一种基于氨能源船舶的冷热电三联供复合系统的制作方法



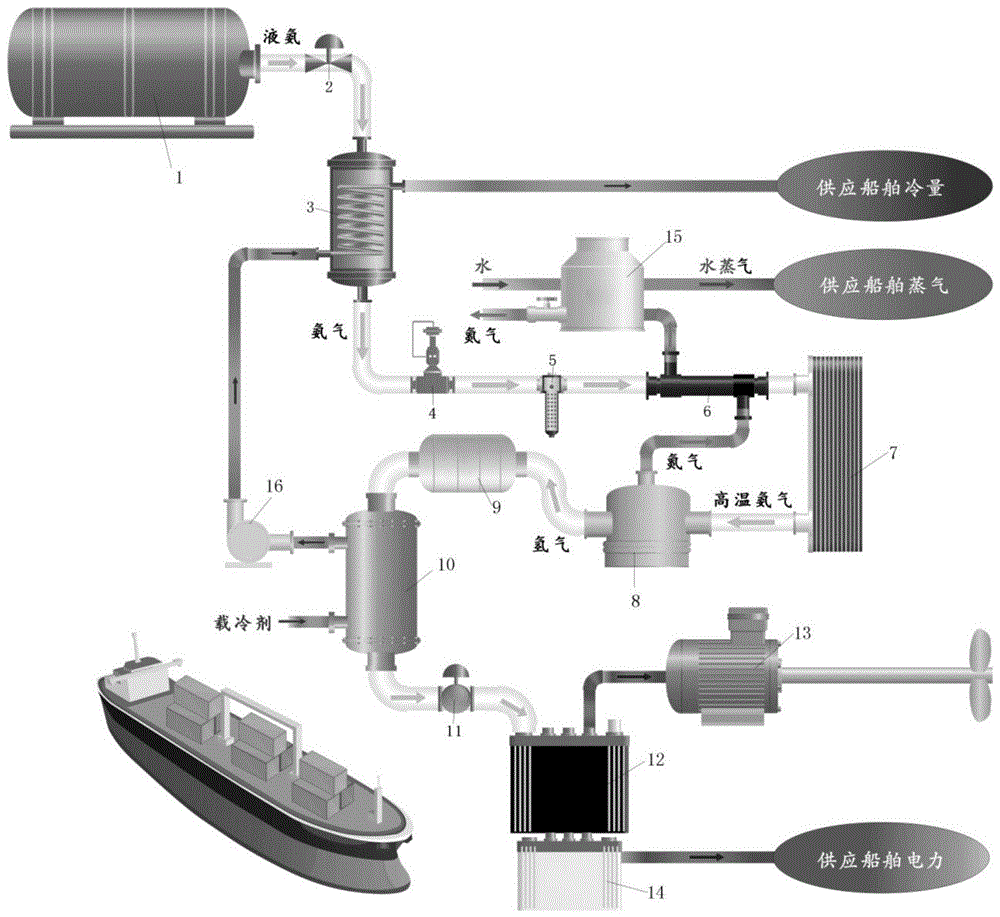
本实用新型涉及液氨能源系统冷热电联产领域,具体而言,尤其涉及一种利用液氨载氢,催化制氢,燃料电池发电和回收利用该过程冷、热能量的氨能源船舶冷热电三联供复合系统。
背景技术:
从2020年起,国际海事组织要求世界航运业施行低于0.5%的全球硫排放限制,而在2050年之前需要将船舶海事的碳排放量减少一半以上。这对于目前大部分使用重油的多硫、多颗粒物排放的船舶行业是一大挑战。环境污染和气候变暖给海洋环境带来了巨大的压力,因此在船舶冷热电系统中优化能源使用效率合理开发高效清洁能源以及其相关转化技术,是目前亟需解决的关键性问题。氢是一种完全清洁可再生终极能源,其热值约为汽油的3倍,远高于天然气且用于燃料电池仅产生水,可完全避免硫氧化物和颗粒物排放,可以预见未来30到50年内大部分船舶都会选用氢作为主要船用燃料。然而,自然状态下游离态氢存在量极少,如何经济低碳环保的富集纯化进而制造氢气从而使用是氢能源推广普及的一大难题。由于技术限制,目前大规模制氢过程(化石燃料重整、电解水以及生物制氢)要么存在污染排放量偏大,耗电量更高,安全性经济性较差等诸多问题。此外,生产后的储氢更是一大难题,例如车用压缩氢气需要生产设计压力为98mpa的储氢罐才能满足要求,液氢储运更加困难需要将氢气在-253℃进行液化,存罐技术难度材料要求更高。上述困难一直阻碍氢能在各种邻域的发展,急需寻找可替代的具有经济性储氢制氢的方法。
氨作为清洁可再生的含氢质量分数17.6%的有机物质,被广泛用于农工业基础性产品和化工原料,目前中国氨产量占世界三分之一,合成氨厂家网络分布全国,其生产技术成熟储运价格低廉。氨在600℃左右常压加入常规催化剂可完全裂解为氢气和氮气且转化率高达99.9%,具有非常大的产氢潜力。相比于氢,氨仅需在常压-33℃或者常温压力7bar左右就可液化,而且液氨的体积能量密度是液氢的1.53倍,在相同体积条件下能量储运率更高。目前,国内加氢站的氢气价格约70元每公斤,而液氨的价格约3000元每吨,其分解得到的氢气约16.7元每公斤,其中还没有对比氢和氨在储存、运输、分解等成本的差价。因此,氨作为载氢-制氢的原料气来源是一种极其有前途的技术形式。
总结目前现有的制氢-储氢技术都集中在高耗能以及高排放方面,纯粹的把制氢和储氢技术割裂开来,制出氢气后并没有进行后续的氢储运的技术衔接,以致后续的压缩、液化以及氢化物储运再次进行大量的能源消耗。这种技术模式导致整个制氢-储氢产业最后的用氢成本远大于化石燃料及相关治理排放的费用,而且用氢时的能源效率并没有抵消制氢-储氢时的能耗排放。
技术实现要素:
根据上述提出现有的制氢-储氢技术把制氢和储氢技术割裂开来造成大量能源消耗的技术问题,而提供一种基于氨能源船舶的冷热电三联供复合系统。本实用新型颠覆性的以氢的储运为开端,制氢和流程内的冷热电联合利用为终端,打破了传统方法先制氢后储运的复杂过程和极高成本,本实用新型以富氢物液氨为储氢载体,通过液氨气化、氨气预热、加热、催化分解以及氢气纯化、燃料电池发电,废氮气换热、液氨气化冷热量回收利用等一系列的能量转换系统及方法,形成一套基于氨能源船舶的冷热电三联供综合系统。
本实用新型采用的技术手段如下:
一种基于氨能源船舶的冷热电三联供复合系统,包括制氢系统、船舶电力供给系统和冷热能量回收换热循环系统;
所述制氢系统包括依次连通的船用液氨储罐、流量调节阀组、气化器、压力调节阀组、干燥过滤器、氨气预热器、电加热器、氨催化分解氢分离单元、氢纯化器、氢冷却器和氢气压力流量控制阀组;
所述船舶电力供给系统包括氢-空气燃料电池、电动机螺旋桨和蓄电池;所述氢冷却器将氢气通入所述氢-空气燃料电池进行发电并将电力输送至所述蓄电池进行储存;所述氢-空气燃料电池将电力输送至船舶的电动机,电动机接收电力推动所述电动机螺旋桨转动使船舶行进;所述船舶电力供给系统还能够为船舶其他用电设备供电;
所述冷热能量回收换热循环系统包括余热锅炉和载冷剂泵;所述余热锅炉通过管路与所述氨气预热器相连通,所述冷热能量回收换热循环系统回收的所述氨催化分解氢分离单元内发生裂解反应后废气氮气所携带的热量经所述氨气预热器供给至所述余热锅炉,所述余热锅炉用于产生饱和蒸汽供应船舶辅机和客舱热量需求;所述载冷剂泵分别通过管路与所述气化器相连通,所述冷热能量回收换热循环系统通过载冷剂在所述气化器内进行冷量回收用于对船舶设备进行冷却以及供应船舶相关冷量需求。
进一步地,所述冷热能量回收换热循环系统通过载冷剂在所述气化器内回收液氨气化的冷量能够供给至所述氢冷却器。
进一步地,所述冷热能量回收换热循环系统回收的所述氨催化分解氢分离单元内发生的裂解反应后废气氮气所携带的热量,首先供给至所述氨气预热器使氨气升温从而减少所述加热器的功耗,然后经所述氨气预热器供给至所述余热锅炉。
进一步地,所述载冷剂为乙二醇水溶液或氮气以及其它防爆载冷剂。
进一步地,所述氨催化分解氢分离单元包括进口歧管、出口歧管和管壳式裂解分离装置;所述管壳式裂解分离装置内填充有催化剂;所述管壳式裂解分离装置设置有氮气出口;所述进口歧管与所述管壳式裂解分离装置内部相连通;所述出口歧管伸入所述管壳式裂解分离装置内部;所述出口歧管内壁附有氢透膜。
进一步地,所述催化剂为ru、ni和fe等金属基氨分解催化剂;所述氢透膜为钯基合金膜。
进一步地,所述纯化器内由多孔固体物质分子筛吸附剂填充,用于除去氢气中微小水分杂质和氨、氮气。
进一步地,所述气化器、所述氨气预热器和所述氢气冷却器可为板翅式、板式、缠绕管式或壳管式换热器;所述气化器、所述氨气预热器和所述氢气冷却器内部可为打孔、波纹或锯齿型翅片。
进一步地,所述冷热电三联供复合系统开启时使用所述蓄电池驱动所述制氢系统开始制氢,开机时所述电加热器满负荷工作,当产出氢气后所述电加热器变为小负荷工作或者间歇工作模式。
较现有技术相比,本实用新型具有以下优点:
1、本实用新型提供的基于氨能源船舶的冷热电三联供复合系统,摒弃了目前纯粹把制氢和储氢技术割裂开来(即先制氢再储运氢),开创性的提出了先储运载氢原料,再现场制氢的技术流程,克服了现有技术在大规模耗能制氢后无后续氢储运的技术衔接,以至氢的压缩、液化储运再次进行大量的能源消耗甚至比制氢经济性更差的这一不可合理局面。
2、本实用新型提供的基于氨能源船舶的冷热电三联供复合系统,克服目前氢气、液氢储运成本高、易燃易爆等缺点,利用载氢原料液氨经行储运,由于液氨获取途径广泛成本低廉(<3000¥/吨),换算成氢气为16.7¥/kg而目前加氢站氢气价格约为70¥/公斤,且比其它载氢体系单位质量储氢量高(17.6%),此外液氨的体积能量密度是液氢的1.53倍,相同体积的燃料,液氨的续航里程是液氢的1.53倍。
3、本实用新型提供的基于氨能源船舶的冷热电三联供复合系统,有别于传统的柴油或lng船舶冷热电三联产,柴油船舶利用发动机驱动发电机发电,利用电力驱动制冷、锅炉装置进行冷热供应;lng船舶利用有机朗肯循环进行发电,通过热回收来产生冷热供应;本实用新型相比于柴油和lng引擎,利用氢-空气燃料电池没有任何排放污染;另外本实用新型相比于lng船舶有机朗肯循环冷热电联产系统简单明了,能量利用率高,而且不会存在lng冷能梯级利用的和有机朗肯循环效率的制约。
4、本实用新型提供的基于氨能源船舶的冷热电三联供复合系统,经济、安全、环保、节能,摒弃了lng,液氢的昂贵储存以及易燃易爆条件,过程中不产生任何氮氧-碳氧颗粒物排放,通过换热网络完全回收利用氨催化制氢所提供的额外能量。为了预防氢气冷却降温时易燃易爆的危险,本实用新型在系统内没有直接利用分解后的氢气余热来气化原料气,而是巧妙的设置了其它防爆载冷剂作为介质在气化器和氢冷却器之间进行热量的传递和转换。
5、本实用新型提供的基于氨能源船舶的冷热电三联供复合系统,不仅可储运富氢介质及现场制造纯化率99.9%以上的氢气作为燃料电池燃料发电,而且利用集成换热网络回收该过程冷量和废热以减少制氢能耗,同时还兼顾了高效、无污染和经济性,满足了船舶行驶中蒸汽热量、冷量以及电力的三重需求。
综上,应用本实用新型颠覆性的以氢的储运为开端,制氢和流程内的冷热电联合利用为终端,打破了传统方法先制氢后储运的复杂过程和极高成本,本实用新型以富氢物液氨为储氢载体,通过液氨气化、氨气预热、加热、催化分解以及氢气纯化、燃料电池发电,废氮气换热、液氨气化冷热量回收利用等一系列的能量转换系统及方法,形成一套基于氨能源船舶的冷热电三联供综合系统。因此,本实用新型的技术方案解决了现有的制氢-储氢技术把制氢和储氢技术割裂开来造成大量能源消耗的问题。系统和模块化方法适于液氨能源系统冷热电联产以及相关氨能源在船舶、汽车等领域的推广使用。
基于上述理由本实用新型可在液氨能源系统冷热电联产等领域广泛推广。
附图说明
为了更清楚地说明本实用新型实施例或现有技术中的技术方案,下面将对实施例或现有技术描述中所需要使用的附图做以简单地介绍,显而易见地,下面描述中的附图是本实用新型的一些实施例,对于本领域普通技术人员来讲,在不付出创造性劳动性的前提下,还可以根据这些附图获得其他的附图。
图1为本实用新型所述基于氨能源船舶的冷热电三联供复合系统的框架图。
图2为本实用新型所述冷热能量回收换热循环系统工作原理示意图。
图3为本实用新型所述氨气裂解氢分离单元装置示意图。
图中:1、船用液氨储罐;2、流量调节阀组;3、气化器;4、压力调节阀组;5、干燥过滤器;6、氨气预热器;7、电加热器;8、氨催化分解氢分离单元;81、进口歧管;82、管壳式裂解分离装置;83、出口歧管;84、氮气出口;9、氢纯化器;10、氢冷却器;11、氢气压力流量控制阀组;12、氢-空气燃料电池;13、电动机螺旋桨;14、蓄电池;15、余热锅炉;16、载冷剂泵。
具体实施方式
需要说明的是,在不冲突的情况下,本实用新型中的实施例及实施例中的特征可以相互组合。下面将参考附图并结合实施例来详细说明本实用新型。
为使本实用新型实施例的目的、技术方案和优点更加清楚,下面将结合本实用新型实施例中的附图,对本实用新型实施例中的技术方案进行清楚、完整地描述,显然,所描述的实施例仅仅是本实用新型一部分实施例,而不是全部的实施例。以下对至少一个示例性实施例的描述实际上仅仅是说明性的,决不作为对本实用新型及其应用或使用的任何限制。基于本实用新型中的实施例,本领域普通技术人员在没有做出创造性劳动前提下所获得的所有其他实施例,都属于本实用新型保护的范围。
需要注意的是,这里所使用的术语仅是为了描述具体实施方式,而非意图限制根据本实用新型的示例性实施方式。如在这里所使用的,除非上下文另外明确指出,否则单数形式也意图包括复数形式,此外,还应当理解的是,当在本说明书中使用术语“包含”和/或“包括”时,其指明存在特征、步骤、操作、器件、组件和/或它们的组合。
除非另外具体说明,否则在这些实施例中阐述的部件和步骤的相对布置、数字表达式和数值不限制本实用新型的范围。同时,应当清楚,为了便于描述,附图中所示出的各个部分的尺寸并不是按照实际的比例关系绘制的。对于相关领域普通技术人员己知的技术、方法和设备可能不作详细讨论,但在适当情况下,所述技术、方法和设备应当被视为授权说明书的一部分。在这里示出和讨论的所有示例中,任向具体值应被解释为仅仅是示例性的,而不是作为限制。因此,示例性实施例的其它示例可以具有不同的值。应注意到:相似的标号和字母在下面的附图中表示类似项,因此,一旦某一项在一个附图中被定义,则在随后的附图中不需要对其进行进一步讨论。
在本实用新型的描述中,需要理解的是,方位词如“前、后、上、下、左、右”、“横向、竖向、垂直、水平”和“顶、底”等所指示的方位或位置关系通常是基于附图所示的方位或位置关系,仅是为了便于描述本实用新型和简化描述,在未作相反说明的情况下,这些方位词并不指示和暗示所指的装置或元件必须具有特定的方位或者以特定的方位构造和操作,因此不能理解为对本实用新型保护范围的限制:方位词“内、外”是指相对于各部件本身的轮廓的内外。
为了便于描述,在这里可以使用空间相对术语,如“在……之上”、“在……上方”、“在……上表面”、“上面的”等,用来描述如在图中所示的一个器件或特征与其他器件或特征的空间位置关系。应当理解的是,空间相对术语旨在包含除了器件在图中所描述的方位之外的在使用或操作中的不同方位。例如,如果附图中的器件被倒置,则描述为“在其他器件或构造上方”或“在其他器件或构造之上”的器件之后将被定位为“在其他器件或构造下方”或“在其位器件或构造之下”。因而,示例性术语“在……上方”可以包括“在……上方”和“在……下方”两种方位。该器件也可以其他不同方式定位旋转90度或处于其他方位,并且对这里所使用的空间相对描述作出相应解释。
此外,需要说明的是,使用“第一”、“第二”等词语来限定零部件,仅仅是为了便于对相应零部件进行区别,如没有另行声明,上述词语并没有特殊含义,因此不能理解为对本实用新型保护范围的限制。
实施例1
如图1-3所示,本实用新型提供了一种基于氨能源船舶的冷热电三联供复合系统,包括制氢系统、船舶电力供给系统和冷热能量回收换热循环系统;
用于制氢的所述制氢系统包括依次连通的船用液氨储罐1、流量调节阀组2、气化器3、压力调节阀组4、干燥过滤器5、氨气预热器6、电加热器7、氨催化分解氢分离单元8、氢纯化器9、氢冷却器10和氢气压力流量控制阀组11;所述制氢系统的各设备之间通过管路相连通;
所述制氢系统的制氢过程依次包括液态氨储存、气化、除杂及氨气升温、催化裂解转化制氢和分离纯化,具体过程为:从所述液氨储存罐1来来流的液氨,经过所述流量调节阀组2调节流量后进入所述气化器3气化为氨气,氨气通过所述压力调节阀组4调压并由所述干燥过滤器5除去微量杂质和水分后进入所述氨气预热器6,所述电加热器7使氨气温度提升到反应温度,通过所述氨催化分解氢分离单元8催化原料氨气裂解为氢气和氮气,最后依次经过所述氢纯化器9和所述氢冷却器10,并经过所述氢气压力流量控制阀组11调节压力和流量后成为所述所述船舶电力供给系统中所述氢-空气燃料电池12的供给燃料使所述氢-空气燃料电池12进行发电;
所述船舶电力供给系统包括氢-空气燃料电池12、电动机螺旋桨13和蓄电池14;所述氢冷却器10将氢气通入所述氢-空气燃料电池12进行发电并将电力输送至所述蓄电池14进行储存;所述氢-空气燃料电池12将电力输送至船舶的电动机,电动机接收电力推动所述电动机螺旋桨13转动使船舶行进;所述船舶电力供给系统还能够为船舶其他用电设备供电;
所述冷热能量回收换热循环系统包括余热锅炉15和载冷剂泵16;所述余热锅炉15通过管路与所述氨气预热器6相连通,所述冷热能量回收换热循环系统回收的所述氨催化分解氢分离单元8内发生裂解反应后废气氮气所携带的热量经所述氨气预热器6供给至所述余热锅炉15,所述余热锅炉15用于产生饱和蒸汽供应船舶辅机和客舱热量需求;
具体的,回收的高温废氮气余热首先给所述氨气预热器6使其尽快达到反应温度从而减少所述加热器7的功耗,其余的热量释放给所述余热锅炉15从而产生饱和蒸汽供应船舶辅机和客舱热量需求;
所述载冷剂泵16分别通过管路与所述气化器3相连通,所述冷热能量回收换热循环系统通过载冷剂在所述气化器3内进行冷量回收用于对船舶设备进行冷却以及供应船舶相关冷量需求;
本实用新型包含两个能量回收换热网络,分别为所述冷量回收换热网络是利用泵送载冷剂循环回收气化器3内液氨气化的冷量从而供应给船舶的冷量需求方;热量回收换热网络则是利用分解后高温氮气在预热器6内循环加热被气化后的低温氨气从而节约电加热器7的功耗。该设计使系统更加节能环保,系统耗电部件仅为载冷剂循环泵16以及电加热器7,系统开启时仅用蓄电池14驱动电加热器7加热氨气开始反应制氢即可,循环开机时电加热器满负荷工作,当产出氢气后加热器变为小负荷工作或者间歇工作模式。
进一步地,所述冷热能量回收换热循环系统通过载冷剂在所述气化器3内回收液氨气化的冷量能够供给至所述氢冷却器10。
进一步地,所述冷热能量回收换热循环系统回收的所述氨催化分解氢分离单元8内发生的裂解反应后废气氮气所携带的热量,首先供给至所述氨气预热器6使氨气升温从而减少所述加热器7的功耗,然后经所述氨气预热器6供给至所述余热锅炉15。
进一步地,所述气化器2、所述氢冷却器10以及船舶冷却需求所循环的所述载冷剂为乙二醇水溶液、氮气或者其它防爆载冷剂。
进一步地,如图3所示,所述氨催化分解氢分离单元8包括进口歧管81、出口歧管83和管壳式裂解分离装置82;所述管壳式裂解分离装置82内填充有催化剂;所述管壳式裂解分离装置82设置有氮气出口84;所述进口歧管81与所述管壳式裂解分离装置82内部相连通;所述出口歧管83伸入所述管壳式裂解分离装置82内部;所述出口歧管83内壁附有氢透膜;
通过设置歧管,能够增大反应面积减少催化剂中毒失效现象,使氨气通过进口歧管内被分成几股通入管壳式裂解分离装置,被催化剂裂解为氢气和氮气,出口歧管附有氢透膜只有氢气可以进入管中导出,每股导出的氢气由出口歧管的出口端歧管汇聚排出。
进一步地,所述催化剂为ru、ni和fe等金属基氨分解催化剂及类似材料,所述氢透膜为钯基合金膜等类似材料。
进一步地,所述纯化器9内由多孔固体物质分子筛吸附剂填充,用于除去氢气中微小水分杂质和氨、氮气;所述多孔固体物质分子筛吸附剂为结晶型铝硅酸盐等类似材料。
进一步地,所述气化器2、所述氨气预热器6和所述氢气冷却器9可为板翅式、板式、缠绕管式或壳管式换热器;所述气化器2、所述氨气预热器6和所述氢气冷却器9内部可为打孔、波纹或锯齿型翅片。
进一步地,所述冷热电三联供复合系统开启时使用所述蓄电池14驱动所述制氢系统开始制氢,开机时所述电加热器7满负荷工作,当产出氢气后所述电加热器7变为小负荷工作或者间歇工作模式。
进一步地,所述冷热电三联供复合系统的额外耗电部件为载冷剂循环泵16以及氨气电加热器7再无其它耗电设备。
进一步的,所述氨催化分解氢分离单元8内,原料气在一定温度650℃~700℃左右常压下被催化剂反应分解为氢气和氮气,该过程可体现如下:
该过程为吸热膨胀反应,即单位摩尔氨气在一定温度的催化作用下裂解为75%的氢气和25%的氨气并吸收47.3kj热量,因此提高温度和降低压力有助于氨的动态分解,因此一般常压和650℃左右温度氨气裂解转化率可达99.9%。
采用本实用新型所述基于氨能源船舶的冷热电三联供复合系统进行供电时具体包括如下步骤:
步骤1:液氨储运气化
氨气在常温加压0.86mpa或常压低温-33℃时转化为液态储存在船用液氨储罐1内,通过流量调节阀组2调节流量后通入气化器3,进行气化变为氨气,并通过冷热能量回收换热循环系统在所述气化器3内进行冷量回收;氨气通入干燥器过滤器5,通过压力调节阀组4控制气化器3内的压力及输出的氨气的流量;
步骤2:氨气干燥除杂及加热
氨气通过干燥器过滤器5进行干燥除杂,在氨气预热器6内,利用冷热能量回收换热循环系统回收的所述氨催化分解氢分离单元8内发生裂解反应后废气氮气所携带的热量把氨气预热到500℃左右,然后氨气经过设定温度的电加热器7加热到催化裂解温度650-700℃左右;
步骤3:氨气催化裂解分离及氢气纯化
工艺条件下的原料气通入氨催化分解氢分离单元8,在一定温度下被催化剂分解为氢气和氮气;氢气依次经过氢纯化器9和氢冷却器10进行纯化和冷却;
氨催化分解氢分离单元8通过管层附有的钯金属基氢透膜,分解的气体经过透氢膜后只有氢气能进入纯化器9内,其中的微小水分杂质和氨、氮气等被分子筛吸附,剩下氢气导出作为燃料;
步骤4:船舶燃料电池发电以及供电
氢气经过氢气压力流量控制阀组11通入氢-空气燃料电池12进行发电并将输送至所述蓄电池14进行储存;氢-空气燃料电池12将电力输送至船舶的电动机,电动机接收电力推动所述电动机螺旋桨13转动使船舶行进;所述船舶电力供给系统还能够为船舶其他用电设备供电;
本实用新型所述基于氨能源船舶的冷热电三联供电方法,包括的系统换热网络能量回收利用流程具体为:
分离后的废气氮气和纯化后的氢气进入系统换热网进行能量回收利用,所述的系统冷、热能量回收换热网络供应循环,即为对氨升温裂解反应后废气氮气所携带的热量进行回收,换热网络回收的高温废氮气余热首先给氨气预热器6使其尽快达到反应温度从而减少加热器7的功耗,剩下的释放给余热锅炉15从而产生饱和蒸汽用以供应船舶热量需求。液氨气化冷量回收换热网络循环通过载冷剂在气化器3内进行冷量回收经过载冷剂泵16以及相关管路用以供给船舶相关冷量需求。
如图1所示,给出了氨能源船舶中燃料储存、气化、升温、分解转化制氢,燃料电池发电,废氮充当热源以及基于上述过程的冷热电联供综合系统的工艺流程和设计思路。
如图2所示,所述的系统冷、热能量回收换热网络供应循环,即为对氨升温裂解反应后废气氮气所携带的热量进行回收,换热网络回收的高温废氮气余热首先给氨气预热器6使其尽快达到反应温度从而减少加热器7的功耗,剩下的释放给余热锅炉16从而产生饱蒸汽用以供应船舶热量需求。液氨气化冷量回收换热网络循环通过载冷剂在气化器3内进行冷量回收经过载冷剂泵16以及相关管路用以供给船舶相关冷量需求。
本实用新型不仅可储运富氢介质及现场制造纯化率99.9%以上的氢气作为燃料电池燃料发电,而且利用集成换热网络回收该过程冷量和废热以减少制氢能耗,同时还兼顾了高效、无污染和经济性,满足了船舶行驶中蒸汽热量、冷量以及电力的三重需求。
最后应说明的是:以上实施例仅用以说明本实用新型的技术方案,而非对其限制;尽管参照前述实施例对本实用新型进行了详细的说明,本领域的普通技术人员应当理解:其依然可以对前述实施例所记载的技术方案进行修改,或者对其中部分或者全部技术特征进行等同替换;而这些修改或者替换,并不使相应技术方案的本质脱离本实用新型实施例技术方案的范围。
起点商标作为专业知识产权交易平台,可以帮助大家解决很多问题,如果大家想要了解更多知产交易信息请点击 【在线咨询】或添加微信 【19522093243】与客服一对一沟通,为大家解决相关问题。
此文章来源于网络,如有侵权,请联系删除


