《一种硫酸镍的纯化方法》采用介孔二氧化硅吸附剂进行吸附除杂,后经膜过滤进行固液分离,该吸附剂失效后可通过酸化进行再生再利用,但同时该方法需在加热条件下进行,且吸附时间较长,生产效率较低;申请号为201611136085.1的《一种硫酸镍钴锰溶液除氟、硅离子的方法》采用常见的除杂技术,即对酸溶镍钴锰溶液进行中和除杂,再经萃取除杂,后经除油制备精制硫酸镍钴锰溶液,但处理的镍钴锰离子总浓度仅为30-60g/l,若通过蒸发结晶工艺生产硫酸镍钴产品,则由于该工艺生产的精制溶液金属含量较低,在蒸发结晶时蒸发量较大,能耗较高,且处理效率较低。由于镍钴溶液中硅的存在,通常当硅(以sio2计)的质量浓度高于100mg/l时,在萃取除杂时将产生第三相,这将导致分相困难,且降低萃取剂的利用率和生产效率,而且硅的存在必将降低最终产品质量。采用普通方法除硅引入的杂质将增加后续除杂负担、能耗较高、处理效率较低,且除硅试剂不可再生,对于质量有更高要求的镍钴盐结晶产品(如电池级硫酸镍钴)而言,在除杂时对硅杂质的含量要求也更高,故行业内迫切需要开发一种新的除硅试剂或除硅方法,对镍钴溶液进行深度除硅的同时要求能耗低、处理效率高、不引入杂质离子且对下一工序无影响,且最终产品杂质达到要求,为解决上述问题,本发明提供一种高直收率、高生产效率、低产渣量、低能耗、并且除硅试剂可再生的一种除硅方法。
技术实现要素:
本发明旨在解决上述技术问题,提供一种镍钴溶液净化除硅的方法,所述方法成本低、效率高、操作简单、能耗低、产渣量少、主金属损失量少、不引入杂质离子、处理主金属离子浓度范围宽、采用的除硅试剂可再生使用,经济环保。
本发明的技术方案为:
一种镍钴溶液净化除硅的方法,所述方法使用氢氧化锆作为除硅试剂。
进一步地,所述除硅试剂氢氧化锆的用量为硅(以sio2计)质量的60-100倍。
进一步地,所述镍钴溶液为硫酸镍、硫酸钴溶液或二者的混合溶液。
进一步地,所述镍钴溶液ph为2.5-4.0,镍钴溶液中主金属离子浓度为30-130g/l。
进一步地,所述镍钴溶液净化除硅的方法,包括如下步骤∶
s1除硅:向酸溶后镍钴溶液中加入除硅试剂氢氧化锆,反应结束后固液分离,得到第一硅渣和第一除硅后液;第一硅渣进入洗涤工序;第一硅渣浆化洗涤后得到第一水洗液和第一水洗硅渣;第一水洗液与第一除硅后液合并进入下一工序,第一水洗硅渣进入解吸工序;
s2解吸:向第一水洗硅渣中加入水,搅拌浆化,加入无机酸调节ph使硅溶出,解吸结束后固液分离,得到第一解吸液和第一解吸硅渣,第一解吸液进入废水处理系统,第一解吸硅渣进入解吸后洗涤工序;第一解吸硅渣浆化洗涤后得到第二水洗液和第二水洗硅渣;第二水洗液进入废水处理系统,第二水洗硅渣进入再生工序;
s3再生:向第二水洗硅渣中加入水,搅拌浆化,加入碱调节ph,再生结束后固液分离,得到第一再生液和第一再生氢氧化锆,第一再生液进入废水处理系统,第一再生氢氧化锆进入洗钠工序;
s4洗钠:向第一再生氢氧化锆中加入水进行浆化洗涤,洗涤结束后得到第三水洗液和洗钠后第一氢氧化锆;第三水洗液进入废水处理系统,洗钠后第一氢氧化锆进入步骤s1-s4,多次循环步骤s1-s4。
进一步地,步骤s1除硅的反应时间为0.5-2h,步骤s2解吸的时间和s3再生的时间均为1-2h。
进一步地,步骤s2中,所述无机酸为硫酸,解吸ph为1.0-1.5;步骤s3中,所述碱为10%-50%的氢氧化钠水溶液,再生ph为10.0-11.0。
进一步地,步骤s4中,所述洗钠的级数为2-3级。
进一步地,步骤s1-s4中,反应或洗涤温度均为20℃-80℃。
进一步地,步骤s1-s4中,所述浆化洗涤用水量、所述解吸与再生时所加水的量均为湿基质量的3-6倍。
本发明的工艺流程如图1所示。
由于采用上述技术方案,本发明的有益效果为:
(1)除硅后液中硅(以sio2计)浓度低于0.01g/l,硅(以sio2计)的去除率高于96%;
(2)避免系统硅累积,避免在萃取时发生三相导致的一系列问题,改善萃取车间工作环境;
(3)降低主金属的损失量,提高系统主金属的直收率;
(4)不引入杂质离子,避免后续除杂困难;
(5)处理主金属离子浓度范围宽,降低后续工序的能耗;
(6)除硅时间短,处理效率高;
(7)除硅试剂可再生,除硅工序只产生少量废水,是一种环境友好型除硅技术。
附图说明
图1为本发明工艺流程图。
具体实施方式
下面将结合本发明实施例中的附图,对本发明实施例中的技术方案进行清楚、完整地描述,显然,所描述的实施例仅仅是本发明一部分实施例,而不是全部的实施例。基于本发明中的实施例,本领域普通技术人员在没有做出创造性劳动前提下所获得的所有其他实施例,都属于本发明保护的范围。
实施例1
取硫酸钴溶液10l,溶液初始ph=4.0,加入氢氧化锆(锆含量57.29%)80.0g,20℃下搅拌反应0.5h,固液分离,得到第一除硅后液和第一硅渣,第一硅渣以6倍湿基质量的水在20℃下浆化洗涤0.5h,固液分离,得到第一水洗硅渣和第一水洗液。向第一水洗硅渣中加入3倍湿基质量的水,滴加93%硫酸至体系ph=1.2,20℃条件下搅拌浆化反应1h,固液分离,得到第一解吸硅渣和第一解吸液,向第一解吸硅渣中加入3倍湿基质量的水,在20℃下浆化洗涤0.5h,固液分离,得到第二水洗硅渣和第二水洗液,向第二水洗硅渣中加入3倍湿基质量的水,滴加10%液碱至体系ph=11.0,20℃下浆化搅拌反应1h,固液分离,得到第一再生氢氧化锆和第一再生液,向第一再生氢氧化锆中加入3倍湿基质量的水,20℃下浆化洗涤3次并固液分离,单次洗涤时间为0.5h,得到洗钠后第一氢氧化锆湿基约153g和第三洗液。洗钠后第一氢氧化锆用于二次除硅,得到二次除硅后液和二次硅渣,对二次硅渣再进行解吸、再生、洗钠、除硅,循环进行,得到七次除硅后液和对应的硅渣,除硅前后液成分及硅脱除率如表1-1所示,解吸液成分及硅的液计解吸率如表1-2所示。
表1-1除硅前后钴液成分及硅的液计脱除率
表1-2解吸液硅及液计解吸率计算(%)
说明:吸附量计算按照表1-1的脱除率对应计算,水分按50%计,解吸后硅渣解吸前质量的96%,解吸液体积按0.46l计算,解吸率=解吸量/吸附量×100%。
实施例2
取硫酸镍溶液50l,溶液初始ph=3.0,加入氢氧化锆(锆含量57.29%)930.0g,50℃下搅拌反应1h,固液分离,得到第一除硅后液和第一硅渣,第一硅渣以3倍湿基质量的水在50℃下浆化洗涤0.5h,固液分离,得到第一水洗硅渣和第一水洗液。向第一水洗硅渣中加入6倍湿基质量的水,滴加93%硫酸至体系ph=1.5,50℃下搅拌浆化反应2h,固液分离,得到第一解吸硅渣和第一解吸液,向第一解吸硅渣中加入6倍湿基质量的水,在50℃下浆化洗涤0.5h,固液分离,得到第二水洗硅渣和第二水洗液,向第二水洗硅渣中加入6倍湿基质量的水,滴加30%液碱至体系ph=10.0,50℃下搅拌反应2h,固液分离,得到第一再生氢氧化锆和第一再生液,向第一再生氢氧化锆中加入6倍湿基质量的水,50℃下浆化洗涤2次,固液分离,单次洗涤时间为1h,得到洗钠后第一氢氧化锆约1785g和第三洗液。洗钠后第一氢氧化锆用于二次除硅,得到二次除硅后液和二次硅渣,对二次硅渣再进行解吸、再生、洗钠、除硅,循环进行,得到七次除硅后液和对应的硅渣,除硅前后液成分及硅脱除率如表2-1,解吸液成分及硅的液计解吸率如表2-2所示。
表2-1除硅前后镍液成分及液计去除率
表2-2解吸液硅及液计解吸率计算(%)
说明:吸附量计算按照表2-1的脱除率对应计算,解吸液体积按10.713l计算。
实施例3
取硫酸镍溶液1m3,溶液初始ph=2.5,加入氢氧化锆(锆含量57.29%)50.0kg,80℃下搅拌反应2h,固液分离,得到第一除硅后液和第一硅渣,第一硅渣以6倍湿基质量的水在80℃下浆化洗涤1h,固液分离,得到第一水洗硅渣和第一水洗液。向第一水洗硅渣中加入3倍湿基质量的水,滴加93%硫酸至体系ph=1.0,80℃下搅拌浆化反应2h,固液分离,得到第一解吸硅渣和第一解吸液,向第一解吸硅渣中加入3倍湿基质量的水,在80℃下浆化洗涤1h,固液分离,得到第二水洗硅渣和第二水洗液,向第二水洗硅渣中加入3倍湿基质量的水,滴加50%液碱至体系ph=11.0,80℃下搅拌反应2h,固液分离,得到第一再生氢氧化锆和第一再生液,向第一再生氢氧化锆中加入3倍湿基质量的水,80℃下浆化洗涤3次,单次洗涤时间为0.5h,固液分离,得到洗钠后第一氢氧化锆约96kg和第三洗液。洗钠后第一氢氧化锆用于二次除硅,得到二次除硅后液和二次硅渣,对二次硅渣进行解吸、再生、洗钠、除硅,循环进行,得到七次除硅后液和对应的硅渣,除硅前后液成分及硅脱除率如表3-1所示,解吸液成分及硅的液计解吸率如表3-2所示。
表3-1除硅前后镍液成分及液计去除率
表3-2解吸液硅及液计解吸率计算(%)
说明:吸附量计算按照表3-1的脱除率对应计算,解吸液体积按288l计算。
上述说明是针对本发明较佳可行实施例的详细说明,但实施例并非用以限定本发明的专利申请范围,凡本发明所提示的技术精神下所完成的同等变化或修饰变更,均应属于本发明所涵盖专利范围。
起点商标作为专业知识产权交易平台,可以帮助大家解决很多问题,如果大家想要了解更多知产交易信息请点击 【在线咨询】或添加微信 【19522093243】与客服一对一沟通,为大家解决相关问题。
此文章来源于网络,如有侵权,请联系删除


